What is a Combo Welder? Discover Its Function, Types, and Setup
Published on: December 21, 2024 | Last modified: March 4, 2025
By: Joe Carter
A combo welder is a tool that combines multiple welding processes into one machine. It’s super handy for both beginners and pros.
It’s a question I’ve heard often: what is a combo welder? Understanding it is crucial if you’re diving into welding. From my experience, knowing how welding machines work can save you time and money, ensure safety, and expand what you can create.
In this article, we’ll explore how a combo welder works, types of combo welders, setup steps, performance factors, common issues and solutions, maintenance tips, and applications. We’ll also look into alternatives and FAQs to give you a detailed view of this versatile tool. You’ll find out what makes a good welder and where can I buy a Miller welder!
Contents
- What is a Combo Welder?
- How Does a Combo Welder Work?
- Types Of Combo Welders
- Steps to Set Up a Combo Welder
- Understanding Combo Welder Specifications
- Factors Influencing Combo Welder Performance
- How to Address Common Problems
- Aftercare, Inspection, and Advanced Tips for Combo Welders
- Applications Of Combo Welders
- Are There Any Alternatives to Using A Combo Welder?
- Frequently Asked Questions (FAQs)
- Conclusion
- References
What is a Combo Welder?
A combo welder is a versatile tool that combines MIG, TIG, and stick welding. It’s popular for metal fabrication, repair, and art projects. You can use it for various metals like steel and aluminum, making it super handy.
How Does a Combo Welder Work?
A combo welder (Combination Welder) is a versatile tool that combines welding processes like MIG (Metal Inert Gas) and TIG (Tungsten Inert Gas) in one machine. It lets you tackle materials like steel and aluminum with ease. Many combo welders operate on 120V or 240V, offering flexibility for various projects. They’re popular in professional shops and home garages due to their efficiency and convenience. Combo welder: What Is It?
These welders suit different users. Depending on the model, they can handle weld thicknesses ranging from 0.6 mm to 10 mm (1/32 Inch to 3/8 Inch). A solid understanding of the technical aspects and welding techniques makes a significant difference in achieving high-quality welds.
Trust me, I’ve used a combo welder for years, and it’s a game changer. You get the best of both worlds with MIG and TIG welding. It’s one of the most versatile welders available—perfect for hobbyists and professionals alike!
Types Of Combo Welders
What are the different types of combo welders?
-
MIG Welders
MIG (Metal Inert Gas) welders are user-friendly and ideal for beginners. A combo welder using MIG simplifies welding various metals. You’ll need semi-automated wire feeders and argon shielding gas for cleaner welds. For effective reshaping and disassembly of metal structures, understanding how to cut welds is crucial.
-
TIG Welders
TIG (Tungsten Inert Gas) welders offer precise control for thin materials. A combo option works well with stainless steel and aluminum. To operate one, hold a tungsten electrode, fused by a non-reactive gas, while feeding filler material as needed. A crucial aspect of ensuring weld quality is understanding the role of a hot pass in welding.
-
Stick Welders
Stick welders use a consumable electrode to create welds, making them great for outdoor work. A combo welder enables you to handle various environments and surfaces. To use it, strike an arc between the stick and metal for a strong bond. Exploring whether you can safely observe welding activities from afar might be crucial for maintaining a safe working environment; find out more in this guide on viewing welding safely.
-
Multi-process Welders
Multi-process welders perform MIG, TIG, and Stick welding. A combo setup provides flexibility for different projects. To switch processes, adjust the settings, choose the right electrode or wire, and use the appropriate shielding gas. Divers engaging in underwater welding must consider unique hazards and challenges, which can be further explored in how dangerous is underwater welding.
-
Portable Welders
Portable welders are compact and easy to transport, perfect for jobs on the go. A combo welder lets you weld anywhere without heavy equipment. To operate, plug it into a power source, and you’re ready to fuse metals quickly.
However, welding without proper safety gear can be dangerous, leading to serious eye damage and other health risks, which you can learn more about in why welding masks are essential.
We covered the various types of combo welders here. Next, we will cover how to set up a combo welder.
Steps to Set Up a Combo Welder
Here are the steps for using a combination welder effectively. Follow these carefully for the best results!
-
Select the Right Settings
Start by choosing the appropriate settings on your combo welder. For MIG, use a voltage range of 18-25 V and a wire feed speed of 100-300 inches per minute (Ipm). For TIG, base the amperage on material thickness; 1 amp per 0.001 inch (0.025 Mm) is a good rule. Constantly adjusting your settings is crucial for a smooth weld. Welding galvanized steel can present significant safety hazards that welders must address, such as the risk of zinc fumes being toxic to your health, which you can learn more about in the dangers of welding galvanized steel.
Make sure you’re using the right gas mixture as well. For MIG welding, use a blend of 75% argon and 25% CO2. This mix enhances weld quality, especially on mild steel. Avoid guesswork; clear settings simplify the process.
-
Connect the Electrode and Ground Clamp
First, securely connect your electrode to the holder. Ensure the electrode extends about 1-2 inches (2.5-5 Cm) beyond the holder for proper arc length. Then, attach the ground clamp to a clean metal surface. A poor ground can lead to weak welds or machinery damage.
Always check the connections beforehand. A solid ground is vital for consistent welding quality. If you’re wavering between types of welders, remember that a combo welder excels here.
-
Choose Your Welding Technique
Pick between MIG or TIG based on your project needs. For thicker materials, MIG is often best. If precision is key, like in artistic projects, lean towards TIG. TIG creates cleaner welds on thin materials but requires practice.
Training can significantly refine your technique. Work on scrap metal before tackling a major task. The more versatile you are with settings, the better the outcomes.
-
Maintain Proper Speed and Angle
Keep the welder at a consistent speed—2-6 inches (5-15 Cm) per second is ideal for MIG. Adjust your angle to about 15 degrees from vertical for effective penetration. Going too slow creates excessive heat; going too fast leads to weak bonds. Precision is everything!
If adjustments are necessary you might also need to remove existing welds for perfect rework.
Watch your puddle closely. It should look shiny and fluid but not too wide or narrow. Adjusting your technique as you work can mean the difference between a clean bead and a mess.
-
Observe the Weld Quality
After completing your weld, carefully observe its appearance. A good weld should have even penetration and minimal spatter. If you spot issues, identify what went wrong—this helps you learn and improve. For example, inconsistent feeds can lead to a porous weld.
Don’t hesitate to fix mistakes immediately. Grinding or chiseling off a failed weld can salvage materials and provide valuable learning opportunities. Plus, your final product will thank you!
We have now covered the steps to set up a combo welder. Next, we will examine combo welder specifications.
Understanding Combo Welder Specifications
To maximize your welding experience, it’s essential to understand combo welder specifications.
Specification | Description | Units |
---|---|---|
Input Voltage | Common input ranges for residential use | 120V or 240V |
Weld Thickness Range | Materials thickness the welder can handle | 0.6 mm to 10 mm (1/32 to 3/8 inch) |
Wire Feed Speed | Typical speed ranges for wire feed | 100-300 in/min (254-762 cm/min) |
Amperage Range | Common range for various applications | 20A to 250A |
Duty Cycle | Percentage of time the welder can operate safely | Typically 30%-60% |
Weight | Portability considerations | 30 lbs to 50 lbs (13.6 kg to 22.7 kg) |
Knowing these specifications will help you choose the right combo welder for your needs. Want to make sure you’re getting the best performance? Always check these numbers before making a purchase.
Understanding how welding techniques affect project outcomes is crucial, including the importance of managing factors that contribute to weld spatter causes.
We have now covered combo welder specifications and key features. Next, we will examine the factors affecting combo welder performance.
Factors Influencing Combo Welder Performance
What factors impact a combo welder’s effectiveness and versatility in the field?
-
Material Thickness
Material thickness significantly affects weld penetration and strength. Thicker materials (Over 6 Mm or 1/4 Inch) often require more power and a specific technique.
-
Welding Technique
The technique you choose, such as stringer beads versus weave patterns, influences final strength. Each style produces different heat distribution, impacting appearance and durability.
-
Electrode Type
The electrode type can make or break your weld. For instance, using an E7018 rod for mild steel delivers great strength, while an E6013 electrode offers easier arc stability for thin materials. When it comes to sourcing materials for such projects, understanding where to buy metal for welding can streamline your work process efficiently.
-
Gas Quality
The quality of shielding gas, typically Argon or CO2, affects weld appearance. Contaminants can cause porosity, weakening weld strength by up to 40%.
-
Environmental Conditions
Wind, temperature, and humidity are critical. For example, welding outdoors on a windy day may require a wind shield to maintain weld quality.
So far we covered factors affecting combo welder efficiency. Next, let’s look at solutions for typical issues encountered.
How to Address Common Problems
Now, let’s look at unique issues related to the combo welder.
-
Inconsistent Arc Stability
The combo welder can exhibit arc instability. Test the arc quality to identify this issue. Use a short-circuit or spray transfer method for smoother operation. Adjust settings and check connections to resolve it.
-
Overheating Components
The combo welder’s components may overheat. You’ll notice heat on the wire feeder or welding unit. To fix this, check for dust buildup and ensure proper ventilation. Adjust your duty cycle if the usage is too high.
-
Inadequate Weld Penetration
The combo welder might struggle with penetration. This issue usually arises from incorrect voltage settings. Increase your voltage and decrease your travel speed to improve penetration.
-
Material Contamination
Contaminants like grease can affect weld quality. Clean materials with a wire brush or solvent to restore quality and strength.
-
Difficulty in Material Feeding
If you face feeding troubles, the combo welder’s tension might be faulty. Ensure the roller tensions are set correctly. Inspect for kinks in the wire and adjust the feeder’s settings.
Aftercare, Inspection, and Advanced Tips for Combo Welders
Here’s essential advice to keep your combo welder in top shape.
Aftercare Tips
After using your combo welder, clean the torch tip with brass wire brushes. Keep the electrode holder’s cable free from burns by using heat-resistant sleeves. Finally, adjust the gas flow rate to 12-15 liters per minute (LPM) to prevent loss of shielding gas.
Inspection Points
Inspect the ground clamp connection for corrosion; it should show zero resistance. Check the gas hoses for cracks or leaks using soapy water. Look for any foreign objects in the welding nozzle, like spatters that could impair performance. I rely on the Miller Matchless SOLO for clear visibility.
Expert Tips
If you’re experienced, focus on optimizing your combo welder’s settings. Set the dual-purpose voltage to 230V (And 115V for Home Tasks) for better patchwork results. Experiment with duty cycles; efficient running can achieve 60% at your preferred settings while reducing wear. Lastly, monitor copper stakes for even welding temperature.
Applications Of Combo Welders
I’ve seen people use combo welders for various projects, and they have many practical applications, such as:
- Metal Art Creation: Artists use combo welders to create intricate metal sculptures. The ability to switch between MIG and TIG processes allows for precision and versatility in crafting.
- Automotive Repairs: Auto mechanics rely on combo welders for welding parts like chassis or frames. This versatility speeds up repairs, especially in collision shops where time is critical.
- Pipe Fabrication: In HVAC (Heating, Ventilation, and Air Conditioning) and plumbing, professionals use combo welders to join pipes. Their ability to switch processes ensures strong, leak-free joints, enhancing customer satisfaction.
- Custom Furniture Making: Woodworkers use combo welders to create unique metal furniture pieces. This enhances design possibilities and improves craftsmanship quality in custom builds.
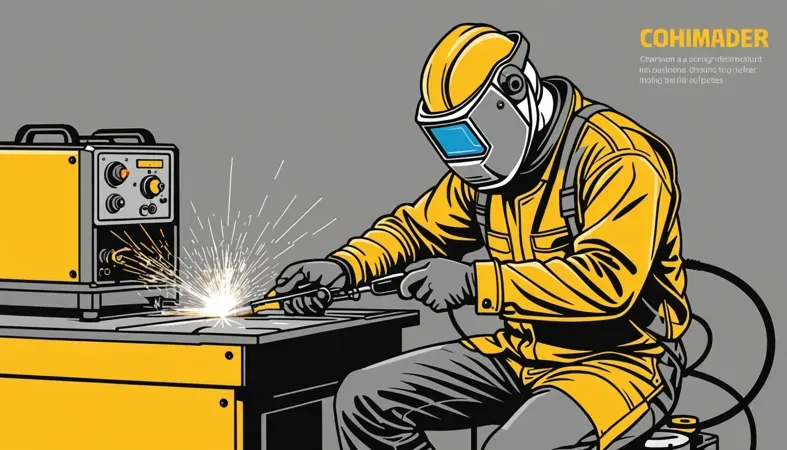
Are There Any Alternatives to Using A Combo Welder?
If you’re looking for alternatives, consider options like MIG welders, TIG welders, or stick welders. Each has its strengths. For example, a Miller Multimatic 215 is great for versatility and can handle various materials well. It’s always beneficial to assess the different types of welding equipment available before making a decision.
A welding mask is essential for safety in these processes, and interestingly, you might wonder if it’s possible to view an eclipse with a welding mask.
From what I’ve encountered personally, sometimes a dedicated unit suits your project better. If you’re mainly doing thin materials, a Lincoln Electric Pro MIG 180 might be your best bet. It gives you some fine control while being easy to handle.
Frequently Asked Questions (FAQs)
Now let us look at some questions I typically get asked.
What’s the Highest Paid Welding Job?
What’s the highest paid welding job? The highest paid welding job is often an underwater welder. These professionals can earn between $40,000 to $100,000 (USD) per year, depending on experience and location. The work is risky but high in demand, especially in offshore oil and gas projects.
How Long Does It Take to Become a Combo Welder?
How long does it take to become a combo welder? It typically takes about 6 months to 2 years. This timeframe includes schooling or apprenticeship programs, which include hands-on training and theory, allowing you to gain welding certifications and skills.
What’s the Hardest Type Of Welding?
What’s the hardest type of welding? Pipe welding is considered one of the hardest. It requires precise skills and techniques since it involves working in awkward positions and dealing with various materials. Quality is crucial here, as it affects safety and durability.
What Makes a Good Welder?
What makes a good welder? A good welder possesses strong attention to detail and excellent hand-eye coordination. They need to understand different welding techniques, metallurgy, and safety protocols to ensure high-quality work.
Where Can I Buy a Miller Welder?
Where can I buy a Miller welder? You can purchase a Miller welder from their official website, authorized dealers, or major retailers like Home Depot and Lowes. Prices vary based on the model and features, typically ranging from $200 to over $2,500 (USD).
Conclusion
I hope this gave you what you needed about combo welders. We covered what a combo welder is, how it works, the types available, steps to set it up, factors influencing performance, common problems, aftercare tips, applications, and alternatives to using one. We touched on everything from buzz box welders to good gifts for welders.
A combo welder is a multi-purpose tool that combines different welding processes. This means you can tackle various projects, whether it’s MIG, TIG, or stick welding, all in one machine. If you need additional advice, I’m here to help, so don’t hesitate to ask about choosing the right welder for your needs.
For further insights into the world of welding, feel free to explore more at What is Welding.
References
- ISO. (2017). ISO 3834: Quality Requirements for Fusion Welding of Metallic Materials. Geneva, Switzerland: ISO.
- American Welding Society. (2020). AWS C5.6: Recommended Practices for Gas Metal Arc Welding. Miami, FL: AWS.
- American Welding Society. (2020). AWS Welding Handbook: Welding Science and Technology (Vol. 1). Miami, FL: American Welding Society.
Joe Carter is a retired welding professional with over 40 years of hands-on experience in the industry, spanning ship repair, structural welding, and even underwater projects. Joe is a master of MIG, TIG, and Stick welding. Passionate about mentoring the next generation of welders, Joe now shares his decades of expertise and practical insights to help others build rewarding careers in welding.
American Welding Society, Combo Welder, MIG Welding, Pipe Welding, TIG Welding, Welding, Welding Applications, Welding Processes, Welding Techniques