What Causes Crater Cracks in Welding? Insights on Causes, Prevention, and Tips
Published on: April 17, 2025 | Last modified: March 4, 2025
By: Joe Carter
Crater cracks are tiny fractures that appear at the end of a weld. These cracks can weaken the weld and lead to structural issues.
One question I was asked a lot is what causes crater cracks in welding? It’s crucial to understand this because ignoring them can lead to bigger problems down the line. From my experience, I’ve seen how small cracks can take hold and compromise a whole project if not addressed early.
In this guide, I’ll explore what causes crater cracks in welding, the types of crater cracks, steps to prevent them, various factors contributing to their occurrence, typical issues related to crater cracks, aftercare and inspection tips, use cases, and alternative solutions. You’ll also find answers to frequently asked questions to help deepen your understanding of what causes a weld to crack and other related issues.
Contents
- What Causes Crater Cracks in Welding?
- What Causes Crater Cracks in Welding?
- Types Of Crater Cracks in Welding
- Steps for Preventing Crater Cracks in Welding
- Factors Contributing to Crater Cracks in Welding
- Typical Issues With Crater Cracks in Welding
- Aftercare, Inspection, and Advanced Tips for Crater Cracks in Welding
- Use Cases Of Crater Cracks in Welding
- Other Options for Addressing Crater Cracks in Welding
- Frequently Asked Questions (FAQs)
- Common Misconceptions About Crater Cracks in Welding
- Impact of Crater Cracks on Different Industries
- Conclusion
- Additional Reading
What Causes Crater Cracks in Welding?
Crater cracks occur due to rapid cooling of the weld metal. They typically result from improper technique or insufficient filler material. You’ll often see them in steel and aluminum applications where precision is crucial.
What Causes Crater Cracks in Welding?
Crater cracks occur near the end of a weld, where molten metal solidifies too quickly. Studies show these cracks form in the last few millimeters of the weld pool. They’re mainly caused by thermal shrinkage during cooling or rapid cooling. In high-stress metals like steel, about 20-80% of welds can crack if not done properly.
Uneven cooling of the weld bead creates stress concentration. If the end of the weld isn’t filled properly, you increase the chance of a crater crack. Expertise in using the right filler (Material) is essential.
If I were you, I’d pay close attention to how you finish each weld bead. I’ve seen crater cracks develop due to poor technique. Remember, the causes of crater cracks in welding often relate to avoiding hydrogen cracking, so keep that in mind!
Types Of Crater Cracks in Welding
-
Surface Crater Cracks
Surface crater cracks occur on the weld surface. They arise from rapid cooling after welding, causing tension and stress. To prevent this, welders should control cooling rates with sufficient post-weld heat treatment.
-
Internal Crater Cracks
Internal crater cracks are hidden within the weld. They form when gases or impurities create voids, leading to instability. To avoid these, use clean materials and set proper shielding gas flow to prevent contamination.
-
Heat-affected Zone Crater Cracks
These cracks develop in the area surrounding the weld. They’re caused by uneven heating and cooling of the metal. To mitigate this, maintain consistent preheating and post-welding temperatures to minimize thermal shock.
-
Shrinkage Crater Cracks
Shrinkage crater cracks occur when the weld metal cools and contracts. They arise from restraint in the surrounding base metal. To prevent this, use proper joint designs that allow for expansion and contraction without restriction.
-
Porosity-related Crater Cracks
Porosity-related crater cracks are caused by trapped gases in the weld. These result from moisture or contaminants in the base material. To fix this, ensure all materials are dry and clean, and control your welding speed to allow proper gas escape. This highlights the importance of understanding what causes porosity in welding.
You should now have a good understanding of various crater crack types in welding. In the next part, we’ll discuss prevention steps.
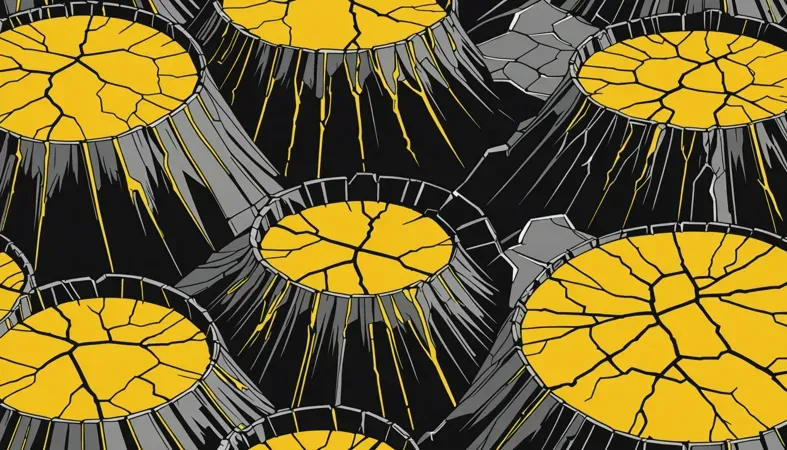
Steps for Preventing Crater Cracks in Welding
Here are steps to prevent crater cracks in your welding projects. Follow these closely for the best results.
-
Proper Joint Preparation
Start by cleaning the joint. Remove contaminants like oil or rust. Clean surfaces reduce cracking by ensuring the weld metal bonds well. Aim for a proper fit; gaps can lead to uneven cooling and crater cracks. For edge joints, clarity on technique is crucial; explore the method of welding edge joints for optimized results.
Use a mechanical or chemical method to prepare the surface. Sandblasting is highly effective. Maintain a smooth surface to control the weld pool during the process. Keeping a consistent joint width is crucial; 2 mm (0.08 In) is a good guideline.
Welding alloy wheels requires precision and skill to ensure their structural integrity is maintained. It is essential to understand the limits of repairs and how many times you can weld an alloy wheel without compromising safety.
-
Monitoring Welding Parameters
Set your welding parameters correctly. Voltage, amperage, and travel speed significantly impact the outcome. A voltage that’s too high may cause excessive heat, leading to crater cracks. Watch the temperature; it’s key for maintaining weld integrity. Proper electrical safety is crucial to prevent electric shock in welding.
Use a multimeter to monitor your settings. Aim for the lowest heat input necessary. Proceed slowly with travel speeds around 254-406 mm/min (10-16 In/min) to control the weld pool and prevent rapid cooling. Selecting an appropriate welding cable is crucial because it affects performance and safety, and you can learn more about what determines the size of a welding cable.
-
Utilizing Appropriate Filler Material
Choose filler material that matches your base metal. Mismatched materials can lead to vulnerabilities and cracks. Look for a filler with similar thermal expansion (Around 12.5 X 10⁻⁶/°C) as your base material.
Your filler metal should also meet the required strength. For example, when welding carbon steel, selecting an ER70S-6 grade enhances resilience against cracking. Avoid low-quality fillers as they increase the risk of defects.
-
Controlling Cooling Rates
Manage how quickly your welds cool. Rapid cooling can occur with thick sections or pre-existing stress, leading to crater cracks. Aim for a controlled cooling rate of about 5°C/min (41°f/min) to reduce stress. Heat sinks, like backing bars, are beneficial.
Preheat your materials, especially in thick sections. Keep them at around 120°C (250°F) before starting. This maintains a stable temperature and promotes quality throughout the weld.
-
Implementing Post-weld Treatments
Apply heat treatment after welding to relieve stress. This can effectively reduce the risk of cracks. Use techniques like post-weld heat treatment (PWHT) at controlled temperatures of about 600°C (1112°F) for low-alloy steels.
Consider selective stress-relief thermal cycles, especially in high-stress applications. If left untreated, residual stresses can lead to cracks over time, so don’t skip this step.
That covers methods to prevent crater cracks in welding. Let’s now take a look at the factors that contribute to them.
Factors Contributing to Crater Cracks in Welding
What factors can lead to crater cracks during welding?
-
Welding Speed
Welding speed directly affects heat concentration. Slower speeds can cause overheating, increasing stress on the weld pool and potentially leading to crater cracks.
-
Arc Length
A longer arc increases heat input, creating a larger crater that’s more vulnerable to cracking as the weld cools.
-
Base Material Composition
Pay close attention to material composition. Different alloys react differently to welding heat, affecting the likelihood of crater and longitudinal cracks.
-
Heat Input
High heat input can increase grain growth, leading to brittle structures within the weld. Keeping heat below 1,000 J/cm reduces crack risk.
-
Environmental Conditions
Welding in high humidity or wind can cause rapid cooling. This quick temperature change can create thermal stress, promoting crater cracks.
We have now covered the factors that lead to crater cracks in welding. Next, we will examine common issues related to crater cracks.
Typical Issues With Crater Cracks in Welding
Let’s examine specific problems associated with crater cracks.
-
Inconsistent Welding Techniques
Crater cracks often occur due to unsteady techniques. Maintain a consistent travel speed. If you notice cracks, check your welding travel; it should be uniform.
-
Improper Cooling Methods
Crater cracks can result from uneven cooling. Ensure slow and uniform cooling. Quenching too quickly can lead to cracks.
-
Defective Equipment
Old or faulty welding machines can cause crater cracks. Regularly check your equipment and replace worn parts. A good welder must stay sharp!
-
Contaminated Filler Materials
Crater cracks may signal dirty filler materials. Always use clean, specified fillers. Inspect before you weld—it saves headaches later.
-
Inadequate Quality Control Measures
No scans? No tests? You might welcome crater cracks. Implement strict quality control (QC) measures. Document results at every stage for solid outcomes.
We covered common problems associated with crater cracks in welding. Next, we will cover aftercare, inspection, and advanced tips.
Aftercare, Inspection, and Advanced Tips for Crater Cracks in Welding
Here’s solid advice on aftercare, inspection, and expert tips for addressing crater cracks.
Aftercare Tips
Once you’ve identified crater cracks, ensure a slow cooling process. Rapid cooling can worsen these flaws. Control cooling at roughly 10°C (50°F) per hour for larger areas to minimize stress concentration.
Inspection
Inspect welds closely using a magnifying tool. Look for visible microvoids or non-uniformities. I prefer a 10x magnifier for accuracy and cross-reference findings against standards like ASTM E165. Thorough knowledge of welding techniques is crucial, especially when considering the principles of arc welding technology.
Expert Tips
Adjust your welding technique. Use a narrower arc at around 200 A for better penetration, which reduces metallurgical issues. Stagger your work by alternating welds to ease stress concentration—a proven method to significantly prevent crater cracks. For more detailed procedures, consult the welding guidance that outlines effective practices.
Use Cases Of Crater Cracks in Welding
People use crater crack analysis in quality assurance labs. It has several applications, including:
- Pipelines: Essential for testing weld integrity before transporting gases. It prevents leaks, ensuring safety and compliance.
- Aerospace Components: Critical in aircraft manufacturing. It ensures structural integrity, avoiding catastrophic failures during flight.
- Automotive Repairs: Common for fixing frame welds. It focuses on reliability to handle performance stresses and extend vehicle lifespan.
- Offshore Structures: Key in oil rigs and platforms. It addresses environmental stressors that can cause cracks, enhancing durability.
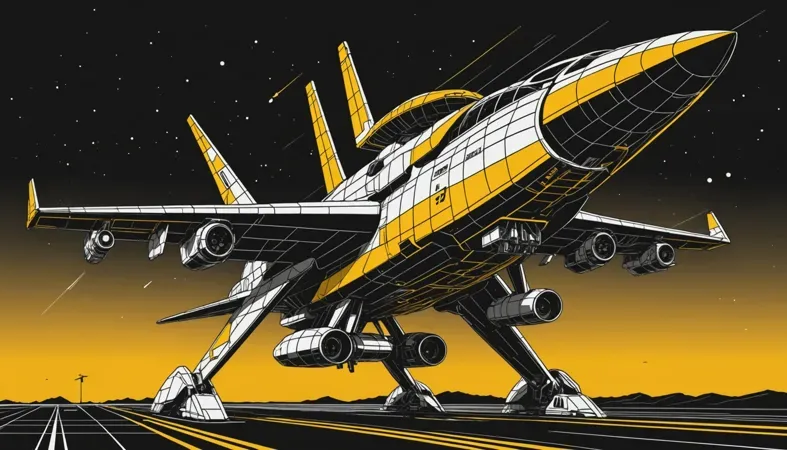
Other Options for Addressing Crater Cracks in Welding
Instead of just focusing on common methods, consider alternatives like using proper filler materials, such as E7018 for low hydrogen welding. These options are often preferred when working with high-strength steel, providing better ductility and reduced crack susceptibility. Based on my observations, adjusting your electrode angles can also minimize crater crack formation, ensuring a smoother finish.
Additionally, preheating materials can be a game-changer. For instance, preheating to about 150°F (65°C) helps reduce the chance of welds cracking, particularly in thicker sections. It’s all about finding the right combination of practices to combat those pesky cracks efficiently.
Frequently Asked Questions (FAQs)
Now let us look at some questions I typically get asked.
What Causes Longitudinal Cracks in Welds?
Longitudinal cracks in welds occur due to poor welding techniques or improper heat management. When weld heat is excessive, it can lead to rapid cooling, causing stress and cracks. Parameters like heat input and cooling rates directly affect weld integrity.
What Causes a Weld to Crack?
A weld can crack from several factors, including insufficient preheating, internal stresses, and material defects. For instance, high-strength steels are particularly sensitive to stress and need careful handling. Understanding the material properties is key to preventing cracks. Selecting the right welding electrode is crucial in addressing these challenges as it ensures compatibility and promotes weld integrity, so it is important to know how to choose electrode for welding.
What is Hydrogen Cracking in Welding?
Hydrogen cracking in welding is a serious issue where hydrogen diffuses into the weld and creates cracks. This happens mostly in high-strength steel and during the cooling phase. Controlling hydrogen levels is critical in preventing this type of cracking. Knowing what electrode classifications mean is crucial for selecting the right materials, especially for welding processes that involve specialized electrodes like E316-16 electrodes.
What is Cracking in Welding?
Cracking in welding refers to visible fractures in the weld area due to various stressors. Factors like thermal stress and material composition play roles in causing this issue. Effective weld planning helps to mitigate the risk of cracking significantly.
What Causes Welds to Crack?
Welds typically crack due to rapid cooling, high carbon content in metals, and contaminants in the weld area. As much as 50% of weld failures result from such issues, emphasizing the importance of cleanliness and proper heat management.
How to Prevent Crater Cracks in Welding?
Preventing crater cracks involves proper finish techniques and controlling the cooling rate of the weld. Techniques like reducing heat input and ensuring a good travel speed can minimize this risk. Regularly checking equipment and processes can enhance weld quality.
Common Misconceptions About Crater Cracks in Welding
There are a few myths that can mislead welders about crater cracks. Let’s clear the air.
-
Myth 1: Crater Cracks Only Show Up in Steel
Many believe only steel is prone to crater cracks. But aluminum and other alloys can also develop these cracks. Proper technique applies to all metals.
-
Myth 2: Bigger Welds Won’t Crack
Some think that larger welds are immune to cracking. Wrong! Larger welds can actually increase the risk if cooling isn’t controlled properly.
-
Myth 3: Crater Cracks Are Not Serious
Don’t underestimate crater cracks! They can lead to major structural failure if ignored. They’re a sign of deeper issues.
-
Myth 4: It’s Only About Temperature
While temperature control is key, other factors like filler material and technique are just as vital. You can’t blame only heat!
Impact of Crater Cracks on Different Industries
Understanding how crater cracks can affect various industries can help inform your welding practices.
Industry | Impact of Crater Cracks | Potential Consequences |
---|---|---|
Aerospace | Can lead to catastrophic failures in flight. | Risk to passenger safety and loss of expensive aircraft. |
Pipelines | Cracks can lead to leaks. | Environmental disasters and regulatory penalties. |
Automotive | Weakens structural integrity. | Increased repair costs and compromised safety. |
Construction | Can affect the durability of critical structures. | Potential building collapses or structural failures. |
Conclusion
We’ve made it to the end, and I hope it was helpful. We covered various aspects of crater cracks, including types, contributing factors, prevention steps, typical issues, aftercare, inspections, and even use cases. Each of these elements helps to clarify the complexities surrounding what causes crater cracks in welding.
I trust these insights have been helpful in understanding what causes crater cracks in welding. Essentially, these cracks can form due to rapid cooling, improper technique, and even issues with the welding material itself, among other factors. By addressing welding fundamentals and following best practices, you can mitigate these issues effectively.
To explore more valuable resources and tips on welding, be sure to visit What is Welding.
Additional Reading
- American Society of Mechanical Engineers. (2019). ASME Section IX: Welding and Brazing Qualifications. New York, NY: ASME.
- International Institute of Welding (IIW): https://www.iiwelding.org
- Cary, H. B., & Helzer, S. C. (2005). Modern Welding Technology (6th ed.). Upper Saddle River, NJ: Pearson.
Joe Carter is a retired welding professional with over 40 years of hands-on experience in the industry, spanning ship repair, structural welding, and even underwater projects. Joe is a master of MIG, TIG, and Stick welding. Passionate about mentoring the next generation of welders, Joe now shares his decades of expertise and practical insights to help others build rewarding careers in welding.
Crack Prevention, Crater Cracks, Electrical Safety, Filler Metal, Metalworking, Structural Integrity, Welding, Welding Defects, Welding Techniques