How Long Does JB Weld Take to Dry? Essential Drying Times and Factors
Published on: November 22, 2024 | Last modified: March 4, 2025
By: Mark Carter
JB Weld is a strong epoxy adhesive. It’s great for repairing metal, plastic, and more.
So, how long does jb weld take to dry? Well, it’s crucial to know this for your projects. In my experience, rushing might lead to weak bonds or messy repairs, which you won’t want, right? The drying time for JB Weld typically depends on the specific product you’re using, but most variants set in 4-6 hours and fully cure in 15-24 hours.
Patience is key because a proper cure ensures a strong, durable bond that you can rely on. Once applied and fully cured, you’ll also be glad to know how long JB Weld lasts, as its bonds are designed to withstand years of wear and tear in a variety of conditions.
In this guide, we’ll cover how long it takes for jb weld to dry, the various types of JB Weld, prerequisites for use, application steps, precautions to take, different drying times, factors affecting drying, unique issues, aftercare and inspection, advantages of using JB Weld, its real-world applications, and alternatives. You’ll get a complete view!
Contents
- How Long Does JB Weld Take to Dry?
- What is JB Weld?
- Types Of JB Weld
- Prerequisites
- Precautions
- Steps to Apply JB Weld
- Types Of Drying Times for JB Weld
- Factors Affecting JB Weld Drying Time
- Understanding JB Weld Drying Under Various Conditions
- Unique Issues
- Aftercare and Inspection Tips
- Why This is Worth It: Advantages
- Real-world Uses for JB Weld
- Exploring Alternatives to JB Weld
- Frequently Asked Questions (FAQs)
- Conclusion
- References
How Long Does JB Weld Take to Dry?
JB Weld is a strong epoxy adhesive. So, how long does JB Weld take to dry? It typically takes 4-6 hours to cure fully at 24°C (75°F). Expect difficulty in applications needing quick bonding, like auto repairs.
What is JB Weld?
JB Weld is a two-part epoxy adhesive known for its strong bonding properties. It consists of a resin and a hardener that, when mixed, create a durable, heat-resistant bond. The tensile strength of JB Weld can reach up to 5020 psi (Pounds Per Square Inch) or about 34.6 MPa (Megapascals). It can withstand temperatures up to 550°F (288°C) when cured, making it versatile for indoor and outdoor applications.
Now, let’s explore how long JB Weld takes to dry. It typically sets in about 4 to 6 hours, though full curing may take 15 to 24 hours. I’ve noticed that in cooler temperatures, the curing process can feel slower, but it’s worth the wait for that strong bond.
Keep in mind that the exact drying time can vary depending on the specific conditions and thickness of the application. If you’re working in a colder environment, you may want to allow for extra time before handling the bonded materials.
A friend of mine used JB Weld to fix a cracked engine block. They were amazed at how quickly it set, and within hours, they were back on the road. Depending on how long you let JB Weld cure, it can range from that initial set time to a full day for a solid final bond. Knowing how long JB Weld takes to dry can save you a headache, especially for critical repairs.
Types Of JB Weld
Original JB Weld
This classic epoxy provides strong bonding. It typically dries in 4 to 6 hours, but it’s best to let it cure for 15 to 24 hours.
JB Kwik Weld
This fast-setting adhesive bonds quickly, drying in about 4 to 6 minutes. To speed up the process, keep it in a warm area, and it can fully set in 1 hour.
JB Waterweld
This type works well on wet surfaces, drying in 15 to 25 minutes. For better adhesion, roughen the surface before application and let it set for about 1 hour.
JB Highheat Weld
This epoxy withstands high temperatures. It takes about 1 hour to dry. To ensure a strong bond, apply it to heat-resistant surfaces and allow 16 to 24 hours for a full cure.
JB Plasticweld
This is specially designed for plastics, drying in about 20 to 30 minutes. For optimal strength, mix thoroughly and let it cure for 1 to 3 hours after application.
We’ve wrapped up the various types of JB Weld here. Next up, we’ll look at the necessary prerequisites.
Prerequisites
What do you need to start the JB Weld process?
- JB Weld Product: Use JB Weld Original, like the 8265S kit. It’s the classic choice for strong bonding.
- Mixing Tool: A small mixing stick, such as a craft stick or toothpick. You’ll blend the two parts for the best results.
- Application Tool: A quality putty knife, like the 3M Auto Body Putty Knife. This helps apply the mixture smoothly.
- Sanding Tool: 120-grit sandpaper. It’s used for prepping (Preparing) and smoothing the surfaces before application.
We covered the necessary prerequisites here. Next, we will cover important precautions to consider.
Precautions
Here are essential safety tips for proper drying.
- Ventilation: Always work in a well-ventilated area. Poor airflow can concentrate fumes. Open windows and use fans.
- Gloves: Wear protective gloves to avoid skin contact, which can cause irritation or burns. Consider using nitrile gloves.
- Temperature: Keep the temperature above 50°F (10°C) for optimal curing speed. Cold slows down drying.
- Storage: Store JB Weld in a cool, dry place, away from sunlight. Heat can reduce its effectiveness. Aim for below 75°F (24°C).
These precautions are vital—stay safe!
You should now have a good understanding of safety measures, tips, and precautions. In the next part, we’ll discuss how to apply JB Weld.
Steps to Apply JB Weld
Here are the steps for effectively drying JB Weld. Follow these closely for the best results.
Prepare the Surface
Start by cleaning the surfaces you’ll bond. Use a wire brush or sandpaper to remove dirt, grease, and rust. Ensure the area is dry—moist surfaces can weaken JB Weld’s grip. This stage is critical; even a tiny bit of grime can lead to failure.
Check that surfaces fit together well and that there are no gaps. If they aren’t even, fill the gaps with extra weld, which will add to drying time. The ideal application temperature is 21-27°C (70-80°F). Warmer temps speed up drying.
Mix the JB Weld
Next, thoroughly mix equal parts of resin and hardener. Use a clean, disposable stir stick and mix until uniform—about one minute. A proper mix is vital; insufficient mixing may prevent hardening. Temperature can affect the chemical reaction’s activity!
Apply the JB Weld mixture within 30 minutes for best results. Don’t rush, but keep an eye on the clock! In cooler environments, it may take longer to set. Don’t overlook this mixing step; it’s your foundation!
Apply the Mixture
Use a clean tool or spatula to smoothly spread the mixed JB Weld onto the prepared surfaces. Ensure even coverage. The recommended application thickness is at least 0.5 mm (0.02 In). Avoid applying too much, as this will prolong drying time. Welding processes, especially those involving materials like galvanized steel, can have serious safety implications. It’s important to understand the risks involved when working on such projects including potential hazards with galvanized steel.
Don’t disturb the bond once applied. Even slight movement can compromise what you’re trying to create. It’s important to leave it alone while it sets; patience pays off here.
Clamp and Secure
After applying the mixture, use a clamp or weight to press the pieces together. This ensures a solid bond. Clamping for 2-6 hours gives JB Weld a chance to form a strong attachment. Insufficient clamping or shifting could lead to failure.
For larger pieces, use multiple clamps for even pressure. Check periodically to keep everything aligned. Avoid slip-ups here. Be firm but not excessive with your pressure!
Allow to Cure
Now comes the hard part: letting it cure. JB Weld generally takes about 4-6 hours to set for light handling, but for a full cure, expect to wait 15-24 hours. Avoid stressing the bond during curing. Temperature, humidity, and thickness will influence the duration. When learning about techniques like welding, understanding how to weld vertical surfaces is crucial for achieving stable connections.
If you need faster results, expose the bond to gentle heat, but don’t overdo it. An ideal curing environment speeds up strength. Keeping everything at around 21-27°C (70-80°F) helps significantly.
So far we covered the process for applying JB Weld. Next, let’s look at the different drying times for JB Weld.
Types Of Drying Times for JB Weld
Let’s explore the different drying times for JB Weld: Fast Cure, Standard Cure, Extended Cure, High-Temperature Cure, and Cold Weather Cure.
Fast Cure
Fast Cure JB Weld sets in 4 to 6 hours and achieves 50% strength in just 1 hour. This option is ideal for quick fixes.
Standard Cure
The Standard Cure option takes 15 to 24 hours to set and reaches full strength in about 24 hours. This is a dependable choice for most repairs.
Extended Cure
Extended Cure JB Weld takes 30 to 48 hours to dry fully. It’s strong under stress and perfect for heavy-duty repairs. Choose this for projects needing extra time.
High-temperature Cure
High-Temperature Cure JB Weld withstands temperatures up to 500°F (260°C) and cures fully in 24 hours. This is a reliable option for heat-related repairs.
Cold Weather Cure
Cold Weather Cure JB Weld is designed for temperatures below 40°F (4°C) and may take longer to cure, generally about 24 to 48 hours. This type is essential in chilly conditions.
Factors Affecting JB Weld Drying Time
What factors influence JB Weld’s drying time? Here’s a quick look.
Ambient Temperature
Higher temperatures speed up chemical reactions. For every 10°C (18°F) increase, JB Weld’s curing accelerates by about 50%. At ideal temperatures around 21-27°C (70-80°F), JB Weld can set in just 4 to 6 hours.
Humidity Levels
Low humidity promotes faster drying. When humidity’s above 60%, it can slow curing by causing moisture inhibition (Delay). A dry environment ensures better adhesion and quicker curing.
Surface Material
The surface material is crucial. Non-porous surfaces, like metals, cure faster than porous materials, like wood, which tends to absorb moisture and affects drying time.
Thickness Of Application
Thicker applications take longer to cure. JB Weld cures from the outside in; a heavy layer may take hours longer than a thin layer. Aim for a thickness of about 1/8 inch (3.2 Mm) for optimal drying.
Mixing Ratio
JB Weld must be mixed in the correct ratio to cure properly. Deviating from a 1:1 ratio of resin to hardener can lead to poor curing. Follow the instructions for the best results.
Understanding JB Weld Drying Under Various Conditions
Other than just the basic drying time, let’s dive deeper into how different settings impact JB Weld effectiveness.
Condition | Recommended Temperature (°C/°F) | Drying Time | Notes |
---|---|---|---|
Optimal Conditions | 21-27 °C (70-80 °F) | 4-6 hours | Ideal for fast drying and strong bond formation. |
High Humidity | Above 60% RH | Variable; 6-12 hours or longer | Moisture can delay curing; ensure a dry environment. |
Cold Temperatures | Below 10 °C (50 °F) | 12-48 hours | Cold slows down the curing process significantly. |
High Temperatures | Above 38 °C (100 °F) | 2-4 hours | Can accelerate drying, but extreme heat risks damaging bond strength. |
Thicker Application | N/A | 8-36 hours | Thicker layers take longer to dry; keep applications thin. |
By knowing how various conditions affect JB Weld drying, you can optimize your repairs for the best results every time.
Unique Issues
Let’s look at several unique challenges with JB Weld.
Inconsistent Drying Times
JB Weld’s drying times vary with temperature and moisture. If it’s tacky after 24 hours, it’s drying slowly. Apply heat, but don’t exceed 150°F (65°C) to resolve it.
Adhesion Failures
JB Weld might fail to stick if surfaces aren’t clean; I’ve seen it too often! Cleaning is crucial—use acetone to wipe the surfaces. If it fails, sand the area before reapplying.
Impact Of Overheating
JB Weld breaks down above 500°F (260°C). Look for cracked or brittle areas. If overheated, you’ll need to remove it and reapply in a cooler environment.
Compatibility With Other Materials
JB Weld doesn’t bond well with plastics. You may notice separation after curing. To fix this, use a primer specifically for plastic before applying JB Weld.
Difficulty in Removal
Removing JB Weld can be tough. If you need to, pure acetone or a chisel helps. It’s too strong if ordinary tools don’t work—grab a heat gun for easier removal.
Aftercare and Inspection Tips
Here’s specific advice for maintaining JB Weld after application and inspecting its quality.
Aftercare Suggestions
After mixing and applying JB Weld, let it cure for 15 to 24 hours at room temperature (20 to 25 °C or 68 to 77 °F). Keep the area free from stress or movement until it fully sets. For maximum durability, avoid moisture exposure for the first 24 hours to prevent weakening the bond. A critical aspect of weld quality can be seen in the importance of the hot pass in welding processes.
Inspection Guidance
Inspect the JB Weld bond for uneven surfaces or air bubbles; these may indicate an insufficient mix. Use a digital caliper for precise measurements based on application specifications. Ideally, the bond thickness should consistently measure around 1 to 3 mm (0.04 To 0.12 In). I use a Dremel tool for checking potential imperfections.
Advanced Tips
If you’re experienced, consider using a heat gun to speed up the curing process in cool conditions. Remember, JB Weld sets best at around 25 °C (77 °F). For underwater or high-stress applications, layering JB Quik may increase strength and accelerate setting time.
Why This is Worth It: Advantages
The main benefit of knowing how long JB Weld takes to dry is timing. A friend used it to fix a broken pipe quickly, and it saved the day!
It also boosts confidence in your repairs, ensures stronger bonds, enhances productivity, and reduces stress. Knowing the drying time helps you plan your project and prevents unexpected delays.
Real-world Uses for JB Weld
People use JB Weld for automotive repairs, but it has many unique applications, such as:
- Aerospace Manufacturing: JB Weld bonds lightweight materials like composites and metals. It’s popular for repairing aircraft components where durability and weight are important.
- Marine Repair: Many boat owners use JB Weld for hull repairs since it adheres well to fiberglass. Its water-resistant properties make it a preferred choice for watercraft.
- Plumbing Repairs: JB Weld works well on metal pipes. It’s often used for quick leak fixes, especially in emergencies when traditional methods can’t work fast enough.
- Electronics Repair: Technicians frequently use JB Weld to fix circuit boards. Its heat-resistant properties ensure it withstands temperature changes, making it a go-to for gadget repairs.
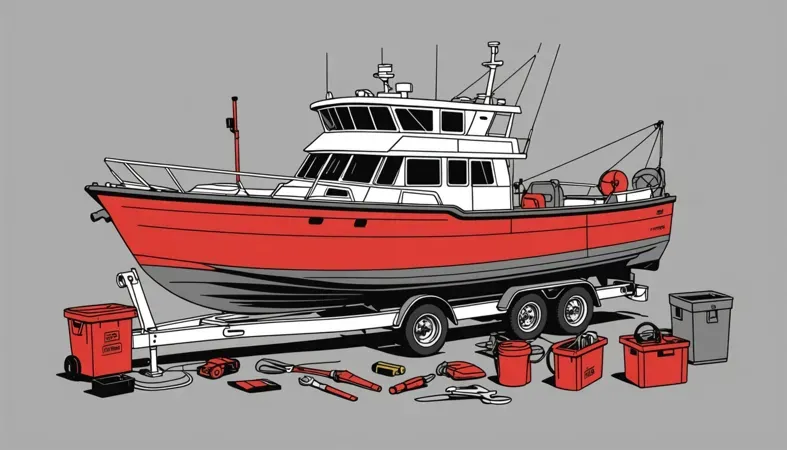
How long does JB Weld take to dry when repairing your boat?
Exploring Alternatives to JB Weld
If there’s one thing I’ve gained from my journey, it’s that there are reliable alternatives to JB Weld. Products such as Loctite Epoxy Weld or Gorilla 2-Part Epoxy can provide similar bonding strength. You might prefer these options for their faster drying times or easier application methods, which are discussed among various welding alternatives that can meet your needs.
Additionally, consider using Mighty Putty or epoxy sticks when you need a quick fix on smaller projects. These alternatives often cure in less than an hour, saving you time. Remember, always follow product instructions for the best results!
Frequently Asked Questions (FAQs)
Now let us look at some common questions I typically get asked about JB Weld.
Can You Make J-B Weld Dry Faster?
Yes, you can make J-B Weld dry faster. To speed up the drying process, apply heat using a heat gun or an infrared lamp. Heat increases the molecular activity and can reduce drying time significantly, cutting down the time from several hours to as little as 30 minutes.
What Will J-B Weld Not Stick to?
J-B Weld will not stick to certain surfaces, including silicone, Teflon, and other types of plastic. This happens because these materials have low surface energy, preventing proper adhesion. Always check materials first to ensure a solid bond.
Is J-B Weld As Strong As a Real Weld?
No, J-B Weld is not as strong as a real weld. Traditional welding fusion bonds metals, achieving tensile strength ranging from 30,000 to 50,000 psi (Pounds Per Square Inch). J-B Weld, while durable, typically reaches a tensile strength of around 3,960 psi. Welding upside down requires specific techniques and precautions, especially considering the challenging positions and the gravitational pull on the molten metal, as described in this guide on welding upside down.
Can You Apply a Second Layer Of J-B Weld?
Yes, you can apply a second layer of J-B Weld. However, you should wait until the first layer completely cures before adding another. This ensures maximum adhesion, which will help the overall strength of your repair.
How Long Should You Wait Before Using J-B Weld?
You should wait at least 4 to 6 hours before using J-B Weld for light loads. For optimal bonding strength, full cure takes about 15 to 24 hours at room temperature, allowing the repair to handle tougher conditions.
Does Temperature Affect J-B Weld Drying Time?
Yes, temperature does affect J-B Weld drying time. Warmer temperatures expedite drying, while colder environments can slow the curing process significantly. For the best results, maintain temperatures between 21°C to 38°C (70°F to 100°F) during application.
Can J-B Weld Be Used on Underwater Repairs?
Yes, J-B Weld can be used for underwater repairs. J-B Weld’s WaterWeld variant is specifically formulated for wet conditions and can set underwater. It works great for plumbing and marine applications, providing a strong bond even when submerged.
What Happens if I Sand J-B Weld Too Soon?
If you sand J-B Weld too soon, you risk damaging the bond. Sanding before the adhesive fully cures can weaken the structure, leading to failure. It’s essential to wait at least 4 to 6 hours before starting any sanding or finishing work.
Can J-B Weld Withstand High Temperatures?
Yes, J-B Weld can withstand high temperatures. Once fully cured, it tolerates temperatures up to 260°C (500°F). This makes it a great choice for engine repairs and other high-heat applications, ensuring it won’t easily break down under pressure.
Conclusion
We’ve reached the end, and I appreciate you sticking around. We covered what JB Weld is, the different types available, prerequisites for use, application steps, and necessary precautions. We also discussed drying times, factors affecting those times, unique issues, aftercare tips, advantages, real-world uses, and even alternatives.
Now that you have a comprehensive understanding of JB Weld, you can confidently approach your projects with the knowledge of how to utilize this versatile adhesive. Whether you’re a DIY enthusiast or a professional contractor, JB Weld can provide the strength and reliability needed for your repairs and creations. Take the time to experiment and discover uses and benefits that can enhance your work and save you time and money in the long run.
I trust these insights have been helpful. So, how long does JB Weld take to dry? It typically sets in about 4 to 6 hours but can fully cure in 15 to 24 hours. Keep in mind, drying times can vary based on temperature, humidity, and the specific product used, so always check the instructions for the best results.
For further exploration of welding and related topics, visit us at What is Welding, where we are dedicated to delivering the latest technical expertise.
References
- American Welding Society. (2020). AWS Welding Handbook: Welding Science and Technology (Vol. 1). Miami, FL: AWS.
Mark is a skilled welding engineer specializing in advanced metal joining technologies and process design. With a formal education in welding engineering and a background rooted in practical experience, Mark bridges the gap between theory and application. He is passionate about making technical concepts accessible, empowering welders to embrace innovation while mastering essential skills. Mark combines his scientific expertise with a commitment to supporting the welding community alongside his uncle, Joe.
American Welding Society, Applications, Auto Body, Curing Process, DIY, Drying Time, Epoxy Adhesive, Jb Weld, Repair Solutions, Safety Tips, Welding