How to Calculate Welding Cost Per Inch? Cost Breakdown, Steps, and Tips
Published on: April 15, 2025 | Last modified: March 4, 2025
By: Joe Carter
Cost is what you pay for something. In welding, it’s crucial to understand since it affects project budgets.
One thing that’s regularly asked of me is how to calculate welding cost per inch. Knowing this helps you estimate project costs accurately. I remember a job where this calculation saved me and my client a lot of headaches down the line.
In this guide, I’ll explain the basics of calculating welding costs, cover types of costs in welding, outline steps to calculate welding cost per inch, share precautions, discuss factors influencing welding costs, and explore issues unique to welding. You’ll also learn about aftercare, inspection, tips, benefits, typical applications, and alternatives. So let’s dig into how to calculate weld inches on pipe and more!
Contents
- How to Calculate Welding Cost Per Inch?
- What is Cost?
- Types Of Costs in Welding Calculation
- Steps to Calculate Welding Cost Per Inch
- Steps to Calculate Welding Cost Per Inch
- Precautions
- Factors Influencing Welding Costs
- Issues Unique to Welding Costs
- Aftercare, Inspection, and Advanced Tips
- Benefits
- Typical Applications
- What Are Alternatives to Calculating Welding Cost Per Inch?
- Frequently Asked Questions (FAQs)
- Conclusion
- References
How to Calculate Welding Cost Per Inch?
Cost is the amount spent on welding per inch. To calculate the welding cost per inch, divide total expenses by weld length in inches. It typically ranges from $1 to $10 per inch, depending on project type. Difficulty grows with complexity and job size, commonly used in pipe welding.
Understanding the construction of essential components can improve welding project efficiency. One such component is a bridge rectifier, which is crucial for converting AC to DC in welding equipment. Learn how to build a bridge rectifier for an AC welder to enhance your setup’s functionality.
What is Cost?
Direct Costs
Cost refers to the total expense incurred in producing goods or services. It includes expenses like materials and labor. In welding, this means the price for consumables like filler wire or gas. It also includes wages for skilled welders, which range from $15 to $45 USD (About €14 to €42) per hour, depending on expertise. Cost definition and meaning.
Indirect Costs
Indirect costs are expenses not directly tied to a specific project, such as utility bills, shop rent, or equipment maintenance. Though not always obvious, they can account for about 20-30% of total expenses. Understanding these costs helps with accurate budgeting.
Fixed Costs
Fixed costs remain constant regardless of production volume. Examples include monthly rent for your welding shop or a leased machine. These can significantly impact overall profitability. Managing these costs is essential for a successful operation.
Variable Costs
Variable costs change based on production levels. When you weld more, you’ll spend more on materials and labor. If production decreases, these costs will drop. It’s vital to track these to effectively control your budget.
Opportunity Costs
Opportunity costs measure what you forfeit when choosing one option over another. For instance, if you choose to weld instead of taking an on-site job, what income do you lose? These hidden costs can affect your decisions in welding projects.
So, how do you calculate welding cost per inch? It’s straightforward but requires understanding both direct and indirect costs. I recall pricing jobs based solely on material costs, only to learn that neglecting labor and overhead resulted in underbidding.
I found a method useful for pricing jobs quickly and accurately. One specific instance was calculating weld inches on a pipe. This became crucial in a major project where every dollar counted; knowing how to calculate weld inches on the pipe kept my bids competitive without compromising on quality.
Types Of Costs in Welding Calculation
What types of costs should you know about?
Material Cost
Material cost includes expenses for welding supplies, such as rods or wires. To find this cost per inch, divide the total cost of materials by the total weld length. For example, if you spend $100 on materials for 50 inches of weld, that’s $2 per inch (100 / 50 = 2).
Labor Cost
Labor cost is what you pay welders for their time and expertise. To calculate this cost per inch, multiply the hourly wage by the hours worked, then divide by the total weld inches. If a welder earns $30 an hour and takes 2 hours for 20 inches, that’s $3 per inch (30 X 2 = 60; 60 / 20 = 3).
Equipment Costs
Equipment costs relate to the wear and tear on welding tools and machines. To calculate this, divide total equipment costs by the expected weld length. For example, if the equipment costs $300 and is expected to weld 300 inches, that’s $1 per inch (300 / 300 = 1).
You should now have a good understanding of the various costs associated with welding. In the next part, we’ll discuss how to calculate welding cost per inch.
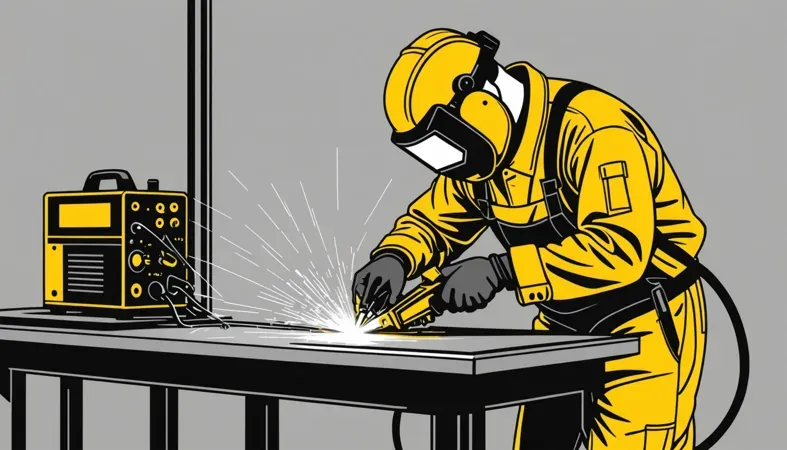
Steps to Calculate Welding Cost Per Inch
What do you need to calculate the welding cost per inch?
- Welding Cost Calculator: You need a welding cost calculator, like an Excel template. It helps you input data and get quick estimates.
- Material Pricing Guide: Use a material pricing guide, such as the 2023 Steel Prices Report. It provides current costs per kg (Or Lb), helping you budget effectively.
- Gas Flow Meter: Get a gas flow meter, such as the Harris 6240. You’ll need it to measure the flow rate of shielding gas in L/min (Or Scfh), which affects your welding price.
- Welder Hourly Rate Sheet: Have a welder hourly rate sheet, like the Bureau of Labor Statistics (BLS) report. It shows average welding labor rates in your area, which is crucial for accurate calculations.
- Operational Costs Breakdown: Compile a breakdown of operational costs, including electricity costs in kWh (Or Kw). It’s essential to factor in all your expenses.
We’ve wrapped up the steps for calculating welding costs per inch here. Next up, we’ll look at additional factors affecting costs.
Steps to Calculate Welding Cost Per Inch
Here are the steps to calculate the welding cost per inch. This guide focuses on practical actions to simplify your calculations.
Determine the Price Of the Material
Start by finding the cost of the welding material you’ll use. For MIG welding, find the price of the filler wire per pound (0.45 Kg). For instance, if it’s $20 for 5 pounds ($4 Per Pound or $8.82 Per Kg), this gives you a solid foundation for your cost calculations.
Consider different filler materials. If you change the filler, the cost can vary significantly. Stainless steel wire, for instance, can cost around $50 for the same weight. Your choice really impacts your total welding cost.
Measure the Weld Length
Next, measure the total length of the weld in inches (Cm). Use a tape measure if you’re welding pipes. For example, if a pipe measures 60 inches (152.4 Cm) long, just measure accurately to avoid costly mistakes. Reading weld symbols accurately is crucial for precision and consistency in welding projects, and knowing how to read weld symbols can significantly improve your technique.
Different joint types may vary in length. A butt joint, for example, is generally shorter than a T-joint setup. Always account for this in your total length for an accurate calculation.
Calculate the Welding Labor Cost
Now, add the labor cost. Calculate the “man-hours” needed for welding. If it takes you 2 hours to weld that 60-inch pipe and your labor rate is $50 per hour, that totals $100 in labor costs. Don’t forget that labor can add up quickly; it’s one of the biggest expenses. To optimize efficiency, understanding how to weld pipe with 6010 can be beneficial.
Estimating properly can save you from budget surprises later. If you lose an hour due to measurement mistakes, your costs will climb without you realizing it!
Combine All Costs to Find Total Cost
Now, combine all costs. Add the price of the welding material and the labor cost. If you have $20 (Material) + $100 (Labor), your total cost is $120. This is your foundational cost for that weld, helping you price future jobs. For those moving to more advanced welds, knowing how to weld effectively overhead can greatly enhance your skill set.
Don’t ignore additional costs like overhead. Account for equipment depreciation, electricity, and consumables. Over time, these hidden costs can add up to 10-15% of your total welding expenses.
So far in this section we covered the steps to calculate the welding cost per inch. In the next section we will talk about safety precautions.
Precautions
Here are essential safety tips for calculating welding costs.
- Use a calibrated measuring tool: Accurate measurements prevent errors. Consider products like the Stanley 33-725, ideal for welding inch calculations.
- Maintain a clean work area: This reduces the risk of accidents and errors. A spacious, organized bench helps tremendously.
- Verify material weight: Knowing the specific weight of materials ensures accurate costs. Use a digital scale, like the Ozeri ZK14-S, for precise measurements.
- Wear appropriate PPE (Personal Protective Equipment): Safety gear protects against sparks and heat. I recommend a Miller Welding Helmet for facial protection.
Remember, safety precautions are vital; they protect you and enhance your efficiency.
Factors Influencing Welding Costs
Next, we’ll discuss the factors affecting welding costs: Material Type, Welding Method, Project Complexity, Location of Work, and Market Demand.
Material Type
Material type is crucial. Different materials weld differently. For example, stainless steel costs about $0.90 to $1.20 (USD 2.50 – USD 3.30) per inch to weld, while mild steel costs around $0.50 (USD 1.35) per inch. To calculate the welding cost per inch, multiply the cost per inch by the total length of the weld in inches. The choice of welding rod size also impacts cost with a specific number of 1/8 7018 rod per pound affecting both materials and expenses.
Welding Method
The welding method significantly impacts costs. TIG welding, while precise, often costs more—around $1.50 (USD 4.00) per inch—due to slower speeds. In contrast, MIG welding typically costs about $0.70 (USD 1.90) per inch, as it’s quicker. Choose the method wisely to control costs.
Project Complexity
Complex projects can drive costs up. Intricate designs may require extra labor and time to fit together properly. For example, a weld taking 10 hours might cost around $2,000 (USD 5,400) due to material and labor. Always factor in time—it’s money in welding!
Location Of Work
The work location affects costs too. Welding onsite in difficult areas may incur extra costs due to transport and equipment mobilization. In contrast, welding in a shop generally allows for lower rates, averaging $0.60 (USD 1.60) per inch. Location matters—don’t overlook it!
Market Demand
Market demand significantly influences prices. During high demand, costs can rise. For instance, during a construction boom, welding prices may increase to $3.00 (USD 8.10) per inch due to the need for skilled laborers. Stay aware of market trends to save money.
We’ve wrapped up the factors that influence welding costs here. Next up, we’ll look at specific issues related to welding costs.
Issues Unique to Welding Costs
What factors shape the expenses associated with your welding projects?
Fluctuating Material Prices
Material costs can vary widely. For example, steel prices range from $0.30 to $0.80 per pound, significantly impacting your overall welding expenses.
Labor Skill Levels
Skilled welders demand higher wages. In some regions, wages average between $18 and $30 per hour, affecting costs if your projects require faster or more complex work.
Equipment Downtime
If your welding equipment isn’t operational, you’re losing money. Daily operational costs for rentals range from $200 to $500, and downtime can inflate your expenses.
Unexpected Waste
Material waste can catch you off guard. Research indicates that waste may account for 5% to 20% of total materials, directly affecting how you estimate your weld length.
Regulatory Compliance Costs
Approval processes and safety standards may require more upfront spending. Compliance costs can range from $1,000 to $10,000, so consider this in your planning.
We have now covered issues unique to welding costs. Next, we will examine aftercare, inspection, and advanced tips.
Aftercare, Inspection, and Advanced Tips
Let’s examine unique technical issues related to cost.
Weld Contamination Cost
Costs increase when contaminants like dirt enter the weld. Inspect for discoloration. Clean surfaces with solvents or grinders.
Under- or Over-welding Cost
Incorrect weld depth can be expensive. Measure with gauges. Rework deeper or add layers to meet specifications.
Heat Affected Zone (HAZ) Cost
A wide HAZ increases costs due to potential weakness. Use thermometers to check temperature. Adjust settings for minimum heat input.
Poor Fit-up Cost
Costs rise with poorly fitting materials. Check gaps with feeler gauges. Refit components before you start welding.
We’ve wrapped up aftercare, inspection, and advanced tips here. Next up, we’ll look at the benefits.
Benefits
Here’s valuable advice on aftercare, inspection, and expert tips for welding costs.
Aftercare Tips
After calculating the welding cost per inch, ensure proper cooling. Reduce warping by maintaining a cooldown rate of 30 °C/min (54 °F/min) for structural joints. For further insights on this process, consider reviewing additional welding guidance. Apply anti-corrosive treatment within 24 hours to minimize future repair costs using products like Rust-Oleum.
It’s essential to ensure adequate eye protection by selecting the minimum shade for arc welding to prevent eye strain and injuries.
Inspection
Start inspection by checking your weld’s bead width—aim for 5 mm (0.2 In) for strength and aesthetics. For critical jobs, use ultrasonic testing to detect internal weaknesses; it helps you avoid costly failures later. I trust my Fluke 8808A for accurate measurements every time. If you need to perform welds without standard equipment, consider exploring alternative welding techniques.
Expert Tips
If you’ve got several years of experience, focus on optimizing your filler material. Choose a wire with a diameter of 0.8 mm (0.03 In) for thicker metals; this saves money in the long run. Calculate the cost per inch precisely by tracking every welded inch and correlating it to labor—analyzing patterns reveals better efficiency. Understanding different welding techniques can enhance your work’s quality, including the process of tack welding.
We have now covered the advantages of the topic. Next, we will examine common uses and applications in various contexts.
Typical Applications
Knowing how to calculate welding cost per inch helps you budget effectively. I found it useful for work, especially when providing quotes for clients with various project sizes.
It also ensures accurate pricing, tracks productivity, saves time during estimations, and helps prevent cost overruns.
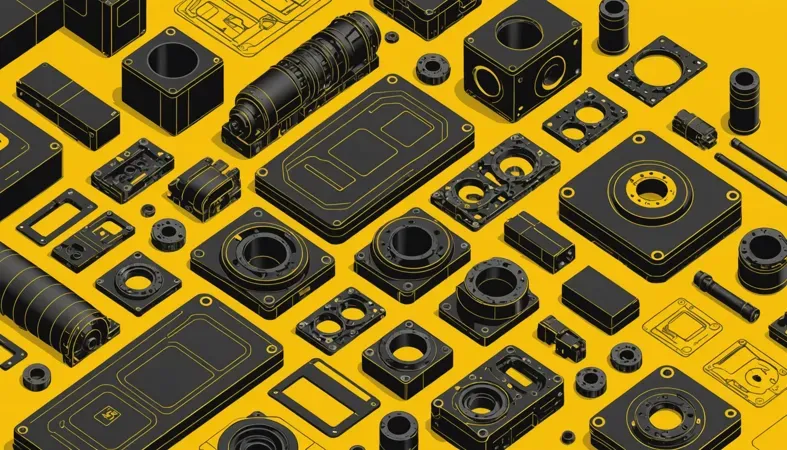
What Are Alternatives to Calculating Welding Cost Per Inch?
I’ve seen people use effective strategies for pricing welding jobs. Here are some practical applications:
- Pipe Fabrication: Contractors often calculate welding costs per inch for pipe welding projects. This ensures budget accuracy and material tracking, especially popular in the oil and gas industry.
- Automotive Customization: Shops estimate the cost of custom welds in automotive fabrication using this method. It allows for precise bids and competitive pricing in a thriving market.
- Structural Steel Erection: Calculating per-inch welding costs streamlines project management for structures. This method is widely adopted in the construction industry for its efficiency.
- Manufacturing Production Lines: In high-volume manufacturing, knowing the per-inch costs ensures profitability. Many plants use this for better financial forecasting.
Frequently Asked Questions (FAQs)
There are alternatives to calculate welding costs effectively. For instance, using tools like the Welding Cost Calculator Excel can save time for larger projects. Also, cost estimation PDFs provide relief from manual calculations, making it easier to budget accurately.
Some professionals prefer automated systems like MIG/TIG welding cost calculators. They offer real-time analysis and can adapt to various welding parameters. These methods aren’t just efficient; they have consistently worked for me when diving into complex projects with numerous welding inches.
Conclusion
We’ve reached the end, and I appreciate you sticking around. We covered how to calculate welding cost per inch, types of costs, the calculation steps, precautions, factors influencing costs, unique issues, inspection tips, benefits, typical applications, and alternatives to this process. You now have a good grasp of the essential elements needed to figure things out accurately.
To summarize how to calculate welding cost per inch, you’ll want to add up costs like labor, materials, and overhead, then divide by the total weld length in inches (Cm). Remember, if you take into account all the factors we discussed, like types of joints and work area specifics, you’ll get a clearer picture. Wishing you success in your welding projects; I hope you’ll find this information useful and easy to apply.
For further insights and resources on welding, feel free to visit our homepage: What is Welding.
References
- ISO. (2017). ISO 3834: Quality Requirements for Fusion Welding of Metallic Materials. Geneva, Switzerland: ISO.
- International Organization for Standardization. (2017). ISO 3834: Quality Requirements for Fusion Welding of Metallic Materials. Geneva, Switzerland: ISO.
Joe Carter is a retired welding professional with over 40 years of hands-on experience in the industry, spanning ship repair, structural welding, and even underwater projects. Joe is a master of MIG, TIG, and Stick welding. Passionate about mentoring the next generation of welders, Joe now shares his decades of expertise and practical insights to help others build rewarding careers in welding.
Cost Per Inch, Pipe Welding, Project Management, Safety Tips, Welding, Welding Budgeting, Welding Cost Calculation, Welding Equipment, Welding Expenses, Welding Techniques