How to Remove Spot Welds? Steps, Methods, and Precautions
Published on: February 3, 2025 | Last modified: March 4, 2025
By: Joe Carter
Spot welds are a way to join two pieces of metal together. They’re created using heat and pressure, producing strong, permanent bonds.
This is a question we frequently get: how to remove spot welds? It’s crucial to know this for any metalwork project because improperly removed spot welds can damage components. In my experience, following the right method saves time and frustration when working on repairs or modifications.
In this guide on how to remove spot welds, we’ll go over the types of spot welds, necessary tools and prerequisites, step-by-step instructions, essential precautions, various methods, factors that affect removal, and common issues you might face. We’ll also discuss aftercare, benefits of removal, typical applications, and even explore some alternatives that might work better. Whether you want to know how to cut spot welds or how to drill spot welds, we’ve got you covered!
Contents
- How to Remove Spot Welds?
- What Are Spot Welds?
- Types Of Spot Welds
- Prerequisites
- Essential Precautions
- Steps for Removing Spot Welds
- Types Of Methods for Removing Spot Welds
- Factors Affecting Spot Weld Removal
- Advanced Techniques for Spot Weld Removal
- Common Issues
- Aftercare, Inspection, and Advanced Tips for Removing Spot Welds
- Benefits Of Removing Spot Welds
- Typical Applications Of Spot Weld Removal
- Alternatives That Might Work Better
- Frequently Asked Questions (FAQs)
- Wrap Up
- References
How to Remove Spot Welds?
Spot welds are small, fused metal joints. To remove spot welds, use a spot weld cutter or drill to penetrate and separate materials—typically found in auto body work. It’s not hard with practice, but it takes patience.
What Are Spot Welds?
a common type of weld, mainly used in sheet metal applications. They form when two metal surfaces are electrically fused together at specific points. Typical spot welds are made using a welding machine that applies heat through resistance. They generally have a strength of about 45,000 psi (310 Mpa) for mild steel.
Removing spot welds can be tricky. Using special tools like spot weld chisels and drill bits makes this task much easier. In my experience, a spot weld removal tool saved me time and effort during a car restoration project.
I found it handy when I needed to separate spot welds on an auto body. While working on my old truck, I discovered the value of quickly cutting spot welds. It helped me a lot during the job, ensuring I left the surrounding areas intact while removing spot-welded panels without damage.
Types Of Spot Welds
What are the different types of spot welds?
-
Projection Welds
Projection welds use a raised area to create a bond between two pieces of metal. To separate them, use a spot weld removal chisel gently at the projection’s edges. Tap the chisel lightly; as it penetrates, move along the joint to cut through the weld smoothly.
-
Seam Welds
Seam welds connect two sheets edge-to-edge for strength. To undo them, drill through the seam with a spot weld drill bit. Start at the weld’s center and slowly drill out the material, taking care not to damage the surrounding metal.
-
Flash Welds
Flash welds form when two pieces are heated under pressure until they fuse. To cut these, use a grinder for quick removal. Steady your hand and grind along the weld line until the materials separate, ensuring an even surface.
-
Laser Welds
Laser welds use concentrated light to create a precise bond. To remove them, carefully grind down the welded area. Use fine grit for better control and to prevent warping the metal while clearing the weld.
-
Resistance Spot Welds
Resistance spot welds apply heat and pressure to a specific spot to join materials. To peel them apart, use a spot weld removal chisel or drill bit. Position your tool over the weld until it penetrates, then lightly twist to loosen the bond. When welding on a vehicle, it is crucial to be aware of the necessary precautions, including what to disconnect to ensure safety and avoid damage.
We covered various types of spot welds here. Next, we will discuss the necessary prerequisites.
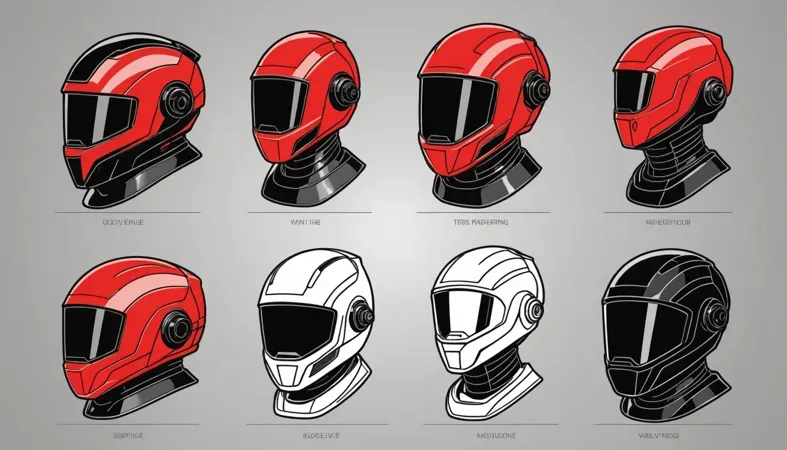
Prerequisites
What do you need to start removing spot welds?
- Spot Weld Removal Chisel: Use a specialized chisel, like the 3M Spot Weld Removal Chisel. It cuts precisely around the weld without damaging nearby materials.
- Spot Weld Drill Bit: Get a spot weld drill bit, such as the ABN Spot Weld Bit Set. It drills through the weld effectively, making removal easier and cleaner.
- Body Repair Hammer: A hammer like the ARES 440601 is essential for tapping around the weld area to break the joint, facilitating easier separation.
- Pry Bar: A pry bar, such as the TEKTON 30523, is needed to help pry apart the panels after cutting through the weld. It provides leverage and control during removal.
That covers the necessary prerequisites for the topic. Let’s now take a look at essential precautions to consider.
Essential Precautions
Let’s cover important safety measures for removing spot welds.
- Eye Protection: Always wear safety glasses to protect your eyes from sparks and debris. Choose a pair that meets ANSI Z87.1 standards.
- Ventilation: Ensure proper airflow to avoid inhaling toxic fumes from heated metal. Use a fan or work outdoors when possible.
- Fire Safety: Keep a fire extinguisher nearby, as welding can ignite nearby materials. Look for an ABC-rated extinguisher.
- Head Protection: A hard hat protects your head from overhead hazards. I recommend the MSA V-Gard Hard Hat for its durability.
Remember, these safety precautions are essential to avoid injuries. They’re vital for your well-being.
We have now covered essential precautions for safe practices. Next, we will examine the steps for removing spot welds.
Steps for Removing Spot Welds
Here are the steps to effectively remove spot welds. Follow them closely for the best results.
-
Identify Spot Weld Locations
Start by finding the spot welds. Look for small, raised areas on the metal—these usually appear where two sheets join. Use a marker or center punch to mark each spot weld, keeping a few millimeters away from the weld itself to make drilling easier. Be methodical; missing even one weld can cause damage. If you’re working with welding machines, knowing how to convert a 220V welder to a 110V setup can be highly beneficial for different project requirements. For step-by-step guidance, explore how you can convert a 220 welder to 110.
.
If you’re working on a car, spot welds are often hidden under paint and coatings. You may need to grind away surface paint or rust to expose them. Take your time; an undetected spot weld can complicate removal and might bend or break surrounding panels.
-
Drill a Pilot Hole
Next, drill a pilot hole in the center of each marked spot weld. Use a metal drill bit that matches the spot weld drill bit—usually around 5 mm (0.2 Inches) will suffice. This initial hole guides the main drill bit and prevents it from wandering. Keep your drill steady to avoid damaging the surrounding metal. It’s equally important to maintain safety by taking measures to avoid inhaling welding fumes.
Don’t rush this step. It’s crucial to stay focused and precise. A clean, accurate pilot hole sets you up for success. If you drill too deep, you risk damaging the panel underneath, so aim for a depth just beyond the weld material.
-
Remove the Weld Material
After drilling your pilot holes, switch to a spot weld removal drill bit designed for deeper penetration and easier material removal. Engage the drill bit at a slow speed and gently increase pressure as you feel the weld material break away. Keep the drill bit perpendicular to the surface.
Check your progress frequently. You can also use a spot weld chisel to knock out any leftover bits; this method can be quicker and more effective than drilling out every piece of weld material. If you’re drilling on thinner panels, watch for excessive heat that can warp the metal—you want that panel intact!
-
Inspect the Area
After removing the welds, carefully inspect the area for any remaining material or damage. You want a clean surface for reassembly or modifications. Feel along the edges where the panels join; even small remnants can cause issues later. A smooth finish ensures everything lines up perfectly during reassembly.
Now’s a good time to clean the area with a wire brush or grinder to remove any slag or debris. Ensure the cleaned surface is suitable for welding or painting for a strong final assembly. Don’t skip this step; a little time spent now will prevent headaches later.
You should now have a good understanding of how to remove spot welds. In the next part, we’ll discuss various methods for removal.
Types Of Methods for Removing Spot Welds
Let’s explore methods for removing spot welds, including drilling, grinding, cutting torches, plasma cutting, and chiseling.
-
Drilling Methods
Drilling out a spot weld is a common choice. Use a spot weld drill bit with a pilot point to center the hole. Typically, set the drill speed to around 2000 RPM (Revolutions Per Minute) for optimal results.
-
Grinding Techniques
Grinding is an effective method. A grinding wheel grinds down the spot weld until the pieces separate. Be cautious, as this can produce a lot of heat and may warp the metal.
-
Cutting Torch Methods
A cutting torch uses intense heat to remove welds. This method requires skill to control the flame precisely. It’s faster than drilling but can damage surrounding areas if not handled carefully.
-
Plasma Cutting Techniques
Plasma cutting is advanced. It uses ionized gas to melt through metal. This method is efficient for thicker materials but requires a power supply and proper safety gear.
-
Chiseling Approaches
Chiseling is a manual method suitable for delicate jobs. Use a chisel to separate the parts with steady pressure. It may take longer but provides better control.
Factors Affecting Spot Weld Removal
What factors influence the removal of spot welds? Here’s a breakdown.
-
Material Thickness
Thicker materials need more power and time to cut through. For instance, working with metal that’s 2 mm (0.079 In) thick may require a stronger tool compared to 1 mm (0.039 In) thickness.
-
Weld Size
The size of the weld matters. Larger spots, especially those over 9.5 mm (0.375 In), can be harder to separate than smaller ones.
-
Weld Quality
Weld quality is crucial. A poorly done weld may not break cleanly, while high-quality spot welds usually offer a smoother removal process, reducing metal damage.
-
Tool Type
Your choice of tool affects the process. Using a spot weld removal drill bit is often more effective than a standard drill. These specialized tools provide higher precision and ease of use.
-
Heat Treatment
Prior heat treatments can weaken the weld. Applying heat may soften the metal around the spot weld, making removal easier. However, excessive heat can warp surrounding material.
Advanced Techniques for Spot Weld Removal
Let’s dive into some advanced techniques for removing spot welds. These methods can save you time and improve the quality of your work.
Technique | Description | Advice | Typical Use |
---|---|---|---|
Spot Weld Cutter | Specialized tool that drills out spot welds cleanly. | Use a constant speed of 2500 to 3000 RPM for best results. | Auto body repair, sheet metal work. |
Oxy-Acetylene Torch | Intense heat burns through welds quickly. | Practice control to avoid heat damage to surrounding areas. | Thick metal applications. |
Rotary Tool with Cutting Wheel | Grinds down the weld area precisely. | Keep the tool steady to maintain control and precision. | Detailed work on thin materials. |
Plasma Cutter | Utilizes ionized gas to remove spot welds effectively. | Ensure you wear proper protective equipment; the sparks can be intense! | Heavy-duty projects requiring quick removal. |
Heat Gun Method | Applying heat to soften the weld for easier removal. | Maintain moderate heat; excessive can warp the surrounding metal. | Delicate areas where precision is critical. |
By employing these techniques, you can enhance your efficiency and achieve cleaner results in your spot weld projects. The right method can make all the difference!
Common Issues
Let’s look at the unique problems affecting spot welds.
-
Inadequate Tooling
Spot welds suffer from poor tooling, causing inconsistent weld quality. Use the correct electrode diameter and pressure. Monitor voltages around 5.5 kV (5,500 V).
-
Heat Damage to Surrounding Metal
Spot welds can cause heat damage. Cooling time is crucial to avoid warping. Keep cooling methods like air or water quenching on hand.
-
Incomplete Weld Removal
Spot welds may be only partially removed, leaving residual metal. Check for remaining spots with a marker and follow up with physical removal methods.
-
Accidental Damage to Adjacent Parts
During removal, spot welds can harm nearby components. Use shields or protective coverings to prevent damage. Pay attention to clearance before starting work.
-
Surface Imperfections Post-removal
After spot weld removal, expect surface imperfections like craters or unevenness. Use a grinder to smooth the surface and polish to restore the finish.
Aftercare, Inspection, and Advanced Tips for Removing Spot Welds
Here’s some expert advice to ensure you get the best results after removals.
Aftercare Recommendations
After detaching your spot welds, clean the area with a wire brush or an 80-grit (Grit is the Roughness Measure) grinder to remove debris and remaining weld material. Apply a rust inhibitor immediately to prevent oxidation (Rust). Ideally, use a product like VHT Rust Converter to seal exposed metal, as moisture can quickly initiate corrosion.
Inspection Procedures
Start inspection by checking for intact base metal; it should be free of cracks larger than 0.5 mm (0.02 In). Use a magnifying glass or a borescope for hard-to-see spots. Confirm previous welds didn’t weaken surrounding metal using liquid dye penetrant from CRC, which highlights tiny flaws you might miss. If none are found, you’re all set!
Expert Tips
If you’re experienced, elevate your game by using one size larger drill bit for more efficient removal; aim for about 6.35 mm (0.25 In) compared to the original weld size. Consider using heat: a nitrogen torch melting technique can simplify spot-weld removal without warping adjacent materials. For precision cutting, a rotary cutting tool with an average speed of 30,000 RPM is your best friend.
Benefits Of Removing Spot Welds
The main advantage of removing spot welds is the flexibility it provides for repairs. I found it useful when I needed to replace a damaged panel on my car.
This technique simplifies separating spot welds without harming the surrounding metal. You’ll also save time, improve the quality of your work, reduce costs, and maintain the project’s structural integrity.
Typical Applications Of Spot Weld Removal
People use techniques for removing spot welds on various projects. Here are some applications:
- Auto Body Repair: Removing spot welds to replace damaged panels is essential. This avoids costly repairs and is popular among mechanics.
- Metal Fabrication: Deconstructing assemblies in manufacturing allows for redesigns or modifications. It’s common in custom fabrication shops.
- HVAC System Maintenance: Technicians often remove spot welds to access internal components. This keeps systems running efficiently and is standard practice.
- Electronics Recycling: Spot weld removal helps recover valuable materials from obsolete devices. It’s increasingly used in eco-friendly recycling efforts.
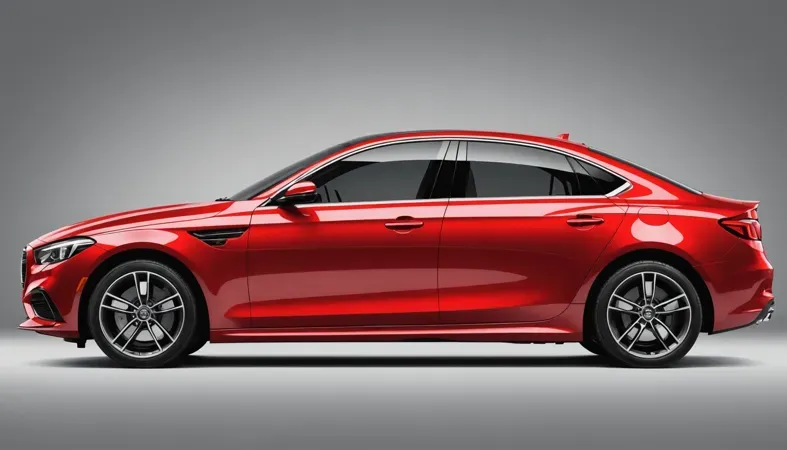
Alternatives That Might Work Better
I’d like to share what has consistently worked for me when tackling spot welds. You can try using a spot weld removal chisel, such as the OTC 6575, which provides a clean cut. In tight spaces, a spot weld drill bit can work wonders and ensure you don’t damage surrounding material.
Another option is to use a high-speed rotary tool, such as a Dremel, to grind down the welds. This method can offer more control and precision, especially on auto body panels. Remember, choosing the right tool often makes all the difference in speeding up the process and achieving a better result.
Frequently Asked Questions (FAQs)
Now let us look at some common stuff I typically get asked about spot welds.
What is the Easiest Way to Remove Spot Welds?
The easiest way to remove spot welds is by using a spot weld cutter. This tool is specifically designed to drill through the metal, allowing you to cut the weld without damaging the surrounding area. Spot weld cutters often feature a pilot drill and can be found in sizes of 6.35 mm (0.25 Inches) to 12.7 mm (0.5 Inches).
Can You Drill Out a Spot Weld?
Yes, you can drill out a spot weld. By using a suitable drill bit, it’s possible to remove the weld material. Typically, a cobalt or high-speed steel bit is used, as they withstand high temperatures and wear well.
What is the Best Tool for Spot Welds?
The best tool for spot welds is a spot welder. Spot welders create strong, localized welds quickly and easily. They come in different power levels, usually ranging from 5 kW to 20 kW, allowing you to choose based on your material thickness. When operating a spot welder, it is crucial to select the right shielding gas as it plays a significant role in ensuring weld quality and consistency. To learn about what gas is used for welding, consider this resource.
How Do You Find Spot Welds?
You can find spot welds by using a simple method called tapping. Rap the surface with a small hammer. Listen for a difference in sound. Spot welds are solid anchors, so the sound will change when you hit one. It helps you identify where to drill.
How to Separate Spot Welded Panels?
You separate spot welded panels by using a sharp chisel or grinding blade. Carefully insert the tool between the panels and tap gently. This method weakens the weld bond, helping you detach the panels safely without damage.
Wrap Up
You made it to the end. We covered key topics like what spot welds are, various types of spot welds, prerequisites, essential precautions, and specific steps for removal. We also discussed methods for removing spot welds, factors that affect removal, common issues, and aftercare tips.
To remove spot welds, remember to first locate the welds and consider methods like drilling or cutting. Use tools carefully, sticking to safety measures discussed. If you need additional advice, I’m here to help with how to remove spot welds and spread your knowledge on options like drilling out spot welds or separating panels efficiently.
For further insights and resources on welding, visit our homepage at What is Welding, where you can find more expert blogs and valuable welding advice.
References
- American Welding Society. (2015). AWS D1.1/D1.1M: Structural Welding Code – Steel. Miami, FL: AWS.
- American Welding Society. (2020). AWS Welding Handbook: Welding Science and Technology (Vol. 1). Miami, FL: American Welding Society.
Joe Carter is a retired welding professional with over 40 years of hands-on experience in the industry, spanning ship repair, structural welding, and even underwater projects. Joe is a master of MIG, TIG, and Stick welding. Passionate about mentoring the next generation of welders, Joe now shares his decades of expertise and practical insights to help others build rewarding careers in welding.
American Welding Society, Auto Body, Automotive Repair, Metal Fabrication, Metalwork, Safety Precautions, Spot Welds, Structural Integrity, Tools And Equipment, Welding, Welding Techniques