Can You Weld Copper to Copper? Key Considerations, Methods, and Applications
Published on: January 17, 2025 | Last modified: March 4, 2025
By: Joe Carter
Copper is a reddish-brown metal known for its excellent conductivity and resistance to corrosion. It’s widely used in electrical wiring and plumbing.
A common inquiry I receive is can you weld copper to copper? This topic’s crucial because proper welding technique ensures strong, reliable joints. In my experience, following best practices in welding can prevent issues down the line.
In this guide, I’ll cover what copper is, types and their weldability, essential prerequisites, steps to weld successfully, safety tips, types of welding processes, factors impacting the welding of copper, common issues, aftercare and inspection tips, advantages of welding, applications, and alternatives. We’ll even touch on related topics like can you weld copper to steel and more!
Contents
- Can You Weld Copper to Copper?
- What is Copper?
- Types Of Copper and Their Weldability
- Prerequisites to Keep in Mind
- Considerations for Welding Copper to Copper
- Steps to Weld Copper to Copper
- Safety Tips
- Types Of Welding for Copper to Copper
- Factors Affecting Copper Welding
- Typical Issues in Welding Copper
- Aftercare, Inspection, and Advanced Tips for Welding Copper to Copper
- Why This is Worth It: Advantages
- Applications You Should Know About
- Alternatives That Might Work Better
- Frequently Asked Questions (FAQs)
- Conclusion
- Additional Reading
Can You Weld Copper to Copper?
Yes, you can weld copper to copper, but it’s tricky. Copper has a high thermal conductivity, which makes it difficult to fuse. The best way is using TIG (Tungsten Inert Gas) welding for strong, clean joints.
What is Copper?
Copper is a versatile metal known for its excellent electrical and thermal conductivity. It has a tensile strength of about 210 MPa (30,000 Psi) and a melting point of 1,984°F (1,085°C). This reddish-brown metal makes up about 0.0068% of Earth’s crust by weight. A key advantage of copper is its resistance to corrosion, making it ideal for various applications, including wiring and piping.
You might wonder about welding techniques for copper. In my experience, welding copper to copper poses unique challenges due to its high thermal conductivity. When connecting two pieces, maintaining the right heat flow can be tricky. Additionally, improper setup can lead to weak joints.
I can’t tell you how often I’ve used copper in different projects. For example, I once helped install a copper plumbing system, which involved connecting copper pipes to steel ones. This taught me that while welding copper to copper is tough, understanding how it interacts with other metals, like steel, is just as important.
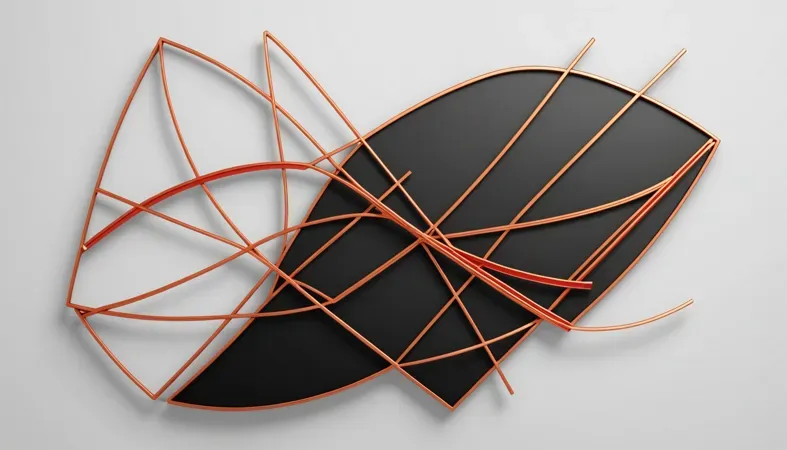
Types Of Copper and Their Weldability
What types of copper will you work with?
-
Copper C10100
Copper C10100 is high-purity, oxygen-free copper used in electrical applications. You can weld this type successfully. Use TIG (Tungsten Inert Gas) welding with a copper filler rod, as described in various resources on copper welding techniques. Properly clean the surface to avoid contamination.
-
Copper C11000
Copper C11000 is pure copper known for excellent electrical conductivity. You can weld C11000 effectively. Use TIG or MIG welding and manage heat to prevent warping.
-
Copper C14500
Copper C14500 contains small amounts of silver for specialized applications. You can weld it, but be cautious. Use TIG welding and maintain a consistent distance between the electrode and the copper for a strong bond.
-
Copper C17510
Copper C17510 is an alloy of copper and beryllium for added strength. You can weld this type, but it requires caution. Use a filler material compatible with beryllium copper and monitor heat closely to avoid brittleness.
-
Copper C18800
This grade of copper includes nickel for enhanced corrosion resistance. Yes, it can be welded, but use the correct method. Utilize the TIG method and choose a filler rod compatible with nickel for best results. For optimal results, it’s important to know how to see better when welding.
So far we covered the various types of copper and their weldability. Next, let’s look at important prerequisites to consider.
Prerequisites to Keep in Mind
What do you need to get started?
- TIG Welding Machine: Use a machine like the Miller Syncrowave 210 for precise heat control when welding copper to copper.
- Copper Welding Rod: Use rods such as Harris 4047 Copper Alloy. They’re essential for adding material and filling gaps in your weld.
- AC/DC Power Supply: A unit like the Lincoln Electric AC/DC Stick Welder is necessary for optimal fusion of copper. AC is often better for thinner sections.
- Cooling System: Use a water-cooled torch system to prevent overheating during welding. This helps maintain performance and quality.
We have now covered essential prerequisites for welding. Next, we will examine important considerations for welding copper to copper.
Considerations for Welding Copper to Copper
When welding copper, several factors can affect the final outcome. Let’s dive into those key considerations!
Consideration | Details | Impact |
---|---|---|
Thermal Conductivity | Copper’s thermal conductivity is about 390 W/(m·K). This means it dissipates heat quickly. | Can lead to incomplete fusion when not managed properly. |
Cleaning Methods | Use methods like wire brushing or sandblasting for effective surface prep. | Inadequate cleaning can cause poor adhesion and weak welds. |
Joint Design | Lap joints are preferred for their strength and heat distribution. | Ensure better load-bearing capability and reduce distortion. |
Cooling Rate | A slow cooling rate is essential, particularly for larger sections. | Quick cooling can create stress fractures—aim for controlled cooling. |
Filler Material | Choosing a compatible filler, like copper-silver alloy, that has about 15% silver improves joint strength. | Affects overall tensile strength and weld integrity. |
We’ve wrapped up the key factors for welding copper to copper here. Next up, we’ll look at the welding process steps.
Steps to Weld Copper to Copper
Here are the steps to weld copper together. Follow them carefully for better results.
-
Clean the Copper Surface
Start by cleaning the copper surfaces to remove dirt and corrosion. I typically use a wire brush and isopropyl alcohol. Ensure the area is moisture-free—copper can oxidize easily. Clean surfaces are essential for a strong weld; I’d say 99% of problems stem from poor preparation.
-
Choose the Right Filler Material
Select a filler material compatible with copper, such as a copper-silver alloy welding rod. This rod usually has around 15% silver content, enhancing strength and fluidity. I find a filler rod with similar thermal expansion coefficients minimizes cracking. The right filler improves results, especially for thin copper sections (Usually Less Than 6 Mm or 0.25 Inches).
-
Set Your Torch Parameters
Adjust your torch settings before welding. A good rule is to use an acetylene-oxygen mix with a 3:1 ratio—this typically produces a flame temperature of around 3,200°C (5,792°F). I recommend starting with a smaller flame to control the heat; too much heat will make the copper burn bright green. Maintain a torch distance of about 10 to 15 mm (0.39 To 0.59 Inches) from the metal surface while welding. Understanding the effects of welding on eye safety is crucial for all welders and you can learn more about welding eye damage risks.
.
-
Begin Welding at a Controlled Speed
Weld at a steady speed and maintain consistency. Aim for about 250 mm/min (10 Inches/min), especially for butt joints. An even speed affects both appearance and weld integrity. Zig-zagging slightly can help ensure proper heat penetration and fusion—just don’t drift away from your weld path.
-
Allow to Cool Gradually
Once finished, let the welded section cool naturally to avoid thermal shock. Rapid cooling can cause stress fractures. I sometimes wrap the weld in insulated cloth for a while; it helps slow the temperature drop. Patience in cooling can greatly enhance the strength of your weld.
We covered how to weld copper to copper here. Next, we will cover important safety tips.
Safety Tips
Let’s review essential precautions for welding copper.
- Wear Protective Gear: Always use gloves, goggles, and a face shield. Jackson Safety Protective Goggles can reduce injury risk by 75% during welding.
- Ventilate Your Workspace: Poor air quality can create inhalation hazards. Use a fan or weld outdoors for better airflow.
- Control Heat Settings: Excessive heat can warp copper. Set a TIG welder to 100 A to avoid overheating.
- Clean Copper Joint Thoroughly: A clean surface ensures a strong bond. Use a wire brush or grinder to remove contaminants.
Your safety is crucial; always prioritize precautions to enjoy welding.
Types Of Welding for Copper to Copper
Let’s explore the different types of welding for copper to copper: TIG Welding, MIG Welding, Oxy-Acetylene Welding, Flux-Cored Arc Welding, and Resistance Welding.
-
TIG Welding
TIG (Tungsten Inert Gas) welding uses a non-consumable tungsten electrode. It’s precise and ideal for thin copper joints. You’ll need a heat input of about 100-200 amps for effective welding.
-
MIG Welding
MIG (Metal Inert Gas) welding allows you to weld copper quickly and efficiently. It uses a continuously fed filler metal, typically 0.030 to 0.045 inches (0.76 To 1.14 Mm) in diameter. This method requires a wire feed speed of 150-300 inches per minute for optimal results. Understanding the risks involved is crucial, and you can explore how dangerous is welding to stay informed.
-
Oxy-acetylene Welding
This method combines oxygen and acetylene to produce a flame that can melt copper, reaching temperatures of about 3,200°C (5,792°F), suitable for thicker pieces. Controlling the flame is essential to avoid burning the copper.
-
Flux-cored Arc Welding
Flux-cored arc welding (FCAW) is effective for on-site welds involving copper. It uses tubular wire filled with flux. You’ll achieve good results by maintaining a voltage of 20-30 volts.
-
Resistance Welding
In resistance welding, copper pieces are clamped together and joined using electric current. This method creates heat through resistance, requiring about 3,000-5,000 amps depending on thickness. It’s a clean, efficient way to weld without filler metals.
Factors Affecting Copper Welding
What factors influence effective copper welding? Let’s dive in!
-
Material Thickness
Thickness impacts heat distribution. Thicker copper (Over 3 Mm or 0.12 In) requires more heat to weld properly, while thinner sheets (Under 1 Mm or 0.04 In) need less.
-
Welding Temperature
Welding copper requires temperatures around 950°C (1742°F). If this isn’t reached, fusion may fail, resulting in weak joints.
-
Joint Design
A lap joint is recommended for copper. It allows for better heat transfer and joint strength, especially between different copper types like oxygen-free and electrolytic.
-
Heat Input
Managing heat input is critical. Too much heat can cause burn-through, while too little prevents adequate fusion. Aim for a controlled feed rate.
-
Cooling Rate
Cooling rates affect crystal structure. Slow cooling can lead to grain growth, weakening the weld, while rapid cooling can cause cracks.
Typical Issues in Welding Copper
Let’s look at common problems when welding copper.
-
Welding Distortion
Copper’s high thermal conductivity causes distortion. Look for warped edges. To resolve this, heat the entire area evenly to reduce focused heat zones.
-
Cracking at Weld Joints
Copper joints often crack due to thermal stress. Inspect for fine cracks after welding. I recommend preheating to avoid this issue.
-
Difficulties in Achieving Fusion
Copper can pose fusion challenges due to its reflective properties. If the bead isn’t sticking well, increase the amperage and thoroughly clean the surface.
-
Higher Oxidation Rates
Copper oxidizes quickly during welding, creating a brittle layer. Check for a green tint. Removing oxide layers before welding is crucial; use proper gas shielding techniques.
-
Porosity in Welds
Copper welds can have porosity from moisture contamination. Look for tiny holes or pinholes. Keep the work area dry and use purged welds to minimize this effect.
Aftercare, Inspection, and Advanced Tips for Welding Copper to Copper
Here’s key advice on maintaining and evaluating your copper welds for longevity.
Aftercare Tips
After welding your copper pieces, immediately remove slag (Welding Debris) with a wire brush. Clean the weld area with a solution like 5% hydrochloric acid to prevent oxidation. Then, apply a cold galvanizing compound, such as Rust-Oleum Cold Galvanizing, to protect against corrosion.
Inspection Techniques
Inspect visually for any cracks or discoloration. Use a digital microscope to check for gaps larger than 0.2 mm (0.008 In). Employ x-ray inspection or a welder-friendly prism (Pen Inspection Tool) for hidden joint flaws—these can save time and money.
Expert Tips
If this isn’t your first copper welding project, consider optimizing your technique. Adjust your amperage to 150–200 A based on joint thickness, typically between 0.8 mm and 3 mm (0.031 And 0.118 In). Use silicon-bronze filler wires, like BW-4520, to enhance weld strength. Always preheat larger sections to around 200°C (392°F) for the best results.
Why This is Worth It: Advantages
The main benefit of welding copper to copper is its excellent conductivity. I can’t count how many times I’ve used it for electrical connections, ensuring they’re solid and reliable.
Moreover, this method creates strong, durable joints that can handle thermal expansion. It also offers corrosion resistance, simplifies repair work, and keeps costs down compared to other welding methods.
Applications You Should Know About
I’ve used copper welding in electrical work, but it has many applications, such as:
- Electrical Connections: Copper is crucial for making durable electrical connections. Its excellent conductivity makes it ideal for high-power applications.
- Heat Exchangers: In HVAC (Heating, Ventilation, and Air Conditioning) systems, welding copper pipes creates efficient heat exchange systems that enhance climate control.
- Radiators: Welded copper radiators are common in automotive applications. They dissipate heat effectively, keeping engines cool under stress.
- Artistic Sculptures: Artists use copper welding to create stunning metal artworks. The fusion allows for intricate designs and strong structures, ensuring durability.
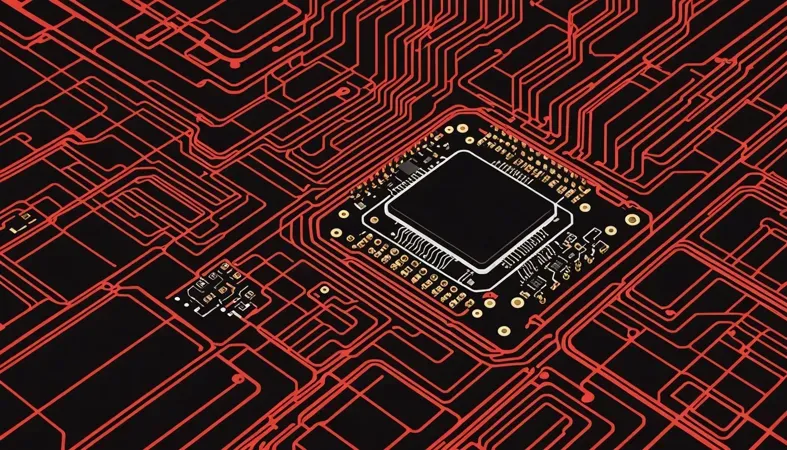
Alternatives That Might Work Better
If you’re looking for alternatives, soldering is a great option for joining copper. Products like Harris Stay-Brite or JB Weld might be your go-to for a strong bond without heat damage. After countless attempts and adjustments, I’ve figured out that soldering often provides enough strength for plumbing or electrical applications.
Another solid method is brazing, using materials like Sil-Fos® or Phos-Copper. They work well when you need to fill gaps and produce a robust joint. Plus, these methods generally require less heat, so they’re perfect for heat-sensitive items.
Frequently Asked Questions (FAQs)
Now let us look at some common questions I typically get asked.
Can You Weld Copper to Steel?
Yes, you can weld copper to steel. However, it requires special techniques due to the difference in melting points. Copper melts at about 1,984°F (1,085°C), while steel is around 2,500°F (1,370°C). Use titanium filler to ensure a proper bond. To achieve this, many professionals opt for specialized welding methods such as heliarc welding techniques.
Can You Weld Copper to Stainless Steel?
Yes, you can weld copper to stainless steel. This welding typically uses a dissimilar metal filler rod. The challenging difference in thermal expansion between the two materials can cause cracking, so careful control of your heat input is vital. Additionally, the process can produce harmful fumes, so it’s crucial to prevent inhaling welding fumes effectively.
What Temperature is Needed to Weld Copper to Copper?
The temperature needed to weld copper to copper is about 1,984°F (1,085°C). At this temperature, the copper structure will begin to melt. Using proper preheating techniques can help with joint integrity.
Can You MIG Weld Copper to Steel?
Yes, you can MIG weld copper to steel. This method requires a compatible filler material and careful attention to heat input. The copper’s thermal conductivity can affect the welding arc, which could lead to weld defects if not managed properly.
When working with thin metal, mastering precise techniques is crucial to prevent burn-through and other common issues; learn how to weld thin metal effectively to improve your results.
How Do You Weld Two Pieces Of Copper Together?
To weld two pieces of copper together, use either gas tungsten arc welding (GTAW) or gas metal arc welding (GMAW). Ensure you preheat the copper to about 392°F (200°C) to prevent cracking. Always choose the right filler for a strong bond. For those also interested in pipe welding, you can explore useful techniques on how to weld pipe with 6010.
Can Copper Be Welded to Aluminum?
No, you can’t directly weld copper to aluminum as they don’t metallurgically bond. Instead, use a compatible filler and a method like explosion welding for joint integrity. This process offers a unique way to combine these metals without direct welding.
Conclusion
We’ve reached the end, and I appreciate you sticking around. We covered what copper is, the different types of copper and their weldability, prerequisites for welding, steps to weld copper to copper, safety tips, types of welding methods, factors that affect copper welding, typical issues, aftercare, inspection tips, advantages of welding, applications, and some alternatives. Each section had valuable insights, making your copper welding journey clearer.
So, can you weld copper to copper? Yes, you sure can, but it requires the right method and precautions. We discussed welding techniques, safety aspects, and common challenges; just be mindful of things like heat control. Contact me if you’d like more guidance on this or related topics like welding copper to steel, aluminum, or stainless steel.
For further exploration into the world of welding, visit What is Welding.
Additional Reading
- American Welding Society. (2015). AWS D1.1/D1.1M: Structural Welding Code – Steel. Miami, FL: AWS.
- American Welding Society (AWS): https://www.aws.org
- Appleton, W. (2020). Welding and Cutting: A Practical Handbook. Hauppauge, NY: Nova Science Publishers.
Joe Carter is a retired welding professional with over 40 years of hands-on experience in the industry, spanning ship repair, structural welding, and even underwater projects. Joe is a master of MIG, TIG, and Stick welding. Passionate about mentoring the next generation of welders, Joe now shares his decades of expertise and practical insights to help others build rewarding careers in welding.
American Welding Society, Copper Welding, Electrical Applications, Pipe Welding, Safety Tips, Thermal Conductivity, TIG Welding, Welding, Welding Techniques