How to TIG Weld? Steps, Techniques, Safety Tips, and Applications
Published on: November 22, 2024 | Last modified: March 4, 2025
By: Joe Carter
TIG stands for Tungsten Inert Gas. It’s a type of welding that uses a non-consumable tungsten electrode to produce the weld.
A question that keeps coming up is how to tig weld. It’s crucial to understand this technique as it provides strong, clean welds in various materials, especially aluminum and stainless steel. I remember my first project; without proper guidance, I struggled. The outcome taught me that following the right steps transforms your work.
In this guide on how to tig weld, I’ll cover the types of TIG and their applications, prerequisites to keep in mind, steps for TIG welding, safety tips, different TIG welding techniques, factors influencing TIG quality, common issues to watch for, aftercare and inspection methods, advantages of TIG welding, its industry uses, and alternatives to TIG welding. I’ll help you learn how to weld with TIG effectively.
Contents
- How to Tig Weld?
- What is TIG?
- Types Of TIG and Their Applications
- Prerequisites to Keep in Mind
- Steps for TIG Welding
- Safety Tips
- Types Of TIG Welding Techniques
- Factors Influencing TIG Welding Quality
- Typical Problems to Be Aware Of
- Advanced TIG Welding Techniques
- Why This is Worth It: Advantages
- Industry Uses Of TIG Welding
- Alternatives for TIG Welding Techniques
- Frequently Asked Questions (FAQs)
- Conclusion
- References
How to Tig Weld?
TIG stands for Tungsten Inert Gas, a method of welding. To TIG weld, you need a TIG torch, filler rod, and a clean surface. It’s precise, but tricky; suitable for stainless steel (5-10 Mm Thick) and aluminum.
What is TIG?
TIG stands for Tungsten Inert Gas welding. It’s a process that uses a non-consumable tungsten electrode to create the weld. TIG welding uses a shielding gas, often argon, to protect the weld from contamination. It’s versatile and works with various materials, including aluminum, stainless steel, and mild steel.
So, how do you TIG weld? It’s all about mastering the technique. You need to control the heat, maintain a proper travel speed, and keep the tungsten at the right angle. In my experience, starting with thinner materials makes a big difference—it’s easier to manage and helps you learn faster.
For work, I used TIG on a project that required precision. TIG welding stainless steel gave me cleaner welds than MIG welding. When I learned how to TIG weld as a beginner, I focused on practice, ensuring my technique was solid before progressing. Ultimately, it’s about getting comfortable with your setup and understanding how heat affects different materials.
Types Of TIG and Their Applications
What types of TIG welding techniques will you encounter?
-
DC TIG Welding
DC (Direct Current) TIG welding is excellent for steel and stainless steel. Set your machine to DC polarity, then strike an arc between the tungsten electrode and the workpiece. Maintain a distance of about 1/16 inch (1.6 Mm) for optimal arc stability. In order to explore different welding techniques you might want to understand more about what is seam welding.
-
AC TIG Welding
AC (Alternating Current) TIG welding is ideal for aluminum and magnesium. Adjust your welder to the AC setting, and keep your tungsten electrode about 1/16 inch (1.6 Mm) from the metal. This ensures a clean, stable arc for melt-through.
It is crucial to understand the importance of a hot pass in welding as it significantly contributes to the strength and reliability of the weld, ensuring a robust joint. Learn more about the process of a hot pass in welding.
-
Pulsed TIG Welding
Pulsed TIG welding provides control over heat penetration, making it useful for thin materials. Set your machine to pulse mode and adjust the pulse frequency, typically around 1-10 Hz. This enables fine fusion without burn-through. When mastering this technique, it is crucial to know how to weld sheet metal effectively.
-
Root Pass TIG Welding
Root pass TIG welding starts welds in pipes. Position the tungsten near the base of the joint and keep a filler rod nearby. Use a low heat setting (Around 80-100 Amps) to create a solid bead for the initial layer. If weld corrections or modifications are needed for precision, it’s essential to know how to remove welds effectively.
-
TIG Welding With Filler Rods
This technique involves adding filler material to strengthen welds. Hold the filler at a 45-degree angle to the weld pool while keeping it about 1/16 inch (1.6 Mm) from the tungsten. Feed the rod into the pool for even distribution.
That covers the various types of TIG welding and their uses. Let’s now take a look at essential prerequisites to consider.
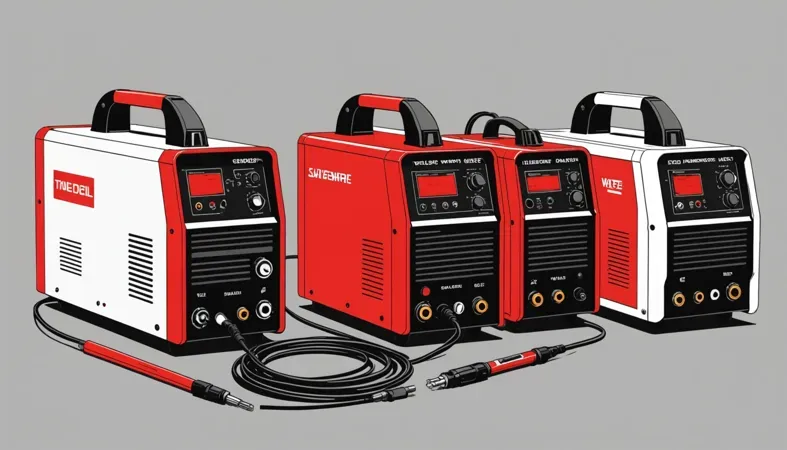
Prerequisites to Keep in Mind
What do you need to start TIG welding?
- TIG Welder: You’ll need a machine like the Miller Syncrowave 210. It’s essential for creating high-quality, precise welds.
- Tungsten Electrodes: Use 2% Thoriated Tungsten, such as 1/8” (3.2 Mm). These provide better arc stability and longer life.
- Filler Rod: Choose AER, like ER 4047 for aluminum or ER 70S-6 for steel. They fill gaps and ensure strong bonds.
- Gas Cylinder: Get a 40 cubic feet (1.1 M³) argon cylinder. It supplies the shielding gas needed for a clean weld.
That covers important prerequisites to keep in mind. Let’s now take a look at the steps for TIG welding.
Steps for TIG Welding
Here are the essential steps for effective TIG welding. Follow them for a smooth experience.
-
Prepare the Material for Welding
Start by cleaning the material’s surface thoroughly. Use a wire brush or grinder to remove rust, paint, or oil. This prevents impurities from ruining your weld. Cleanliness is crucial, especially when TIG welding aluminum—it must be spotless!
Once clean, fit the pieces together and use clamps to hold them in place. Proper alignment improves weld strength and appearance. Misaligned pieces can lead to issues later!
-
Set Up the TIG Welder
Set your welder to the correct settings. For steel, use about 110-130 amps for 1/8-inch (3.2 Mm) thickness. For aluminum, increase this to about 150-180 amps, depending on material thickness. Always check your welder’s chart for specifics.
Connect the torch and ground clamp. Ensure the Tungsten electrode size fits your project; a 1/8-inch (3.2 Mm) electrode is ideal for steel. Mismatching can lead to poor arc stability.
-
Adjust the Gas Flow Rate
Set the Argon gas flow rate. Most TIG setups work best with a flow of 15-20 cubic feet per hour (CFH). Lower settings may prevent burn-through when welding thin materials, but ensure sufficient shielding. Proper techniques are crucial when moving on to processes like forge welding, and understanding how to forge weld can enhance your welding skills significantly.
Test the gas flow by briefly igniting the arc. You want a consistent shield around the weld pool. If you see bubbles, increase the gas flow. A good gas shield is crucial for weld quality.
-
Start the Welding Process
Initiate the arc by tapping or lightly scratching the workpiece. Move the torch slowly and steadily along the joint, maintaining a distance of about 1/8-inch (3.2 Mm) from the surface for a stable arc. Practice this motion; finding the right pace is essential.
As you deposit filler rod, keep a consistent angle of around 15-30 degrees. Move smoothly to create a clean bead, ensuring proper heat penetration without burning through. Finesse takes practice, so don’t rush it!
We have now covered the process of TIG welding. The next section will discuss important safety tips.
Safety Tips
Let’s look at essential precautions for tig welding.
- Protective Gear: Always wear a helmet, gloves, and a thick jacket. I recommend the 3M Speedglas Welding Helmet.
- Ventilation: Ensure proper airflow in your workspace. Install ventilation fans if it isn’t well ventilated.
- Material Handling: Keep your work area clean and uncluttered. Avoid having flammable materials nearby.
- Electrical Safety: Double-check connections and inspect equipment regularly. I use the Miller Multimatic 215 for safe, reliable performance.
Safety precautions protect you—don’t underestimate their importance!
We have now covered essential safety tips for TIG welding. Next, we will explore various types of TIG welding techniques.
Types Of TIG Welding Techniques
Let’s explore various TIG welding techniques, including the Stringer Bead, Weaving, Circle, Peck, and Stitch methods.
-
Stringer Bead Technique
The Stringer Bead technique involves a straight, single bead of weld. Keep the torch steady while moving along the joint. This works best for materials around 1/8 inch (3 Mm) thick.
-
Weaving Technique
With the Weaving technique, create a zig-zag pattern across the joint. This effectively fills wider gaps and allows better penetration, making it ideal for materials over 1/4 inch (6 Mm) thick.
-
Circle Technique
The Circle technique uses circular motions to create round beads, allowing for better heat control. This method is great for joints requiring precision.
-
Peck Technique
In the Peck technique, progress slowly, dipping the tungsten in and out. This method is mainly used for deep groove welds, helping manage heat input and achieve thorough penetration.
-
Stitch Technique
The Stitch technique involves intermittent, short beads. Let the base metal cool between beads to prevent distortion. This is useful for welding thin metals, keeping the sections strong without warping.
Factors Influencing TIG Welding Quality
What factors affect your TIG welding process? Here’s a quick breakdown.
-
Material Thickness
Material thickness impacts heat input and fusion. Thin materials (Under 3 Mm) require precise, lower heat settings, while thicker sections (Over 5 Mm) can handle higher temperatures.
-
Electrode Type
The right electrode is crucial for quality. Use 2% thoriated tungsten for steel (Operating at 150–180 Amps), or pure tungsten for aluminum for effective arc stability.
-
Welding Speed
Adjust the speed based on the material. Too fast leads to poor penetration, while too slow causes overheating. Aim for around 15–50 inches per minute for steady beads.
-
Gas Type
Use argon for most metals. For reactive metals like titanium, a mix of argon and helium may be needed. This mix enhances coverage and stabilizes the arc.
-
Temperature Control
Maintaining optimal temperatures is key. Too hot can alter material properties, while too cool can lead to weak welds. Monitor temperatures accurately using thermocouples or infrared sensors.
Typical Problems to Be Aware Of
Let’s now look at some unique issues that can arise while using TIG.
-
Inconsistent Arc
TIG welding may show an inconsistent arc, indicated by flickering or irregular sounds. To fix this, adjust the tungsten electrode and ensure you’re using the correct amperage, usually between 10-200 A (Amperes), depending on the material.
-
Incomplete Fusion
If you notice incomplete fusion in your TIG welds, it’s often due to insufficient heat. Check the travel speed and use a slightly lower speed to improve weld penetration. Aim for a uniform bead for the best results.
-
Excessive Heat Input
TIG welding can cause excessive heat input, leading to warping. Identify this by inspecting for molten edges. You can resolve it by decreasing the amperage—typically, 1 A per 0.025 mm (0.001 In) of thickness is a good guideline.
-
Contaminated Torch and Electrode
Contamination can occur if you see black spots in your weld. This usually comes from grease on your torch or electrode. Clean your tools regularly with an appropriate solvent to maintain a clean environment.
-
Porosity in Welds
If you find porosity in TIG welds, check your shielding gas flow. Aim for a flow rate of 15-20 L/min (Liters Per Minute). Cleaning the base material can also improve quality and prevent air from entering.
Advanced TIG Welding Techniques
Let’s dive into some advanced techniques you can apply once you’re comfortable with basic TIG welding.
Technique | Description | Best For |
---|---|---|
Backhand Technique | Hold the torch at a backward angle to the weld direction. This method produces less heat and is great for thinner metals. | Thin materials and precision tasks. |
Forehand Technique | Hold the torch angled forward. This creates a hotter arc and penetrates deeper, suitable for thicker metals. | Thicker materials requiring deep fusion. |
Multi-Pass Welding | Make multiple passes to build up thickness. Each layer allows better control over heat distribution. | Materials needing increased strength, like pipes. |
Stitch Welding | Weld in short bursts, allowing the base metal to cool in between. This prevents warping and distortion. | Thin sheets and delicate projects. |
Weaving Technique | Create a zigzag motion while welding. This helps in filling wider gaps and improves penetration. | Wider joints or thicker sections. |
These advanced methods can enhance your TIG welding skills and allow for greater adaptability in various welding scenarios. They might take some practice to master, but the quality of your welds will improve significantly.
To achieve precision in your projects, understanding how to effectively join metal at precise angles, such as when executing welds on 45-degree angles, is crucial.
Why This is Worth It: Advantages
The main benefit of TIG welding is precision. It’s helped me with projects where clean, strong welds were crucial, like with thin materials or intricate designs.
You also gain versatility, improved control, enhanced weld strength, and minimal slag. These advantages make TIG welding ideal for a variety of materials, from stainless steel to aluminum.
Industry Uses Of TIG Welding
I’ve seen people use TIG welding for precision tasks. It has many unique applications, such as:
- Aerospace Components: TIG welding is used for thin materials like titanium. It’s highly precise, ensuring strong joints critical for flight safety. It’s popular due to its high-quality performance.
- Pipe Welding in Refineries: Essential for stainless steel and carbon steel pipelines, TIG offers a clean weld, minimizing contamination—a vital feature in corrosive environments.
- Artwork and Sculptures: Artists use TIG for its ability to create intricate designs in exotic metals. It’s favored by artisans seeking unique, detailed finishes.
- Thin Sheet Metal Fabrication: Extensively used in automotive part fabrication, TIG manages thin sheets well, maintaining strength without warping—important for structural integrity.
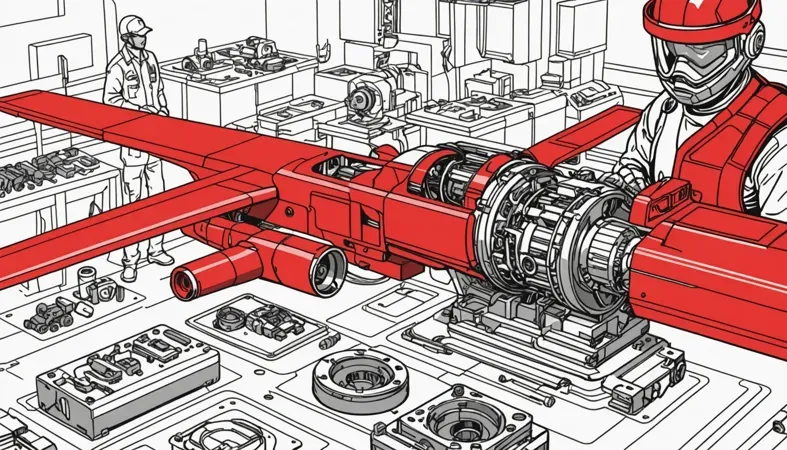
Alternatives for TIG Welding Techniques
Looking for alternatives to achieve results like TIG welding? Consider MIG welding as a quicker option for projects. It’s often preferred for thicker materials, such as steel and aluminum, because it’s faster and easier to use.
In my experience, stick welding can also replace TIG in certain settings, especially in outdoor projects. You get reliable results with less sensitivity to wind but at the cost of precision. For instance, products like Lincoln Electric’s Power MIG 210 might be just what you need for efficiency.
Frequently Asked Questions (FAQs)
Now let us look at some common questions I typically get asked regarding TIG welding.
Can I Teach Myself to TIG Weld?
Yes, you can teach yourself to TIG weld. With practice and the right resources, many welders start out as self-taught. Online tutorials, videos, and welding forums offer tips and guidelines that can accelerate your learning. Many successful welders attribute their skills to consistent practice.
What Are the Steps to TIG Welding?
The steps to TIG welding include setting up your equipment, preparing the metal, and using the torch. First, you’ll need to select the correct tungsten electrode and set your machine’s amperage. Preparing the metal involves cleaning and fitting the pieces well. Following these steps helps ensure a quality weld.
Do You Drag or Push With TIG?
With TIG welding, you typically push the torch. Pushing creates a cleaner weld pool and better penetration. This technique lets you control the arc length and maintain a stable puddle, resulting in a smoother finish and less contamination in your weld. If you wish to expand your skills, consider exploring how to use a welder effectively.
.
Is TIG Welding Good for Beginners?
TIG welding can be a good choice for beginners, depending on their goals. It provides high-quality welds and greater control. However, it requires practice to master its techniques. The precision it offers is beneficial in various applications, especially in thin materials.
How Do I Choose the Right Electrode for TIG Welding?
To choose the right electrode for TIG welding, consider the material you’re welding. For instance, use a 2% thoriated tungsten for stainless steel, or a 2% cerium for aluminum. Matching the electrode to your material improves your arc stability and weld quality significantly.
What Type Of Gas is Used for TIG Welding?
Argon gas is commonly used for TIG welding. It provides an inert shielding atmosphere, which prevents oxidation while welding metals. Typically, flow rates of 10 to 20 cubic feet per hour (CFH) are used based on the thickness of the material you’re working on.
Conclusion
I hope this was worth your while. We covered what TIG welding is, the types and their applications, prerequisites you need, steps to follow, safety tips, various techniques, factors affecting quality, typical problems, and aftercare. Plus, we discussed the advantages of TIG welding and its industry uses.
Hopefully, I was able to impart some of my experience on how to TIG weld. In simpler terms, to weld using TIG, just remember to prepare your materials, choose the right tungsten, set your gas properly, and maintain a steady hand. By following these steps, you can easily master the basics of TIG welding and create strong, precise welds.
If you’re eager to learn more about the broader world of welding, I encourage you to visit What is Welding for additional insights.
References
- American Welding Society. (2015). AWS D1.1/D1.1M: Structural Welding Code – Steel. Miami, FL: AWS.
- Lancaster, J. F. (1999). The Physics of Welding (2nd ed.). Oxford, UK: Pergamon Press.
- Cary, H. B., & Helzer, S. C. (2005). Modern Welding Technology (6th ed.). Upper Saddle River, NJ: Pearson.
Joe Carter is a retired welding professional with over 40 years of hands-on experience in the industry, spanning ship repair, structural welding, and even underwater projects. Joe is a master of MIG, TIG, and Stick welding. Passionate about mentoring the next generation of welders, Joe now shares his decades of expertise and practical insights to help others build rewarding careers in welding.
American Welding Society, Electrical Safety, Metal Fabrication, Pipe Welding, Safety Tips, TIG Welding, Welding, Welding Applications, Welding Materials, Welding Techniques