Can You MIG Weld Stainless Steel? Tips, Tricks, and Techniques
Published on: November 26, 2024 | Last modified: March 4, 2025
By: Joe Carter
A common inquiry I receive is can you mig weld stainless steel? Understanding this is important because stainless steel has unique properties. In my experience, it requires specific techniques to ensure a strong, clean weld.
In this guide, we’ll explore MIG welding stainless steel, covering types of stainless steel and their weldability, prerequisites for a successful weld, detailed steps for MIG welding, safety tips, various MIG welding types, factors affecting the weld quality, common issues that may arise, aftercare procedures, and the advantages of using this method. We’re diving deep into whether you can weld stainless steel with a MIG welder!
Contents
- Can You Mig Weld Stainless Steel?
- What is Stainless Steel?
- Types Of Stainless Steel and Their Weldability
- Prerequisites: Things You Should Prepare in Advance
- Safety Tips
- Steps for Successfully MIG Welding Stainless Steel
- Types Of MIG Welding for Stainless Steel
- Factors Affecting MIG Welding Of Stainless Steel
- What Could Go Wrong: Common Issues
- Aftercare & Inspection for MIG Welding Stainless Steel
- Advanced Techniques for MIG Welding Stainless Steel
- Advantages Of MIG Welding Stainless Steel
- Where is Stainless Steel Used?
- Alternatives That Might Work Better
- Frequently Asked Questions (FAQs)
- Conclusion
- References
Can You Mig Weld Stainless Steel?
Yes, you can mig weld stainless steel. It’s a bit trickier due to stainless steel’s heat sensitivity, which can warp or burn through. Use a suitable filler and keep your settings low and steady for best results.
What is Stainless Steel?
Stainless steel is a corrosion-resistant alloy made primarily of iron, carbon, and at least 10.5% chromium. This composition gives it remarkable strength and resistance to rust. The addition of nickel, molybdenum, or other elements can enhance its properties further. Stainless steel can withstand temperatures from -268 °C to about 650 °C (-450 °F to 1,202 °F), making it versatile for many applications.
Now, let’s discuss welding stainless steel. Many ask, “Can I MIG weld stainless steel?” From personal experience, I can tell you it’s definitely possible. With the right settings and shielding gas, you can achieve strong, clean welds that hold up well over time.
A friend of mine used stainless steel to fabricate custom exhaust systems. He found that precise MIG welding settings are crucial for success. He often wondered, “Can you weld stainless steel with a MIG welder?” After much experimentation, he discovered that the ideal blend of wire and gas made all the difference in creating durable, professional-quality welds.
Types Of Stainless Steel and Their Weldability
What are the types of stainless steel for welding?
-
Austenitic Stainless Steels
Austenitic stainless steels are the most common type, known for their high corrosion resistance due to their high nickel content. You can easily weld this type using a MIG welder. Use Stainless Steel MIG wire with a tri-mix of inert gases, like argon and CO2, for the best results. To achieve optimal welding performance you must consider the necessary amperage settings.
-
Ferritic Stainless Steels
Ferritic stainless steels have a high chromium content that provides good rust resistance. You can weld them with a MIG welder, but using a flux-cored wire is preferable. For good results, maintain a clean surface and keep your speed steady while welding.
-
Martensitic Stainless Steels
Martensitic stainless steels are tougher but less resistant to corrosion than others. While you can weld this type with MIG, expect more warping and cracking. To minimize these issues, preheat the steel before welding and be cautious with your settings.
-
Duplex Stainless Steels
Duplex stainless steels combine properties of both austenitic and ferritic types, offering high strength and resistance. You can weld it with a MIG welder. To weld efficiently, use low heat input to avoid compromising its unique structure.
-
Precipitation Hardening Stainless Steels
Precipitation hardening grades are known for their strength and toughness. Yes, they can be MIG welded. To ensure the best joint quality, maintain precise heat control and follow up with proper post-weld treatments.
That covers the various types of stainless steel and their weldability. Let’s now take a look at necessary preparations to undertake.
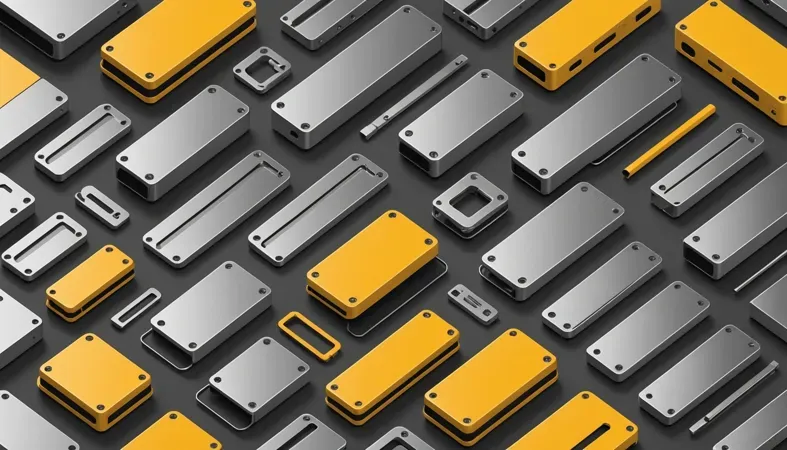
Prerequisites: Things You Should Prepare in Advance
What do you need to get started?
- Stainless Steel MIG Wire: You’ll need .030” (0.8 Mm) ER308L wire for proper fusion and defect prevention.
- MIG Welder: A Miller Multimatic 215 is a good choice. It has settings for stainless steel.
- Argon Shielding Gas: A 75% Argon and 25% CO2 (75/25) mix is best for reducing oxidation.
- Weld Cleaning Brush: Get a stainless steel brush like the E.Z. Brush to prep the weld area by removing contaminants.
That covers the essentials you need to prepare beforehand. Let’s now take a look at important safety precautions to follow.
Safety Tips
Let’s review safety tips for MIG welding stainless steel.
- Protective Gear: Always wear an approved welding helmet and gloves, such as Lincoln Electric’s gear. They protect you from harmful UV rays and sparks.
- Ventilation: Ensure your workspace is well-ventilated. Use exhaust fans like the Tornado 2 to remove fumes and prevent breathing hazards.
- Flammable Materials: Clear away flammable materials at least 10 feet (3.05 M) away. This reduces fire risk in your working area.
- Electrical Safety: Regularly check your equipment for frayed cords. Using synthetic-based FireFlex extension cords reduces short-circuiting hazards.
Staying safe while welding preserves your health and is vital for project success.
That covers safety precautions for MIG welding. Let’s now take a look at the steps for successfully welding stainless steel.
Steps for Successfully MIG Welding Stainless Steel
Here are the steps to follow for MIG welding stainless steel, step by step!
-
Set Up Your Workspace
Clear a flat, clean area for welding. Make sure it’s well-ventilated; you’ll want fresh air. A workbench at waist height (60 to 90 Cm) is ideal for maintaining control. Ensure no flammable materials are nearby; safety first!Organize your tools within reach. Prepare your MIG welder, hoses, and grinders. Have a fire extinguisher ready, just in case. Time spent setting up now will save you loads of trouble later!
-
Choose the Right Filler Wire
Select the appropriate gas-shielded wire for stainless steel. A good choice is ER308L, which works well for 304 stainless. The wire diameter should be 0.035 inches (0.9 Mm) for most projects. A larger diameter is better for thicker materials.
Consider the shielding gas, too. Argon-based gas is preferred; a mixture of 75% Argon and 25% CO₂ works well, with a flow rate of 15 to 20 cubic feet per hour. Test different gas mixtures for the best results on tricky joints.
-
Adjust MIG Welding Settings
Set your MIG welder to the correct voltage and wire speed. For MIG welding stainless steel, adjust the voltage between 20-25 volts, depending on thickness. Thinner sheets (0.025 Inches or 0.63 Mm) may require lower voltage, while thicker sections (Up to 0.120 Inches or 3 Mm) can handle higher voltage to avoid burn-through. Wire speed is also crucial—set it between 250-350 inches per minute (635-890 Cm/min). Adjusting these settings often requires testing and tweaking on scrap pieces first to achieve the perfect bead. Setting too fast may lead to weak welds; too slow may warp the material.
In some cases, welders may seek to modify their equipment; for example, converting a 220 welder to 110 for more versatility.
-
Perform a Test Weld
Before starting your main project, always weld a test piece first. This lets you gauge your settings and technique without risking the main job. Use similar scrap metal to check for penetration and cleanliness of the bead—this will help immensely! After welding, inspect your test weld. Aim for a smooth surface and consistent bead profile. If you notice undercuts or excessive spatter, reassess your settings. Each welder has a different technique; mastering yours will make a big difference. You can explore innovative methods by learning how to make an arc welder with a microwave transformer.
We covered the steps for successfully MIG welding stainless steel. Next, we will explore the various types of MIG welding for stainless steel.
Types Of MIG Welding for Stainless Steel
Let’s move on to the types. We’ll cover Gas Metal Arc Welding, Gas Tungsten Arc Welding, Pulsed MIG Welding, Short Circuit MIG Welding, and Spray Transfer MIG Welding.
-
Gas Metal Arc Welding
Gas Metal Arc Welding (GMAW) is the most common MIG welding method. It uses a continuous wire feed to create the weld, shielding the metal with an inert gas like argon. This method allows effective MIG welding of stainless steel, offering high deposition rates of about 4-24 pounds per hour (1.8-10.9 Kg/hr). Understanding the various welding processes used can further enhance one’s skills in this technique.
When starting out, selecting the best welder for a beginner can greatly enhance the learning experience and ensure optimal results, offering guidance in choosing a good welder.
-
Gas Tungsten Arc Welding
Gas Tungsten Arc Welding (GTAW), often called TIG welding, uses a non-consumable tungsten electrode to produce the weld, making it suitable for thin materials. You can weld stainless steel with GTAW, but it’s usually slower than MIG.
-
Pulsed MIG Welding
Pulsed MIG welding alternates between low and high current settings. This method enhances penetration and improves heat control. It’s effective for welding thicker stainless steel and allows speeds up to 25 inches per minute (63.5 Cm/min).
-
Short Circuit MIG Welding
Short Circuit MIG welding is a low-heat process excellent for thin stainless steel. In this method, the wire contacts the workpiece, creating a short circuit. You can MIG weld stainless steel with minimal distortion, as it uses lower heat input compared to other methods.
Choosing the appropriate breaker size is crucial for safely operating welding equipment. Understanding the correct breaker for welders can help prevent electrical issues.
-
Spray Transfer MIG Welding
Spray Transfer MIG is ideal for thick materials. In this process, molten metal droplets are atomized into a spray, creating a strong weld with a smooth appearance. While it requires higher currents, you can achieve transfer rates of 10-14 pounds per hour (4.5-6.4 Kg/hr) when MIG welding stainless steel.
Factors Affecting MIG Welding Of Stainless Steel
What factors influence your ability to weld stainless steel successfully?
-
Material Thickness
Thicker stainless steel requires more heat. For example, 3 mm (0.12 In) needs increased amperage, around 130-170 A, to create a strong bond.
-
Welding Position
Welding flat is easier than vertical or overhead. If you’re in the wrong position, you may struggle with penetration and control.
-
Heat Input
Aim for a heat input of 1.0-1.5 kJ/mm. Too much heat can cause distortion, while too little can lead to weak welds.
-
Electrical Settings
Use the right voltage and wire speed settings. For instance, 20-24 V with a wire feed speed of 300-600 IPM (Inches Per Minute) works well for various stainless steel types.
-
Gas Composition
A mixture of argon and CO2 is often used. A common blend is 75% argon and 25% CO2, which stabilizes the arc and improves bead appearance.
What Could Go Wrong: Common Issues
Now, let’s look at specific issues that arise with stainless steel.
-
Burn-through
Stainless steel can suffer burn-through from excessive heat. Check for holes or molten metal to identify this issue. To resolve it, adjust settings to lower the amperage (argon GTAW Recommended, Starting at ≤ 10 A/mm).
-
Poor Penetration
Poor penetration in stainless steel occurs due to fast travel speeds. Slow down and increase the heat input. Check your settings for affected thin plates (2-3 Mm Thickness) to ensure proper fusion.
-
Cracking
Cracking often results from rapid cooling in stainless steel. Look for hairline cracks after welding. To fix this, preheat the area being welded and control cooling rates to prevent thermal shock.
-
Inconsistent Weld Bead
Stainless steel may exhibit an inconsistent bead due to incorrect travel speed or wire feed. Inspect the width’s uniformity when finished. Resolve this by adjusting your rod and maintaining a steady hand.
-
Heat-affected Zone Damage
Heat-affected zones can weaken the surrounding material in stainless steel. Check for color changes or loss of luster. Control heat flow and consider interpass cooling to address this issue.
Aftercare & Inspection for MIG Welding Stainless Steel
Here are essential aftercare, inspection, and advanced tips for welding stainless steel.
Aftercare Tips
After you weld stainless steel with MIG, clean the joint immediately with a wire brush. Use a mixture of warm water and dish soap to remove residue. Finally, apply a corrosion inhibitor like WD-40 (0.18 Kg) to prevent rust on the freshly cut edges.
Inspection
Inspect the weld beads with a calibrated gauge. Check for undercuts greater than 0.5 mm and gaps larger than 0.3 mm. Use a digital caliper, such as the Infraredia model, to measure imperfections accurately.
Advanced Techniques for MIG Welding Stainless Steel
Once you’ve mastered the basics of MIG welding stainless steel, it’s time to explore advanced techniques to improve your results.
Welding Positioning
- Flat Position: Easiest for beginners. Offers better control and visibility, resulting in a more consistent bead.
- Vertical Position: More challenging, but crucial for many applications. Keep your heat low to prevent sagging.
- Overhead Position: Toughest but necessary for certain projects. Use short welds and allow cooling time to minimize pool collapse.
Multi-Pass Welding Techniques
For thicker sections, using a multi-pass technique can enhance strength and integrity. Aim for:
- First Pass: Use a stringer bead for deeper penetration.
- Second Pass: A weaving pattern fills gaps and spreads heat for even coverage.
- Final Pass: A tighter weave improves the aesthetics and minimizes slag inclusion.
Control Cooling Rates
Slow cooling rates reduce the chances of cracking. Here’s how:
Method | Description | Cooling Rate Reduction |
---|---|---|
Heat Sinks | Place copper or aluminum blocks next to welds to absorb heat. | Lower by up to 50% |
Blanketing | Cover welds with ceramic blankets to trap heat. | Lower by 30% |
Post-Heat Treatment | Apply localized heat after welding. | Variable based on material |
Utilize Welding Oscillation
Oscillating the gun while welding spreads heat and enhances bead uniformity. Try these patterns:
- Fore-Aft Motion: Back and forth along the weld line.
- Circular Motion: Small circles to widen the heat zone.
By applying these advanced techniques, you can elevate your MIG welding skills and ensure superior results with stainless steel.
Advantages Of MIG Welding Stainless Steel
The biggest advantage of MIG welding stainless steel is speed. A friend used it to build a custom exhaust system, finishing in half the time compared to stick welding.
Additionally, MIG welding offers cleaner welds, less spatter, easier heat control, and versatility for various stainless steel grades. You can also work on thin materials without burning through.
Where is Stainless Steel Used?
I’ve known people to use stainless steel in construction and culinary tools, but it has many applications, such as:
- Food Processing Equipment: Used for mixers and conveyors. It’s popular for its corrosion resistance, making it safe for food contact.
- Biomedical Devices: Used in surgical instruments. Stainless steel is preferred for its biocompatibility and ease of sterilization.
- Marine Applications: Found in boat fittings and hardware. Its durability against saltwater corrosion makes it a go-to material.
- Pipes and Tubing: Used in the chemical and oil industries for strength and corrosion resistance, which is crucial in heavy-duty environments.

Alternatives That Might Work Better
When you’re looking for options, consider TIG welding if you want precise control. It’s often preferred for thin stainless steel where aesthetics matter, as it produces cleaner welds. Products such as Lincoln Electric’s TIG Welding Kit deliver excellent results for those detailed jobs.
Another alternative is using Stick welding, especially with electrodes like E308L. It’s a solid choice for thicker stainless steel sections, offering robust joints. From my unique perspective, each method brings unique benefits, so choose based on your specific project needs and materials.
Frequently Asked Questions (FAQs)
Here are some questions I typically get asked about stainless steel welding.
Is It Hard to MIG Weld Stainless Steel?
Yes, it can be challenging to MIG weld stainless steel. This challenge arises due to its higher thermal conductivity and lower melting point, which can lead to warping. Precise control is essential; otherwise, you might face burn-throughs or weak joints. Arc control plays a critical role in ensuring stable MIG welding processes, especially when dealing with different materials and thicknesses. To understand more about arc control on a MIG welder, explore its impact on your welding results.
Can I Weld Stainless Steel With Regular MIG Wire?
No, you can’t weld stainless steel with regular MIG wire. Regular MIG wire lacks the proper alloy composition needed for stainless steel, leading to poor weld quality and corrosion resistance. You should use a specific stainless steel MIG wire, typically ER308L for most applications.
Is MIG or TIG Better for Stainless Steel?
MIG and TIG welding both have their advantages, but TIG is generally better for stainless steel. TIG welding offers greater control over heat input and a cleaner, more precise weld. However, MIG is faster and easier, so your choice depends on your project needs. For an efficient application of welding techniques, it is essential to understand how to use a welder.
What Wire to Use When MIG Welding Stainless Steel?
When MIG welding stainless steel, you should use ER308L wire. This wire is commonly used for austenitic stainless steels. It provides excellent corrosion resistance and can withstand high temperatures—ideal for various applications.
Can I Weld Stainless Steel With a Stick Welder?
Yes, you can weld stainless steel with a stick welder. This process usually requires specific electrodes, like E308 or E316. While stick welding is not as common for stainless, it’s effective for certain conditions, especially outdoors where wind is less of a concern.
Conclusion
We’ve reached the end, and I appreciate you sticking around. We covered the essentials like what stainless steel is, types of stainless steel, and their weldability. We also discussed steps for MIG welding stainless steel, safety tips, and factors affecting the welding process, plus what could go wrong and how to care for your welds afterward.
So, can you MIG weld stainless steel? Yes, you sure can. With the right setup, using a MIG welder can give you strong, clean welds. Wishing you success in your welding projects as you tackle stainless steel with confidence!
If you’re eager to dive deeper into the world of welding, check out What is Welding for more comprehensive information.
References
- American Welding Society. (2015). AWS D1.1/D1.1M: Structural Welding Code – Steel. Miami, FL: AWS.
- Occupational Safety and Health Administration (OSHA): Welding, Cutting, and Brazing: https://www.osha.gov/welding-cutting-brazing
- American Welding Society (AWS): https://www.aws.org
Joe Carter is a retired welding professional with over 40 years of hands-on experience in the industry, spanning ship repair, structural welding, and even underwater projects. Joe is a master of MIG, TIG, and Stick welding. Passionate about mentoring the next generation of welders, Joe now shares his decades of expertise and practical insights to help others build rewarding careers in welding.
American Welding Society, Electrical Safety, Metal Fabrication, MIG Welding, Stainless Steel, Welding, Welding Equipment, Welding Safety, Welding Techniques, Welding Tips