How to Weld Steel to Steel? A Guide on Techniques, Preparation, and Safety
Published on: March 10, 2025 | Last modified: March 4, 2025
By: Joe Carter
And how to weld steel to steel is crucial for creating solid joints. If you don’t follow the right steps, you might end up with weak welds that could fail under pressure. I’ve seen firsthand how a small mistake in welding can lead to big problems down the line.
In this guide, you’ll learn about what steel is, various steel types and their weldability, prerequisites for welding, steps for welding steel, safety measures, types of welding suited for steel, factors affecting welding, common issues, aftercare and inspection, key benefits, applications, other options, and frequently asked questions. This comprehensive approach will simplify how to weld steel and ensure your projects are successful.
Contents
- How to Weld Steel to Steel?
- What is Steel?
- Types Of Steel and Their Weldability
- Prerequisites: Things You Should Prepare in Advance
- Steps for Welding Steel to Steel
- Safety Measures
- Types Of Welding for Steel
- Factors Affecting How to Weld Steel to Steel
- Common Issues
- Aftercare Tips for Welding Steel to Steel
- Advanced Techniques for Welding Steel to Steel
- Key Benefits
- Applications You Should Know About
- Other Options You Can Consider
- Frequently Asked Questions (FAQs)
- Additional Reading
How to Weld Steel to Steel?
Steel, a strong alloy of iron, is key in how to weld steel to steel. You need a MIG or TIG welder, wire or rod, and protective gear. It’s moderately difficult, commonly used in constructions and vehicles.
What is Steel?
Steel is an alloy made primarily of iron and carbon, typically containing 0.2% to 2.1% carbon by weight. It can also include small amounts of manganese, silicon, or other elements to enhance its properties. Steel’s strength comes from its crystal structure and composition. This alloy has a tensile strength between 370 megapascals (Mpa) and 1,600 MPa (54,000 Psi to 232,000 Psi), making it a strong and versatile material.
Now, let’s discuss how to weld steel to steel. When you weld steel, you need to consider factors like the type of steel and the welding method. In my experience, TIG welding provides great control, especially for thinner materials. It’s about finding the technique that works best for you.
While working on a custom metal frame, learning how to prep steel for welding proved invaluable. Ensuring that the surfaces were clean and fit properly made the process much easier. It’s crucial to remember that proper steel prep can significantly affect the outcome of your welding, such as when joining structural steel to create a sturdy support.
Types Of Steel and Their Weldability
-
Mild Steels
Mild steel is low-carbon steel, making it easy to weld. To connect mild steel pieces, use electric arc or MIG welding. Start by cleaning the surfaces, then use a 0.035-inch (0.9 Mm) wire with CO2 shielding gas for a clean joint.
-
Stainless Steels
Stainless steel is known for its corrosion resistance. You can weld it using TIG or MIG processes. Ensure you use compatible filler metal, such as ER308L, and maintain a clean environment to prevent contamination.
-
Carbon Steels
Carbon steels come in different grades, affecting their weldability. Preheat thicker sections to about 400°F (204°C) to prevent cracking. Use 7018 electrodes for a strong bond in 1/8-inch (3.2 Mm) fillet welds.
-
Alloy Steels
Alloy steels contain elements that enhance strength and toughness. Welding, as outlined in various methods for welding by metals, requires attention to heat input. To avoid distortion, use low-heat settings and coat joints with anti-spatter spray for cleaner results.
Additionally, mastering techniques to efficiently cut welds can significantly improve precision in metalwork projects.
-
Tool Steels
Tool steels are hard and designed for making tools. Welding can be tricky due to heat treatment. Preheat up to 500°F (260°C) and select a suitable filler like AWS E8018 to ensure a strong weld.
For those delving into different welding techniques, understanding how to weld edge joints can enhance your welding repertoire significantly.
We have now covered the various types of steel and their weldability. Next, we will examine essential preparations to undertake in advance.
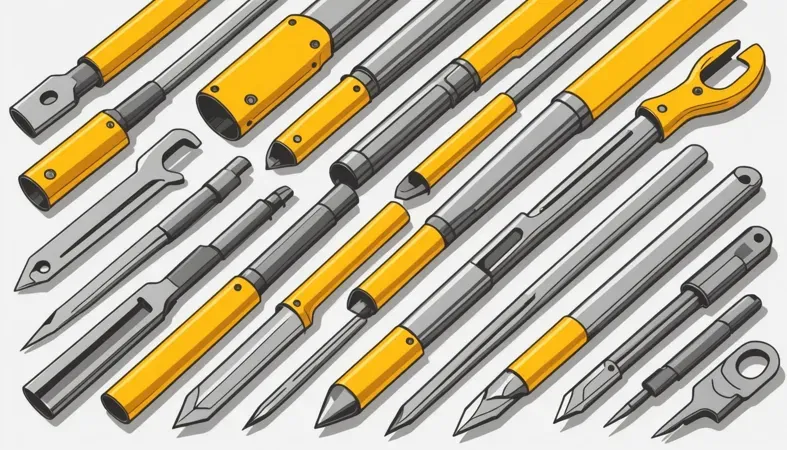
Prerequisites: Things You Should Prepare in Advance
What do you need to get started?
- MIG Welder: You need a MIG welder, like the Lincoln Power MIG 210. It’s crucial for efficiently joining steel and ensuring strong welds.
- Shielding Gas: You should have a cylinder filled with 75% Argon and 25% CO2. This mixture protects the weld from contamination, resulting in a cleaner joint.
- Welding Wire: You’ll need a spool of ER70S-6 welding wire, preferably around 0.030 in (0.76 Mm). This wire is ideal for various steel types, providing good results.
- Ground Clamp: A reliable ground clamp, such as the Miller 200427, is necessary. This ensures a solid electrical connection, essential for weld quality.
- Clean Steel Surface: Prep the steel with a wire brush or grinder. Clean surfaces allow better weld penetration and overall bond strength.
You should now have a good understanding of necessary preparations for welding. In the next part, we’ll discuss the steps for welding steel to steel.
Steps for Welding Steel to Steel
Here are the steps for correctly welding steel together. Follow these closely for the best results.
-
Prepare the Steel Surfaces
Clean all rust, dirt, and grease from your steel surfaces. Use a wire brush or grinder to expose shiny metal. This step significantly affects weld quality. If you skip it, your weld won’t penetrate properly and may result in weak joints.
For optimal results, aim for a smooth surface with no contaminants. Joint preparation is crucial when welding thinner materials. A clean surface ensures a stronger bond, vital for durability.
-
Set Up the Welding Equipment
Set up your welding machine according to the steel thickness. For 1/8 in (3.175 Mm) steel, use about 90-130 Amps for MIG welding. I remember having issues my first time because my settings were off, so double-check them!Ensure the ground clamp is securely attached to your workpiece. This reduces arc blow and enhances arc stability. Trust me, it makes a noticeable difference!
-
Adjust the Welding Parameters
Set the appropriate voltage and wire feed speed based on your welding process. For MIG welding 1/4 in (6.35 Mm) steel, use about 18-20 volts and a wire feed speed of around 300 inches per minute (7.62 M/min). The right settings prevent burning through the steel.
Don’t underestimate the importance of shielding gas. For MIG with CO2, a mix of 75% Argon and 25% CO2 offers the best penetration. If I’m working with stainless steel, I increase the Argon for better results.
-
Perform the Welding Procedure
Start your weld, maintaining a steady and even speed to create a consistent bead. Overlapping can lead to poor penetration and potential structural failure. Aim for a travel speed of 8-12 in/min (20-30 Cm/min) for most applications.
If you’re welding multiple passes, let each layer cool slightly before adding the next. This helps avoid distension and warping. I’ve seen many beginners skip this and regret it later due to warped materials!
We covered techniques for welding steel to steel here. Next, we will cover safety measures to ensure a secure process.
Safety Measures
Let’s focus on essential precautions for welding steel to steel.
- Use Proper PPE: Always wear gloves, masks, and safety glasses. I recommend Jackson Safety Velocity LX Goggles for comfort and effectiveness. They provide maximum eye protection from sparks and spatter.
- Maintain a Clean Workspace: Keep your area free of clutter and flammable materials. A clean workspace reduces fire risks and distractions.
- Ventilate Your Area: Work in well-ventilated spaces to avoid inhaling harmful fumes. Use a gas meter to monitor toxic gas levels; OSHA recommends a maximum exposure of 5 ppm.
- Check Equipment: Regularly inspect your welding gear for wear and tear. Using Miller Electric tools (Like the Multimatic 215) reduces malfunctions, enhancing safety. A well-functioning machine leads to fewer accidents.
Remember, prioritizing safety precautions is my top tip for a successful weld.
So far we covered safety precautions. Next, let’s look at the different types of welding used for steel.
Types Of Welding for Steel
Let’s explore the types of welding for steel, including MIG, TIG, Stick, Flux-Cored Arc, and Submerged Arc welding.
-
MIG Welding
MIG welding (Metal Inert Gas Welding) is a popular method for steel. It uses a continuous wire feed as the electrode and an inert gas to shield the weld. Weld speeds range from 10 to 25 inches per minute (25 to 63 Cm/min), depending on settings.
-
TIG Welding
TIG welding (Tungsten Inert Gas Welding) provides cleaner and more precise welds. It uses a non-consumable tungsten electrode and requires filler metal. Typical current settings range from 20 to 250 amps for effective steel welding. Welding safety is crucial in mitigating hazards associated with this process, and understanding how dangerous welding is can help in implementing proper precautions.
-
Stick Welding
Stick welding (Shielded Metal Arc Welding, or SMAW) is straightforward and versatile. It utilizes a coated electrode that melts to form a weld. Speeds range from 20 to 50 inches (50 to 127 Cm) per minute, making it ideal for outdoor work.
-
Flux-cored Arc Welding
This welding type is similar to MIG but uses a tubular wire filled with flux. It’s suitable for thick steel and performs better in windy conditions. Many welders achieve speeds of 16 to 20 inches per minute (40 to 51 Cm/min), making it efficient for heavier materials.
-
Submerged Arc Welding
Submerged Arc Welding (SAW) involves welding with a continuously fed wire while the weld zone is covered by granular flux. This method excels with thick steel sections and can deliver deposition rates up to 18 pounds per hour (8.2 Kg/h), making it highly productive.
When considering welding techniques, it’s important to be aware of potential risks, particularly the hazards associated with welding galvanized steel, which pose significant safety concerns. Discover more about welding galvanized steel safely.
Factors Affecting How to Weld Steel to Steel
What factors impact your welding process? Here are the key ones.
-
Material Thickness
Steel thickness matters, especially if it’s 1/8 inch (3 Mm) or more. Thicker material requires higher heat and different filler materials for a strong bond.
-
Welding Speed
Welding too fast can lead to weak joints, while going too slow can overheat and warp the steel. Aim for a speed of 2-3 inches per minute (5-8 Cm) for thin materials.
-
Joint Design
Joint design is crucial for weld quality. A proper groove or butt joint allows better penetration, which is essential, especially with carbon steel and alloys.
-
Heat Input
Heat input affects how well the steel bonds during welding. An ideal range is around 25-40 kJ/m (15-30 Kj/in), depending on the steel type and thickness.
-
Welding Position
Welding position influences your technique and weld quality. Overhead or vertical welding generally requires more skill and control than flat welding.
Common Issues
Let’s look at unique problems you might face when welding steel.
-
Porosity in Welds
Steel can develop porosity, which appears as bubbles in your weld. You can spot it by examining a finished joint closely. To fix it, ensure no contaminants, like oil or moisture, are on your steel before welding. Tackling more challenging techniques, such as performing welds in difficult positions, requires understanding something like how to weld upside down.
-
Inconsistent Weld Quality
Steel may show inconsistent welds from poor technique. It’s essential to maintain a steady travel speed and use the correct voltage. Check your welder settings and practice uniform motions.
-
Burn Through
This occurs when steel overheats during welding, creating holes. You’ll recognize it by excessive drips or holes in your weld. Lower your heat settings to prevent this in the future.
-
Weld Cracking
Weld cracking can damage the structural integrity of steel joints. They usually appear as straight lines in the welds. Preheat the steel before welding and post-heat it to minimize cracks.
-
Under-mixing Of Alloys
If you’re mixing alloys in steel welding and it has an uneven composition, that’s under-mixing. Look for inconsistencies in metallurgical properties. Ensure thorough mixing before use.
Aftercare Tips for Welding Steel to Steel
Here are some key aftercare, inspection, and advanced techniques to ensure a successful weld.
Aftercare Tips
After finishing your steel weld, let it cool gradually for 2 to 4 hours to prevent warping. Apply a light coat of anti-corrosion spray, like WD-40, to protect the welded area from rust. Regularly check for heat-induced cracks, especially in the HAZ (Heat Affected Zone); these can lead to structural failure. Learning effective heliarc welding techniques can enhance your welding skills and ensure better results in your future projects. For more information on heliarc welding, check out how to heliarc weld.
Inspection Techniques
Inspect your welded joints using ultrasonic testing for invisible flaws, ensuring the sensitivity is at least 0.2 mm (0.008 In). Use a magnetic particle test (MPT) to find surface cracks effectively. I recommend the Magnaflux® kit; it’s simple and reliable for detecting defects.
Advanced Techniques for Welding Steel to Steel
Let’s dive into some expert techniques to enhance your welding skills and ensure high-quality results.
Tack Welding
- Tack welding involves creating small, temporary welds to hold pieces in position before the final weld.
- This technique helps align materials precisely and reduces the risk of distortion during the main welding process.
Preheating
- Preheating steel before welding can minimize thermal stress and prevent cracking.
- Typically, you should preheat thicker steel sections to around 150-300°F (65-150°C), depending on the material specifications.
Stringer Beads vs. Weave Patterns
- Stringer beads create a narrow, consistent weld, ideal for thin metals or those prone to distortion.
- Weave patterns involve moving the electrode in a zigzag motion, allowing better coverage on thicker materials.
Backing Bars
- Using backing bars during welding can reduce burn-through on thin materials.
- These bars provide support and help maintain weld integrity, particularly in vertical and overhead positions.
Technique | Benefits | Ideal For |
---|---|---|
Tack Welding | Aligns workpieces, minimizes distortion | All steel types, initial setup |
Preheating | Reduces cracking risk, improves weld quality | Thick steel sections |
Stringer Beads | Precise, controlled welds | Thin metals |
Weave Patterns | Wider coverage, ideal for thick metals | Thicker steel pieces |
Backing Bars | Prevents burn-through, maintains weld integrity | Thin materials, vertical welding |
Key Benefits
The biggest advantage of welding steel to steel is the strength of the bond. While working on a custom frame, this skill helped me create durable structures that can withstand loads.
Moreover, this technique enhances versatility by allowing the joining of various steel types, improving fabrication speed, and reducing material costs. It also enables repairs on existing structures, saving you time and effort.
Applications You Should Know About
I’ve known people to use welding techniques to join steel for many projects. However, it has several unique applications, such as:
- Automotive Frame Repair: It’s crucial for fixing car frames and restoring structural integrity. This application is popular among mechanics.
- Steel Beams in Construction: It joins steel beams, ensuring strength in buildings. It’s standard in commercial construction.
- Pipeline Construction: Welded joints secure gas and oil pipelines, essential for safety and durability in the industry.
- Artistic Sculptures: Artists use welding to create large metal artworks. It’s a growing trend in modern art installations.
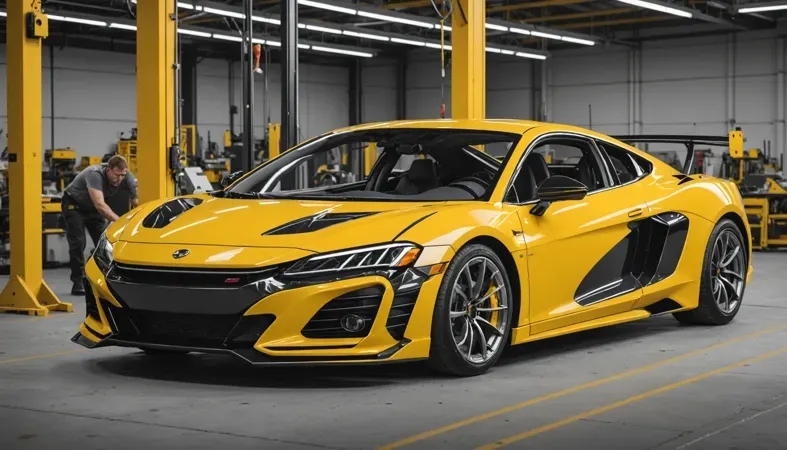
Other Options You Can Consider
You may also explore using adhesives like epoxy for bonding steel. Products such as JB Weld or Permatex Steel Weld work effectively when high heat or pressure isn’t feasible. It’s often preferred in applications where welding might weaken surrounding materials.
Another great option is brazing. This technique uses a filler metal with a melting point above 450°C (842°F) to join steel parts. It’s a cleaner choice and offers a strong bond, similar to what you get with traditional welding.
Frequently Asked Questions (FAQs)
Now let us look at some questions I typically get asked.
How Do You Join Steel to Steel?
To join steel to steel, you can use techniques like welding, bolting, or riveting. Welding creates a strong bond by melting and fusing metal together, which is particularly effective for projects involving steel welding, while bolting involves mechanical fasteners. On average, welded joints are 75% stronger than the base metal, making welding a preferred choice.
You can explore various welding positions used in industry by learning about 1F to 4F welding techniques.
Can You Weld Two Different Steels Together?
Yes, you can weld two different steels together. However, you’ll need to consider their chemical composition and properties. Differing carbon content affects permeability and hardness. For optimal results, aim for similar types like low-carbon steel with a maximum carbon difference of 0.4% to ensure proper fusion.
What Welder Do I Use for Steel?
For welding steel, a MIG (Metal Inert Gas) welder is highly effective. MIG welding is easy for beginners and offers a smooth, continuous feed of filler metal. Consider a welder with at least 200 A (Amps) for general steel applications, ensuring compatibility with thick materials.
How Do You Bond Steel to Steel Without Welding?
You can bond steel to steel without welding using adhesives or mechanical fasteners. Epoxy adhesives can create strong bonds, with tensile strengths of up to 30 MPa (4350 Psi), depending on the product. Mechanical solutions include using bolts or rivets for quick assembly.
How to Prep Steel for Welding?
To prep steel for welding, clean the surfaces thoroughly to remove rust, oil, and dirt. A clean surface improves the quality of the weld. Typically, a power sander or grinder works well, creating a surface finish of 1.5 to 3 micrometers for the best adhesion.
How Do I Anneal Steel After Welding?
To anneal steel after welding, heat it uniformly to a temperature between 550°C and 700°C (1022°F to 1292°F). This process relieves internal stresses from welding and improves ductility. After heating, slow-cool the steel to room temperature to complete the annealing process.
I’m glad we could cover this together. We discussed essential items like what steel is, types of steel and how well they can be welded, prerequisites for welding, steps involved in the welding process, safety measures, types of welding techniques for steel, factors affecting the welding process, common issues you might face, aftercare and inspection tips, along with the key benefits and applications of welding steel. We even touched on other options you can consider and answered some of your frequently asked questions.
To wrap it up, learning how to weld steel to steel means knowing the right preparation, safety measures, and techniques to use. Remember the steps we covered: choose the right type of steel, prep it properly, and use the suitable welding method. Keep in mind that with the right tools, like a MIG or TIG welder, and proper techniques, you’ll create strong, reliable welds every time.
For further insights and information about welding, feel free to explore more at What is Welding.
Additional Reading
- American Welding Society. (2015). AWS D1.1/D1.1M: Structural Welding Code – Steel. Miami, FL: AWS.
- Welding Institute (TWI): https://www.twi-global.com
- European Welding Federation (EWF): https://www.ewf.be
Joe Carter is a retired welding professional with over 40 years of hands-on experience in the industry, spanning ship repair, structural welding, and even underwater projects. Joe is a master of MIG, TIG, and Stick welding. Passionate about mentoring the next generation of welders, Joe now shares his decades of expertise and practical insights to help others build rewarding careers in welding.
American Welding Society, Metal Fabrication, MIG Welding, Steel Welding, TIG Welding, Welding, Welding Safety, Welding Techniques, Welding Wire