How Hot to Pre-heat Aluminum for TIG Welding? Tips, Steps, and Safety Insights
Published on: November 16, 2024 | Last modified: March 4, 2025
By: Joe Carter
Pre-heating is the process of warming up aluminum before welding. It helps improve the quality and strength of the weld.
It’s a question I’ve heard often: how hot to pre-heat aluminum for tig welding? Knowing the right temperature is crucial because if it’s too cold, you might get cracking or poor fusion. I’ve seen firsthand how it affects my welds – when pre-heating’s done right, it makes a huge difference in the final product.
In this guide, we’ll cover how hot to pre-heat aluminum for tig welding, different types of pre-heating, what you’ll need, steps to pre-heat aluminum, safety tips, types of heat settings, factors affecting pre-heating, common issues, inspection after welding, key benefits, typical applications, and when to try a different approach. Whether you’re learning how to tig weld aluminum for beginners or just brushing up on techniques, you’ll find the answers you need.
Contents
- How Hot to Pre-heat Aluminum for Tig Welding?
- What is Pre-heating?
- Types Of Pre-heating
- Things You’ll Need
- Steps to Pre-heat Aluminum for TIG Welding
- Safety Tips
- Types Of Heat Settings for Pre-heated Aluminum
- Factors Affecting Pre-heating Aluminum
- How Temperature Variations Affect Pre-heating Aluminum for TIG Welding
- Impact of Different Aluminum Alloys on Pre-heating
- Common Issues You Might Encounter
- Aftercare, Inspection, and Advanced Tips
- Key Benefits
- Typical Applications
- When to Try a Different Approach
- Frequently Asked Questions (FAQs)
- Summary
- References
How Hot to Pre-heat Aluminum for Tig Welding?
Pre-heating is warming aluminum before welding. So, how hot to pre-heat aluminum for tig welding? Aim for 150-200°F (65-93°C) to reduce cracking. It can be tricky and works well in thicker sections or critical applications.
What is Pre-heating?
Pre-heating is the process of warming aluminum before welding. This technique reduces the risk of cracking and improves weld quality. Typically, you pre-heat aluminum to temperatures between 100°F and 300°F (38°C to 149°C). This step increases thermal conductivity and ensures better fusion during welding.
When pre-heating aluminum for TIG welding, aim for a specific temperature based on the aluminum alloy. In my experience, it’s best to use an infrared thermometer to monitor the temperature. A consistent heat helps prevent mistakes when joining aluminum for complex projects.
In my experience, I used pre-heating to address tricky aluminum joints. This technique was essential for preparing aluminum for TIG welding. The results were impressive; every joint became stronger and more reliable, showing that attention to detail adds significant value in processes like welding aluminum with TIG.
Types Of Pre-heating
What types of pre-heating can you use when working with aluminum?
-
Indirect Pre-heating
This method uses external heat sources, like an oven or heating blankets. Aim for around 150-300°F (65-150°C). Place the aluminum in a controlled environment, such as an oven set to the correct temperature, for 30 to 60 minutes.
-
Direct Pre-heating
This approach applies heat directly with a torch or heating unit. Aim for about 200-400°F (93-204°C). Move the torch evenly over the surface and check with an infrared thermometer until you reach the desired temperature.
-
Localized Pre-heating
This method targets specific areas of the aluminum. Aim for about 250-350°F (121-177°C). Concentrate your torch on the area you plan to weld, keeping it there until it’s hot enough.
-
Uniform Pre-heating
This technique ensures an even temperature across the piece. Aim for a range of 200-350°F (93-177°C). Use a heating blanket or move the torch evenly until the entire aluminum surface reaches the target temperature.
-
Spot Pre-heating
This method involves quick heating in small areas. Target approximately 300-400°F (149-204°C). Use a torch to heat small spots on the aluminum before welding, keeping each spot in motion to avoid overheating.
It’s also important to be aware of toxic substances in welding that could pose health risks.
You should now have a good understanding of various pre-heating methods. In the next part, we’ll discuss necessary materials and tools.
Things You’ll Need
What do you need to start preheating aluminum for TIG welding?
- Heat exchanger or torch: You’ll need a quality torch, like the Miller Electric M-15 Series, which provides precise heat control for effective preheating.
- Infrared thermometer: A tool like the Etekcity Lasergrip 800 measures surface temperatures accurately, helping you reach the optimal preheat level of 150-250°F (65-121°C).
- Heat-resistant blanket: Use a blanket such as the Tillman 1650 to protect surrounding areas from heat damage during the process.
- Thermal insulation panels: Items like CeramaBraid® thermal insulation are essential for maintaining the right temperature while you weld.
That covers the necessary materials for the process. Let’s now take a look at how to pre-heat aluminum for TIG welding.
Steps to Pre-heat Aluminum for TIG Welding
Here are the essential steps to pre-heat aluminum for successful TIG welding.
-
Adjust the Temperature Settings
Set your welding torch to about 150°C to 200°C (302°F to 392°F). This range works for most aluminum alloys. For different alloys, you may need slight adjustments. Aim for a spot that ensures optimal fusion without overheating. If you ever need to correct a mistake or refine a joint, learning the appropriate techniques on how to remove welds can be invaluable.
TIG welding can be tricky; if you’re working with 6061 aluminum, stick to the lower end of the range. High temperatures can warp your material. Take your time and test as you go.
-
Use a Heat Source to Pre-heat
Use a propane torch or similar heat source to evenly warm the aluminum. Move the torch in circular motions, keeping it at least 10 to 15 cm (4 to 6 Inches) away from the surface to prevent excessive localized heat. Gradual heating allows the aluminum to expand properly.
Heat the area you’d be welding for at least 5 to 10 minutes. This duration may vary depending on the part’s thickness. Remember, patience pays off.
-
Monitor Surface Temperature
Monitor the surface temperature with an infrared thermometer. Aim for a consistent reading of 150°C to 200°C (302°F to 392°F) across the plate. Consistency is crucial! Missing temperature readings can ruin weld quality.
Check multiple points to avoid cool spots. Aluminum cools quickly, especially in thick areas. Knowing your surface temperatures results in stronger welds with less distortion.
-
Evaluate Pre-heating Effectiveness
Before welding, pinch a test piece of aluminum. It should feel warm, not too hot to hold. If it feels cold, give it more time. Skipping this step can lead to poor penetration or porosity in your welds.
Minimizing welding defects is crucial for a smooth finish which includes learning how to avoid spatter during the process.
.
Be confident in the pre-heat. Once it passes the pinch test, you’re ready. This small test can save you a lot of hassle later.
We’ve wrapped up the steps to pre-heat aluminum for TIG welding here. Next up, we’ll look at safety tips.
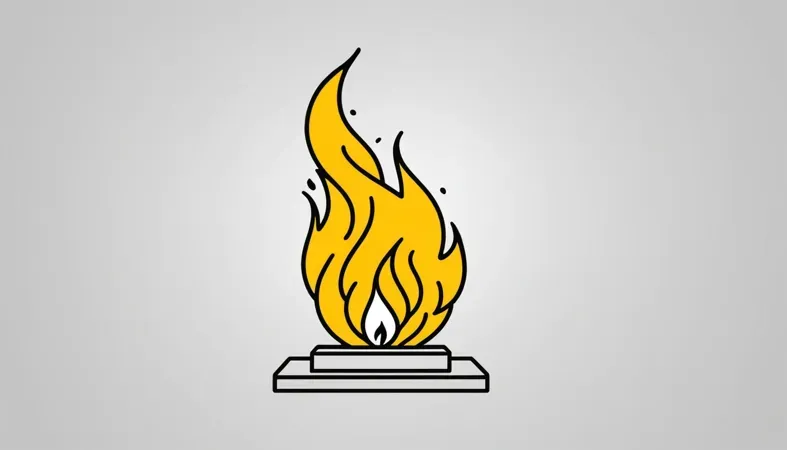
Safety Tips
Let’s quickly review key precautions for preheating aluminum.
- Temperature Monitoring: Use an infrared thermometer for accurate readings; I recommend the Fluke 62 Max. It’s crucial to prevent overheating.
- Ventilation: Ensure your workspace is well-ventilated; use fans or exhaust systems if possible. This prevents inhaling harmful fumes.
- Protective Gear: Always wear appropriate safety gear like gloves and goggles. Mixing aluminum welding with heat can burn your skin.
- Even Heating: Preheat aluminum evenly for the best results; a BBQ propane torch works well here. This avoids warping during welding.
Never underestimate the importance of safety precautions; they’re essential for your well-being!
So far we covered essential safety tips. Next, let’s look at various types of heat settings for pre-heated aluminum.
Types Of Heat Settings for Pre-heated Aluminum
Let’s discuss the types of heat settings: low, medium, high, variable, and consistent temperature settings.
-
Low Temperature Settings
Low temperature settings typically range from 100°F to 200°F (38°C to 93°C). They’re suitable for very thin aluminum, about 1/16 inch (1.6 Mm) thick. Warping is less likely, making them ideal for beginners.
-
Medium Temperature Settings
Medium temperature settings range from 200°F to 400°F (93°C to 204°C). These work well for aluminum thickness between 1/16 inch (1.6 Mm) and 1/8 inch (3.2 Mm). This heat level balances weld penetration and distortion effectively. Proper helmet adjustment can enhance safety and precision during welding tasks, and you can learn more about how to adjust welding helmet.
-
High Temperature Settings
High temperature settings range from 400°F to 600°F (204°C to 316°C). These heat levels suit thicker metal, over 1/8 inch (3.2 Mm). However, monitor for excessive melting or distortion.
-
Variable Heat Settings
Variable heat settings let you adjust the temperature dynamically during the welding process. This feature helps manage different thicknesses seamlessly, making it a favorite for professionals. It provides more control for intricate projects.
-
Consistent Temperature Settings
Consistent temperature settings maintain steady heat throughout the weld, typically ranging from 300°F to 500°F (149°C to 260°C). They’re great for projects needing uniformity without the risk of overheating, ensuring a clean weld each time.
Factors Affecting Pre-heating Aluminum
What factors influence the temperature for preparing aluminum before TIG welding?
-
Thickness Of Aluminum
The thicker the aluminum, the more pre-heat you’ll need. For example, 1 inch (25.4 Mm) thickness may require temperatures of 300°F (149°C) or more.
-
Type Of Aluminum Alloy
Knowing your alloy is crucial. The 6000 series typically requires less pre-heat than the 2000 series, which can significantly impact your preparation and final weld strength.
-
Ambient Temperature
In colder environments, you may need to raise pre-heat temperatures to around 250°F (121°C) to prevent cracking.
-
Welding Speed
Faster welding speeds can cool the material quickly, so slightly higher pre-heat can compensate. Aim for around 350°F (177°C) for high-speed welds.
-
Heating Method Used
Methods like flame or induction heating vary in effectiveness. Induction heating targets the aluminum directly and achieves rapid, uniform temperatures crucial for the best weld.
How Temperature Variations Affect Pre-heating Aluminum for TIG Welding
Understanding how temperature variations can impact your pre-heating process for aluminum TIG welding is essential.
Temperature Variation | Effect on Weld Quality | Recommended Action |
---|---|---|
Under 150°F (65°C) | High risk of cracking and poor fusion. | Increase pre-heat duration. |
150°F to 200°F (65°C to 93°C) | Optimal range for most aluminum alloys. | Proceed with welding, monitoring closely. |
200°F to 250°F (93°C to 121°C) | Good for thicker materials; enhances penetration. | Adjust heat if working in colder environments. |
Over 250°F (121°C) | Increased risk of distortion and burn-through. | Lower heat immediately and cool down the material. |
Impact of Different Aluminum Alloys on Pre-heating
Different aluminum alloys can significantly influence how to pre-heat them before TIG welding.
- 1000 Series: Minimum pre-heat needed. Focus on cleanliness.
- 2000 Series: Higher heat required, around 250°F (121°C) to reduce cracking.
- 6000 Series: Moderate pre-heat of 150°F to 200°F (65°C to 93°C) works best.
- 7000 Series: Needs careful monitoring; pre-heat to 200°F (93°C) to prevent stress cracks.
Common Issues You Might Encounter
Let’s examine problems that can arise during the pre-heating process.
-
Inconsistent Temperature Distribution
Pre-heating aluminum requires uniform heat. If it’s not consistent, parts may weld poorly. Use an infrared thermometer to check temperatures in different spots. Adjust your heat source for balance. Understanding the technical considerations involved in welding different materials is crucial, especially when you need to weld a gas tank safely.
-
Overheating the Aluminum
Pre-heating can lead to overheating, especially in thin sections. Check the area often with a digital probe to avoid exceeding 300°F (150°C). If you see discoloration, lower the heat.
-
Burn-through Risks
Excessive pre-heating increases burn-through risk. Check the base material’s thickness; if it’s below ¼ in (6 Mm), reduce the pre-heat time.
-
Oxidation on the Surface
Pre-heating can cause oxide layers on aluminum, preventing good weld penetration. Inspect the surface and use a clean stainless steel brush to remove any buildup before welding.
-
Cracking During Welding
Pre-heating helps reduce cracking but can also create it if unevenly applied. Monitor your heat gradually—cool in 10°F (5°C) increments. Check for cracks immediately after welding; if any form, revisit your pre-heat process.
Aftercare, Inspection, and Advanced Tips
Here’s specific guidance for what to do after pre-heating aluminum for TIG welding.
Aftercare Recommendations
After reaching the optimal pre-heating temperature of around 150°C (300°F), gradually shift the heat away or use a heat sink, like aluminum blocks, to avoid thermal shock. Keep your work area at a stable 24°C (75°F) to maintain integrity during cooling.
Inspection Duties
Inspect the weld for distortion and warping from heat. Use a straightedge tool to check alignment; any deviation beyond 0.5 mm (0.02 In) may need correction. Tools like the Starrett Adjustable Parallel are invaluable for precise inspections.
Expert Tips
Experienced welders should aim for a uniform temperature gradient. Use digital infrared pyrometers for accuracy, targeting a reading of 120-150°C (250-300°F). Maintaining controlled pre-heat significantly reduces the risk of cracks; aim for a consistent heat profile over debrittled zones.
Key Benefits
The main benefit of knowing how hot to preheat aluminum for TIG (Tungsten Inert Gas) welding is improved weld quality. In my experience, it helped reduce cracking and ensure a strong bond.
Additionally, preheating enhances penetration, decreases distortion, minimizes oxidation, and promotes smoother arc stability. These factors combined lead to a cleaner, more reliable weld.
Typical Applications
I’ve known people to use preheating for TIG welding aluminum, especially in high-stress projects. It also has numerous unique applications, such as:
- Aerospace Components: Used to bond parts like wing frames. Preheating reduces cracking and increases strength under extreme conditions.
- Marine Hulls: Ideal for welding aluminum boats. Preheating prevents warping in large panels, ensuring durability against corrosion.
- Automotive Parts: Essential for components like engine mounts. Preheating improves the flow of the filler material, achieving clean welds.
- Custom Bike Frames: Many custom shops preheat tubes to ensure solid joints. It helps fit different metals together seamlessly, creating lightweight frames.
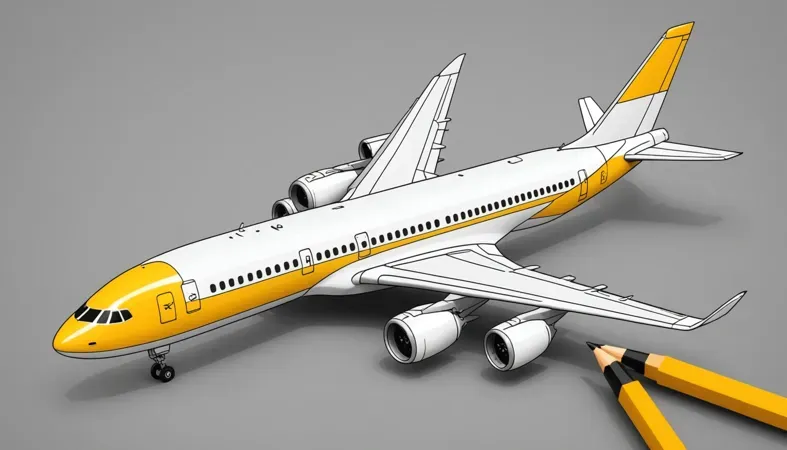
When to Try a Different Approach
Sure, pre-heating’s great, but you’ve got alternatives! Using an aluminum heat blanket, such as an Ace Heat Blanket, can distribute heat evenly without direct flame. You might also consider a heat gun like the Milwaukee M18, which’s effective for smaller projects or intricate welds.
In some cases, a torch can do the trick too. Just remember, whether you choose a blanket or heat gun, the key’s to get that material warm enough for proper fusion. I’ve often found myself thinking that exploring these methods can simplify the process while still yielding excellent results.
Frequently Asked Questions (FAQs)
Now let’s look at some common questions I typically get asked about pre-heating and TIG welding aluminum.
What is the Recommended Pre-heating Temperature for Aluminum?
Yes, the recommended pre-heating temperature for aluminum is typically between 150°C to 260°C (300°F to 500°F). Pre-heating reduces the risk of cracking during welding by increasing the material’s ductility and promoting better fusion.
How Do You Prepare Aluminum for TIG Welding?
To prepare aluminum for TIG welding, you should clean the surface thoroughly with a solvent and wire brush. This process removes oxides and contamination, ensuring the weld pool’s integrity and minimizing flaws.
What is the Best Setting for TIG Welding Aluminum?
The best setting for TIG welding aluminum varies, but commonly recommended settings include around 100 to 200 amps depending on material thickness. Adjusting the AC frequency and balance controls enhances penetration and cleaning action.
Can You TIG Weld Aluminum Without Pre-heating?
Yes, you can TIG weld aluminum without pre-heating, but it might lead to issues like cracking. Pre-heating provides better results, especially in thicker sections or high-stress applications, so it’s often recommended for improved weld integrity. Understanding how electrode classifications like E316 16 indicate properties can further enhance welding outcomes.
How to Weld Aluminum With a TIG Welder?
To weld aluminum with a TIG welder, you’ll need a clean surface, proper filler rod, and suitable settings. Using an AC current typically provides better results for aluminum due to its oxidation layer.
Summary
We are almost done. We covered how hot to pre-heat aluminum for TIG welding, the importance of pre-heating, different pre-heating methods, necessary tools, essential steps, safety tips, heat settings, factors affecting heat application, potential issues, post-welding care, benefits, applications, and when to consider alternatives. This gives you a rounded understanding of successfully preparing aluminum for welding.
In short, you should pre-heat aluminum to around 300°F (150°C) for optimal results. This process helps reduce cracking and improves weld quality. Happy welding, and remember: well-prepped aluminum means stronger seams and a smoother experience during the TIG welding journey.
For further insights and resources on welding, we invite you to explore our main page: What is Welding where you’ll find a wealth of information to enhance your knowledge.
References
- American Welding Society (AWS): https://www.aws.org
Joe Carter is a retired welding professional with over 40 years of hands-on experience in the industry, spanning ship repair, structural welding, and even underwater projects. Joe is a master of MIG, TIG, and Stick welding. Passionate about mentoring the next generation of welders, Joe now shares his decades of expertise and practical insights to help others build rewarding careers in welding.
Aluminum Alloys, Aluminum Pre-heating, Aluminum Welding, American Welding Society, Safety Tips, TIG Welding, Welding, Welding Techniques, Welding Temperature