What is Robotic Welding? Explore Advantages, Types, and Applications
Published on: April 25, 2025 | Last modified: March 4, 2025
By: Joe Carter
Robotic welding uses automated machines to join metal parts together. These robots improve efficiency and precision in welding tasks.
A frequent question I encounter is, what is robotic welding? It’s crucial because understanding it helps you see its benefits. From my experience, we’ve seen reduced errors, saving time and costs in production lines.
In this guide, I’ll cover how robotic welding works, types of robotic welding, steps for successful welding, factors that affect the process, common issues you might encounter, aftercare and inspection tips, industry applications, and alternatives to robotic welding. Expect insights on what are the advantages of robotic welding and how to program a robotic welder as we dive in.
Contents
- What is Robotic Welding?
- How Does Robotic Welding Work?
- Types Of Robotic Welding
- Key Components of Robotic Welding Systems
- Factors Affecting Robotic Welding
- Steps for Robotic Welding
- Common Issues You Might Encounter
- Industry Applications for Robotic Welding
- What Are the Alternatives to Robotic Welding?
- Frequently Asked Questions (FAQs)
- Conclusion
- References
What is Robotic Welding?
Robotic welding uses automated machines to fuse metal pieces together. These robots provide fast, precise, and consistent welding, making them popular in automotive and manufacturing industries. They reduce labor costs and improve safety, enhancing production efficiency.
How Does Robotic Welding Work?
automated machines to join metal parts refer to using automated machines to join metal parts through processes like MIG (Metal Inert Gas) or TIG (Tungsten Inert Gas) welding. These robots operate with high precision, often achieving an accuracy of ±0.1 mm. They weld quickly, usually completing parts in a fraction of the time it takes a human welder. A robotic welder can work in environments where temperatures exceed 1,300 °C (2,372 °F), ensuring strong, consistent welds.
In robotic welding, engineers program the robots using specialized software, allowing them to follow intricate paths. This expertise helps determine optimal welding parameters, like speed and heat levels. The robots often include sensors to adjust their operations based on real-time feedback, enhancing the overall weld quality.
If I were you, I’d explore beginner-friendly resources on programming a robotic welder. Diving into platforms like YouTube can provide quick tutorials. Believe me, once you grasp the basics, you’ll appreciate how much robotic welding can boost efficiency in production.
Types Of Robotic Welding
What are the types of robotic welding?
-
Arc Welding
Arc welding uses an electric arc to melt metal. This robotic process automates the joining of two metal pieces by creating intense heat through a circuit. The robot precisely controls the arc length and angle to ensure a consistent weld, typically using steel at around 250°C (482°F). Understanding the various welding processes can provide deeper insights into how these techniques are applied in different manufacturing scenarios.
Welders should also be aware of what is weld flash to ensure safety during the process.
-
MIG Welding
MIG (Metal Inert Gas) welding applies a continuous wire feed to join metal pieces. A robotic welder uses a continuously fed wire electrode and a shielding gas to create a strong bond. The robotic arm moves steadily along the joint, controlling speed and wire feed for clear, even welds. Choosing the appropriate power source is essential for efficient welding operations, which involves determining what size generator to run for your equipment.
-
TIG Welding
TIG (Tungsten Inert Gas) welding relies on a non-consumable tungsten electrode to create the weld. This method requires precise control of heat and filler material for uniform results. The robot coordinates the movement of the tungsten rod while feeding a filler rod for smooth seams. It is essential to master techniques for welding thin materials as understanding how to weld sheet metal ensures precision.
-
Spot Welding
Spot welding joins metal pieces using electrical resistance. It generates heat by passing current through the metals at specific spots. The robotic system uses electrodes that clamp onto the metals, applying pressure and electricity in sequence to form weld spots.
-
Laser Welding
Laser welding employs focused laser beams to melt and join materials. This highly accurate method minimizes heat-affected zones around the weld. The robot targets the joint with a laser, precisely controlling power and speed for fine detail without warping the surrounding materials.
We’ve wrapped up the different types of robotic welding. Next up, we’ll look at the key components of robotic welding systems.
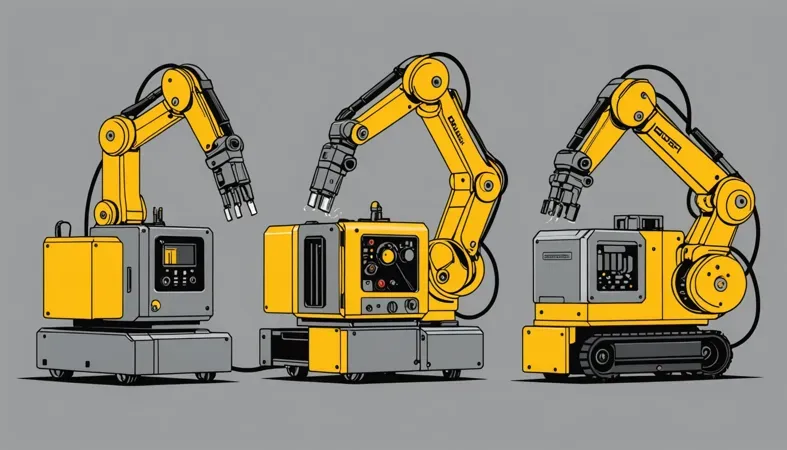
Key Components of Robotic Welding Systems
Understanding the key components that make up robotic welding systems is essential for grasping their operation.
Component | Description | Functions |
---|---|---|
Robot Arm | The mechanical arm that performs the welding task. | Moves along programmed paths; holds the welding torch or tool. |
Welding Torch | Device that delivers heat to melt and join metal pieces. | Controls heat input; can be equipped for different welding techniques like MIG or TIG. |
Controller | The brain of the welding robot. | Processes inputs from programming; sends signals to control movements and welding parameters. |
Sensors | Devices that provide feedback during the welding process. | Monitor parameters like temperature, position, and weld quality for adjustments. |
Power Supply | Provides the necessary energy for the welding processes. | Generates the correct voltage and current for different welding techniques. |
We’ve wrapped up the key elements of robotic welding systems here. Next up, we’ll look at factors influencing robotic welding.
Factors Affecting Robotic Welding
What factors influence the effectiveness of robotic welding? Here’s a quick overview.
-
Welding Material Properties
The type and properties of materials like steel or aluminum significantly impact robotic welding. For instance, the melting point of steel is around 1,538°C (2,800°F), while aluminum melts at about 660°C (1,220°F). Welding robots adjust parameters based on these properties for optimal results.
-
Robot Speed and Movement
Robotic welding speed can range from 200 to 1,000 mm/s. Faster movements reduce the heat-affected zone, minimizing warping. However, excessive speed can lead to poor weld penetration; finding the right balance is crucial.
-
Welding Technique Used
Consider the welding technique—MIG, TIG, or spot welding—each has its nuances. MIG welding is typically faster and easier to program than TIG but may sacrifice some precision. Different techniques require different robot settings, so choose wisely.
-
Environmental Conditions
Environmental factors such as temperature and humidity can affect welding outcomes. Ideally, welding should occur in conditions with a temperature around 21°C (70°F) and humidity below 50%. Extreme fluctuations can create weld defects.
-
Quality Control Protocols
Robust quality control ensures consistency in welds. Effective metrics include monitoring weld bead size and penetration depth, which should be between 0.5 mm and 3 mm, ensuring each weld meets standards. Regular inspections using sensors or visual checks help maintain high quality.
That covers the elements influencing robotic welding. Let’s now take a look at the procedures involved in robotic welding.
Steps for Robotic Welding
Now, let’s cover the steps to implement robotic welding effectively. Follow each step closely for the best results!
-
Select Appropriate Equipment
Choose the right robotic welder for your project. Assess factors like payload capacity (The Weight the Robot Can Handle) and welding method. For example, MIG (Metal Inert Gas) robots typically allow for higher travel speeds and efficiency. Don’t compromise; selecting the wrong equipment can lead to inefficiency or system overload.
Understanding how to select the most effective and cost-efficient MIG welder can significantly enhance your project’s success. For those working with budget constraints, finding the best cheap MIG welder is crucial to maintain both quality and performance.
Ensure compatibility with your welding application. For instance, if you’re joining steel, look for robots designed for high-heat scenarios. Some models can’t manage heat properly, resulting in inadequate welds. Do your homework and match specific features to your task. Understanding specialized welding processes will also help you make the right choice for your project.
Understanding the techniques necessary can be crucial when you’re learning how to weld in a vertical position.
-
Program the Robot
Program the welding robot with precise movement instructions and welding parameters. Use CAD (Computer-aided Design) software to create a welding path for the robot. Optimize each coordinated movement; errors can cause uneven welds. You want smooth operation with minimal rework!
Customize settings like travel speed, arc length, and voltage based on material thickness. For example, thinner materials may require lower voltage and faster travel speeds. Fine-tuning these parameters ensures high-quality welds and can significantly reduce production time.
-
Prepare the Workpieces
Clean and align the workpieces for an accurate weld. Remove dirt, oil, or rust that can compromise weld integrity. Properly positioned parts make a significant difference! I’d double-check that alignment, as improper positioning may require time-consuming adjustments mid-process.
Secure the pieces using clamps or fixtures to prevent movement during welding. Consistent, stable positioning promotes even heat distribution. Aim for uniform spacing between edges to avoid weld defects, which can weaken the final product. Proper safety measures are crucial when welding to avoid risks associated with improper protection, including understanding welding without a mask.
-
Monitor the Welding Process
Constantly track the welding process to identify any issues early. Use sensors to monitor parameters like temperature and travel speed in real-time. This data helps maintain consistent quality, so don’t overlook anomalies! Active monitoring can enhance efficiency and reduce errors.
If your robot supports it, use feedback systems to adjust parameters on the fly. This keeps the weld consistent despite material variations. Some robots even synchronize movement with current flow, optimizing performance dynamically. You don’t want to risk creating a product full of defects!
We’ve wrapped up the steps involved in robotic welding. Next up, we’ll look at common issues you might encounter.
Common Issues You Might Encounter
Let’s look at unique challenges in robotic welding.
-
Equipment Malfunctions
Robotic welding systems can experience servo motor failures. Identify this by unusual noises or inability to move. Check cables and joints. If it’s mostly misaligned, recalibrate and replace faulty parts.
-
Inconsistent Weld Quality
Robotic welding may produce uneven welds due to poor programming. Regularly review parameters and settings. Use calipers to measure seam widths. Adjust as needed, keeping your settings well-documented.
-
Programming Errors
Robotic welding can suffer from misprogrammed paths. Check for issues by looking for misalignments in weld beads. Review software logs to identify faults and reprogram sections as needed.
-
Material Compatibility Issues
Robotic welding faces challenges with incompatible materials. Use metal conductivity tests to assess compatibility. If mismatched, switch to suitable welding wires or modify the welding technique.
-
Safety Hazards
In robotic welding, safety risks may arise from exposed components. Look for loose wiring or debris near the robot’s path. Always reduce risks with proper shielding and regular equipment checks.
Industry Applications for Robotic Welding
I’ve seen robotic welding transform industries with applications like:
- Automotive Manufacturing: Used for welding car frames and components, it boosts efficiency and precision, leading to fewer defects. It’s popular in assembly lines.
- Aerospace Construction: Applied in welding aircraft structures, it ensures high strength-to-weight ratios. Its popularity stems from strict quality and safety standards.
- Shipbuilding: Utilized for large metal structures, robotic welders handle heavy tasks, reduce labor, and ensure durability, common in naval dockyards.
- Heavy Equipment Fabrication: Used in assembling industrial machinery, it maintains consistency in welds and minimizes waste. It’s a staple in construction equipment factories.
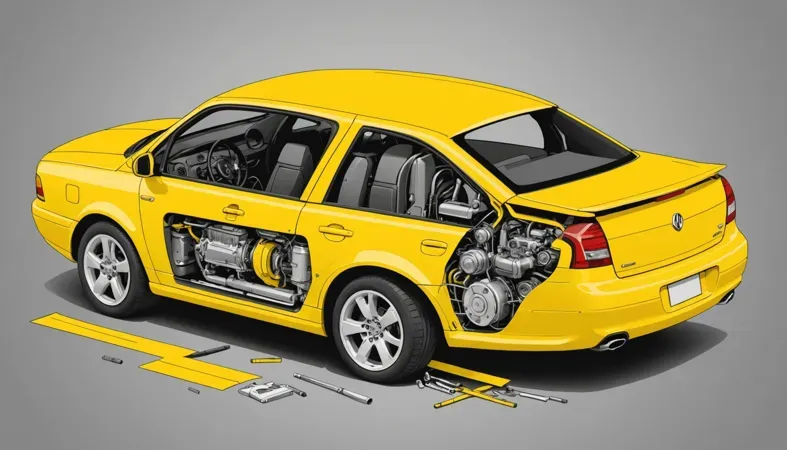
What Are the Alternatives to Robotic Welding?
There are several alternatives to robotic welding that can achieve similar results. Manual welding methods, like MIG (Metal Inert Gas) or TIG (Tungsten Inert Gas) welding, are often preferred for custom and intricate projects. Through years of practice, I’ve come to understand that these methods offer more flexibility and control, especially for unique designs or small production runs. When considering manual welding, understanding the correct wire size for a welder is crucial for optimal performance.
Additionally, friction stir welding and laser welding are notable options. Products like the Friction Stir Welding machines from ESAB can provide robust, high-quality joints. Each alternative comes with its own set of pros and cons, so choose based on your project’s specific needs.
Frequently Asked Questions (FAQs)
Now let’s look at some questions I typically get asked about robotic welding.
What Are the Advantages Of Robotic Welding?
Yes, the advantages of robotic welding include high precision, speed, and repeatability. Robotic welders work with an accuracy of ±0.1 mm in positioning, reducing human error. This leads to better weld quality and lower production costs since robots can operate continuously, maximizing efficiency.
How Accurate is Robotic Welding?
Robotic welding is very accurate, achieving tolerances of ±0.1 mm (±0.004 In). This precision is crucial in industries like automotive, where parts must fit perfectly. The use of sophisticated sensors allows robots to adjust dynamically to ensure the welds meet rigorous specifications.
How Much is a Welding Robot?
The cost of a welding robot can range from $40,000 to $150,000. Factors influencing this price include brand, capabilities, and features. Investing in a robotic welder can yield high returns through increased productivity and reduced labor costs over time.
What Sensors Are Used in Robotic Welding?
Robotic welding utilizes various sensors, including vision systems, proximity sensors, and temperature sensors. Vision systems help in aligning workpieces accurately, while temperature sensors monitor weld heat. These technologies enhance quality control and improve overall weld performance.
How to Program a Robotic Welder?
To program a robotic welder, you typically use computer software to create welding paths. Most robots offer offline programming, allowing you to set parameters without interrupting production. Familiarity with the specific robot’s programming language is essential for efficient operation.
What is Cobot Welding?
Cobot welding refers to collaborative robot welding that works alongside human welders. These robots are designed for safety and assistance, improving overall workflow. Cobots are often easier to program and can handle repetitive tasks, allowing humans to focus on more complex operations.
Conclusion
Phew, that’s a lot to unpack. We covered what robotic welding is, how it works, the different types, the steps to set it up, factors affecting its performance, common issues, aftercare, inspection tips, and various industry applications. We also touched on alternatives and answered some FAQs.
Hopefully, I was able to impart some of my experience about robotic welding. In simple terms, it’s a process where robots perform welding tasks with high precision and repeatability. So, when you ask what is robotic welding, think of it as a way to boost efficiency and consistency in manufacturing with a cost-efficient and accurate approach.
To further enhance your understanding of welding techniques and practices, feel free to explore more resources at What is Welding.
References
- Lincoln Electric. (2020). The Procedure Handbook of Arc Welding (15th ed.). Cleveland, OH: Lincoln Electric Company.
- American Welding Society. (2015). AWS D1.1/D1.1M: Structural Welding Code – Steel. Miami, FL: AWS.
Joe Carter is a retired welding professional with over 40 years of hands-on experience in the industry, spanning ship repair, structural welding, and even underwater projects. Joe is a master of MIG, TIG, and Stick welding. Passionate about mentoring the next generation of welders, Joe now shares his decades of expertise and practical insights to help others build rewarding careers in welding.
American Welding Society, Automation, Industrial Applications, Manufacturing Efficiency, MIG Welding, Robotic Welding, Welding, Welding Techniques, Welding Technology, Welding Wire