What Are Weld Wheels? Understanding, Types, and Weight
Published on: February 10, 2025 | Last modified: March 4, 2025
By: Mark Carter
Weld wheels are specialized wheels used for transporting items efficiently. They’re commonly found in workshops, helping workers move heavy equipment with ease.
So, what are weld wheels? It’s crucial to know their role in any welding project. From my experience, using the right weld wheels can drastically enhance your workflow, reducing time spent on moving materials around, ensuring safety, and maintaining project flow.
In this guide, I’ll cover important topics about weld wheels, including how they work, various types available, steps to understanding weld wheels, factors that influence their performance, and frequently asked questions. You’ll even discover how to identify weld wheels and understand how much do weld wheels weigh. Let’s dive in!
Contents
What Are Weld Wheels?
Weld wheels, often crafted from alloy, are super strong rims used in high-performance vehicles. They can handle heavy loads and tough conditions, making them popular in racing and off-roading. Their lightweight design boosts speed and handling.
Beyond automotive applications, welding also extends to specialized fields like underwater welding, raising questions about the dangers of this technique.
How Do Weld Wheels Work?
Weld wheels, also known as Weld Racing wheels, are engineered for high-performance racing. Made from aluminum, typically 6061 alloy, they offer excellent strength-to-weight properties. Typical Weld wheels weigh between 15 and 30 pounds (6.8 To 13.6 Kg), depending on size and design. They provide great structural stiffness while minimizing flex under high torque, which is crucial for racers.
When selecting Weld wheels, consider size, offset, and bolt pattern. They range from 15×6 inches (38×15 Cm) to 15×14 inches (38×36 Cm), making them versatile for various vehicles. Identifying Weld wheels by their unique design features and certifications can enhance your racing experience.
I can’t stress how vital Weld wheels are for better track performance. From personal experience, I’ve seen a weight reduction of up to 10 pounds (4.5 Kg) when switching to lighter Weld wheels, significantly boosting acceleration. Knowing the weight of Weld wheels helps optimize your vehicle’s specifications for the best results.
Types Of Weld Wheels
What types of specialized wheels exist?
Steel Weld Wheels
Steel weld wheels are durable and heavy. They’re designed for rugged applications and deliver strong performance in racing. Manufacturers use high-strength steel and typically employ welding and machining processes to ensure lasting quality. A critical stage in welding, known as a hot pass in welding, helps secure the durability and strength of the wheels.
Aluminum Weld Wheels
Aluminum weld wheels are lightweight and provide excellent strength-to-weight ratios. They’re ideal for improving speed and handling in cars. Producers cast or forge aluminum, then weld the pieces together for added strength while keeping the overall weight low. When dealing with vehicle components, knowing how to weld thin metal effectively ensures the durability and performance of the welded joints.
Cast Iron Weld Wheels
Cast iron weld wheels are known for their rigidity and high wear resistance. They’re often used in heavy-duty applications. Manufacturers melt iron, pour it into molds, and then weld iron fittings for structural stability. In setting up equipment for welding, one important aspect is determining the appropriate breaker size for welders.
Composite Weld Wheels
Composite weld wheels blend materials for enhanced performance. They offer unique advantages in weight and durability. Makers like Billet Specialties use advanced materials and layering techniques to ensure they perform well under various conditions.
Magnesium Weld Wheels
Magnesium weld wheels are ultra-light and offer fantastic performance boosts. They’re commonly used in professional racing for maximum efficiency. High-purity magnesium is alloyed and welded into shape, minimizing weight without sacrificing strength.
We covered different types of weld wheels here. Next, we will cover the steps to understanding weld wheels.
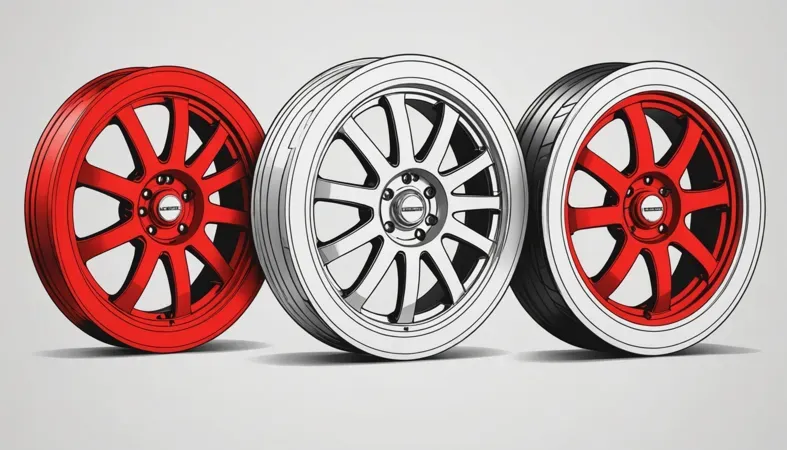
Steps to Understanding Weld Wheels
Here are the steps to understanding Weld wheels and their specifics.
Identify the Type Of Weld Wheels
Start by determining which type of Weld wheels you need. There are various types, like Weld Racing wheels and older Weld wheels, each with unique specifications. For instance, Weld Racing wheels typically weigh around 12 lbs (5.4 Kg) each, while Truck Weld wheels may weigh more due to size and durability.
Selecting the right one is crucial for performance. For enhanced strength, consider the Racing models. They’re made from lightweight materials like aluminum alloy, improving fuel efficiency and handling.
Assess Compatibility With Your Vehicle
Next, check if the selected Weld wheels fit your vehicle’s make and model. Each vehicle has different bolt patterns and offsets. For example, a common offset for Weld Off-Road Wheels is 38 mm, while traditional cars might use a 25 mm offset or less. Knowing this can save you trouble during installation.
Note that some Weld wheels, like the Weld Racing wheels 15×10, may require specific tire sizes. It’s vital to cross-check your vehicle’s specifications against potential wheel sizes.
Calculate Total Weight Capacity
Understand the total weight capacity your Weld wheels can handle. Weld wheels often have load ratings from 1,200 lbs to 3,000 lbs (544 Kg to 1,361 Kg). You can usually find this information stamped on the wheel or in the product specifications. If ever dealing with the adverse effects of welding, it’s essential to know how to treat flash burn in eyes effectively.
This is crucial for safety and performance, especially for off-road or racing applications. Keep this in mind when choosing your Weld wheels; you wouldn’t want to push their limits during a high-speed maneuver!
Examine Surface Finish and Design
Next, look at the surface finish and design of the Weld wheels. Popular finishes include polished, chrome, or painted options, all contributing to aesthetics and performance. Some Weld wheels, like Method Race Wheels, offer a rugged design suitable for off-road adventures.
If you prefer durability, a matte or coated finish resists chips and corrosion. A darker finish may hide dirt better. Consider how often you plan to clean your wheels—this choice matters!
Review Maintenance Requirements
Lastly, research the maintenance your Weld wheels will need. Some require regular cleaning to maintain a new appearance, while others need minimal care. Using specialized wheel cleaners can prevent dust and grime buildup on durable finishes.
Inspect them periodically for dents or damage, especially if you often take your vehicle off-road. This will save you from costly replacements later!
We’ve wrapped up the steps to understanding Weld wheels here. Next up, we’ll look at factors influencing Weld wheels.
Factors Influencing Weld Wheels
What factors impact the quality and performance of weld wheels?
Material Composition
Weld wheels are often made from lightweight aluminum alloys, typically 6061-T6. This alloy balances strength and weight, resulting in wheels that weigh about 18 to 25 lbs (8 to 11.3 Kg).
Welding Technique
The welding method, such as TIG or MIG, affects the strength of the wheel’s joints. For instance, TIG welding generally offers better precision, leading to less distortion and improved performance under stress.
Temperature Control
Temperature management during welding is critical. For aluminum wheels, keep the heat below 325°C (617°F) to prevent softening the metal, ensuring structural integrity.
Environmental Considerations
Welding outdoors or in high humidity can cause defects. Dust and moisture can hinder the welding process, affecting the wheel’s durability.
Wheel Design and Structure
The shape and design significantly impact performance and aesthetics. Variations in design can affect weight distribution and aerodynamics, making some wheels better suited for racing or off-road use.
We covered the elements affecting weld wheels. Next, we will explore the typical uses of weld wheels.
Common Applications of Weld Wheels
Weld wheels aren’t just strong; they have various applications across industries. Let’s take a closer look at where you might see them in action.
Application | Description | Typical Materials | Weight Capacity |
---|---|---|---|
Drag Racing | Used for high-speed drag racing, providing low weight and high strength. | Aluminum Alloy (6061-T6) | Up to 2,000 lbs (907 kg) |
Off-Road Vehicles | Designed to withstand rugged terrain, enhancing durability in harsh conditions. | Steel & Composite Materials | 2,500 lbs (1,134 kg) |
Sports Cars | Improves handling and performance by reducing unsprung weight. | Magnesium Alloy | 1,800 lbs (816 kg) |
Heavy-Duty Trucks | Supports substantial loads necessary for transporting heavy equipment. | High-strength Steel | 3,500 lbs (1,587 kg) |
Farm Equipment | Enhances mobility on farms, capable of handling rough terrains. | Cast Iron | 2,000 lbs (907 kg) |
Choosing the right weld wheels for your application is key. So, whether you’re hitting the track or cruising off-road, understanding these applications will help you make an informed decision.
We have now covered the typical uses of weld wheels. Next, we will examine common inquiries regarding them.
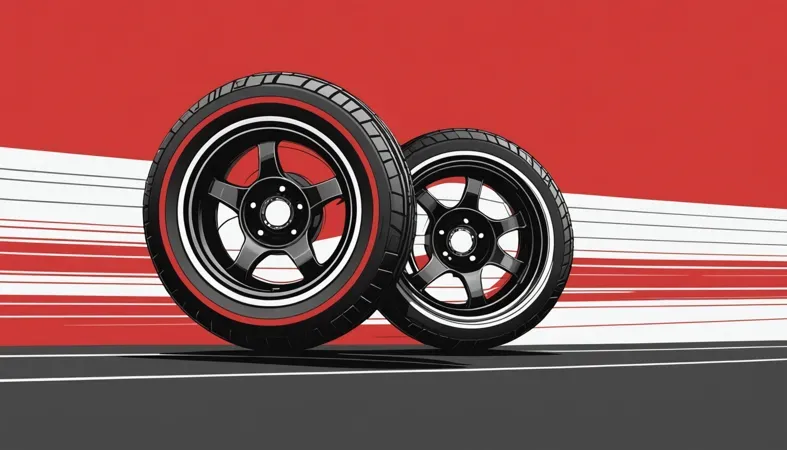
Frequently Asked Questions (FAQs)
Now let us look at some common questions I typically get asked.
How to Identify Weld Wheels?
You can identify weld wheels by examining the design and construction. Weld wheels usually have a multi-piece structure with a smooth surface and unique bolt patterns. Look for markings or branding, which often indicate the manufacturer and model, making it easier to find specifications online.
How Much Do Weld Wheels Weigh?
The weight of weld wheels depends on their size and material. On average, a single 15-inch weld wheel weighs between 9 kg (20 Lbs) and 11 kg (25 Lbs). Heavier models can weigh up to 14 kg (30 Lbs); weight plays a role in performance and suitability for your vehicle.
What Are the Benefits Of Weld Wheels?
Weld wheels offer several benefits, including exceptional durability and improved performance. They’re designed to withstand extreme conditions, such as racing or off-roading. Additionally, their lightweight properties allow for better fuel efficiency and handling compared to traditional steel wheels.
Are Welded Wheels Good?
Yes, welded wheels are good for various applications. Their strong construction reduces the risk of bending or breaking under pressure. Many enthusiasts prefer them for racing and off-road vehicles due to their ability to handle high stress and impact effectively.
What is a Welding Wheel?
A welding wheel refers to wheels specifically designed for welding operations. Typically used in fabrication, welding wheels can help increase efficiency and precision during metalworking tasks. They can enhance the quality of the weld joint, reducing rework and improving overall productivity. If you are working with zinc-plated steel you might want to know about welding zinc-plated steel to optimize your procedures effectively.
Conclusion
We covered what weld wheels are, how they work, their types, factors influencing them, and some frequently asked questions. We discussed identifying weld wheels, their weights, and their essential roles in welding projects. You got a good look at each aspect that contributes to understanding weld wheels. It is also crucial to consider the health risks associated with welding such as potential cancer risks.
I trust these insights have been helpful. So, what are weld wheels? In simple terms, they’re specific wheels designed to fit with welding tasks, known for their strength and precision. Remember, their weight typically ranges from 5 to 10 kg (11 to 22 Lbs), and they come in various types suitable for different applications.
Thank you for exploring these insights with us. If you’re interested in diving deeper into the world of welding, feel free to visit What is Welding for more valuable information.
References
- American Society of Mechanical Engineers. (2019). ASME Section IX: Welding and Brazing Qualifications. New York, NY: ASME.
- O’Brien, R. L. (1991). Welding Handbook: Welding Processes, Part 1. Miami, FL: AWS.
Mark is a skilled welding engineer specializing in advanced metal joining technologies and process design. With a formal education in welding engineering and a background rooted in practical experience, Mark bridges the gap between theory and application. He is passionate about making technical concepts accessible, empowering welders to embrace innovation while mastering essential skills. Mark combines his scientific expertise with a commitment to supporting the welding community alongside his uncle, Joe.
Automotive, Certification, Construction, High-performance Wheels, Structural Integrity, TIG Welding, Weld Wheels, Welding, Wheel Types, Wheel Weight