How to Weld With Flux Core? Essential Steps, Safety Tips, Benefits
Published on: November 22, 2024 | Last modified: March 4, 2025
By: Joe Carter
Flux core is a type of welding wire that has a core filled with flux. This flux creates a shielding gas when melted, protecting the weld from contamination.
One question I get asked a lot is how to weld with flux core. It’s crucial to nail this down, as proper technique can make or break your welds. In my experience, starting with the right settings leads to smoother, stronger welds.
In this guide, you’ll learn how to weld with a flux core welder, explore types of flux core and their weldability, review essential prerequisites, follow steps for welding, get safety tips, understand factors to consider, identify common problems, and discover the benefits and applications of flux core welding.
Contents
- How to Weld With Flux Core?
- What is Flux Core?
- Types Of Flux Core and Their Weldability
- Essential Prerequisites to Get Started
- Steps for Welding With Flux Core
- Safety Tips
- Factors to Consider When Welding With Flux Core
- Typical Problems to Be Aware Of
- Aftercare, Inspection, and Advanced Tips for Welding With Flux Core
- Advanced Techniques for Flux Core Welding
- Key Benefits Of Flux Core Welding
- Where is Flux Core Welding Used?
- When to Try a Different Approach
- Frequently Asked Questions (FAQs)
- Conclusion
- References
How to Weld With Flux Core?
How to weld with flux core? Flux core uses a tubular wire filled with flux to shield welds. You set the welder to about 0.030 to 0.045 inches (0.76 to 1.14 mm) and practice on thicker metals. For those interested in the various techniques involved, this method is beginner-friendly for outdoor applications, making it an excellent choice among different welding processes.
What is Flux Core?
Flux core is a type of welding where the filler material, or wire, has a core filled with flux. This flux produces a shielding gas during welding, keeping impurities out and leading to strong welds. Flux core wires come in two types: gas-shielded and self-shielded, with diameters often ranging from 0.030 inches (0.76 Mm) to 0.045 inches (1.14 Mm).
When welding with flux core, you can use either a self-shielded wire or a gas-shielded option. Self-shielded wires generate their own gas from the flux core. I remember my first time trying it; the welding process was smooth, but working on small details was challenging.
I’ve seen a friend weld metal body panels with flux core. His results were impressive—smooth and strong joints. It took practice to get used to the process, but he ultimately succeeded. If you want to learn how to weld using flux core wire, it’s worth trying for various projects, especially outdoor jobs.
Types Of Flux Core and Their Weldability
What types of flux core are available for your projects?
-
Gasless Flux Core
Gasless flux core doesn’t need shielding gas. To weld with this type, feed the wire directly to the work. Start with a higher amperage (Around 140 A) for thicker materials while maintaining a travel speed that keeps the weld pool consistent.
-
Self-shielded Flux Core
Self-shielded flux core shields itself from contamination. To create strong joints, hold the gun at about 15 degrees and move steadily. Monitor your wire feed rate; ideal settings are between 250-300 inches per minute (Ipm).
-
Dual-shielded Flux Core
Dual-shielded flux core uses both gas and wire for protection. To weld effectively, use a shielding gas like argon or CO2. Adjust your flow rate to about 20-25 cubic feet per hour (Cfh) while traveling slowly to allow heat to penetrate. For those interested in setting up their own welding station at home, finding the best welding machine for home use is crucial to achieve professional results.
-
Metal-cored Flux Core
Metal-cored flux core wire is ideal for high-speed applications. You’ll need a gas like argon or oxygen for proper shielding. Set your welder’s voltage to approximately 24-28 volts for a stable arc and smooth weld.
-
Submerged Arc Flux Core
In submerged arc flux core, the arc is hidden under a layer of flux. To weld this way, use a special machine designed for it. Set your flux feed to around 5-10 pounds per hour and adjust your amperage based on thickness, focusing on penetration depth. For those wondering where to source their welding gas, consider exploring various purchasing options.
That covers the various types of flux core and their weldability. Let’s now take a look at the essential prerequisites to get started.
Essential Prerequisites to Get Started
What do you need to weld with flux core?
- Flux Core Wire: You need quality wire, such as Lincoln Electric NR-211-MP (0.035 In or 0.9 Mm Diameter). It’s essential for strong welds, providing a protective shield during welding.
- Welder: You should have a reliable flux core welder like the Hobart Handler 140. This welder works with various materials and delivers good output for both beginners and professionals.
- Contact Tip: Get contact tips, like the Tweco 1-5, for various wire sizes. They ensure a consistent feed and improve weld quality.
- Welding Mask: A welding mask with an auto-darkening feature (Like Lincoln Electric’s Viking) is crucial for protecting your eyes from harmful UV and infrared rays and improving visibility.
That covers the essential prerequisites for getting started. Let’s now take a look at the steps for welding with flux core.
Steps for Welding With Flux Core
Now, let’s dive into the steps to effectively use a flux core welder.
-
Prepare the Work Area
Start by clearing clutter from your work area. Maintain at least 5 feet (1.5 Meters) of space around you for safety and ease of movement. Ensure the ground is level and free of flammable materials. Proper lighting makes a significant difference while you work.
Next, set up a welding table for added stability. A flat surface minimizes shaky hands and provides better control. Grab a sturdy table and get ready!
-
Select Appropriate Filler Material
Choose the right flux core wire for your task. For welding steel, use .030 inches (0.8 Mm) or .035 inches (0.9 Mm) diameter wire. Select E71T-GS for mild steel and E71T-1 for thicker materials. The correct wire prevents gaps and creates a stronger weld.
Consider the type of metal you’re welding. Each wire type works best in specific situations. Take the time to select the right flux core wire; it’s worth it!
-
Set Up the Welder Settings
Adjust your welder settings to match your wire choice. Refer to a flux core welding settings chart for guidance. A good starting point for .030 inches (0.8 Mm) wire is 18-20 volts with a wire feed speed of 200 inches per minute. Fine-tuning keeps your welds clean.
Getting the settings right transforms your work quality. If the weld looks messy or doesn’t penetrate well, make small adjustments. Keep practicing until you find that sweet spot!
-
Begin the Welding Process
Start welding at the edges of your metal pieces. Keep the nozzle tip about 1/4 inch (6 Mm) from the materials. Use a steady pace and let the arc do the work. Watch for spattering, as it may indicate a setting issue.
Maintain a straight line while welding. Inconsistent movement can lead to weak joints. Practicing on scrap metal first boosts confidence. Remember, consistency is key for a strong weld!
We’ve wrapped up the steps for welding with flux core here. Next up, we’ll look at safety tips.
Safety Tips
Here are some precautions to ensure safe welding practices.
- Wear a Welding Helmet: A proper helmet protects against sparks and UV rays. I recommend the Lincoln Electric VIKING 3350.
- Use Gloves: Quality gloves prevent burns and cuts. Consider the Revco Black Stallion G3010 gloves for optimal protection.
- Ensure Ventilation: Flux fumes can be harmful. Use a fan or work in a ventilated area for proper airflow.
- Check Equipment: Regularly inspect your welding machine and cords to avoid electrical hazards. Perform checks monthly.
Remember, safety precautions aren’t just nice—they’re essential every time you weld. I’m serious!
We have now covered safety tips for welding. Next, we will examine factors to consider when using flux core welding.
Factors to Consider When Welding With Flux Core
What factors affect your ability to weld effectively with flux core? Let’s dive in.
-
Welding Material Thickness
Material thickness directly influences your welding technique. For thicknesses over 1/4 inch (6 Mm), use 0.035-inch (0.89 Mm) flux core wire for proper penetration.
-
Welding Position and Angle
Your position significantly impacts weld quality. When welding vertically or overhead, keep the angle between 10 and 15 degrees for better arc stability.
-
Electrode Diameter
The right electrode can make or break your weld. Use 0.030-inch (0.76 Mm) wire for thin sheet metal, and switch to 0.045-inch (1.14 Mm) for thick materials.
-
Travel Speed
Your travel speed should match the material and wire size. A slow speed can cause excessive heat, while moving too fast may result in weak or cold welds. Aim for 5-10 inches per minute.
-
Heat Input
Controlling heat input is crucial. Too little heat can cause incomplete fusion, while too much can burn through the material. Use the correct settings on your welder for optimal results.
Typical Problems to Be Aware Of
Let’s look at specific issues that arise with flux-cored welding.
-
Inadequate Penetration
Flux-cored welding often suffers from inadequate penetration. Check if your workpiece thickness exceeds 10 mm (0.4 In). Increase your voltage or adjust your travel speed for better penetration.
-
Spatter and Slag Issues
Excess spatter can occur with flux-cored welding. Adjust the wire feed speed and use some anti-spatter spray to reduce the mess.
-
Porosity in Welds
Porosity can affect flux-cored welds if you’re not careful. Moisture in the flux creates tiny holes. Ensure your wire is dry and all surfaces are clean and free of contaminants.
-
Weld Cracking
Weld cracking can occur with flux-cored welding if the joint design is incorrect. Use a proper joint configuration and preheat thicker materials over 6 mm (0.24 In) as necessary.
-
Uneven Weld Beads
Flux-cored welding can produce uneven weld beads, often due to incorrect settings or travel speed. Check your gun angle and maintain a steady hand to improve bead consistency.
Aftercare, Inspection, and Advanced Tips for Welding With Flux Core
Here’s essential info on aftercare, inspection, and expert tips for flux core welding.
Aftercare Guidelines
After completing your weld with flux core, clean the joint promptly. Brush off slag with a wire brush and ensure no contaminants remain. For a seamless finish, use a flapper disc with 120 grit (Or Finer) to smooth the surface, especially in areas that need additional welding.
Inspection Checklist
Start inspection by assessing the bead profile. Ensure a uniform width of about 5 mm (0.2 Inches) along the weld. Check for undercuts; any dips can weaken connections. Use a digital caliper to measure consistency—don’t exceed 0.2 mm (0.008 Inches) in depth. I rely on Miller’s XMT 350 for accurate evaluation.
Expert Tips
Advanced flux core welders should adjust voltage in 5-10 V increments for optimal penetration. Keep travel speed around 150 mm/min (6 Inches/min) to avoid burn-through. Experiment with joint angles between 15-30 degrees for better bead control. The more you customize your settings, the better your results will be.
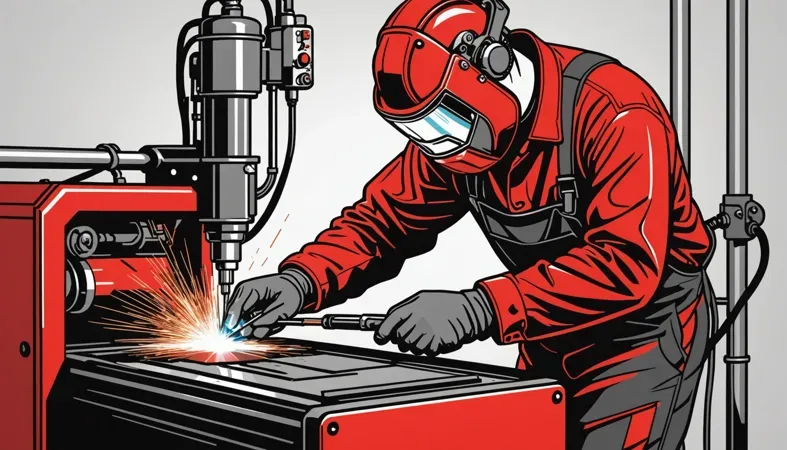
Advanced Techniques for Flux Core Welding
Want to elevate your flux core welding skills? Here are some expert techniques to help you achieve better results!
Weaving Technique
The weaving technique is great for wider weld beads. You can create a zigzag or circular motion while welding. This approach helps fill gaps and improve bead appearance. Use this method on thicker metals for better penetration.
Stringer Bead Technique
For thinner materials, try the stringer bead technique. It involves moving straight along the joint, creating a narrow weld. This minimizes heat input and reduces warping. It’s perfect for sheet metal applications.
Control Your Heat Input
Monitoring heat input leads to cleaner welds. Use a lower voltage setting and faster travel speed for less heat. This approach prevents burn-through and distortion, especially on thin metals.
Joint Preparation
Proper joint preparation can enhance weld quality. Clean edges thoroughly using a wire brush or grinder to remove rust, paint, and contaminants. Aim for a 1/16-inch (1.5 mm) gap for excellent penetration.
Experiment with Different Angles
Try different gun angles between 10 to 20 degrees. Adjusting your angle can help control the bead shape and penetration. Angle your gun towards the direction of travel for the best results.
Understanding Travel Speed
Travel speed should match the material thickness and wire size. A good rule is 5-10 inches per minute (12-25 cm/min) for thicker materials and around 10-15 inches per minute (25-38 cm/min) for thinner sheets.
Technique | Description | Best For |
---|---|---|
Weaving | Zigzag motion for wider welds | Thick metals |
Stringer Bead | Straight motion for narrow welds | Thin materials |
Heat Control | Lower voltage for less heat | Thin metals |
Joint Preparation | Clean edges for better fusion | All joint types |
Angle Experimentation | Change gun angle for better control | All applications |
Travel Speed | Match speed to material type | Thick and thin materials |
Key Benefits Of Flux Core Welding
The biggest advantage of flux core welding is its ability to work outdoors. I saw a friend use it for repairs on his truck during a windy day, and it was seamless!
It also delivers deep penetration (The Ability to Fuse Materials Deeply), resulting in stronger welds. Plus, it’s fast, so you can complete projects quicker. It’s versatile, working well on thick materials. Lastly, it requires minimal clean-up, saving you time and effort.
Where is Flux Core Welding Used?
People use flux core welding to create strong, durable joints on various projects. Its applications include:
- Heavy Machinery Repairs: Ideal for thick metal parts that require deep penetration. Flux core’s efficiency makes it popular in the construction industry.
- Residential Fencing: Perfect for welding tubular steel fences. Its speed and portability are key for quick installations.
- Automotive Exhaust Systems: Great for welding exhaust pipes due to its excellent heat management. It’s commonly used in garages nationwide.
- Metal Art Sculptures: Artists often prefer flux core for its versatility and ability to weld mixed materials, fostering creativity in metalwork.
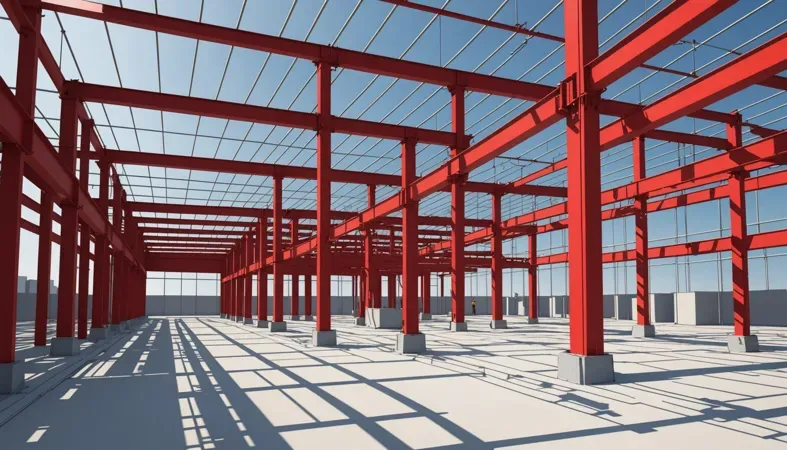
When to Try a Different Approach
You might look into MIG welding or stick welding as alternatives for versatile results. MIG welding, like the Hobart Handler 140, is great for beginners and offers cleaner welds on thin materials. I’ve found stick welding, using rods like E6011, useful for outdoor projects when wind can affect shielding gas in flux core welding.
Choosing these methods can also help with metal thickness. For instance, MIG welding can efficiently handle sheets as thin as 24-gauge (0.56 Mm) while still supporting thicker plates. Depending on your project, switching it up might lead to a more satisfactory finish while maintaining robustness.
Frequently Asked Questions (FAQs)
Here are some commonly asked questions I typically get about welding with flux core.
Can You Get Good Welds With Flux Core?
Yes, you can get good welds with flux core. When you dial in the right settings and technique, flux core can produce quality welds as strong as MIG. In fact, with proper voltage and wire speed, you can achieve bead widths from 6 mm (0.236 In) up to 10 mm (0.394 In) depending on the application. For those new to welding, finding the best equipment to start with can greatly affect your learning curve. If you want to explore some beginner-friendly welder options, it’s essential to choose a machine that suits your specific needs and experience level.
Do You Push or Pull Flux Core Welding?
In flux core welding, you generally pull the weld. Pulling allows for better penetration and a smoother bead. A study indicates that pushing creates more spatter and results in weaker welds, especially in thicker materials over 3 mm (0.118 In).
Why Are My Flux Core Welds So Bad?
Bad flux core welds often come from incorrect settings or technique. Issues like wrong voltage, wire speed, or even poor cleanliness of base metals can lead to inadequate fusion. Remember, proper preparation and parameter adjustments can significantly improve weld quality.
Is Flux Core Welding As Strong As MIG?
Yes, flux core welding can be as strong as MIG welding when performed correctly. Both processes can yield tensile strengths up to 500 MPa (72,500 Psi), depending on the materials and settings used. It’s essential to choose the right filler material for optimal results.
How to Troubleshoot Common Flux Core Welding Problems?
Troubleshooting common flux core welding problems often involves checking your equipment and technique. Start by adjusting settings like wire feed speed and voltage. Additionally, ensure the wire is clean and free of contaminants—this can prevent issues like undercutting and porosity.
What Type Of Flux Core Wire Should I Use for Thin Metal?
For thin metal, you should use a smaller diameter flux core wire, like 0.030 in (0.762 Mm) or 0.035 in (0.889 Mm). Thinner wires allow for more control and reduce the risk of burn-through and distortion on delicate materials.
Can You Use Flux Core Wire on a MIG Welder?
Yes, you can use flux core wire on a MIG welder if it’s set for gasless operation. Most MIG welders can switch between solid wire and flux core but remember to adjust the polarity settings accordingly for proper functionality.
Conclusion
We are almost done. We covered the essential prerequisites for welding with flux core, types of flux core and their weldability, safety tips, steps for welding, common problems, aftercare, key benefits, and typical uses. You also learned when to switch up your approach and answered frequent questions about how to weld with flux core.
Happy you’re here. To weld with flux core, start by picking the right materials and equipment. Remember to stay safe. Keep in mind the right techniques and tips we discussed, like using the correct wire size (Typically 0.030 In [0.76 Mm] to 0.045 In [1.14 Mm]) and maintaining a good angle. That’ll help ensure strong welds that stand the test of time.
We invite you to explore more resources and deepen your understanding of welding techniques at What is Welding, where we are committed to providing you with the latest technical expertise.
References
- Kalpakjian, S., & Schmid, S. R. (2014). Manufacturing Engineering and Technology (7th ed.). Upper Saddle River, NJ: Pearson.
- Occupational Safety and Health Administration (OSHA): Welding, Cutting, and Brazing: https://www.osha.gov/welding-cutting-brazing
Joe Carter is a retired welding professional with over 40 years of hands-on experience in the industry, spanning ship repair, structural welding, and even underwater projects. Joe is a master of MIG, TIG, and Stick welding. Passionate about mentoring the next generation of welders, Joe now shares his decades of expertise and practical insights to help others build rewarding careers in welding.
Flux Core Welding, Safety Tips, Welding, Welding Equipment, Welding Problems, Welding Table, Welding Techniques, Welding Wire