How to Stack Dimes MIG Welding? Techniques, Tips, and Tricks
Published on: April 29, 2025 | Last modified: March 4, 2025
By: Joe Carter
Stack dimes are a term used in welding to describe smooth, evenly spaced weld beads that resemble a stack of dimes. They show skill and precision in the welding process.
Many people are curious about how to stack dimes mig welding. Knowing how to do this correctly is crucial for creating strong and aesthetically pleasing welds. In my experience, mastering this technique improved my confidence and overall effectiveness in welding projects.
In this guide, we’ll cover the basics of stack dimes, examine different types of stack dimes in MIG welding, share essential steps to achieve stack dimes, discuss factors affecting stacking dimes in MIG welding, and answer some frequently asked questions. Get ready to broaden your techniques, learn how to lay dimes with a MIG welder, and boost your welding skills!
Contents
How to Stack Dimes MIG Welding?
Stack dimes refers to perfect, even weld beads resembling stacked coins. To stack dimes in MIG welding, maintain a steady hand, set amperage to 120-180 amps, and keep the arc at 1/8 inch (3 Mm) from the metal. This skill is tough but crucial for automotive and structural projects.
What Are Stack Dimes?
Stack dimes is a popular term in the welding community, especially in MIG (Metal Inert Gas) welding. It describes a technique where welds are stacked side by side, resembling a row of coins. Typically, these welds have a bright, shiny appearance and maintain a consistent width of about 2.5 mm (0.1 Inches). Achieving stack dimes usually indicates good technique, with a travel speed of 15-30 cm/min (6-12 In/min) producing the ideal “dime-stacked” look that many welders strive for.
To stack dimes in MIG welding, maintain the right settings on your welder. Keep a steady hand and a consistent pace. From my experience, don’t rush! It took me a few tries to achieve that perfect stack, and once I did, the pride was worth every bit of effort.
A friend of mine used this technique to create metal artwork. He mastered laying dimes with a MIG welder. He said that achieving those dimes not only earned him compliments but also increased the strength of the welds. Mastering this technique can elevate your welding skills. So, if you’re eager to create something beautiful, remember that knowing how to stack dimes in MIG welding can be your secret weapon!
Types Of Stack Dimes in MIG Welding
What are the different types of stack dimes you can create?
-
Perfect Vertical Stacking Dimes
Perfect vertical stacking dimes look clean and consistent. To achieve them, move the welder vertically in straight lines. Keep the travel speed slow and even—aim for about 4-6 inches (10-15 Cm) per minute. Proper ventilation plays a critical role in ensuring safety during welding. It’s crucial to know how to prevent inhaling welding fumes effectively.
-
Horizontal Stacking Dimes
Horizontal stacking dimes are laid side by side. Move the welder horizontally across the joint. Maintain a steady angle of about 15 degrees for even heat distribution.
-
Overlapping Stacking Dimes
Overlapping stacking dimes blend into one another. Achieve this by slightly overlapping each pass. Adjust the feed speed to about 5-7 inches (13-18 Cm) per minute for a smooth transition.
-
Uniform Stacking Dimes
Uniform stacking dimes maintain the same width and height. Keep a consistent height of about 1/8 inch (3 Mm). Watch your travel speed and maintain it at around 3-5 inches (7-13 Cm) per minute.
-
Irregular Stacking Dimes
Irregular stacking dimes have varied heights and shapes. To stack these, move your hand freely, varying the speed and angle. A slower pace allows for more creative control.
We covered the different types of stack dimes in MIG welding. Next, we will cover the steps to achieve them.
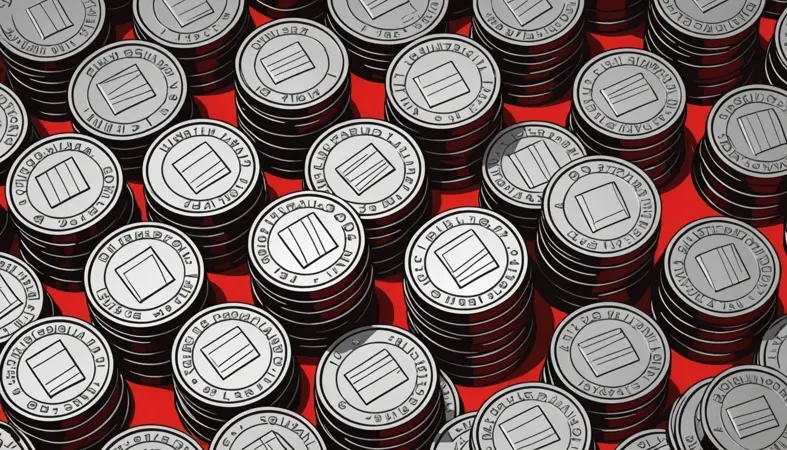
Steps to Stack Dimes in MIG Welding
Here are steps to help you master stacking dimes in MIG welding.
-
Prepare the Weld Area
Start by cleaning the base metal surfaces. Remove any rust, paint, or oil to ensure a strong weld. If you’re working with steel, use a grinder with a flap disc or wire brush for a clean surface. Small imperfections can affect your weld quality.
Set your workpiece at a comfortable height to avoid awkward positions that can hinder stance and control. Keep your workspace clutter-free; a neat area enhances focus and accuracy.
-
Select the Right Settings
Carefully choose your wire speed and voltage. For a solid stack of dimes, start with a wire speed of about 4 to 6 feet per minute (1.2 To 1.8 Meters Per Minute) at 18 to 20 volts. Adjust these settings based on the thickness and position of your base metal. Thinner metals might need a more delicate touch.
I suggest practicing on scrap material first to fine-tune your settings. It’s best to adjust before starting your actual project. Once you find the right look for your seams, note those settings for future reference; it saves time later!
-
Position the Welding Gun Properly
Hold the MIG gun at a 10-degree angle toward your direction of travel. This angle ensures proper gas coverage and reduces spatter. Maintain a distance of about 5/8 inch (16 mm) from the surface, as this affects heating and bead formation.
When it comes to heavy-duty welding equipment, understanding the specific weight can aid in transport and handling, and you might be curious about the Lincoln SA-200 welder’s weight.
If you hold it too far away, your welds will seem inconsistent. Keep that distance steady! Also, try rocking the gun on a slightly curved path to create the coveted dime-stacking look.
-
Control Your Travel Speed
Maintain a consistent travel speed for cleaner welds. Aim for about 3 to 6 inches per minute (7.6 To 15.2 Centimeters Per Minute)—less is often more. If you’re too fast, your welds may be weak; too slow, and you’ll create a big puddle. Trust me, rhythm is key!
Practice moving steadily and smoothly to avoid a shaky bead. Visualize that dime stacking; it should feel like laying down a perfect line. It may take trial and error, but you’ll master that steady pace.
-
Inspect the Welds Thoroughly
This step focuses on quality. Run your hand over the weld to check for inconsistencies like gaps or irregularities, which can affect the strength of your joint. You may need to adjust settings from previous steps to address any issues.
Each weld bead should resemble neat stacks of dimes. If they don’t look right, grind the area and re-weld. Remember, quality is your goal; don’t settle for less!
We’ve wrapped up the steps for stacking dimes in MIG welding here. Next up, we’ll look at factors influencing this technique.
Factors Affecting Stacking Dimes in MIG Welding
What factors determine the quality of dime stacks in MIG welding?
-
Wire Feed Speed
Your wire feed speed directly affects weld bead appearance. A speed of 300-500 inches per minute (7.6-12.7 M/min) is common for consistent dime stacking.
-
Voltage Settings
Using the right voltage is crucial. Typically, you’ll want settings between 18 and 25 volts, depending on material thickness and type, to achieve a smooth, consistent bead.
-
Travel Speed Consistency
Maintaining a steady travel speed, ideally around 6 to 10 inches per minute (15.2-25.4 Cm/min), is key to achieving dime-shaped welds. Too fast, and you’ll burn through; too slow, and you’ll get lumps.
-
Welding Gun Angle
Your angle matters! A 10-15 degree push angle helps direct heat properly and forms uniform dimes. A flat angle can lead to poor consolidation.
-
Material Cleanliness
If your materials are dirty, your dimes won’t shine. Always clean the surfaces—rust, paint, or oil can disrupt the arc and metal flow, causing defects.
That covers the elements influencing stacking dimes in MIG welding. Let’s now take a look at advanced techniques for achieving this.
Advanced Techniques for Stacking Dimes in MIG Welding
Once you’ve mastered the basics, several advanced techniques can further enhance your dime-stacking skills.
-
Pulsed MIG Welding
This technique alternates between high and low heat input. Pulsed welding allows for better control, resulting in smoother beads. Set your pulse frequency to around 2-4 Hz for optimal results.
-
Multi-Pass Techniques
Using multiple passes can help achieve thicker welds. Lay down a first pass, then stack another bead on top. Maintain your welder’s amperage around 180-220 amps for the best layer adhesion.
-
Stringer Beads vs. Weave Patterns
Stringer beads are straight and can give you a tighter stack of dimes. A weave pattern can be useful for wider joints. Experiment with both techniques to see which yields a better bead depth.
-
Utilizing Backhand Technique
For improved control, try the backhand technique. Angle the gun back toward your previous bead. This enhances the heat connection and can lead to better stacking.
Technique | Benefits | Ideal Settings | Notes |
---|---|---|---|
Pulsed MIG Welding | Improved control, smoother beads | 2-4 Hz pulse frequency | Great for thin materials |
Multi-Pass Techniques | Thicker welds, greater strength | 180-220 amps | Ensure good fusion between layers |
Stringer Beads | Tighter, more precise stacks | Consistency is key | Best for narrow joints |
Backhand Technique | Better heat distribution | Adjust angle based on bead size | Requires practice |
That covers advanced methods for stacking dimes in MIG welding. Let’s now take a look at frequently asked questions.
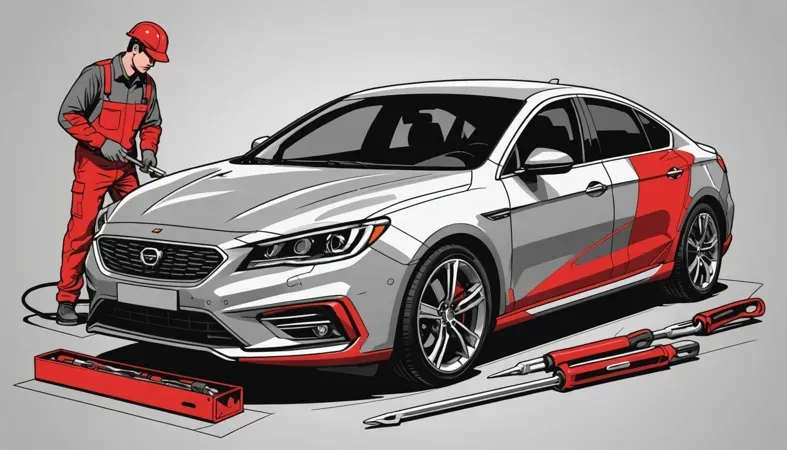
Frequently Asked Questions (FAQs)
Now let us look at some unique questions I typically get asked.
What is the Most Common Mistake When MIG Welding?
The most common mistake when MIG welding is poor wire feed speed. When the wire feed is too slow, it can lead to inconsistent weld beads. Ideally, the wire should feed at approximately 9-12 inches (23-30 Cm) per minute for optimal results. Additionally, understanding the power consumption requirements can enhance efficiency, such as knowing how many watts a welder uses.
What Does “Stacking Dimes” Mean?
“Stacking dimes” means achieving a series of evenly spaced, dome-shaped weld beads. This term highlights a high-quality weld appearance. Welders aim for this to show skill and precision, which helps in inspections and enhances project aesthetics.
How Do You Improve MIG Welding Technique?
You can improve your MIG welding technique by adjusting your travel speed and angle. Maintaining a consistent travel speed of about 8-12 inches (20-30 Cm) per minute allows for better bead control. Keep a travel angle of around 15-20 degrees for optimal penetration. Understanding different techniques can enrich your skills, such as knowing how to build an arc welder with a microwave transformer.
What is the Best Way to Setup a MIG Welder?
The best way to setup a MIG welder includes adjusting the gas flow rate and wire feed speed to match the material thickness. For mild steel, set the gas flow to about 15-20 cubic feet per hour (CFH). This ensures optimal shielding and reduces porosity. A comprehensive look at key components of a semiautomatic welding system can further enhance your welding setup.
How Can I Prevent Burn-through When Welding?
You can prevent burn-through when welding by using a lower heat setting and moving quickly across the weld seam. For thinner materials, use a voltage below 18 volts to minimize heat input. This helps protect the base material from excessive melting and warping.
What Materials Can I MIG Weld?
You can MIG weld a variety of materials like mild steel, stainless steel, and aluminum. Mild steel is the most common, with a thickness of 0.030-0.145 inches (0.76-3.68 mm) being typical for many projects. Each material requires specific MIG settings for successful welding. Properly setting up your equipment can make a significant difference, especially when you learn how to wire a 220 outlet for a welder, which is crucial for the performance of your welding machine.
Conclusion
That’s everything I wanted to share with you. We covered topics like what stack dimes are, types of stack dimes in MIG welding, the steps to stack dimes, and factors that affect stacking. Remember the importance of practice and technique to lay those perfect dimples.
To stack dimes in MIG welding, you need to control your speed, travel angle, and wire feed. Properly adjusting your welder settings can make a significant difference. With the right approach, you’ll consistently create those desirable dime-shaped beads.
Thank you for exploring these insights; if you’d like to delve deeper into the world of welding, visit What is Welding for more valuable resources.
References
- American Welding Society (AWS): https://www.aws.org
- Blodgett, O. W. (1996). Design of Welded Structures. Cleveland, OH: James F. Lincoln Arc Welding Foundation.
Joe Carter is a retired welding professional with over 40 years of hands-on experience in the industry, spanning ship repair, structural welding, and even underwater projects. Joe is a master of MIG, TIG, and Stick welding. Passionate about mentoring the next generation of welders, Joe now shares his decades of expertise and practical insights to help others build rewarding careers in welding.
American Welding Society, Metalworking, MIG Welding, Stacking Dimes, Welding, Welding Equipment, Welding Techniques, Welding Tips, Wire Feed Speed