Can You MIG Weld Cast Iron? | Process, Tips & Techniques
Published on: January 28, 2025 | Last modified: March 4, 2025
By: Joe Carter
Cast iron is a strong material made from iron, carbon, and silicon. It’s commonly used for cookware and engine blocks due to its durability and heat retention.
A common question I hear is, can you mig weld cast iron? It’s crucial to address this because many folks find themselves working with cast iron and need to know the best methods. From my experience, understanding the right techniques and equipment can save you a lot of frustration and lead to successful repairs.
In this guide, I’ll cover the essentials of MIG welding cast iron. We’ll explore types of cast iron and their weldability, necessary prerequisites, detailed steps for welding, and key precautions. Plus, we’ll discuss factors affecting weld quality, troubleshooting common issues, and some aftercare tips. If you’re wondering how to weld cast iron with a mig welder, you’re in the right spot!
Contents
- Can You MIG Weld Cast Iron?
- What is Cast Iron?
- Types Of Cast Iron and Their Weldability
- Prerequisites to Keep in Mind
- Steps for MIG Welding Cast Iron
- Precautions
- Types Of MIG Welding for Cast Iron
- Factors Affecting MIG Welding Of Cast Iron
- Common Issues and Troubleshooting
- Common Mistakes to Avoid When MIG Welding Cast Iron
- Aftercare, Inspection, and Advanced Tips for MIG Welding Cast Iron
- Key Benefits Of MIG Welding Cast Iron
- Real-world Uses for MIG Welding Cast Iron
- Exploring Alternatives to MIG Welding Cast Iron
- Frequently Asked Questions (FAQs)
- Conclusion
- References
Can You MIG Weld Cast Iron?
Yes, you can MIG weld cast iron, but it’s tricky. Cast iron can crack due to its brittleness, so preheating helps. Use a nickel-based filler for better results. Remember, quality welds come from patience and attention!
What is Cast Iron?
Cast iron is a group of iron-carbon alloys with a carbon content over 2% by weight. It’s known for excellent castability and wear resistance. Cast iron is typically hard and brittle. It can withstand high temperatures up to 1,540°C (2,800°F), making it ideal for cookware and construction materials.
Now, let’s address MIG welding cast iron. In my experience, I’ve seen people hesitant to try this method. While MIG welding can work on cast iron, it requires careful technique to avoid cracking. It’s important to understand the material well.
Recently, I repaired a cracked cast iron skillet using a MIG welder. It was daunting, but I learned valuable tips on MIG welding cast iron. Choosing the right wire and settings made a significant difference, allowing me to restore that old skillet to functional glory. It’s always thrilling to blend artistry with technique!
Types Of Cast Iron and Their Weldability
What types of cast iron will you encounter?
-
Gray Cast Iron
Gray cast iron has a high carbon content and is brittle. You can use a MIG welder on this type, but it’s tricky. To weld gray cast iron, clean the surface, preheat to about 200°C (400°F), and use a nickel-based MIG wire for better results.
-
Ductile Cast Iron
Ductile cast iron is tougher and more flexible than gray iron. You can weld it with a MIG welder. Clean thoroughly, preheat to 260°C (500°F), and use a low-hydrogen flux-cored wire.
-
White Cast Iron
White cast iron has a very hard surface due to its carbon structure. It’s difficult to weld using MIG techniques. To fuse this type effectively, convert it to ductile iron or use solid-state welding methods.
-
Malleable Cast Iron
Malleable cast iron is treated to improve flexibility. You can weld it with a MIG machine. Clean, preheat to about 200°C (400°F), and use a nickel alloy filler material.
-
Compacted Graphite Iron
Compacted graphite iron combines the properties of ductile and gray iron. It’s weldable with MIG. Clean well, maintain a temperature of about 260°C (500°F) during welding, and choose an appropriate nickel-based filler.
That covers the different types of cast iron and their weldability. Let’s now take a look at important prerequisites to consider.
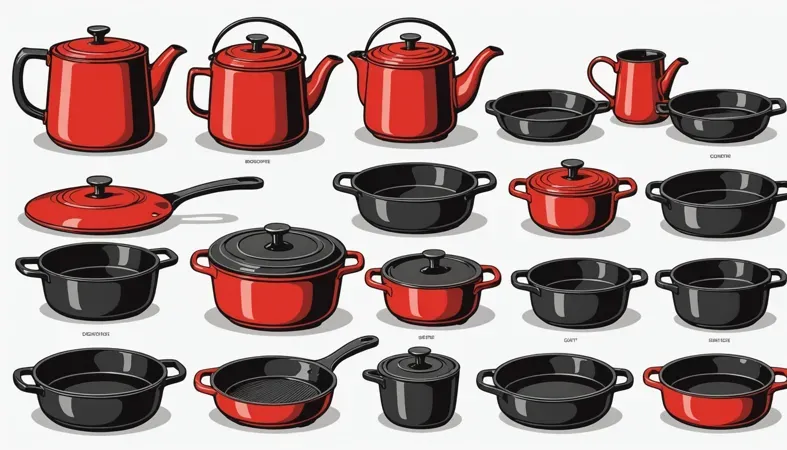
Prerequisites to Keep in Mind
What do you need before diving into can you MIG weld cast iron?
- Cast Iron MIG Wire: Use high-quality wire, like Hobart 4046 or Lincoln ERNiCrMo-3. It’s crucial for strong bonds.
- Nickel MIG Wire: Look for brands like HTP or Lincoln. Nickel wire helps prevent cracking when working with cast iron.
- MIG Welder with Energy Control: A machine like the Miller Multimatic 215 is ideal for adjusting settings on thick cast iron.
- Heat Sink Blocks: Tools like aluminum blocks help manage heat. They prevent cast iron from warping during welding.
We covered important prerequisites to consider. We will now cover the steps for MIG welding cast iron.
Steps for MIG Welding Cast Iron
Here are detailed steps for MIG welding cast iron.
-
Preheat the Cast Iron
Heat the cast iron to about 400°F (204°C) to reduce cracking during welding. Use a propane torch or a heat gun for even heating. This step is crucial—cool metal can warp!
After preheating, check the temperature with an infrared thermometer for accuracy. Keeping the weld area warm as you work reduces stress on the metal. A steady temperature improves weld quality.
-
Select Your MIG Wire and Setting
Choose a nickel-based MIG wire or high-strength cast iron wire. A wire diameter of 0.030 in (0.76 Mm) is typical for cast iron. Set your welder to DCEN (Direct Current Electrode Negative), which minimizes heat input and reduces distortion. In some cases, it may be possible to convert a 220 welder to 110, offering more flexibility for different power supplies.
Adjust the voltage and wire feed settings. For most cast iron, start with about 18-20 volts and a wire feed speed of around 200 inches per minute (5080 Mm/min). Each cast iron type may need slight tweaks, so remain flexible with your settings.
-
Begin the Welding Process
Engage the arc at the edge of the weld joint using a short arc technique. Move slowly along the joint at a consistent speed of about 4-6 inches per minute (102-153 Mm/min). Maintaining a steady hand is crucial for an even bead! Building an arc welder using a microwave transformer can provide a cost-effective solution for DIY enthusiasts.
Watch for signs of overheating, and adjust your movement if the puddle becomes too fluid. Overheating can crack the iron. Patience is key; rushing can ruin your work.
-
Use a Post-weld Heat Treatment
After welding, place your workpiece back in the preheated area for controlled cooling. Allow it to cool gradually to room temperature, ideally at a rate of 50°F (10°C) per hour. This technique significantly reduces stress cracks, which is important in various welding processes.
After it cools, conduct gentle reheating followed by a slow cooldown again. This final step creates an optimal structure that enhances weld integrity. Treat your cast iron right!
-
Check the Weld Quality
Once everything has cooled, visually inspect the weld for consistency and defects. Ensure the bead has no gaps or inclusions. If available, use a grinder to smooth out any irregularities.
If you see cracks, consider a remelt or retry with proper adjustments. Proper verification at this stage can prevent future failures.
We’ve wrapped up the steps for MIG welding cast iron here. Let us turn our attention to precautions.
Precautions
Here are essential precautions for MIG welding cast iron.
- Personal Protective Equipment (PPE): Always wear a welding helmet, gloves, and long sleeves to prevent burns. I recommend the Miller Electric Classic Series helmet for full face protection.
- Proper Ventilation: Ensure good airflow to reduce toxic fumes. A fan that moves at least 400 CFM (Cubic Feet Per Minute) works well.
- Check for Cleanliness: Clean the cast iron surface thoroughly to avoid contamination and ensure proper weld integrity. Products like wire brushes or grinders can help.
- Preheat the Metal: Preheat cast iron to at least 200°F (93°C) before welding to minimize the risk of cracking. A propane torch works well; it’s what I use.
Remember, safety won’t just keep you secure; it’ll also protect your work and effort.
So far we covered safety measures for MIG welding. Let’s look at the different types of MIG welding for cast iron next.
Types Of MIG Welding for Cast Iron
Let’s explore the different types of MIG welding for cast iron: Short Circuit Transfer, Globular Transfer, Spray Transfer, Pulse MIG, and V-Stitch Welding.
-
Short Circuit Transfer Welding
This technique involves the wire touching the molten pool, creating a short circuit. It’s popular for thinner cast iron. You can use 0.023 to 0.035 inches (0.6 To 0.9 Mm) wire with 100% argon or argon-helium gas.
-
Globular Transfer Welding
In this method, larger droplets of metal transfer from the wire to the weld, creating a hotter arc. It works well for thicker sections and usually requires a voltage above 26 volts to achieve the globular effect. You should be aware of the risks of weld flash while performing such processes as it can be hazardous without proper precautions and protection. More about this can be found in what is weld flash.
-
Spray Transfer Welding
Spray transfer uses a fine mist of molten material. It’s best for jobs requiring high quality and minimal spatter. It typically requires over 30 volts and is effective with 0.030 to 0.045 inches (0.8 To 1.2 Mm) wire.
-
Pulse MIG Welding
This advanced method alternates between high and low current, improving control and reducing heat. It’s ideal for thick cast iron. It’s often performed with a pulse rate of several pulses per second for precision.
-
V-stitch Welding
V-Stitch welding combines multiple passes in a V shape. It’s effective for uneven surfaces on cast iron. I prefer this method when strength is crucial because it enhances the bond and heat distribution.
Factors Affecting MIG Welding Of Cast Iron
What factors influence your ability to join cast iron with a welder?
-
Cast Iron Composition
Cast iron contains varying levels of carbon, silicon, and other alloys. For example, gray cast iron has 2-4% carbon, which affects its weldability.
-
Welding Technique Used
You can use MIG or TIG (Tungsten Inert Gas) techniques, but MIG is popular for its speed. The choice impacts bead formation and penetration, requiring knowledge of optimal settings.
-
Heat Input Control
Heat input is crucial. Too much heat can cause cracking in cast iron, so keep it below 500°F (260°C) to avoid damage.
-
Preheating Temperature
Preheating cast iron to about 400°F (204°C) helps reduce thermal shock and can improve weld quality while minimizing cracking.
-
Post-weld Treatment
Allow the welded area to cool slowly. Proper post-weld heat treatment can relieve stress and enhance durability.
Common Issues and Troubleshooting
Let’s look at common issues related to cast iron welding.
-
Porosity in Welds
Cast iron can develop porosity from moisture or contamination. Look for tiny holes in the weld. Clean the surfaces and use controlled pre-heat (65-93°C or 150-200°F) to resolve this.
-
Brittleness Of Welded Area
Cast iron welds may become brittle. It’s critical to use low-hydrogen electrodes. Post-weld heat treatment (Around 649°C or 1200°F) increases ductility.
-
Inadequate Fusion
In cast iron welding, inadequate fusion often results in a weak bond. Check for a lack of bevels. Ensure proper joint preparation and molten filler penetration to fix this.
-
Heat Affected Zone Cracking
Cast iron can crack in the heat affected zone due to rapid temperature changes. Look for visible cracks to identify this issue. Minimize it by controlling heat input during welding.
-
Distortion Of Base Metal
Welding cast iron can cause distortion from heat. Check for warping after welding. Prevent this by heating the area evenly to maintain uniform temperatures.
Common Mistakes to Avoid When MIG Welding Cast Iron
Even seasoned welders can stumble when working with cast iron. Here are some common mistakes to watch out for.
Mistake | Consequence | Solution |
---|---|---|
Insufficient Preheating | Higher risk of cracks due to thermal shock. | Always preheat to about 400°F (204°C) or more. |
Using Mild Steel Filler Wire | Can lead to poor bonding and weak joints. | Stick with nickel-based filler wire for better results. |
Rushing the Welding Process | Inconsistent bead appearance and higher chances of defects. | Patience is key. Take your time to ensure a quality weld. |
Overheating the Weld Area | Can create brittle areas in the weld. | Keep an eye on temperature and adjust settings as needed. |
Neglecting Post-weld Treatment | Increased likelihood of stress cracking. | Implement proper slow cooldown and tempering steps. |
Avoiding these common pitfalls will save you time and frustration, leading to stronger, more reliable welds!
Aftercare, Inspection, and Advanced Tips for MIG Welding Cast Iron
Here’s essential aftercare and inspection advice to perfect your cast iron welds.
Aftercare Tips
After welding cast iron, tempering is crucial. Heat the area to about 500°F (260°C) slowly, then cool it down to relieve stress in the joint. Use a damp cloth to prevent quick cooling, as rapid changes can cause cracking.
Inspection Essentials
Inspect the weld with a magnetic particle test for hidden cracks. Use precise products like Magnaflux penetrant to find flaws effectively. Personally, I’ve had success with TotalCheck for spot-checking small welds.
Expert Tips
Maintain a consistent travel speed of around 10 inches per minute (25 Cm/min) for better fusion. Adjust wire feed speed to at least 250 inches per minute (635 Cm/min) for optimal penetration in thick sections. Instead of standard gas mixtures, try a tri-mix of Argon, CO2, and Helium for a more stable arc.
Key Benefits Of MIG Welding Cast Iron
The biggest benefit of MIG welding cast iron is its ease of use. With a MIG welder, you can achieve clean, strong welds quickly, saving time and effort.
Additionally, you’ll enjoy numerous advantages like versatility in welding positions, reduced distortion, lower heat input, and minimal cleanup. Plus, it works well for thicker sections of cast iron, allowing for repairs or fabrications without hassle.
Real-world Uses for MIG Welding Cast Iron
I’ve seen people use MIG welding techniques to repair cast iron parts. It has several practical applications, such as:
- Automotive Repair: MIG welding can fix cracked engine blocks and cylinder heads. It’s preferred because it’s easier and faster than TIG welding for high-volume jobs.
- Tool Restoration: You can weld deteriorated tool steels in machinery. Repairing old tools is common in restoration shops.
- Heavy Equipment Repairs: It’s used to fix worn attachments and housings on trucks and tractors. This method is favored for its efficiency and strong results.
- Artistic Sculptures: Some artists use MIG welding to create sturdy yet intricate iron sculptures. It’s popular due to its design versatility.
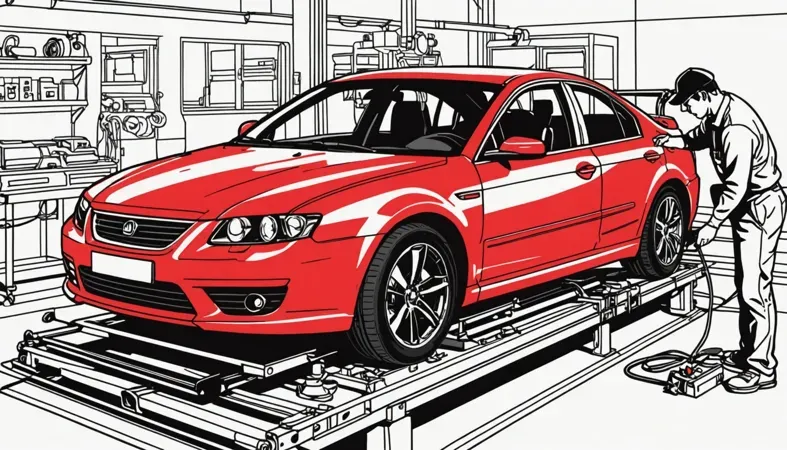
Exploring Alternatives to MIG Welding Cast Iron
There are effective alternatives to MIG methods for repairing cast iron. Techniques like TIG welding offer precise control and stronger joints instead of MIG welding. You can also use specialized rods like Nickel MIG wire or cast iron welding rods, such as Hobart or Lincoln Electric, to achieve great results without the inherent risks of cracking found in MIG welding.
If you’re dealing with intricate cast iron work, consider brazing with high-temperature silver brazing rods for better compatibility. This method—though slower—can yield robust seams that resist thermal stress. Always, remember to preheat the area to minimize the risk of fractures. Choose what’s best for your project!
Frequently Asked Questions (FAQs)
Now let us look at some common questions I typically get asked about welding cast iron.
What MIG Wire Should You Use for Cast Iron?
For MIG welding cast iron, you should use nickel-based wire. Nickel improves ductility and helps reduce cracking. A popular choice is ERNiCu-7, which is often used for its high strength and resistance to corrosion.
What Happens if You MIG Weld Cast Iron?
If you MIG weld cast iron, you risk cracking and brittleness. Cast iron’s high carbon content makes it prone to these issues. Proper preheating and using the right filler can mitigate these risks significantly.
Which Welding is Best for Cast Iron?
The best welding method for cast iron is TIG welding. TIG offers precise control with less heat input, reducing stress and cracking. While MIG can work, TIG provides better results, especially for thicker pieces. Understanding where to obtain quality materials is vital for successful welding projects. You can explore more options on where to buy metal for welding here.
Can You Weld Cast Iron With Mild Steel MIG Wire?
No, you cannot weld cast iron with mild steel MIG wire. Mild steel wire won’t bond properly and leads to joint failure. Always opt for a wire designed specifically for cast iron for successful results.
Can You Weld Cast Iron With Flux Core?
Yes, you can weld cast iron with flux core wire. This option provides some advantages like better penetration, but make sure the flux is compatible with cast iron. Pay attention to heat management to avoid cracks. For a deeper understanding of creating your own welding equipment, explore the process of making a welding machine transformer.
How to Weld Cast Iron With a MIG Welder?
To weld cast iron with a MIG welder, start by preheating the metal to about 600°F (316°C). Then, use a nickel filler rod during the welding process. This helps to prevent cracking and ensures a strong weld. A combo welder who specializes in techniques for diverse materials can provide invaluable knowledge on the subject, explaining what defines a combo welder’s role.
Can You Tig Weld Cast Iron?
Yes, you can tig weld cast iron. TIG welding offers excellent control over the heat input, minimizing stress and preventing cracks. It’s a favored method for complex or thin cast iron components. Properly cutting the welds requires specific techniques which are crucial when aiming for precision and efficiency. Discover these techniques for cutting welds in detail.
Can I Weld Cast Iron With a MIG Welder?
Yes, you can weld cast iron with a MIG welder. Just remember to use the right filler wire and keep heat management in mind. Proper techniques make a big difference in the quality of your welds.
Conclusion
We covered several important aspects about whether you can MIG weld cast iron. This included understanding what cast iron is, its types and how they can be welded, necessary prerequisites, MIG welding steps, precautions, different MIG welding methods, factors affecting weldability, common issues you might face, and aftercare tips. We also explored the benefits of MIG welding cast iron, real-world applications, and alternative welding methods.
To wrap it up, can you MIG weld cast iron? Yes, but you need to be mindful of the specific type of cast iron you’re working with, as its weldability varies. If you’re using the right filler, adjusting parameters, and following proper precautions, you’ll have a better chance of a successful weld. Feel free to reach out if you have further questions about how to effectively MIG weld cast iron.
For additional insights and expert advice on welding, don’t forget to visit our homepage at What is Welding.
References
- American Welding Society. (2020). AWS Welding Handbook: Welding Science and Technology (Vol. 1). Miami, FL: AWS.
- International Organization for Standardization. (2017). ISO 3834: Quality Requirements for Fusion Welding of Metallic Materials. Geneva, Switzerland: ISO.
Joe Carter is a retired welding professional with over 40 years of hands-on experience in the industry, spanning ship repair, structural welding, and even underwater projects. Joe is a master of MIG, TIG, and Stick welding. Passionate about mentoring the next generation of welders, Joe now shares his decades of expertise and practical insights to help others build rewarding careers in welding.
American Welding Society, Cast Iron, Metalworking, MIG Welding, Repair, Welding, Welding Equipment, Welding Safety, Welding Techniques