How to Weld Body Panels? Steps, Safety, and Techniques
Published on: March 15, 2025 | Last modified: March 4, 2025
By: Joe Carter
Body panels are the exterior parts of a vehicle that provide shape and support. They help keep everything together while giving your car its unique look.
One thing that’s regularly asked of me is how to weld body panels. It’s crucial to get it right. Trust me, I’ve seen poor welding lead to all sorts of problems down the line, from rust to safety issues.
In this guide, we’ll cover the types of body panels, the prerequisites for welding, essential steps, safety tips, factors affecting the welding process, unique body panel issues, and aftercare. You’ll also learn the benefits you can expect and other options to consider. Plus, we’ll touch on related topics, like how to weld aluminum body panels and various types of patch panels.
Contents
- How to Weld Body Panels?
- What Are Body Panels?
- Types Of Body Panels
- Prerequisites
- Steps to Weld Body Panels
- Safety Tips
- Types Of Welding for Body Panels
- Common Welding Techniques for Body Panels
- Comparison of Welding Techniques
- Factors Affecting Welding Of Body Panels
- Unique Body Panel Issues
- Aftercare, Inspection, and Advanced Tips for Welding Body Panels
- Top Benefits You Can Expect
- Industry Uses
- Other Options You Can Consider
- Frequently Asked Questions (FAQs)
- Conclusion
- References
How to Weld Body Panels?
Body panels are metal layers on your vehicle. To weld body panels, clean both surfaces, set your welder to 20–30 amps, and use 0.023 in (0.58 Mm) wire. It’s challenging, but useful for repairs like quarter panels and patch panels.
What Are Body Panels?
Body panels are the outer coverings of a vehicle that provide structure, support, and protect vital components. They include parts like doors, hoods, fenders, and quarter panels. Most body panels are made from materials like steel or aluminum, with steel thickness ranging from 0.9 mm (0.035 Inches) to 1.2 mm (0.047 Inches). Choosing the right material is essential; for example, aluminum is lighter but harder to weld.
For welding body panels, proper surface preparation is crucial. Clean and grind the edges for a smooth fit. A MIG welder can simplify the task, especially for beginners, providing good control over the weld pool.
You might be surprised to hear I used aluminum body panels in a recent custom project. I learned to weld aluminum panels, and controlling the heat was key to preventing warping. Understanding these details helped when working on patch panels; maintaining a consistent temperature made the difference between a solid joint and a mess.
Types Of Body Panels
What types of body panels will you encounter?
-
Steel Body Panels
Steel body panels are strong and durable. To weld steel panels, you’ll need a MIG welder with an argon-CO2 mix. Clean the surfaces and set the welder to 18-22 volts and 10-15 IPM (Inches Per Minute) for the feed rate.
-
Aluminum Body Panels
Aluminum panels are lightweight and rust-resistant. To join aluminum, use a TIG welder and a filler rod designed for AW 211 or 4047 alloy. First, grind the edges to create a clean weld area, then set the welder to 100-120 amps.
-
Composite Body Panels
Composite panels combine materials for strength and lightness. Welding can be tricky; you’ll often use adhesives instead. If welding is necessary, use a specific composite welding tool to heat the edges gently until they bond.
-
Plastic Body Panels
Plastic body panels are lightweight but can warp easily. To weld plastic, use a plastic welder with a hot-air tool. Melt the edges at about 475°F (246°C) and apply a plastic filler for added strength. When tackling challenging positions in welding, mastering techniques can significantly enhance your skills, including understanding how to weld upside down.
-
Fiberglass Body Panels
Fiberglass panels are lightweight and resistant to corrosion. Instead of traditional welding, use resin and fiberglass cloth. Sand the area, mix the resin, and layer the fiberglass for strength.
We covered different types of body panels here. Next, we will cover the necessary prerequisites.
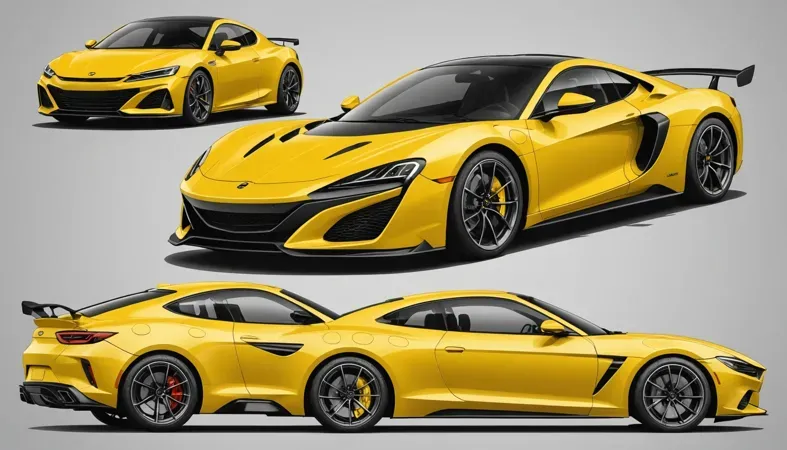
Prerequisites
What do you need to start welding body panels?
- MIG welder: You’ll need a machine like the Hobart Handler 140. This provides the right power and ease of use for welding body panels.
- Body panel metal sheets: Get high-quality steel, such as 18 gauge (1.22 Mm) sheet metal. Its thickness matches most car body specifications.
- Welding wire: Use .030” (0.76 Mm) ER70S-6 wire. This type is ideal for strong welds in automotive work.
- Grinder: A 4.5-inch (115 Mm) angle grinder, like the Dewalt DWE402, is necessary for cleaning and prepping metal edges before welding.
We have now covered the requirements for welding. Next, we will examine the process for welding body panels.
Steps to Weld Body Panels
Here are the steps to effectively weld body panels on your vehicle.
-
Prepare the Work Area
Start by clearing your workspace. You need a flat, stable surface for precision. Ensure the area is well-ventilated to avoid fumes. Consider using a welding table with clamps to secure your body panels while you work.
I always lay down a fireproof mat to keep things tidy and safe. Having everything within reach helps me focus on the weld, reducing movement and mistakes. A clean workspace is key for a smooth welding process. If you ever need to fix mistakes efficiently, explore the techniques on how to remove welds.
-
Clean the Body Panels
Use a wire brush or grinder to remove all rust and dirt from the body panels. This prepares the surface for a strong weld. You want the metal shinier than a new penny! Surface contaminants can weaken your weld and lead to defects.
After cleaning, use acetone or rubbing alcohol to wipe down the panels. This eliminates any remaining oil or grease. For aluminum body panels, a dedicated aluminum cleaner works best. A clean surface ensures solid joint integrity—don’t skip this step!
-
Set Up the Welder
Configure your MIG or TIG welder based on the gauge of metal you’re working with. For thin steel, like body panels, set your welder to about 18-20 amps; for aluminum, adjust it to 150-200 amps. Adjust voltage accordingly; higher voltage helps with penetration.
Use a short stick-out (1/4 Inch or 6 Mm) for better control. I prefer the push technique for MIG welding to ensure a clean bead. Double-check your settings before starting—wrong parameters lead to frustration and poor welds!
-
Perform the Welding
Position the panels tightly alongside one another; gaps will create weak spots. Start with tack welds at each corner to hold everything in place. When beginning the full weld, produce beads of about 1 inch (25 Mm); this minimizes warping. Overheating is the enemy!
Monitor the heat as you go—aim for a consistent blue flame; it’s ideal for melting the edges without burning through. Move steadily, not quickly, to maintain a strong weld bead. Watch that puddle; it tells you how well you’re fusing the body panels!
We covered the process of welding body panels. Next, we will cover safety precautions for welding.
Safety Tips
Let’s explore essential precautions for welding body panels.
- Protective Gear: Always wear a welding helmet with the right shade. I recommend a 3M Speedglas helmet for optimal eye safety, as it blocks 99.9% of UV rays.
- Ventilation: Ensure adequate airflow to prevent inhaling harmful fumes. Use a fan or respirator when needed, especially when welding aluminum, like MIG processes. Proper airflow reduces fume-related injuries.
- Fire Safety: Keep a fire extinguisher nearby while welding. I’ve ensured my workspace has a Class B extinguisher for flammable materials—it’s essential!
- Tool Checks: Inspect your tools before welding for defects. Use a multimeter to check your machine’s output. A small issue can create significant safety hazards.
Remember, safety comes first, and I take it seriously—you should too!
So far we covered essential safety guidelines for welding. Next, let’s look at different welding techniques for body panels.
Types Of Welding for Body Panels
Let’s discuss the types of welding you’ll use: MIG, TIG, Spot, Arc, and Laser welding.
-
MIG Welding
MIG (Metal Inert Gas) welding is ideal for body panels. This method uses a continuous wire feed and inert gas to protect the weld. It’s versatile for aluminum and steel and is perfect for patch panels due to its speed, operating at around 30-200 amps. For those interested in specific applications, understanding how it fits into the broader welding by industry can provide valuable insights.
-
TIG Welding
TIG (Tungsten Inert Gas) welding offers high precision. This method uses a non-consumable tungsten electrode and hand-fed filler material. It’s suitable for thin body panels, operating at around 10-300 amps, providing excellent control but taking longer than MIG.
-
Spot Welding
Spot welding efficiently joins two metal pieces. It uses concentrated heat through electrical resistance and is ideal for thin panels. Typically, it operates at 1,000 to 3,000 amps for just a few seconds, creating strong bonds quickly.
-
Arc Welding
Arc welding uses electrical arcs to melt and fuse metals. Though robust, it’s more suited for thicker materials than standard body panels. It operates at variable amperage, providing flexibility, but may not be ideal for delicate work on car panels.
-
Laser Welding
Laser welding employs focused light beams for precise bonds. This method is highly efficient and creates minimal heat-affected zones. It’s best for thin materials in high-speed production, typically using power up to 8 kW.
Common Welding Techniques for Body Panels
Understanding various techniques can improve your welding results. Let’s dive into some common methods.
-
Butt Welding
Butt welding aligns two panels edge to edge. It’s perfect for thin body panels. Tack welds help secure them before fully welding. Aim for a consistent speed to reduce distortion.
-
Lap Welding
Lap welding overlaps two panels. It’s beneficial for thicker materials but can add weight. Clean the joint area thoroughly to ensure a strong bond and adjust settings to minimize burn-through.
-
Tack Welding
Tack welding provides temporary spots to hold parts. It’s essential before completing a full weld. Place several tack welds at least every 6 inches (15 cm) along the joint for stability.
-
Seam Welding
Seam welding creates a continuous bead, especially in long joints. It’s effective for adding structural integrity. Use the correct amperage to prevent warping; typically, a range of 25-40 amps is ideal for body panels. Understanding the intricacies of welding specific components can enhance your skills, such as knowing how to weld thermocouple wire.
Comparison of Welding Techniques
Welding Technique | Ideal Material Thickness | Strength | Use Case |
---|---|---|---|
Butt Welding | 0.5-1.5 mm (0.020-0.060 In) | High | Thin body panels |
Lap Welding | 1.5-3 mm (0.060-0.120 In) | Moderate | Joining thicker parts |
Tack Welding | 0.5-3 mm (0.020-0.120 In) | Variable | Securing panels during assembly |
Seam Welding | 0.5-2 mm (0.020-0.080 In) | Very High | Long joints for structural strength |
Factors Affecting Welding Of Body Panels
What factors influence your technique for joining body panels effectively?
-
Thickness Of Material
Thinner panels, like 0.8 mm (0.031 In), require precise techniques to avoid burn-through. Thicker materials, around 1.5 mm (0.059 In) or more, need more heat and slower travel speeds.
-
Type Of Welding Method
MIG welding is ideal for body panels, especially aluminum, due to its speed and efficiency. TIG welding offers precision for thin sheets, making it perfect for quarter panels while avoiding warping.
-
Welder Experience Level
Your skills significantly impact weld quality. Beginners often struggle with controlling the arc, which affects penetration and leads to weak joints.
-
Environmental Conditions
Welding in windy or cold conditions can cause poor shielding gas coverage. Aim for controlled environments; ideal temperatures are between 16°C and 27°C (60°F and 80°F).
-
Type Of Filler Material
Using the right filler rod is crucial. For aluminum, use ER4047 for better fluidity and strength. Incorrect selection risks structural integrity.
Unique Body Panel Issues
Let’s look at some technical problems specific to body panels.
-
Warpage Of Panels
Body panels can warp if heat isn’t controlled. Look for twisted or misshaped surfaces. Use backing bars to reduce heat. Aim for lower settings and move quickly to minimize heat input.
-
Poor Penetration
Poor penetration in body panels leads to weak welds. Check for shallow welds or gaps. Adjust your welder to a higher voltage and clean surfaces before welding. This often prevents defects.
-
Inconsistency in Weld Beads
Body panels may show uneven weld beads, often due to varying speeds or inconsistent amperage (Amp) settings. Maintain a steady speed and even heat distribution to resolve this.
-
Excessive Heat Input
Excessive heat can damage body panels, causing burnt edges. Look for melted or discolored areas. Use shorter welds and allow cooling between runs to manage heat.
-
Weld Contamination
Body panels may suffer from contamination if surfaces aren’t clean. Check for soot or oxidation on your welds. Always clean the metal using an appropriate solvent or scrub pads before welding.
Aftercare, Inspection, and Advanced Tips for Welding Body Panels
Here’s some crucial info on how to maintain your newly welded body panels.
Aftercare Guidelines
After welding body panels, clean the area with a solvent like acetone to remove contaminants. Then, apply rust-proof primer within 60 minutes to seal exposed welds. Avoid stress on the panels for at least 48 hours to let the heat-affected zone (HAZ) stabilize. Selecting the right class of fire extinguisher for welding tasks is crucial to ensure safety in case of emergencies, which you can learn more about fire safety measures for welding.
Inspection Checkpoints
Start inspection by checking for visible gaps or seams in the welded joints. Use a digital caliper (Accurate to 0.01 Mm or 0.0005 Inches) to measure panel alignment. I recommend 3M’s body panel adhesive for an extra seal on your bonds.
Expert Insights
Experienced welders should always back-purge aluminum welds, especially on thin panels. Use argon gas to reduce oxidation during welding, aiming for a clean bead at a thickness of 1.5 mm (About 0.06 Inches). Ensure your electrode angle is between 15-20 degrees for optimal penetration and strength.
Top Benefits You Can Expect
The biggest perk of knowing how to weld body panels is saving money. You might be surprised, but I used this skill to fix my old car instead of paying a mechanic.
Furthermore, you’ll gain the ability to create strong, lasting joints. Plus, you can work with various materials—think aluminum, steel, or even fiberglass. You’ll also feel a sense of accomplishment and pride in your work. Finally, knowing this skill lets you repair and customize your vehicle just the way you want.
Industry Uses
I’ve known people to use welding techniques to repair damaged vehicles. It also has many applications, such as:
- Restoration Projects: Skilled welders restore classic cars by replacing rusted body panels, which is vital for preserving the vehicle’s integrity and value.
- Custom Modifications: Welders often modify body panels for custom builds, allowing for unique designs and improved aerodynamics.
- Race Cars: Lightweight aluminum body panels are common in race cars. Welding them efficiently boosts performance while ensuring safety.
- Auto Collision Repair: When accidents occur, welding quickly replaces crumpled sections, helping vehicles return to the road safely.
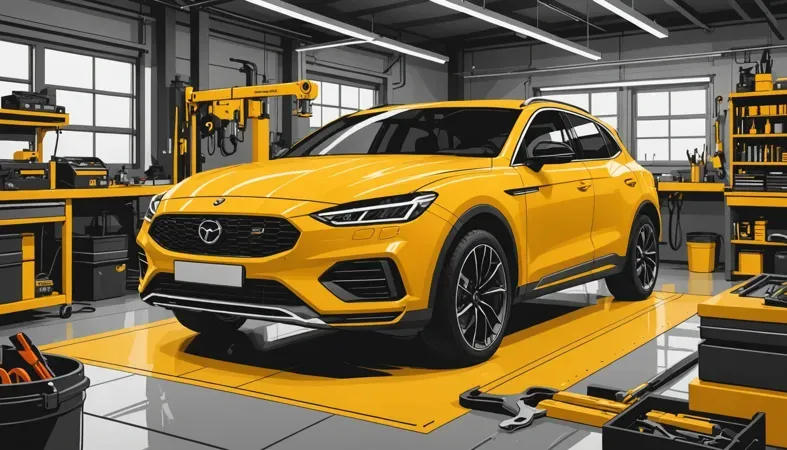
Other Options You Can Consider
When it comes to body panels, you’ve got some great alternatives to welding. For instance, adhesive bonding products, such as 3M Automix Panel Bonding Adhesive, work well when you need a strong, flexible hold. This method’s ideal when working with aluminum body panels since it reduces distortion and heat impact.
Another option is using metal rivets or screws for attaching patch panels. This might be a go-to for beginners or DIYers who want to avoid the mess of welding completely. Plus, tools like the Huxley Bar Riveter provide a solid, effective hold without warping the metal.
Frequently Asked Questions (FAQs)
Now let us look at some common questions I typically get asked.
What is the Best Way to Weld Body Panels Together?
The best way to weld body panels together is to use MIG welding. MIG welding allows for a strong bond and is less likely to warp thin metal sheets. It also requires less skill compared to TIG welding and has a faster welding speed, making it ideal for automotive repairs. Understanding what causes crater cracks is crucial to improve weld quality and efficiency.
What Kind Of Welder for Body Panels?
The best kind of welder for body panels is a MIG welder. MIG welders work well with thinner metals commonly found in car body panels. Look for a unit that can manage 120-220 amps, which provides enough power for most body panel projects.
Is MIG or TIG Better for Body Panels?
MIG is generally better for body panels than TIG. MIG is easier to use, especially for beginners, and is faster for larger projects. Also, MIG uses a continuous wire feed that helps maintain a consistent weld, which is essential for body repairs.
What is the Best Way to Weld Sheet Metal Panels?
The best way to weld sheet metal panels is using a MIG welder with a short-circuit transfer process. This technique minimizes heat input and reduces the risk of burn-through, which is important for thin metal like automotive sheets.
How to Weld Patches on a Car?
You can weld patches on a car using a MIG welder with a proper setup. Make sure to clean the areas and use a clamp to hold the patch while welding. This ensures a precise fit and reduces warping caused by heat.
How to Install Patch Panels Without Welding?
You can install patch panels without welding by using adhesive bonding techniques or using self-piercing rivets. Adhesives provide a strong bond and are often quicker than welding, providing a neat and clean installation.
Conclusion
We’ve reached the end, and I appreciate you sticking around. We covered what body panels are, types of body panels, prerequisites, safety tips, and the steps to weld body panels. We also discussed unique issues, factors affecting welding, and the top benefits of mastering how to weld body panels.
So, how to weld body panels? In essence, it comes down to understanding the types of panels and using the right welding techniques like MIG, while keeping safety in mind. To get started, gather your tools, follow proper safety measures, and practice your skills. If you’d like more guidance, contact me.
For further insights and information, What is Welding is a fantastic resource to enhance your understanding.
References
- American Welding Society. (2015). AWS D1.1/D1.1M: Structural Welding Code – Steel. Miami, FL: AWS.
- American Welding Society. (2020). AWS A3.0: Standard Welding Terms and Definitions. Miami, FL: AWS.
Joe Carter is a retired welding professional with over 40 years of hands-on experience in the industry, spanning ship repair, structural welding, and even underwater projects. Joe is a master of MIG, TIG, and Stick welding. Passionate about mentoring the next generation of welders, Joe now shares his decades of expertise and practical insights to help others build rewarding careers in welding.
American Welding Society, Automotive Repair, Body Panels, MIG Welding, Safety Tips, Welding, Welding Table, Welding Techniques