How Do We Use an Arc Welder in Agriculture?
Published on: May 2, 2025 | Last modified: March 4, 2025
By: Joe Carter
An arc welder is a tool that uses electric arcs to melt and fuse metal pieces together. It’s commonly used for strong, durable welds.
One thing people often ask me about is how do we use a ar welder in agriculture? Understanding this is vital for any farmer or operator. I’ve seen how proper welding can extend the life of equipment and improve productivity on the farm.
In this guide, we’ll cover what an arc welder is, types of arc welders, prerequisites for use, step-by-step guidance, safety tips, various welding techniques, factors affecting welding, common issues, aftercare, and the benefits of using arc welding in agriculture. You’ll get a complete picture of how an arc welder works and its crucial role in farming.
Contents
- How Do We Use an Arc Welder in Agriculture?
- What is an AR Welder?
- Types Of AR Welders
- Prerequisites: What Do You Need
- Safety Tips
- Steps to Use an Arc Welder in Agriculture
- Types Of Arc Welding Techniques in Agriculture
- Factors Influencing Arc Welding in Agriculture
- Enhancing Efficiency with Advanced Techniques
- Common Issues in AR Welding for Agriculture
- Aftercare, Inspection, and Advanced Tips for AR Welding in Agriculture
- Why This is Worth It: Advantages
- Typical Applications Of AR Welding in Agriculture
- Other Options You Can Consider
- Frequently Asked Questions (FAQs)
- Conclusion
- Additional Reading
How Do We Use an Arc Welder in Agriculture?
An arc welder is a tool that fusion welds metals. So, how do we use an arc welder in agriculture? Farmers use it for repairs, like fixing machinery and building structures. It’s tough but can be tricky for beginners.
What is an AR Welder?
An AR welder, or arc welder, is a device used to join two pieces of metal using electricity. It generates an electric arc between an electrode and the base material, reaching temperatures over 3,000°C (5,432°F) that melt the metals together. AR welders are common in various industrial applications due to their versatility and efficiency.
In agriculture, AR welders are essential tools for fabricating and repairing equipment. You might see a farmer welding a metal plow or fixing a combine harvester. Based on my experience, using an AR welder in agriculture saves time and money, enabling quicker repairs and customizations.
I mainly used it at work to fix broken farm implements. Once, when the handle on a tractor’s hitch snapped, I quickly repaired it with the AR welder. Understanding what an arc welder can do in agriculture can be a game-changer. It provides reliable repairs that ensure machinery runs smoothly and improve overall efficiency in farm operations.
Types Of AR Welders
-
Arc Welders
Arc welders create a strong bond between metals using electrical arcs. In agriculture, you use arc welders to fix farm machinery like tractors. First, set up the welder, select the correct rod, wear protective gear, then initiate the arc and weld the parts together smoothly. Mastering techniques such as welding uphill effectively can enhance your welding skills significantly.
-
TIG (Tungsten Inert Gas) Welders
TIG welders offer precise control for thin materials using a non-consumable tungsten electrode. In agriculture, you can use TIG welders to repair delicate metal components like irrigation systems. To weld, connect the TIG torch, adjust the gas flow, and slowly feed the filler rod while keeping a steady hand. Welders must also consider how welding light can impact camera equipment during the repair process; this potential risk to cameras is important to understand for successful welding results.
-
MIG (Metal Inert Gas) Welders
MIG welders utilize a continuous wire feed for quick and easy welding. You use MIG welders for larger projects, like building fences or welding frames for agricultural equipment. To weld, set your machine’s voltage, choose the right wire diameter, load the welding gun with the wire, then pull the trigger to weld.
-
Stick Welders
Stick welders are versatile and use a consumable electrode for bonding metals. In farming, you can fix heavy equipment like plows with stick welders. To do this, select the correct electrode, set the welder’s amperage, and strike an arc to fuse the metal steadily.
-
Multi-process Welders
Multi-process welders can perform various welding styles like MIG, TIG, and stick. In agriculture, you can adapt these welders for different repairs on various equipment. To use, switch modes as needed, set your parameters, and effectively tackle whatever welding task you’re handling.
We covered the various types of AR welders. Next, we will cover the necessary prerequisites and requirements.
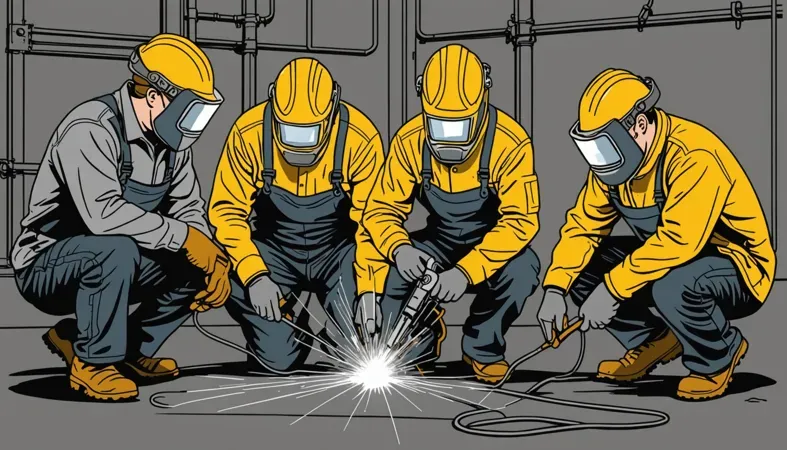
Prerequisites: What Do You Need
What do you need to start using an arc welder in agriculture?
- Arc Welder: You need a reliable model like the Miller Millermatic 211 (Ideal for Light Agricultural Work). It offers versatility and portability, essential for various tasks.
- Welding Wire: Choose ER70S-6 (0.8 Mm/0.030 In), designed for MIG welding. This wire ensures good penetration and a strong bond.
- Welding Cart: Get a durable cart like the Miller ArcStation. It keeps your equipment organized and accessible in the field.
- Workpiece Preparation: Clean your joints with a grinder such as the Makita GA4530. Clean surfaces ensure effective welding and stronger joints.
We’ve wrapped up the necessary requirements for preparation. Next up, we’ll look at essential safety guidelines.
Safety Tips
Let’s explore essential precautions for using an arc welder.
- Audio Protection: Always wear earplugs, as arc welding can produce noise up to 120 dB. Prolonged exposure may cause hearing damage, so I recommend 3M Peltor X1A Ear Muffs.
- Proper Ventilation: Ensure your workspace has good airflow to avoid smoke buildup. A fan can help; use an exhaust fan rated at 100 CFM (Cubic Feet Per Minute) to maintain airflow.
- Fire Safety Gear: Wear fire-resistant clothing. Use cotton or leather to prevent burn injuries, as traditional materials work best here.
- First-Aid Kit: Keep a first-aid kit handy. Injuries can happen, and being prepared is key; include gauze and antiseptics for urgent care.
Remember, safety precautions are essential. I can’t stress that enough!
We have now covered safety guidelines for welding. Next, we will examine the steps to utilize an arc welder in agriculture.
Steps to Use an Arc Welder in Agriculture
Here are steps to effectively use an arc welder in agriculture for optimal results.
-
Set Up the Arc Welder
Position your arc welder on a stable surface at a comfortable height. Check the welder’s settings; typically, set the output to 100-200 Amperes for agricultural tasks. For example, when using the Miller Millermatic for thin metal, adjust the voltage for optimal penetration. Taking a few extra minutes to set this up saves time later.
Consider the type of metal you’ll weld. Steel usually needs a hotter arc, while aluminum requires a cooler one. I recommend using .030 inches (0.76 Mm) wire for general tasks. Adjust your speed based on the material to avoid burn-through and ensure strong joints.
-
Prepare Your Workpiece
Clean the surfaces of the pieces you’re welding. Use a wire brush or grinder to remove paint, rust, and debris. This preparation enhances weld quality. You’d be surprised how much better the joint looks when surfaces are properly prepped!
If you’re working on larger machinery, clamp the workpieces in place. Lining up the pieces prevents distortion from heat while welding. This allows you to focus on creating strong welds without losing alignment, saving hours of rework on the farm.
-
Begin Welding
Start the arc and maintain even speed and steady motion. Move your hand consistently, aiming for a travel speed of about 15 inches per minute (38 Cm/min) for most agricultural metals. It’s easy to rush, so take your time to avoid a mess!
Watch the puddle; it should be bright and fluid. If the puddle isn’t right, either slow down or slightly increase the amperage. Pay attention to gaps; run a bead slightly beyond the edge for a strong foundation. Don’t forget to weave for wider joints when needed!
-
Inspect Your Welds
After welding, inspect the joints visually. Look for smooth, consistent beads without pits or holes. A good weld should have a uniform appearance. I often run my finger along the weld to check for rough spots—this is a quick way to catch imperfections!
Finally, use a grinder to polish sharp edges or remove slag if necessary. This step improves aesthetics and reduces the risk of injury later. Doing a final inspection ensures everything’s in good shape before putting your equipment back to work.
So far we covered how to effectively use an arc welder in agriculture. Next, let’s look at various arc welding techniques.
Types Of Arc Welding Techniques in Agriculture
Let’s explore the types of arc welding techniques: Shielded Metal Arc Welding, Gas Metal Arc Welding, Gas Tungsten Arc Welding, Submerged Arc Welding, and Flux-Cored Arc Welding.
-
Shielded Metal Arc Welding
Shielded Metal Arc Welding (SMAW) is a manual process that uses a consumable electrode coated with flux. It generates an electric arc between the electrode and the workpiece. SMAW is versatile and effective for repairing farm equipment outdoors.
-
Gas Metal Arc Welding
Gas Metal Arc Welding (GMAW) combines a solid wire electrode with shielding gas, resulting in clean welds with minimal cleanup. GMAW is especially useful for high-quality welds on thinner materials, such as piping and structural parts in agriculture.
-
Gas Tungsten Arc Welding
Gas Tungsten Arc Welding (GTAW) uses a non-consumable tungsten electrode to create the weld. It offers precision and high-quality results, making it suitable for thin materials or intricate projects. I find it effective for automotive repairs in farm machinery.
-
Submerged Arc Welding
Submerged Arc Welding (SAW) employs continuously fed filler metal and a blanket of granular flux to shield the weld. This method is effective for thick materials, providing strong, smooth joints. It’s commonly used for large agricultural structures like silos and workshops.
-
Flux-cored Arc Welding
Flux-Cored Arc Welding (FCAW) is similar to GMAW but uses tubular wire filled with flux. It can be operated with or without shielding gas, making it ideal for outdoor conditions. FCAW excels in welding steels found in agricultural machinery.
Factors Influencing Arc Welding in Agriculture
What factors influence the effective use of an arc welder in agriculture?
-
Material Type
Different materials require specific welding processes. For instance, steel needs higher heat, while aluminum demands a gentler approach.
-
Environmental Conditions
Welding outdoors can be challenging, as wind and moisture affect weld quality. Extreme temperatures can also distort welded materials.
-
Power Supply Stability
Consistent voltage is crucial. A power drop can cause weak arcs and poor penetration.
-
Rod Selection
Choosing the right welding rod is essential for your material’s needs. For example, a 7018 rod is ideal for structural steel and provides great strength and ductility.
-
Welding Technique
Using the right technique results in a clean and strong weld. A steady hand and proper speed reduce defects.
Enhancing Efficiency with Advanced Techniques
Let’s explore how advanced welding techniques can boost productivity and precision in agricultural applications.
Technique | Description | Benefits | Ideal Use Cases |
---|---|---|---|
Pulsed Arc Welding | This method modulates the current between high and low levels. It controls heat input effectively. | Reduces distortion, provides better penetration, and minimizes heat-affected zones. | Thin metal fabrication, like creating frames for greenhouses. |
When Utilizing Weaving Techniques | Weaving involves moving the arc in a zigzag pattern during welding. | Creates wider beads, leading to stronger joints and better coverage. | Repairing large joints or gaps in heavy equipment. |
Multi-pass Welding | This technique involves making multiple weld passes over the same area. | Increases the strength of the weld and allows for greater control over weld quality. | Used for thick materials, such as structural supports in barns. |
Weaving Patterns | Using different weaving patterns for varying joint configurations provides quality adaptation. | Improves heat distribution across welded joints. | Ideal for irregular shapes in metal structures or contouring reinforcements. |
Common Issues in AR Welding for Agriculture
Here are some unique challenges you might face with an AR welder.
-
Inconsistent Arc Stability
An AR welder can struggle with stability if settings aren’t precise. Check the power supply and ensure a clean gas flow. If the arc starts and stops unexpectedly, adjust the arc length.
-
Electrode Contamination
An AR welder’s electrode can pick up dirt or oil. Inspect it closely. Clean the surface with a wire brush and ensure a firm grip on the electrode holder.
-
Improper Heat Settings
Setting the right heat for your AR welder is crucial. If the weld’s too cold, you’ll see poor penetration. Adjust the amperage based on the material thickness; start with a range of 120-160 amps.
-
Weld Cracking
A cracked weld can occur due to rapid cooling or low-quality filler. Look for shallow or jagged cracks on the surface. Preheat the metal if needed, and use quality materials to minimize this issue.
-
Poor Penetration
Poor penetration may lead to weak joints. Inspect the weld seam; if it appears bruised, increase the amperage or slow your travel speed to allow for proper heat penetration.
Aftercare, Inspection, and Advanced Tips for AR Welding in Agriculture
Here’s essential guidance on aftercare, inspection, and advanced techniques for AR welding in agriculture.
Aftercare Tips
After completing your AR welding project, cool down your welder by letting it idle for 15-20 minutes. Clean the nozzle with a specialized tip cleaner using a 0.6 mm (0.024 In) diameter wire. Check the gas shield for blockages; residue can affect your next weld cycle. When working with delicate materials, learn methods to fix welding spatter on glass to ensure precise results.
Inspection Guidelines
Inspect your AR welder before each use. Look for wear on the electrode; just 1 mm of wear can impact performance. Use a multimeter to ensure consistent voltage levels around 20-30 V across terminals. I recommend using Lincoln Electric’s SuperArc wires for reliable electrode quality during inspections.
Expert Tips for Experienced Welders
If this isn’t your first time using an AR welder, tune your machine to match the specific metal thickness. Use advanced pulsing techniques; a pulse frequency of 2-4 Hz works well. Maximize penetration on a 10 mm (0.394 In) steel plate by adjusting the voltage settings between 22-28 V.
Why This is Worth It: Advantages
The main benefit of using an arc welder in agriculture is its versatility. I mainly used it at work for repairing machinery, which saved time and boosted productivity.
Additionally, arc welding is cost-effective; it allows on-site equipment repairs, minimizes downtime, enhances structural integrity, and supports a wide range of materials.
Typical Applications Of AR Welding in Agriculture
I’ve seen people use an AR welder for equipment repairs, but it has many other uses, such as:
- Field Equipment Repairs: An AR welder’s strong welds effectively fix plows and cultivators. Farmers prefer it for its durability.
- Livestock Feeders: AR welders help build and maintain sturdy troughs, ensuring livestock always has easy access to feed.
- Irrigation System Installations: Welders are essential for creating custom piping for irrigation. This saves time and reduces leaks.
- Trailer Fabrication: It’s used to fabricate trailers that carry heavy loads. This method is popular because it customizes and strengthens equipment.
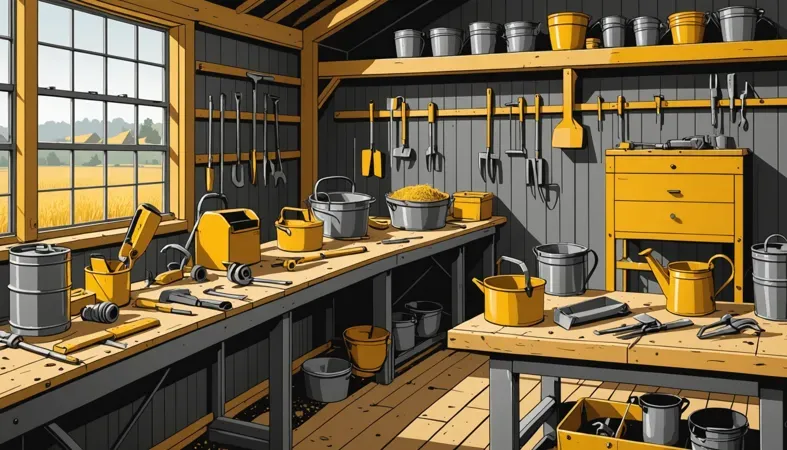
Other Options You Can Consider
You can explore alternatives like plasma cutters or oxy-fuel torches. These tools, such as the Miller Millermatic or Hobart IronMan 24, are great for certain tasks where precision is key. They can cut and join metal with less heat distortion, making them preferable for delicate projects.
Another choice is using high-frequency TIG welders, like Miller Invision 35 and 45. They provide a cleaner finish on stainless steel or aluminum. Having been through similar situations myself, I found that these options work wonders for specific agricultural repairs when an arc welder isn’t ideal.
Frequently Asked Questions (FAQs)
Now let us look at some common questions I typically get asked about arc welders.
What is an Arc Welder?
An arc welder is a machine that uses an electric arc to melt metals together. This process generates temperatures over 3,000°C (5,400°F), which is vital for effective welding. It’s commonly used in construction, automotive repairs, and manufacturing, making it an essential tool in many industries.
One important aspect to consider is how various coatings on metals, like zinc plating, affect the welding process. If you’re wondering whether you can weld zinc plated steel, this technical consideration is crucial to ensure safety and effectiveness in your welding projects.
How Does an Arc Welder Work?
An arc welder works by creating an electric arc between the welding electrode and the metal. This arc produces enough heat to melt both the electrode and the metal workpiece, fusing them together. The process is efficient and can join various metals quickly.
What is Arc Welding Used for?
Arc welding is used for joining metals in a variety of applications, including construction, shipbuilding, and piping systems. Approximately 40% of industrial welds are done using arc welding. It’s versatile and can handle everything from thin sheets to heavy metal structures.
Why is Welding Important in Agriculture?
Welding is crucial in agriculture for repairing and maintaining equipment, like tractors and plows. It ensures machines run smoothly, which in turn increases productivity on farms. A broken piece of machinery can delay operations and cost farmers time and money, highlighting the need for skilled professionals in the industry who can pursue a welding career.
What Would You Use an Arc Welder for?
You would use an arc welder for tasks like repairing metal structures, manufacturing components, or creating artistic metalwork. It’s a go-to tool for situations where strong, durable welds are needed, especially in heavy-duty applications.
Conclusion
We’ve gone through a lot, thank you for sticking it out. We covered what an arc welder is, the types of arc welders, prerequisites for usage, the steps to use one in agriculture, crucial safety tips, various arc welding techniques, factors influencing welding, common issues, aftercare, and typical applications. Each item helps you grasp the essentials of how to efficiently use an arc welder in farming and agriculture.
I trust these insights have been helpful in understanding how do we use an arc welder in agriculture. Essentially, you can utilize an arc welder for tasks like repairing machinery, constructing fences, and even fabricating tools. By knowing the right techniques and safety protocols, you’ll find that welding can greatly enhance productivity on the farm.
To deepen your understanding and explore additional resources related to welding, visit What is Welding.
Additional Reading
- ISO. (2017). ISO 3834: Quality Requirements for Fusion Welding of Metallic Materials. Geneva, Switzerland: ISO.
- Cary, H. B., & Helzer, S. C. (2005). Modern Welding Technology (6th ed.). Upper Saddle River, NJ: Pearson.
Joe Carter is a retired welding professional with over 40 years of hands-on experience in the industry, spanning ship repair, structural welding, and even underwater projects. Joe is a master of MIG, TIG, and Stick welding. Passionate about mentoring the next generation of welders, Joe now shares his decades of expertise and practical insights to help others build rewarding careers in welding.
Agriculture, Arc Welding, Equipment Repair, Farming Tools, MIG Welding, Safety Tips, Welding, Welding Techniques, Welding Wire