Can You Tig Weld Aluminum? Discover Techniques, Tools, and Tips!
Published on: March 8, 2025 | Last modified: March 4, 2025
By: Joe Carter
It’s a question that often arises: can you tig weld aluminum? Understanding why this matters can help you make better decisions. I’ve seen that getting this part right can make or break a project, especially when you consider the right equipment and approach.
In this guide, we’ll cover types of aluminum and their weldability, essential tools, detailed steps for TIG welding aluminum, safety precautions, types of TIG welding methods, factors affecting your weld, addressing common problems, as well as aftercare tips and advantages of tig welding aluminum. You’ll also learn about alternatives and frequently asked questions.
Contents
- Can You Tig Weld Aluminum?
- What is Aluminum?
- Types Of Aluminum and Their Weldability
- Things You’ll Need
- Steps for TIG Welding Aluminum
- Precautions
- Types Of TIG Welding for Aluminum
- How to Address Common Aluminum Welding Issues
- Common TIG Welding Aluminum Techniques
- Aftercare, Inspection, and Advanced Tips for TIG Welding Aluminum
- Why This is Worth It: Advantages
- Applications Of TIG Welding Aluminum
- Exploring Alternatives to TIG Welding Aluminum
- Frequently Asked Questions (FAQs)
- Conclusion
- Additional Reading
Can You Tig Weld Aluminum?
Yes, you can tig weld aluminum. It can be tricky due to aluminum’s high thermal conductivity. Use a high-frequency AC setting on your TIG welder for best results. Make sure to clean the aluminum thoroughly before starting.
What is Aluminum?
Aluminum is a lightweight, silvery-white metal with the symbol ‘Al’ and atomic number 13. It’s the third most abundant element in the Earth’s crust, making up about 8.1% by weight (Approximately 27,000 Parts Per Million). It has a density of 2.7 g/cm³ (0.098 Lb/in³) and excellent corrosion resistance due to a quickly forming oxide layer on its surface. This metal is widely used in industries like manufacturing, construction, and transportation.
Can you TIG weld aluminum? That’s a popular question. I remember my first experience with TIG welding aluminum—what an adventure! It takes skill and attention to detail to get it right, along with specific settings.
A friend of mine used it to restore an old motorcycle frame. They were amazed by how well a DC TIG welder worked for aluminum. To succeed, it’s crucial to know the right techniques, like adjusting for oxidation and controlling the heat—you can’t just dive in. So, how do you weld aluminum with a TIG welder? That’s where the magic happens!
Types Of Aluminum and Their Weldability
What types of aluminum can you weld with a TIG welder?
-
6061 Aluminum
6061 aluminum is a strong, versatile alloy used in many applications, including aerospace. You can weld 6061 aluminum with a TIG welder. For best results, use pure argon (Ar) gas for shielding and set your welder between 110 and 130 amps for a thickness of 3/16 inch (4.76 mm). For further technical detail, understanding arc control settings is crucial when adjusting your welding equipment.
-
5052 Aluminum
This alloy provides good corrosion resistance and weldability, making it ideal for marine use. You can join 5052 aluminum with a TIG welder. To ensure a clean weld, clean the surface with a solvent and use 100% argon gas while welding. Perfecting techniques for challenging positions is crucial, especially when learning how to weld overhead.
-
2024 Aluminum
2024 is a high-strength aluminum but can be difficult to weld. Use caution when welding this alloy with TIG. To improve weldability, preheat to about 300°F (149°C) and use an indirect heat method to keep the heat localized during the weld. Mastering techniques such as how to forge weld can significantly enhance the quality and durability of your metalwork projects.
-
7075 Aluminum
7075 aluminum offers exceptional strength and is often used in aircraft components. You can weld 7075 aluminum, but it’s better to use a specialized filler like 4047. Prepare the surface well and keep the heat input low to avoid cracking.
-
3003 Aluminum
3003 aluminum is known for excellent workability and ductility, making it easy to weld with a TIG welder. To achieve a good weld, maintain an arc length of 1/8 inch (3.17 Mm) and use a filler that matches the alloy, like 4047. If you’re working with different welding setups, you might be interested in learning how to hook up a miller suitcase welder.
You should now have a good understanding of aluminum types and their weldability. In the next part, we’ll discuss necessary tools.
Things You’ll Need
What do you need to weld aluminum with TIG?
- TIG Welder: You need a TIG welder like the Miller Diversion 180. It’s essential for controlling heat and delivering precision when welding aluminum.
- Argon Gas: You need argon gas with at least 99.9% purity for shielding. This prevents contamination and ensures a clean weld by protecting against oxidation.
- Aluminum Filler Rods: You need filler rods, such as 4047, specifically for aluminum. They provide the right strength and compatibility with the base material.
- Tungsten Electrodes: Use 2% thoriated tungsten electrodes, like EWTh-2. They handle high heat well, ensuring a steady arc during the welding process.
We’ve wrapped up essential items for TIG welding here. Next up, we’ll look at the steps for TIG welding aluminum.
Steps for TIG Welding Aluminum
Now, we’ll cover the steps to successfully weld aluminum using TIG. Follow them closely for the best results.
-
Prepare the Work Area
First, clear your work area. Remove debris and ensure good ventilation; aluminum can create harmful fumes. A clean space minimizes distractions and helps you focus on welding. Set up a sturdy table at a comfortable height, around 90 cm (35 Inches), to avoid back strain.
Lighting’s important too. A bright area helps you see your work better. You want precision, and poor lighting can lead to mistakes. Keep your tools organized for quick access when needed.
-
Select Proper Equipment
Choose your TIG welder carefully. Opt for one that supports both AC and DC settings; this flexibility is essential for aluminum. A welder like the Vulcan Omnipro 220 offers great versatility. Ensure your welder is in good condition, as faulty equipment can lead to poor results. Don’t forget a high-quality tungsten electrode. For aluminum, a 2% thoriated tungsten (Purple) works well. Use 0.040 inches (1 Mm) diameter tungsten for precision. Ensure your welding torch is correctly set up before starting. If you need to address mistakes, knowing how to remove welds will be a valuable skill.
-
Clean the Aluminum Surface
Clean the aluminum surfaces you plan to weld. Use a dedicated stainless steel brush or a solvent like acetone to avoid contamination. This step is crucial—any dirt or oxidation can ruin your weld. Always clean right before welding to prevent re-oxidization. For enhanced results, consider mechanical cleaning methods, such as abrasive pads. After cleaning, recheck the surface; it should be shiny and free of debris. This setup ensures better penetration and less porosity in your weld. Understanding welding supplies, such as welding rods, helps in planning effective welding projects.
-
Set Up the TIG Welder
Now, set your TIG welder’s parameters. Adjust the AC balance to 60-80% cleaning action for optimal results on aluminum. Next, adjust the amperage based on the thickness of the aluminum. For example, use about 1 Amp (0.05 A) per 0.025 inches (0.64 Mm) of material thickness.
Use 100% argon shielding gas for aluminum welding. It’ll help protect the weld pool; this combo offers the cleanest finish. Test your settings on scrap aluminum before tackling the main project to save potential headaches!
-
Begin the Welding Process
With everything set, it’s time to start welding. Maintain a steady hand and watch your travel speed; a pace of about 10-15 inches (25-38 Cm) per minute works well for most applications. Keep your torch angle at about 15-20 degrees for better gas coverage. Start small and gradually adjust your technique to what feels right. Watch the puddle as you work. A shiny, fluid puddle indicates you’re doing well; if it looks rough, adjust your settings. Consistent practice on different aluminum types will dramatically improve your skills. Don’t forget to be mindful of your heat input; excessive heat can lead to distortion. Understanding various welding processes will also enhance your overall approach.
That covers the procedures for TIG welding aluminum. Let’s now take a look at safety measures and important precautions.
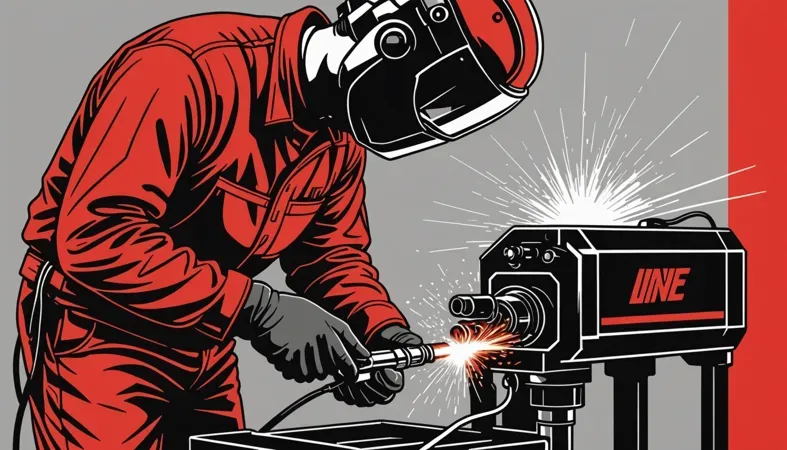
Precautions
Let’s look at crucial safety measures for TIG welding aluminum.
- Personal Protective Equipment (PPE): Always wear safety goggles, gloves, and a welding mask, like a Miller Classic. This protects you from sparks and harmful UV rays.
- Ensure Ventilation: Good airflow prevents inhaling harmful fumes. Use a local exhaust unit, such as a Quest 1000, ensuring a minimum of 3 air exchanges per hour.
- Inspect Equipment Regularly: Check your welder and torch for wear. Regular maintenance prevents malfunctions or accidents; I recommend checking them monthly.
- Safe Workspace: Keep your welding area clean and clutter-free to avoid tripping or contact with flammable materials. Aim for at least 4 m (13 Ft) of clearance around your work area.
Prioritizing safety precautions makes every welding session safer and more effective.
So far we covered safety measures. Next, let’s look at different types of TIG welding for aluminum.
Types Of TIG Welding for Aluminum
Let’s discuss the types of TIG welding: Pulsed TIG, AC TIG, DC TIG, and Scratch Start TIG.
-
Pulsed TIG Welding
Pulsed TIG welding uses a cycle of high and low current. This control allows precise heat input, reducing distortion. It’s great for thin aluminum and produces clean welds!
-
AC TIG Welding
AC (Alternating Current) TIG welding is the go-to for aluminum. It cleans the oxide layer while welding. With a welder like the Vulcan Omnipro 220, you can confidently tackle aluminum, even with varying thicknesses!
-
DC TIG Welding
DC (Direct Current) TIG welding isn’t ideal for aluminum; it’s better for materials like stainless steel. However, with the right technique, you can still weld aluminum—just know the limitations!
-
Scratch Start TIG Welding
This method involves striking the tungsten electrode against the workpiece and then lifting it slightly. It’s straightforward, but you need a steady hand to avoid contamination or uneven starts.
-
TIG Welding With Filler Rod
When you need to add material, use a filler rod during the process. This type of welding works well for joining thicker pieces of aluminum. Ensure you select the right rod—typically, ER4047 works best for aluminum..
How to Address Common Aluminum Welding Issues
Let’s look at specific problems with aluminum welding.
-
Porosity in Welds
Porosity can ruin your weld. Look for small holes in the bead. To fix this, clean the surfaces well and ensure proper gas coverage during welding.
-
Inconsistent Weld Bead
Aluminum can produce uneven weld beads. Steady travel speed and proper tungsten electrode preparation are crucial. Maintain consistency by adjusting your technique and practicing regularly.
-
Heat-affected Zone Issues
Heat can distort aluminum. Look for changes in color or texture around welds. To address this, use cooler settings and manage heat input effectively.
-
Oxidation Problems
Aluminum oxidizes quickly, leading to weld defects. You can identify a greyish-white layer. Clean the surface with a stainless steel brush or chemical cleaner before welding.
-
Filler Metal Compatibility
Using the wrong filler metal with aluminum can weaken joints. Check material specifications and use a compatible filler. Match your filler to the aluminum type, such as 4047 for heat-treatable alloys.
Common TIG Welding Aluminum Techniques
Let’s explore some key techniques that can improve your aluminum welding skills.
Key Techniques for Successful TIG Welding of Aluminum
-
Push vs. Pull Technique
When welding, you can push or pull the torch. Pushing allows for better visibility of the weld puddle, while pulling helps with heat control. Experiment to find which feels better for you!
-
Welding Rod Angle
Maintain a consistent angle of around 15-20 degrees. This angle improves gas coverage and protection against oxidation. Proper positioning reduces defects.
-
Fillers and Filler Placement
Add fillers at the right moment. When the weld puddle is molten, gradually introduce the filler rod into the leading edge. This ensures a smooth transition and minimizes defects.
-
Travel Speed Consistency
Maintain a consistent travel speed of about 10-15 inches per minute (25-38 Cm/min). Variations in speed can cause inconsistent bead size and penetration.
Quick Reference Table for Techniques
Technique | Description |
---|---|
Push Technique | More visibility; best for beginners. |
Pull Technique | Better heat control; advanced option. |
15-20° Torch Angle | Improves shielding gas coverage. |
Consistent Travel Speed | Around 10-15 inches per minute for uniformity. |
Pulsed TIG Welding | Reduces heat input; ideal for thin material. |
Aftercare, Inspection, and Advanced Tips for TIG Welding Aluminum
Here’s specialized advice to keep your aluminum projects top-notch after welding.
Aftercare Tips
After welding aluminum, cool the workpiece slowly to avoid warping. I recommend a cooling rate of about 10°C to 15°C (18°F to 27°F) per minute for thicker sections. Always clean the weld with a stainless steel wire brush or abrasive pad to remove surface oxides and contaminants.
Inspection
Inspect the weld for porosity, cracking, and discoloration. Pay close attention to welded joints, especially where you used 4047 alloy filler. A product like the Miller Sidekick Weld Check can help identify heat-affected zones. I use it regularly; its simplicity saves me time in ensuring weld integrity.
Expert Tips
Here’s a pro tip: use a dedicated aluminum root pass when welding thick sections. Set your TIG welder to 15–20 amps below the material thickness in mm (In) for full penetration. Enable high-frequency arc starts and use a 160 amp pulse to control heat input and distortion—crucial for larger aluminum pieces.
Why This is Worth It: Advantages
The main benefit of TIG (Tungsten Inert Gas) welding aluminum is its precision. A friend used it for intricate projects, and the results were stunning. Moreover, TIG welding creates clean welds, which means less cleanup. It also offers excellent control over heat input, prevents distortion, creates strong joints, and works well on thin materials. To efficiently weld thin metals, you can explore welding sheet metal techniques.
Applications Of TIG Welding Aluminum
TIG welding is widely used for crafting lightweight structures. Its applications include:
- Aerospace Component Fabrication: TIG welding’s precision makes it ideal for thin aluminum used in aircraft parts. It’s commonly used for manufacturing fuel tanks and wings, ensuring strength and lightweight characteristics.
- Marine Industry Fabrication: It’s extensively used for boat hulls and fittings. The corrosion resistance of welded aluminum prevents rust in salty environments.
- Automotive Lightweighting: In automobile fabrication, TIG welding joins aluminum frames and panels. It’s favored for its clean welds that enhance vehicle performance.
- Custom Bike Frames: Enthusiasts use it to create bespoke aluminum bike frames. The strong yet lightweight weld improves bike handling.
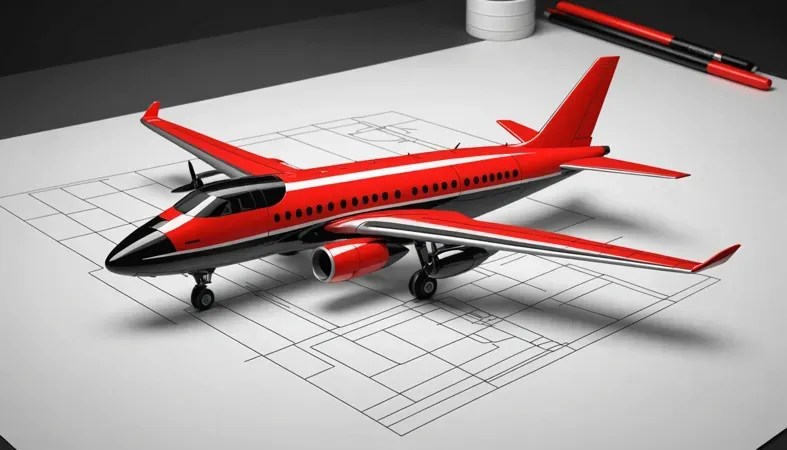
Exploring Alternatives to TIG Welding Aluminum
There are several alternatives to achieve results similar to TIG welding when working with aluminum. MIG welding, using a welder like the Lincoln Electric SP-240T, can deliver a strong bond quickly and is often easier for beginners. If you’re after portability, consider gas welding with acetylene; it’s flexible and can work well for lighter aluminum parts.
If there’s one thing I’ve gained from my journey, it’s that each method has its perks. For thick aluminum pieces, you might opt for Stick welding, especially with a machine like the Miller Multimatic 215. Choosing the right process depends on your skill level and the project’s requirements. Just keep experimenting to find what works best for you!
Frequently Asked Questions (FAQs)
Now let us look at some common questions I typically get asked.
Can You Weld Aluminum With a Regular TIG Welder?
Yes, you can weld aluminum with a regular TIG welder. Most TIG welders are designed to handle aluminum as long as they have the right settings and the proper aluminum filler rod. Ensure your welder has AC capabilities, as aluminum welding requires alternating current to stabilize the arc and produce a clean weld.
How Hard is It to TIG Weld Aluminum?
TIG welding aluminum can be challenging. It often requires precise control and technique. Aluminum has a higher thermal conductivity, which makes it easier to warp and can lead to issues with penetration if not done correctly.
Is It Better to MIG or TIG Weld Aluminum?
It depends on your project needs. TIG welding offers more control and produces cleaner welds, making it better for thinner materials. MIG welding is faster and easier, great for thicker aluminum pieces but can be less tidy in appearance. If you want to master using a welder effectively, explore our guide on how to use a welder.
How Do You Prepare Aluminum for TIG Welding?
You prepare aluminum for TIG welding by cleaning the surface thoroughly. Use a stainless steel brush or solvent to remove contaminants like dirt and oxidation. A clean surface ensures better fusion and prevents defects in the weld. Ensuring precise techniques for tasks such as welding thermocouple wire requires an understanding of specific material properties and methods. For those interested, explore the details on how to weld thermocouple wire.
Can You Weld Aluminum With DC TIG?
No, you shouldn’t weld aluminum with DC TIG. Aluminum requires AC (Alternating Current) to create a stable arc. Using DC can result in poor heat distribution and incomplete welds, making AC essential for effective aluminum welding.
Can Any TIG Welder Weld Aluminum?
Not all TIG welders can weld aluminum. You need a TIG welder with AC capabilities. Models like the Vulcan Omnipro 220 are great examples as they support both aluminum and other materials, giving you versatility in your projects.
Conclusion
That brings us to the end of our discussion on can you TIG weld aluminum. We covered what aluminum is, its types and their weldability, necessary tools, step-by-step TIG welding procedures, precautions, and various techniques. We also looked at factors that impact welding, common issues, aftercare, advantages, applications, and alternatives to TIG welding.
To answer your question again: yes, you can TIG weld aluminum. By using the right setup, such as utilizing AC on your TIG welder, and following the preparation and techniques we discussed, it’s entirely achievable. If you keep the important details in mind, like the need for a clean surface and the appropriate filler rod, you’ll be pleased with the results.
For additional welding insights and strategies, feel free to visit What is Welding.
Additional Reading
- American Welding Society. (2020). AWS Welding Handbook: Welding Science and Technology (Vol. 1). Miami, FL: AWS.
- Little, R. L. (1999). Welding and Welding Technology. New York, NY: McGraw-Hill Education.
- American Welding Society. (2020). AWS A3.0: Standard Welding Terms and Definitions. Miami, FL: AWS.
Joe Carter is a retired welding professional with over 40 years of hands-on experience in the industry, spanning ship repair, structural welding, and even underwater projects. Joe is a master of MIG, TIG, and Stick welding. Passionate about mentoring the next generation of welders, Joe now shares his decades of expertise and practical insights to help others build rewarding careers in welding.
Aluminum Welding, American Welding Society, Metal Fabrication, MIG Welding, Personal Protective Equipment, TIG Welding, Welding, Welding Equipment, Welding Safety, Welding Techniques