Can You Weld Cast Steel? Understand Weldability, Methods, and Tips
Published on: March 18, 2025 | Last modified: March 4, 2025
By: Joe Carter
I’ve been asked many times, can you weld cast steel? Knowing the answer is crucial because welding can affect the integrity of the cast. From my experience, improper welding can lead to cracks and weaknesses, so understanding the right techniques is key.
In this guide, you’ll learn how to weld cast steel, explore the types of cast steel and their weldability, go over prerequisites, follow step-by-step procedures, cover safety tips, and discover the best welding methods. We’ll discuss factors affecting weldability, common issues and troubleshooting, and aftercare tips. You’ll even see what benefits welded cast steel offers and when you might want to choose a different approach.
Contents
- Can You Weld Cast Steel?
- What is Cast Steel?
- Types Of Cast Steel and Their Weldability
- Before You Start (Prerequisites)
- Steps to Weld Cast Steel
- Safety Tips
- Types Of Welding for Cast Steel
- Factors Affecting Weldability Of Cast Steel
- Welding Techniques and Best Practices for Cast Steel
- Aftercare, Inspection, and Advanced Tips for Cast Steel Welding
- Benefits Of Welding Cast Steel
- Typical Uses Of Welded Cast Steel
- When to Try a Different Approach
- Frequently Asked Questions (FAQs)
- Conclusion
- References
Can You Weld Cast Steel?
Yes, you can weld cast steel. It’s not the easiest task due to the higher carbon and silicon content, which makes cracking a risk. To weld it, preheat the material and use low hydrogen electrodes or MIG with solid wire for the best results.
What is Cast Steel?
Cast steel is an alloy made by combining iron with carbon, typically between 0.1% and 0.6% by weight. It’s known for its strength and toughness. Cast steel has a melting point of around 1425-1540°C (2600-2800°F), depending on its composition. With a tensile strength of 370 to 700 MPa (54,000 to 102,000 Psi), it’s a popular choice for construction and manufacturing applications.
You might wonder: can you weld cast steel? That’s a great question! In my years as a welder, I’ve encountered many projects that required welding cast steel. I’ve seen both successful and challenging attempts, and it often depends on the technique and preparation used.
I had a friend who relied on cast steel for fabricating heavy machinery components. He once shared how to weld cast steel effectively using a MIG welder. He emphasized the importance of preheating and using the right electrode to ensure a strong bond. Knowing how to weld cast steel can make a real difference in durability and performance.
Types Of Cast Steel and Their Weldability
What are the types of cast steel, and how do they handle welding?
-
Alloy Cast Steels
Alloy cast steels contain elements like nickel and chromium, which give them unique properties. You can weld alloy cast steels, but preparation’s key. Preheat the metal to about 150°C (300°F) and use a low-hydrogen electrode, such as E7018, to reduce the risk of cracking.
-
Carbon Cast Steels
These are the most common cast steels and usually have good malleability. You can weld carbon cast steels with proper techniques. Clean the surface thoroughly and heat steadily to avoid stress and cracks during the process. To enhance your welding skills and tackle challenges, you might benefit from learning how to cut welds.
-
High Strength Low Alloy Cast Steels
These steels enhance strength while maintaining toughness. They’re weldable, but care is required. Heat the joint to about 200°C (392°F) before welding to minimize warping and maximize strength. For those working with edge joints, proper technique is crucial, and you can learn more about how to weld edge joints.
-
Ni-resist Cast Steels
This type is known for its corrosion resistance due to nickel content. Welding Ni-resist cast steels can be tricky, but those interested in exploring various welding techniques can benefit from understanding how to use TIG (Tungsten Inert Gas) welding effectively. Selecting a proper filler material to match the alloy composition is crucial for achieving strong joints. For more details on this process, refer to the section on welding by metals.
-
Stainless Cast Steels
Stainless cast steels have excellent corrosion resistance and durability. You can weld them, but it’s best to follow specific techniques. Use TIG welding with a filler that matches the material to avoid rusting post-weld.
You should now have a good understanding of cast steel types and their weldability. In the next part, we’ll discuss prerequisites before starting.
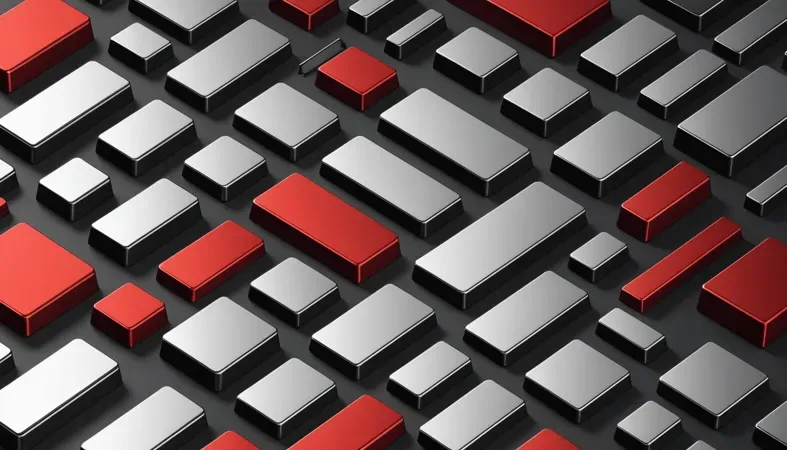
Before You Start (Prerequisites)
What do you need to weld cast steel?
- MIG Welder: Look for a machine like the Lincoln Electric PRO MIG 210. It provides a solid, consistent arc for welding cast steel.
- Welding Rod: Use a 7018 electrode, such as Hobart 7018. It’s essential for strong welds in cast steel due to its low hydrogen content.
- Purge Gas: Argon or argon/CO2 mixes, like 75% argon and 25% CO2, are critical. They prevent oxidation and ensure clean welds when TIG welding cast steel.
- Flux Core Wire: Get .030” (0.76mm) flux core wire, such as Lincoln NR-211. This is crucial for better control and usability outdoors.
So far we covered the essentials before starting. Next, let’s look at the process of welding cast steel.
Steps to Weld Cast Steel
We’ll cover the steps to successfully join cast steel to steel. Follow these closely for the best results.
-
Clean the Cast Steel Surface
Start by thoroughly cleaning the cast steel surface you plan to weld. Use a wire brush or grinder to remove rust, oil, and other impurities. Skipping this step won’t allow the weld to bond properly! A clean surface helps achieve a strong weld and reduces defects.
For best results, wipe down the cleaned area with a solvent like acetone. This reduces contaminants. Remember, a clean surface can increase your weld strength by 30%!
-
Preheat the Cast Steel
Preheating is crucial when welding cast steel. Aim for a temperature between 150°C and 260°C (300°F and 500°F). This reduces cracking and keeps your weld strong. You can use a propane torch, heat blanket, or oven for this.
Check the entire area you’re welding, not just the surface. Preheating minimizes distortion by about 50%. Skipping this can lead to weak joints!
-
Choose the Right Filler Material
Select a high-quality filler rod suitable for cast steel. Using the wrong type can weaken your weld. Options like E7018 or a specific cast steel welding rod are popular choices. These rods provide better ductility and strength.
A matched filler material makes a huge difference. Ensure your filler metal matches the properties of the cast steel. That’s the secret to strong joints!
-
Weld With Control
When you start welding, maintain a steady hand and smooth motion. Use a weaving technique for thick seams if necessary. Aim for a welding speed of about 0.2 to 0.7 m/min (8 to 28 In/min), and ensure consistent heat throughout the joint.
Watch your puddle closely and adjust as needed. If you notice cracking, stop immediately. Slow and steady wins over speed in this case! Many people push too fast and ruin their work.
-
Post-weld Heat Treatment
After finishing your weld, allow the material to cool slowly. Fast cooling can lead to significant stress and cracking. To avoid this, wrap the welded area in insulating blankets to retain heat and promote gradual cooling.
Consider performing a heat treatment for critical welds. It improves ductility, making your weld stronger. I always take the time to perform this step, as it increases my chances of success!
That covers the steps involved in welding cast steel. Let’s now take a look at safety considerations for the process.
Safety Tips
Let’s cover key precautions for welding cast steel.
- Protective Gear: Always wear a welding helmet and gloves, like Lincoln Electric K3713-1 gloves. This prevents burns and eye damage.
- Ventilation: Work in a well-ventilated area to avoid harmful fumes. Install an exhaust fan to ensure good air circulation.
- Test Materials: Inspect the cast steel for cracks before welding. Use a magnet or ultrasonic method to check its strength.
- Fire Safety: Keep a fire extinguisher nearby. Class C or D extinguishers are ideal for metal fires.
Always stay safe; I can’t stress enough how important these precautions are!We have now covered safety tips for welding. Next, we will examine the different types of welding for cast steel.
Types Of Welding for Cast Steel
Let’s explore different welding methods: MIG, TIG, Stick, Flux-Cored Arc, and Submerged Arc welding.
-
MIG Welding
MIG welding (Metal Inert Gas) uses a continuously fed wire electrode. It produces less distortion and works quickly. You can achieve quality welds on cast steel with a wire speed of 4.5 to 10.2 meters per minute (15 to 33 Feet Per Minute). MIG’s versatility and ease of use are significant advantages.
-
TIG Welding
TIG welding (Tungsten Inert Gas) offers high precision. You control the heat with a tungsten electrode and filler rod. This method is best for thinner sections of cast steel, making it an ideal choice for various applications in steel welding, using a current of 90 to 200 Amperes for proper penetration.
-
Stick Welding
Stick welding, or Shielded Metal Arc Welding (SMAW), uses a consumable electrode coated in flux. It’s ideal for outdoor conditions and can handle dirty surfaces. A typical current setting ranges from 70 to 200 Amperes for a strong bond in cast steel.
-
Flux-cored Arc Welding
Flux-cored arc welding (FCAW) employs a tubular electrode containing flux. Similar to MIG, it works well outdoors since the flux protects against contamination. This method provides excellent penetration for cast steel with amperage between 200 and 400 Amperes.
-
Submerged Arc Welding
Submerged arc welding (SAW) places the arc under a blanket of granular flux. It’s efficient for thick sections and deep welds. Weld currents often exceed 600 Amperes when working with cast steel.
When working with materials like galvanized steel, it is crucial to be aware of the potential health risks involved connected with fumes produced during welding. It is essential to understand the dangers associated with welding galvanized steel.
Factors Affecting Weldability Of Cast Steel
What factors influence your ability to weld cast steel effectively?
-
Carbon Content
The carbon content in cast steel typically ranges from 0.1% to 0.4%. Higher carbon levels can increase brittleness, making welding more challenging.
-
Heat Treatment Process
Heat treatment alters the microstructure of cast steel. Properly tempered steel can enhance weldability significantly, reducing the risk of cracking during welding.
-
Material Thickness
Thicker castings affect heat distribution during welding. They may require preheating to prevent cracks.
-
Welding Parameters
Parameters like voltage, wire feed speed, and travel speed are crucial. Proper settings can minimize distortion and improve penetration for stronger joints.
-
Joint Design
A good joint design helps distribute stress effectively. The right joint type aids in achieving better fusion and overall weld quality.
Welding Techniques and Best Practices for Cast Steel
To ensure successful welding of cast steel, applying the right techniques is essential.
Recommended Welding Techniques
-
Preheating Techniques
Preheating cast steel to about 150-260°C (300-500°F) helps reduce cracking. Use a propane torch or heat blanket for even heating.
-
Welding Speed and Motion
Maintain a speed of 0.2 to 0.7 m/min (8 to 28 in/min). Use a steady, consistent motion to achieve good penetration.
-
Interpass Temperature
Keep the interpass temperature between 120°C to 150°C (250°F to 300°F) for effective heat distribution. This prevents stress and maintains weld integrity.
-
Post-Weld Heat Treatment
Consider stress-relief heat treatment. Heat the welded joint to around 650°C (1200°F) for approximately 2 hours to improve ductility.
Common Solutions to Challenges
Here are some challenges and how to resolve them:
Challenge | Solution | Description |
---|---|---|
Cracking | Proper Preheating | Preheat the weld area to decrease internal stress and minimize cracking risk. |
Poor Penetration | Adjust Welding Parameters | Increase amperage or modify your travel speed for deeper welds. |
Porosity | Improve Joint Cleanliness | Ensure all surfaces are free of contaminants and moisture before welding. |
Advanced Techniques
For skilled welders, consider:
- Stringer Beads: Use stringer beads instead of weaving to control heat and avoid warping.
- Multiple Passes: Employ multiple passes for thicker pieces to ensure full penetration and strength.
- TIG Welding: Use TIG for precise control and to achieve high-quality welds, especially in thin sections.
These techniques can greatly enhance your projects and ensure successful joints in cast steel welding.
Aftercare, Inspection, and Advanced Tips for Cast Steel Welding
Here are crucial aftercare, inspection techniques, and expert tips for welding cast steel.
Aftercare Tips
After welding cast steel, let it cool slowly. Rapid cooling can cause cracking. Use a heat blanket to maintain the temperature at around 150°C (300°F) for at least an hour to minimize stress.
Inspection Techniques
Inspect for cracks using dye penetrant fluid, an easy test for tiny fissures. Aim for a 5 mm (0.2 In) margin and check within 24 hours after welding. I prefer using the penetrant from Magnaflux—it’s reliable!
Advanced Tips
If you’re experienced, consider tempering (Heat Treating). Heat it with a controlled ramp to about 650°C (1200°F) for 2 hours to relieve stress. Remember to check your filler metal specifications—using a specialized cast steel rod like E308 for overall strength is essential.
Benefits Of Welding Cast Steel
The ability to weld cast steel lets you repair and modify components effectively. A friend of mine relied on it to fix heavy machinery parts, saving him a lot of money.
Additionally, it offers several advantages: excellent strength in joints, improved durability, cost-effective repairs, and the capability to create custom shapes.
Typical Uses Of Welded Cast Steel
People often use welded cast steel for heavy machinery repairs. It also has several applications, such as:
- Mining Equipment: Used in welds for shovels, buckets, and frames due to its durability under high stress and wear.
- Bridge Construction: Commonly welded into structural components; it provides strength and can withstand fatigue over time.
- Aerospace Parts: Ideal for welding components like brackets and housing supports; it offers high-strength solutions for lightweight applications.
- Marine Applications: Essential for constructing ship components; its weldability and corrosion resistance make it a popular choice.
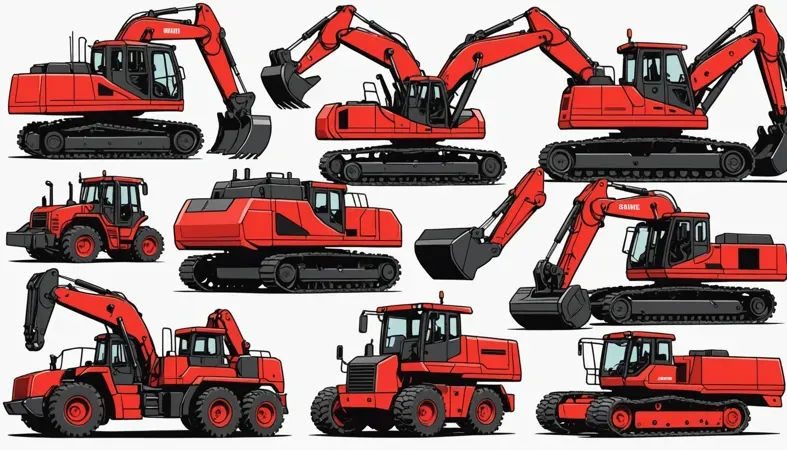
When to Try a Different Approach
Instead of welding, consider options like brazing or using adhesives like epoxy, such as Loctite epoxy. These methods can give you solid joints without the risks of warping that come with welding high-carbon cast steel. From my unique perspective, I’ve noticed that for intricate repairs, machining the parts and using fasteners often yields better results in terms of strength and appearance.
Moreover, you’re not limited to traditional welding rods. Products like the Cast Iron Repair Putty or the Muggy Weld cold welding rod can be lifesavers. Whether you’re in a tight spot or working with dense materials, these alternatives can save you time while maintaining your project’s integrity.
Frequently Asked Questions (FAQs)
Now let us look at some common questions I typically get asked.
Is It Hard to Weld Cast Steel?
Yes, it can be hard to weld cast steel. This difficulty arises from its high carbon content, typically between 2% and 4%. Moreover, the brittleness can lead to cracks if not handled properly. Understanding specific welding techniques is essential for success. Knowing the common causes of porosity in welding can significantly improve the durability of your welds. For more detailed information, visit what causes porosity in welding.
Can You Weld Cast Steel to Regular Steel?
Yes, you can weld cast steel to regular steel. You’ll need to use complementary filler materials such as low-hydrogen rods, like the E7018. Note that proper preheating and post-weld heat treatment can help mitigate the risk of cracking in this fusion. Welding thin gauge metals requires careful technique to prevent warping, and you can understand the specific steps involved by exploring how to weld thin metal.
What Welding Rod is Used for Cast to Steel?
For welding cast to steel, a common choice is the E7018 welding rod. This rod offers good strength and ductility. Additionally, it’s low-hydrogen, helping minimize cracks in the weld joint, especially when dealing with cast materials.
Will 7018 Weld Cast Steel?
Yes, the 7018 rod can effectively weld cast steel. It’s favored for its excellent mechanical properties, being an all-position low-hydrogen electrode. Use this rod with proper techniques to prevent issues like porosity and undercutting. When working with welding processes, it’s crucial to take measures against inhaling welding fumes.
What is the Best Way to Weld Cast Iron?
The best way to weld cast iron is by using nickel-based rods, like Ni-Rod 55. This significantly reduces the chances of cracking. A preheating temperature of about 260°C (500°F) can also help prepare the material for a successful weld.
How Do You Weld Cast Steel With MIG?
You can weld cast steel with MIG by using ER70S-6 filler wire. Ensure the MIG machine’s voltage is set accurately, usually around 20-25 volts. Proper handling and technique will prevent inclusions and ensure good fusion with the base metal.
Conclusion
I’m glad we could cover this together. We talked about what cast steel is, the different types and their weldability, necessary prerequisites, steps to weld, safety tips, and various welding methods. We also addressed factors affecting weldability, common issues, aftercare, benefits of welding, typical uses, and when to try a different approach.
So, can you weld cast steel? In short, yes, it’s doable. With the right preparation, like understanding the type of cast steel, using proper techniques, and keeping an eye on temperatures, you can successfully weld it. Remember, different types of cast steel can react differently—some may require preheating or specialized filler materials.
If you’re interested in diving deeper into the world of welding, What is Welding offers comprehensive insights and resources to enhance your understanding.
References
- Jeffus, L. (2020). Welding: Principles and Applications (9th ed.). Boston, MA: Cengage Learning.
- Canadian Welding Bureau (CWB): https://www.cwbgroup.org
Joe Carter is a retired welding professional with over 40 years of hands-on experience in the industry, spanning ship repair, structural welding, and even underwater projects. Joe is a master of MIG, TIG, and Stick welding. Passionate about mentoring the next generation of welders, Joe now shares his decades of expertise and practical insights to help others build rewarding careers in welding.
Cast Steel, Filler Metal, Metalworking, MIG Welding, Safety Tips, Weldability, Welding, Welding Techniques