How to Weld Aluminum With a Spool Gun? Essential Steps, Safety Tips, and Troubleshooting
Published on: March 2, 2025 | Last modified: March 4, 2025
By: Joe Carter
A spool gun is a welding tool designed to feed wire from a small spool, making it perfect for welding aluminum. It helps maintain a consistent feed rate and minimizes issues like wire tangling.
So, if you are wondering how to weld aluminum with a spool gun, you’re not alone. It’s crucial to follow the right techniques for effective welding, since aluminum’s properties differ from steel. Personally, I’ve seen how using the right method can save time and produce cleaner welds, which makes a big difference in quality.
In this guide on how to weld aluminum with a spool gun, you’ll learn about spool guns, types, essential gear, welding steps, safety tips, and troubleshooting. We’ll also cover factors that influence aluminum welding, advantages of using a spool gun, and other options you can consider. It’s packed with details to help you get started and improve your welding skills!
Contents
- How to Weld Aluminum With A Spool Gun?
- What is a Spool Gun?
- Types Of Spool Guns
- Essential Prerequisites to Get Started
- Steps to Weld Aluminum With a Spool Gun
- Safety Tips
- Types Of Welding Processes for Aluminum
- Factors Affecting Aluminum Welding With a Spool Gun
- Common Issues and Troubleshooting
- Aftercare, Inspection, and Advanced Tips for Welding Aluminum With a Spool Gun
- Techniques for Achieving Clean Welds with a Spool Gun
- Advantages Of Welding Aluminum With a Spool Gun
- Use Cases Of Welding Aluminum With a Spool Gun
- Other Options You Can Consider
- Frequently Asked Questions (FAQs)
- Wrap-up
- References
How to Weld Aluminum With A Spool Gun?
A spool gun feeds wire directly, making it ideal for how to weld aluminum with a spool gun. Set voltage to around 15-18 volts. Use 4047 or 4045 filler wire, and maintain a steady speed. It’s easier for beginners, great for DIY projects.
What is a Spool Gun?
A spool gun is a specialized tool primarily used in MIG (Metal Inert Gas) welding. It has a lightweight design and uses a spool of wire in the gun’s feed mechanism. This setup allows for a steady feed of filler material, making it ideal for welding aluminum. Typically, spool guns use wire with a diameter of 0.030 to 0.045 inches (0.76 To 1.14 Mm), perfect for thin metal applications.
When welding aluminum with a spool gun, you get cleaner welds and less spatter. The gun’s portability makes it easier to maneuver in challenging angles. From my experience, the process is impressively fast. You achieve quick results, especially when you use the right settings for your specific type of aluminum.
I remember my first time using a spool gun to weld aluminum. I was amazed at how simple it was. When I learned how to MIG weld aluminum with a spool gun, everything clicked. You can weld aluminum without a spool gun, but the quality you achieve with one is unmatched. Plus, the right settings, like AC (Alternating Current) or DC (Direct Current) welding, make a significant difference.
Types Of Spool Guns
-
Standard Spool Guns
Standard spool guns are versatile and easy to handle. To weld aluminum, set up your machine correctly. Start by adjusting the voltage and wire feed speed; typically, 18-22 volts (V) works well. Aim for a wire feed speed of 100-200 inches per minute (IPM) for clean welds.
Optimal welding results also depend on proper eye protection, which requires accurately adjusting your helmet’s settings during preparation. You can find more information on adjusting welding helmets to ensure greater precision and safety in your projects.
-
Heavy-duty Spool Guns
Heavy-duty spool guns are designed for tough jobs and thicker aluminum. Ensure the settings match your project. Ramp up the voltage to about 22-25V and wire feed speed to around 300 IPM for stronger weld penetration.
-
Push-pull Spool Guns
Push-pull spool guns use a unique mechanism to feed aluminum wire smoothly. Match the push and pull settings to prevent slippage. Maintain a voltage of 18-20V and set the wire feed speed between 150-200 IPM for consistent arcs.
-
Compact Spool Guns
Compact spool guns are portable and great for small projects. They work well at lower settings. To weld aluminum, set your voltage around 16-18V and keep the wire feed speed near 100 IPM for delicate seams.
-
Automated Spool Guns
Automated spool guns are for industrial use and have programmable features. You can set the machine to adjust settings automatically. Configure it for a voltage of about 20-24V and let the system manage the wire speed for maximum efficiency.
You should now have a good understanding of spool gun types and their applications. In the next part, we’ll discuss the key prerequisites for getting started.
Essential Prerequisites to Get Started
What do you need to prepare for welding aluminum with a spool gun?
- Spool Gun: You’ll need a spool gun, like the Miller Spoolmate 100 series, designed for smooth aluminum wire feeding, which is crucial for a clean weld.
- Aluminum Welding Wire: Use ER4047 or ER5356 wire, sized at 0.035 inch (1.0 Mm). This wire ensures strong welds and minimizes defects.
- Welding Machine: A machine such as the Hobart Handler 210 MVP is essential. It provides the right settings for aluminum, making it easier to achieve good penetration.
- Shielding Gas: Obtain a tank of pure argon gas, typically around 25 cubic feet (0.71 M³). This gas prevents oxidation, enhancing the quality of your weld.
We’ve wrapped up the essential prerequisites for getting started. Next up, we’ll look at the steps for welding aluminum with a spool gun.
Steps to Weld Aluminum With a Spool Gun
Here are steps to efficiently use a spool gun for aluminum welding.
-
Adjust the Settings
First, adjust your spool gun settings for aluminum. You’ll typically use a wire speed of 8-10 m/min (26-32 Ft/min) and a voltage of 12-16 volts. Each machine operates differently, so always refer to your machine’s manual. Setting the right parameters helps achieve a clean bead without burn-through.
Use a mix of 75% argon and 25% CO2 for the gas. This mixture reduces spatter and provides better arc stability. A gas flow rate of about 15-20 cubic feet per hour (CFH) ensures adequate coverage to protect the molten weld from oxidation. A consistent gas flow makes a significant difference.
-
Prepare the Workpiece
Next, clean the aluminum surface thoroughly. Remove any dirt, oil, or oxide layer using a stainless-steel brush or degreaser. Dirt can cause porosity in the weld, leading to weak joints. A clean surface ensures a strong and reliable weld.
Choosing the proper welding rod is crucial for successful aluminum welding. Knowing what welding rod to use can significantly impact weld strength and quality.
Secure the aluminum piece for welding. Whether clamped or fitted in a jig, it needs to stay stable. This minimizes warping and ensures an even weld. A stable setup allows you to focus on welding technique, improving your results.
-
Begin Welding
Start the weld at a corner or edge of the joint. Maintain a steady pace; don’t rush. For best results, angle the gun about 10 to 15 degrees toward the direction of travel for better penetration and a flat bead profile. Keeping a steady hand is essential! Understanding the differences between welding positions can enhance your technique and craftsmanship, as explained in guidelines for welding positions.
Hold the spool gun about 1/4 inch (6 Mm) from the workpiece. This distance minimizes spatter and ensures the aluminum fuses properly. Adjust as needed based on metal thickness; thinner materials require closer spacing for effective heat transfer.
-
Maintain a Steady Speed
As you weld, keep a consistent speed for an even bead. Moving too fast risks weak joints; too slow may cause burn-through. Generally, a speed of about 3-4 inches (7.6-10 Cm) per minute works well for most aluminum thicknesses. Gauge your speed by observing the weld pool. Understanding electrode classifications like E316-16 specifications can further enhance your welding effectiveness.
Look for a clean, wet appearance in the weld bead. If it appears dull and grainy, slow down. Adjusting your speed aids in penetration and appearance. Take the time to get this right; it’s worth it.
-
Fill the Joint
Begin filling the joint with weave patterns or straight stringer beads as you move along. A slight weave pattern helps distribute heat evenly. Pulsing the trigger slightly while moving helps control heat and provides an even fill. The end result will be a stronger, more reliable weld.
Monitor the filler rod as you proceed. The filler must melt smoothly into the joint. Too much filler creates a lump, while too little leads to gaps. It’s about finding the right balance for a finished weld.
We have now covered the process of welding aluminum with a spool gun. Next, we will examine safety precautions.
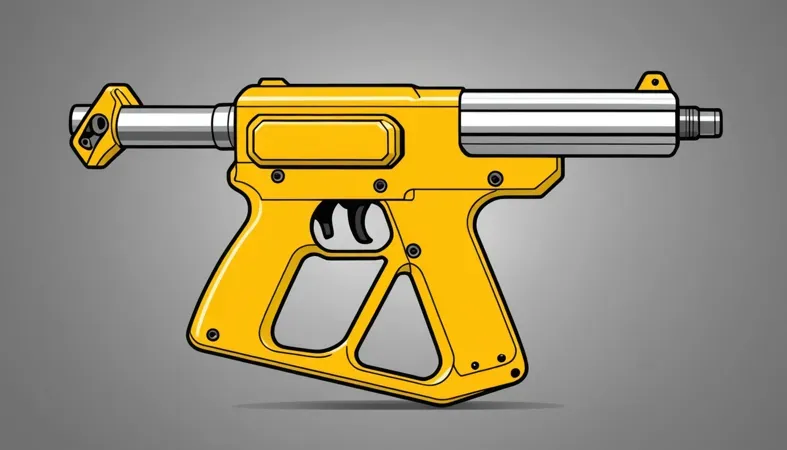
Safety Tips
Let’s review essential precautions for welding aluminum.
- Use Proper Eye Protection: Protect your eyes from sparks. I recommend safety glasses with side shields.
- Ventilate Your Workspace: Ensure good airflow to avoid toxic fumes. Use exhaust fans or work outdoors.
- Wear Fire-Resistant Gear: Use flame-retardant (Fireproof) clothing and gloves to prevent burns. Nomex products work well.
- Check Equipment Regularly: Inspect the spool gun before use for safety and performance. Regular maintenance can prevent accidents!
Taking safety precautions is crucial; I can’t stress this enough!
You should now have a good understanding of safety precautions, best practices, and essential gear. In the next part, we’ll discuss various welding methods for aluminum.
Types Of Welding Processes for Aluminum
Let’s look at the different types of welding processes: MIG, TIG, Stick, Pulsed MIG, and Gas welding.
-
MIG Welding Processes
MIG (Metal Inert Gas) welding is preferred for aluminum. It uses a continuous wire feed for efficient welding. An Argon mixture, like 100% Argon or 75/25 Argon/Helium, is ideal. A spool gun simplifies feeding aluminum wire, especially with its low melting temperature—so you won’t face frustrations!
-
TIG Welding Processes
TIG (Tungsten Inert Gas) is another effective method for aluminum. This process allows better control, making it great for thinner materials. You can use a DC setup—just remember to use a dedicated aluminum electrode for the best results.
-
Stick Welding Processes
Stick welding, or SMAW (Shielded Metal Arc Welding), isn’t commonly used for aluminum, but it’s possible! Specialized electrodes, like E6013, perform adequately. However, the results may be less appealing compared to MIG or TIG.
-
Pulsed MIG Welding Processes
Pulsed MIG welding reduces heat input, which is crucial when welding aluminum. It alternates between high and low current, providing better control and less distortion. Through trial and error, I’ve found this method excels in minimizing warping.
-
Gas Welding Processes
Gas welding works for aluminum but is less efficient. This method uses a flame and filler rod. It’s an old technique, often used for repair, but it falls short in speed and strength compared to MIG and TIG.
Factors Affecting Aluminum Welding With a Spool Gun
What factors impact your ability to weld aluminum effectively with a spool gun?
-
Material Thickness
Material thickness is important. Aluminum sizes typically range from 1/16 inch (1.6 Mm) to 1/4 inch (6.4 Mm). Thicker aluminum requires more heat, so adjust your settings accordingly.
-
Welding Speed
If you’re too fast, you risk weak joints. A speed of 6-12 inches per minute (15-30 Cm) usually yields a strong weld.
-
Temperature Control
Maintaining the right temperature is crucial. Aim for 350°F to 500°F (177°C to 260°C) to prevent warping or burn-through.
-
Filler Metal Selection
Choosing the right filler metal is essential. Typically, use 4047 or 5356 alloys, which blend well with standard aluminum and improve weld strength.
-
Gas Composition
Argon or argon-helium mixtures work best. The correct gas protects the weld pool and enhances penetration for a cleaner finish—use pure argon for thin materials.
Common Issues and Troubleshooting
Let’s look at specific problems that can arise when using a spool gun.
-
Inconsistent Welding Beads
Inconsistent welding beads can occur due to incorrect settings. Adjust your voltage to about 18-22 volts. If the beads vary greatly, check your feed speed and adjust it to 200-350 inches per minute (508-889 Cm/min).
-
Spatter Formation
Spool guns might create excessive spatter if the wire feed speed is too high. Reduce the speed to around 150-250 inches per minute (381-635 Cm/min) and manage the shielding gas flow to minimize spatter.
-
Burn-through
Burn-through can occur when welding thinner materials. Ensure your amperage is set to 40-150 amps, depending on the aluminum thickness, and maintain a proper distance from the material.
-
Poor Penetration
Poor penetration often arises from an improper angle and speed. Adjust the spool gun’s angle to about 10-15 degrees for better results. Increase your travel speed if penetration is insufficient.
-
Wire Feeding Problems
Wire feeding issues can affect spool guns, often due to a tangled wire spool or improper liner. Uncoil the wire properly and check for kinks. Replacing the liner every 100 hours can help significantly!
Aftercare, Inspection, and Advanced Tips for Welding Aluminum With a Spool Gun
Here’s crucial advice on aftercare, inspection, and expert tips to ensure your aluminum welds endure.
Aftercare Tips
After welding aluminum with your spool gun, flush the torch with a suitable solvent, like acetone, for at least 60 seconds. This cleans out residual filler metal or debris. Remove the contact tip and soak it in a cleaning solution to prevent clogs during your next project.
Inspection
Inspect your welds with a gauge like the Kohler Ultratool to measure bead width. Aim for a bead width of 1/8 in (3.2 Mm) for strength. Check for porosity by visually scanning for tiny holes, which often indicate poor feed rates.
Expert Tips
Set your wire feed speed at about 300 to 450 in/min (76 to 114 Cm/min) for optimal results. Use a 0.030 in (0.76 Mm) diameter wire for thinner aluminum. Practice different travel angles; a push angle yields a flatter bead, while a pull technique creates a higher-profile weld.
Techniques for Achieving Clean Welds with a Spool Gun
To really nail aluminum welding with a spool gun, you need specific techniques to ensure clean and strong welds.
Technique | Description | Recommended Settings |
---|---|---|
Weaving Motion | Use a weaving motion to distribute heat evenly across the joint. | Speed: 4-5 IPM (10-13 Cm/min), Voltage: 18-20 V |
Push Technique | Push the gun away from the weld pool to improve arc stability. | Angle: 10-15° forward, Speed: 6 IPM (15 Cm/min) |
Short Circuit Transfer | Use short circuit transfer for thin materials to reduce heat input. | Voltage: 12-15 V, Wire Feed Speed: 100-150 IPM (254-381 Cm/min) |
Stringer Beads | For wider joints, use stringer beads instead of weaving. | Voltage: 17-19 V, Speed: 5 IPM (12 Cm/min) |
Adjusting Torch Angle | Maintain a consistent torch angle of around 15-20° for better penetration. | No specific settings, maintain consistent distance (1/4 inch or 6 Mm) |
Using these techniques correctly will help you improve your aluminum welds significantly. Practice makes perfect, so give these a shot on scrap pieces!
Advantages Of Welding Aluminum With a Spool Gun
The main benefit of using a spool gun is its ability to handle aluminum’s soft, ductile nature. This helps you achieve precise, clean welds.
It also reduces feeding issues, minimizes wire tangling, and enhances arc stability. Plus, it gives you greater control over the welding process, saving you time and lowering the risk of defects.
Use Cases Of Welding Aluminum With a Spool Gun
I’ve used a spool gun for several projects, and it has many applications, including:
- Marine Fabrication: Ideal for creating boat components due to its ability to handle thin aluminum and prevent warping. It’s popular for producing lightweight yet strong parts.
- Outdoor Equipment Repair: Perfect for fixing outdoor machinery like lawn mowers and ATVs. The spool gun’s portability makes it great for on-site repairs.
- Aerospace Components: Extensively used in the aerospace industry to weld aluminum parts where precision and strength are critical. It’s highly regarded for creating clean welds.
- Automotive Industry: Employed in crafting and repairing trailer frame structures because it’s efficient for various aluminum thicknesses. It’s routinely preferred for its speed and versatility.
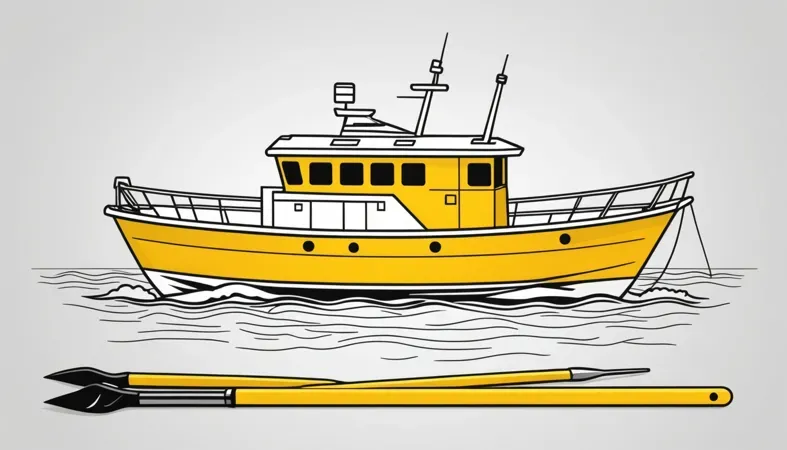
Other Options You Can Consider
Welding aluminum without a spool gun? You’ve got options! Consider a TIG welder, like the Miller Diversion 180, for precise control, especially on thinner materials. Or, use a MIG welder equipped with a standard gun, though it requires more attention to feed settings and wire type.
Through trial and error, I’ve discovered that pulse MIG welding, with machines like the Lincoln Electric Power MIG 210, offers good results too. It’s particularly useful for thicker aluminum while providing better penetration. Each method has its crowd; find what suits your projects best!
Frequently Asked Questions (FAQs)
Here are some questions I typically get asked about welding aluminum.
Do You Push or Pull With an Aluminum Spool Gun?
When using an aluminum spool gun, you typically push the weld. Pushing helps create a cleaner bead and reduces the risk of contamination. It also promotes better penetration, ensuring your weld is strong and durable.
Do You Need AC to Weld Aluminum With a Spool Gun?
No, you don’t need AC to weld aluminum with a spool gun. Spool guns usually work with DC polarity, making them effective for aluminum welding without alternating current. This allows for smoother operations and a more manageable arc.
What Polarity Do You Use to Weld Aluminum With a Spool Gun?
When welding aluminum with a spool gun, you use direct current electrode positive (DCEP). DCEP helps in achieving a stable arc and proper heat distribution. By maintaining this polarity, you enhance the quality of the weld joint.
Can You Weld Cast Aluminum With a Spool Gun?
Yes, you can weld cast aluminum with a spool gun. Using specific filler materials designed for cast aluminum is crucial. This ensures a good bond and suitable mechanical properties of the weld, vital for structural repairs. Exploring advanced welding techniques like heliarc welding methods can further enhance the quality and precision of aluminum welding.
Can You MIG Weld Aluminum Without a Spool Gun?
Yes, you can MIG weld aluminum without a spool gun. However, using a regular MIG setup may require modifications to handle aluminum wire more effectively. This often results in less precise feeding and increased difficulty in obtaining a good weld.
How to Use a Spool Gun to Weld Aluminum?
To use a spool gun for aluminum welding, ensure the gun is wired properly and the correct filler wire is loaded. Always adjust your settings specific to aluminum, like voltage and wire speed, to produce a strong weld bead.
Wrap-up
Phew, we covered a lot in this article. We tackled what a spool gun is, types of spool guns, prerequisites for starting, steps to weld aluminum with a spool gun, safety tips, welding processes, factors affecting welding, common issues, aftercare, inspection, advanced tips, advantages, use cases, and even some other options to consider. It’s important to have a solid understanding of these items for successful welding.
To sum it up, learning how to weld aluminum with a spool gun involves knowing the equipment, necessary preparations, and proper techniques. By following the steps outlined, like ensuring appropriate temperatures and materials, you’ll find the process straightforward. Wishing you success in your welding projects, and remember, practice makes perfect when it comes to mastering those aluminum joints.
If you’d like to expand your knowledge even further, feel free to return to What is Welding for additional insights and resources.
References
- American Welding Society. (2020). AWS Welding Handbook: Welding Science and Technology (Vol. 1). Miami, FL: AWS.
- Canadian Welding Bureau (CWB): https://www.cwbgroup.org
- Blodgett, O. W. (1995). Design of Weldments. Cleveland, OH: James F. Lincoln Arc Welding Foundation.
Joe Carter is a retired welding professional with over 40 years of hands-on experience in the industry, spanning ship repair, structural welding, and even underwater projects. Joe is a master of MIG, TIG, and Stick welding. Passionate about mentoring the next generation of welders, Joe now shares his decades of expertise and practical insights to help others build rewarding careers in welding.
Aluminum, American Welding Society, MIG Welding, Safety Tips, Spool Gun, Troubleshooting Welding, Welding, Welding Techniques, Welding Wire