How to Weld HDPE? Steps, Types, and FAQs
Published on: February 6, 2025 | Last modified: March 4, 2025
By: Joe Carter
HDPE stands for high-density polyethylene. It’s a tough, lightweight plastic often used in containers, pipes, and more.
I get asked all the time about how to weld hdpe. It’s crucial to follow the right steps because improper welding can lead to leaks or breakage. I’ve seen this firsthand; a faulty joint can ruin your whole project and waste time and money.
In this guide, we’ll explore what is HDPE, different types of HDPE and their weldability, steps to weld HDPE, factors affecting HDPE welding, and frequently asked questions. This resource will help you determine if you’re wondering can you weld hdpe or how to weld hdpe sheets effectively.
Contents
How to Weld HDPE?
HDPE, or High-Density Polyethylene, is a tough plastic. So, how to weld HDPE? Use a hot air tool at about 220°C (428°F) and weld with rods. It’s moderately challenging and often used in tanks, pipes, and outdoor furniture.
What is HDPE?
High-Density Polyethylene (HDPE) is a thermoplastic made from the polymerization of ethylene. It has a density of 0.93 to 0.97 g/cm³ (Grams Per Cubic Centimeter), providing strength and durability. This material has impressive chemical resistance and impact strength, often outperforming other plastics in tough conditions. With a melting point of about 120-180 °C (248-356 °F), HDPE is versatile and widely used.
Now, let’s discuss how to weld HDPE. When I first tried welding HDPE, I was surprised by how simple it could be with the right tools. You need to choose the specific temperature and methods suited for HDPE, as these can significantly affect your results.
A friend used HDPE sheets to build a water fountain in his garden. He wondered if he could weld HDPE to seal the joints and prevent leaks. He found that with the right welding kit and a bit of practice, he could effectively weld HDPE plastic sheets. Ever thought about how to weld HDPE pipe? It opens up a world of creative construction possibilities!
Types Of HDPE and Their Weldability
What types of HDPE can you work with?
High-density Polyethylene
High-Density Polyethylene (HDPE) is strong and durable. To join two pieces of HDPE, use a suitable welding gun. Preheat the surfaces to about 260°C (500°F) before applying the welding rod.
Recycled HDPE
This type is made from post-consumer products, benefiting the environment. To weld recycled HDPE, ensure the surfaces are clean and dry. Use an HDPE welding kit, setting the temperature to about 210°C (410°F) for best results. It’s important to be aware of potential risks such as sunburn from welding.
Color Masterbatch HDPE
Color Masterbatch HDPE is infused with color for aesthetics. Since color affects heat absorption, set your welding temperature to about 220°C (428°F) when welding this type. Prep your edges carefully to enhance the joint.
HDPE Foam
This lighter, more flexible form is often used in packaging. To weld HDPE foam, use a lower temperature around 180°C (356°F) to avoid melting it. For those unfamiliar with the process, understanding plastic welding techniques can be quite beneficial. Align the edges carefully and make quick passes with your welding gun.
When making precise repairs, it’s important to know how to cut welds effectively for optimal results.
Sheet HDPE
Sheet HDPE has versatile applications in construction and industry. For this, use extrusion welding. Start by heating to around 240°C (464°F) and apply the rod evenly to create a solid seam.
We have now covered the various types of HDPE and their weldability. The next section will discuss common welding techniques for HDPE.
Common Welding Methods for HDPE
When it comes to welding HDPE, different methods suit different applications. Understanding these methods is essential for a successful weld. Here are the main ones:
Welding Method | Best Use | Temperature Range (°C / °F) | Advantages |
---|---|---|---|
Hot Air Welding | Sheet and pipe welding | 200-300 °C / 392-572 °F | Good for large areas and joints |
Butt Fusion | Pipes and fittings | 210-260 °C / 410-500 °F | Strong seams with minimal equipment |
Electrofusion | Pipes and connections | Varies with fittings | No open flame; great for tight connections |
Extrusion Welding | Large fabrications and repairs | 220-240 °C / 428-464 °F | Fast and creates thick seams |
Laser Welding | Thin sheets and intricate designs | Varies significantly | Precise, minimal thermal impact |
Each method has its context. For instance, if you’re working on a large pipe project, butt fusion might be your best bet. Think about your specific needs before getting started!
We covered various welding techniques for HDPE. We will now cover the process involved in welding HDPE.
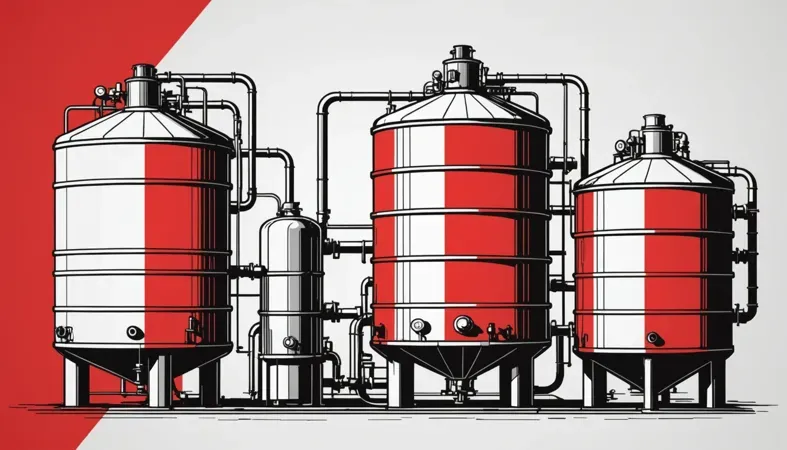
Steps to Weld HDPE
We’ll cover the steps for effectively welding HDPE. Follow each step closely for the best results.
Prepare the Surface
Clean the surfaces you’ll weld. Dust, oil, or moisture can ruin the bond. Use a cloth soaked in isopropyl alcohol. Ensure the surfaces are dry before applying heat.
Choose the Right Welding Technique
Select a suitable welding method for your project. Options include extrusion welding, hot air welding, or butt fusion. These methods operate at different temperatures—commonly between 220°C and 300°C (428°F to 572°F) depending on the HDPE type. Each technique has different setups, so choose wisely!
Set Up the Equipment
Gather your welding tools, like a welding gun, HDPE rod, and temperature gauge. Set your welding heat gun to the correct temperature, usually between 200°C and 300°C (392°F to 572°F) for HDPE. Keeping the temperature steady is crucial; fluctuations can ruin your weld!
Heat the HDPE Ends
Heat both edges of the HDPE pieces until they become glossy—this means they’re ready to bond. A good rule of thumb is to apply heat for about 30 to 60 seconds. Keep moving the gun to avoid overheating. Once they’re hot enough, you’ll notice a slight sag in the material—this is your cue to proceed.
Join the Pieces Together
Press the heated edges together with firm, even pressure. Ensure proper alignment; misalignment can weaken the joint. Hold the pieces together for about 10 to 15 seconds as they cool slightly and bond. Monitor the joint for any gaps or separation as it cools.
Allow for Proper Cooling
Let the weld cool fully—at least 10 to 15 minutes—before handling. Faster cooling can leave a weak joint. Avoid moving or stressing the weld during this time. Patience is key for a reliable finish! Additionally, understanding the importance of a suitable table height can significantly enhance your welding efficiency and safety. Find out more about ideal welding table height for your projects.
So far we covered the steps for welding HDPE. Let’s look at the factors that influence HDPE welding next.
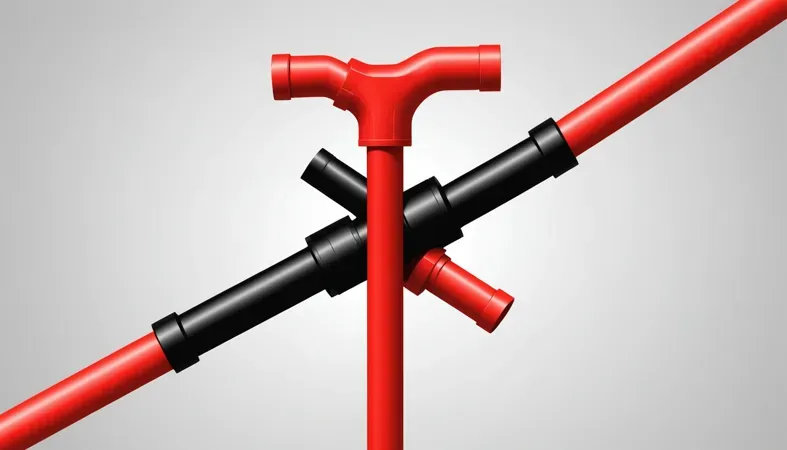
Factors Affecting HDPE Welding
What factors impact welding high-density polyethylene? Let’s break it down.
Material Thickness
Thicker HDPE (Over 10 Mm or 0.39 In) requires higher heat inputs for effective welding. This affects how well layers bond, potentially leading to weak joints.
Welding Temperature
A typical HDPE welding temperature ranges from 220°C to 260°C (428°F to 500°F). Too low a temperature results in poor fusion, while too high degrades the material structure.
Joint Design
A good joint design maximizes strength. For instance, a V-groove can enhance the fusion we’ve discussed.
Cooling Rate
The cooling rate significantly impacts weld strength. Rapid cooling can introduce stresses, leading to cracks in thicker sections.
Presence Of Contaminants
Dirt or moisture on HDPE surfaces can hinder adhesion. Clean joints before welding to maintain high bond integrity.
That covers the elements influencing HDPE welding. Let’s now take a look at common questions and answers regarding this topic.
Frequently Asked Questions (FAQs)
Here are some questions I typically get asked about HDPE welding.
Can HDPE Be Welded?
Yes, HDPE can be welded. It’s essential to use the right technique and equipment, such as fusion welding, to ensure a strong bond. Failure to follow proper procedures can lead to weak joints, which can fail under stress.
What is the Welding Technique for HDPE?
The primary welding technique for HDPE is hot gas fusion welding. This method uses heat to melt the HDPE surfaces, joining them together. It’s effective for creating strong, waterproof seams that are crucial in construction and plumbing.
How to Join HDPE Together?
You can join HDPE using techniques like butt fusion, electrofusion, or extrusion welding. Each method has specific applications and advantages, such as speed or strength, and choosing the right one depends on your project’s requirements.
How Hot to Weld HDPE?
When welding HDPE, you should heat the materials to around 220°C (428°F). This temperature ensures that the HDPE melts properly for a secure bond. Too hot can damage the material, so be precise in your temperature control.
What to Weld HDPE With?
You should weld HDPE with a polyethylene rod or specially designed welding strips. These materials match the HDPE composition, promoting strong joints. Make sure to use fillers that have compatible material properties for the best results. While considering the type of protective gear necessary, there’s often curiosity about welding with prescription glasses.
Summary
We covered the basics of how to weld HDPE, discussing what HDPE is, its types, and their weldability. We outlined steps to weld HDPE, factors affecting the process, and answered frequently asked questions. This gives you a well-rounded understanding of HDPE welding.
So, how to weld HDPE? Simply put, you heat the HDPE material, applying a suitable welding technique like butt or socket welding. Remember, successful welding depends on using the right temperature, roughly 200-220°C (392-428°F), and understanding the type of HDPE you’re working with.
For more in-depth information and the latest technical expertise, visit What is Welding.
References
- American Welding Society. (2020). AWS A3.0: Standard Welding Terms and Definitions. Miami, FL: AWS.
- Blodgett, O. W. (1996). Design of Welded Structures. Cleveland, OH: James F. Lincoln Arc Welding Foundation.
Joe Carter is a retired welding professional with over 40 years of hands-on experience in the industry, spanning ship repair, structural welding, and even underwater projects. Joe is a master of MIG, TIG, and Stick welding. Passionate about mentoring the next generation of welders, Joe now shares his decades of expertise and practical insights to help others build rewarding careers in welding.
American Welding Society, DIY Welding, HDPE, HDPE Types, Pipe Welding, Plastic Welding, Thermoplastics, Welding, Welding Table, Welding Techniques