How to Weld Aluminum? Steps, Tips, and Techniques Covered
Published on: November 16, 2024 | Last modified: March 4, 2025
By: Joe Carter
Aluminum is a lightweight, silvery-white metal. It’s known for being strong and resistant to corrosion.
One question I get asked a lot is how to weld aluminum. It’s so important to follow the right methods because improper techniques can lead to weak joints. In my experience, I’ve seen many welders struggle when they don’t respect aluminum’s unique properties, which is a shame.
In this guide on how to weld aluminum, I’ll cover types of aluminum and their weldability, necessary prerequisites, detailed steps for welding aluminum, important precautions, various welding techniques, factors impacting aluminum welding, common problems you might face, along with aftercare tips. I’ll also discuss the benefits of welding aluminum, its typical applications, alternatives to welding, and answer some frequently asked questions. Get ready to learn exactly what you need to weld aluminum effectively!

Contents
- How to Weld Aluminum?
- What is Aluminum?
- Types Of Aluminum and Their Weldability
- Prerequisites
- Precautions
- Steps to Weld Aluminum
- Types Of Welding for Aluminum
- Factors Affecting Aluminum Welding
- Welding Aluminum Alloys: Detailed Techniques
- Typical Issues in Aluminum Welding
- Aftercare, Inspection, and Advanced Tips for Welding Aluminum
- Why This is Worth It: Advantages
- Typical Applications
- Exploring Alternatives to Welding Aluminium
- Frequently Asked Questions (FAQs)
- Conclusion
- References
How to Weld Aluminum?
How to weld aluminum? Aluminum is a lightweight, corrosion-resistant metal. To weld aluminum, use a TIG welder, with a tungsten electrode and filler rod typically at 20 to 30 amps. It’s tricky, often used in automotive and aerospace.
What is Aluminum?
Aluminum is a lightweight metal with atomic number 13. This silvery-white element weighs about 2.7 grams per cubic centimeter (G/cm³) or 168.5 pounds per cubic foot (Lb/ft³). It’s known for its corrosion resistance due to a protective oxide layer that forms naturally on its surface. Did you know aluminum makes up about 8% of the Earth’s crust? That’s significant!
When it comes to welding aluminum, you need to know some key details. There are various methods like MIG, TIG, and stick welding. In my experience, TIG welding is excellent for thick sections, offering precise control. You really get to showcase your skills with it.
Thinking about how to weld aluminum at home? I remember trying to weld two aluminum pieces together for a project. It was challenging, but with the right setup, I managed to do it! You need to focus on choosing the right equipment, from welding machines to filler materials, especially when working with different aluminum grades.
Types Of Aluminum and Their Weldability
What are the types of aluminum in relation to welding?
-
Wrought Aluminum Alloys
This type is shaped by mechanical processes. Use MIG or TIG methods for welding wrought aluminum. Choose ER4047 or ER5356 filler wires, and set your welder to about 200-250 amps for optimal fusion. To enhance your welding results, it is crucial to avoid spatter in welding.
-
Cast Aluminum Alloys
These alloys are created by pouring molten aluminum into molds. Use TIG welding for precision. Preheat to around 150°F (65°C), use ER4047 filler, and keep your arc tight to avoid porosity.
-
Heat-treatable Aluminum Alloys
These alloys gain strength from heat treatment. Use a specialized filler like 5356. Preheat to 350°F (175°C) and maintain gentle cooling to prevent cracks.
-
Non-heat-treatable Aluminum Alloys
This type maintains strength without heat treatment. Use MIG or stick welding. Choose an appropriate filler like 4045 and set your welder to a lower heat setting of about 150-180 amps.
-
Aluminum-lithium Alloys
These alloys contain added lithium for lighter weight. Use alloy-specific techniques like TIG. Keep temperatures below 800°F (425°C) to avoid weakening the base material.
We covered different types of aluminum and their weldability here. Next, we will cover the prerequisites for welding.
Prerequisites
What do you need to get started?
- TIG Welder: You need a reliable TIG welder, like the Lincoln Electric Square Wave TIG 200. It’s essential for clean, precise aluminum welds.
- Aluminum Filler Rods: Use filler rods made of 4047 aluminum alloy. These rods create strong bonds at high temperatures, ideal for aluminum welding.
- Argon Gas Cylinder: Get an argon gas cylinder, such as Harbor Freight’s 125 cu. ft. (3,532 L) tank. It provides shielding gas that prevents contamination during welding.
- Welding Aluminum Cleaner: Use a cleaner like Weld-Aid AL-15. It removes oxides and impurities, promoting better weld quality and adhesion.
You should now have a good understanding of the necessary requirements. In the next part, we’ll discuss important safety measures.
Precautions
Let’s cover essential safety measures for welding aluminum.
- Protective Gear: Always wear gloves and goggles to prevent burns and eye injuries. Consider using 3M Peltor safety gear for maximum protection.
- Ventilation: Ensure good airflow in your workspace. Fumes from aluminum welding can be harmful; a fan helps greatly.
- Fire Safety: Keep a fire extinguisher nearby. Aluminum can ignite if overheated; a Class D extinguisher is recommended.
- Proper Tool Handling: Use aluminum-specific tungsten rods to avoid contamination, significantly improving weld quality.
Remember, safety precautions can save lives and prevent injuries. Take them seriously!
That covers safety measures and best practices. Let’s now take a look at the steps for welding aluminum.
Steps to Weld Aluminum
Here are the steps to successfully weld aluminum. Follow them for great results!
-
Prepare the Aluminum Surface
Clean the aluminum thoroughly. Use a wire brush or grind it to remove any oxide layer or contaminants. Aim for a bright, shiny surface. This is crucial because the oxide layer (Al2O3) forms quickly and can cause weak joints if not removed. When preparing to weld on a vehicle, it is essential to know what to disconnect when welding to ensure safety and protect sensitive electronics.
For best results, ensure the surface is free from grease, oil, or dirt. I always use a solvent like acetone for a spotless clean. Trust me, skipping this step can lead to a poor weld—nobody wants that!
-
Select the Appropriate Welding Method
Choose between MIG, TIG, or stick welding for your project. MIG (Metal Inert Gas) is usually the simplest for beginners, while TIG (Tungsten Inert Gas) offers better control and cleaner welds. If you’re working on thin aluminum, I recommend TIG for its versatility and high-quality results.
Analyze your project needs. For heavy-duty work, consider stick welding. Each method requires different settings: MIG usually runs at around 60-100 amps, while TIG can go higher depending on aluminum thickness.
-
Set Up Your Welding Equipment
Adjust your welder settings based on the chosen method. For MIG, set it to DC and adjust the wire feed speed to 250-350 inches per minute, depending on thickness. Your shielding gas should be argon or an argon-helium mixture to protect the weld puddle from contamination.
If you’re TIG welding, a 1.6 mm tungsten electrode works best for general aluminum work. Set your amperage to 150 for 3 mm (1/8 Inch) thick aluminum. Mistakes can lead to insufficient heat and poor penetration, so double-check your settings!
-
Perform the Welding Process
Start by holding the torch at a 15-degree angle and maintain a consistent speed. For a 3 mm (1/8 Inch) joint, travel at about 4 to 8 inches per minute. Watch for a puddle forming; that’s where the magic happens. Don’t rush! Move smoothly to prevent defects.
When welding, overlap the edges slightly to ensure a solid bond. Periodically remove any slag or debris, as it can ruin your weld. Keep a close watch; aluminum can burn more easily than steel, so be alert! Understanding the appropriate safety gear is essential, so make sure to familiarize yourself with the minimum shade for arc welding.
-
Inspect the Welded Joint for Quality
While inspection comes later, visually assess your work as you go. Look for clean, shiny beads without cracks or pits. A good joint should be smooth and uniform. If you see inconsistencies, adjust your technique immediately.
As you gain experience, you’ll develop an eye for quality. Let it dry to prevent contamination and allow for a robust joint.
You should now have a good understanding of welding techniques, preparation, and safety for aluminum. In the next part, we’ll discuss welding methods for aluminum.
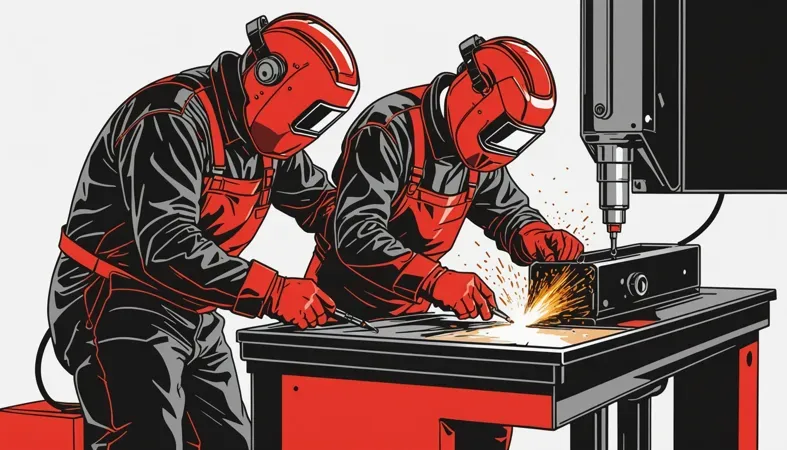
Types Of Welding for Aluminum
Let’s review the different types of welding: MIG, TIG, Stick, Flux-Cored Arc, and Plasma Arc.
-
MIG Welding
MIG (Metal Inert Gas) welding is a popular method for aluminum. It uses a continuous feed of wire and argon gas to shield the weld. This technique is particularly effective for thin materials, typically using a wire speed of about 200 inches per minute (508 cm). For those interested in understanding the various techniques and tools associated with different materials, a deeper dive into welding by metals can provide valuable insights.
Mastering techniques for complex tasks like welding fuel containers can enhance your skill set to weld a gas tank.
-
TIG Welding
TIG (Tungsten Inert Gas) welding provides precision for aluminum projects. It uses a non-consumable tungsten electrode, adding filler material as needed. With heat control, a typical output ranges from 100 to 200 amps for thicker metals.
-
Stick Welding
Stick welding, or SMAW (Shielded Metal Arc Welding), combines coated electrodes with an electric arc. While it’s not the most reliable choice for aluminum, it can work with thicker materials. You’ll typically need 75 to 150 amps, depending on the electrode size.
-
Flux-cored Arc Welding
Flux-Cored Arc Welding (FCAW) is effective for thicker pieces of aluminum. It uses tubular wire with flux inside to create a shield that keeps out contaminants. It can achieve high deposit rates, often around 10-20 pounds per hour (4.5-9 Kg).
-
Plasma Arc Welding
Plasma Arc Welding (PAW) is a high-precision method that produces a concentrated arc. This is ideal for delicate aluminum work, as it allows for tighter weld beads. Amperage typically ranges from 10 to 150, targeting very thin gauges.
Factors Affecting Aluminum Welding
What factors impact the effective joining of aluminum?
-
Material Thickness
The thickness of aluminum influences your choice of welding method. For materials thinner than 5 mm (0.2 Inches), use TIG welding for precision. For thicker pieces over 5 mm, MIG welding may be necessary.
-
Weld Preparation
Preparing the metal surface is crucial. Clean aluminum with a stainless-steel brush or chemical solvent to remove oxidation and contaminants. Neglecting this step can lead to weak welds.
-
Welding Speed
Welding speed can make or break your work. A speed of about 300 mm/min (11.8 Inches/min) is often ideal. Going too fast weakens joints, while too slow can cause distortion or burn-through.
-
Electrode Type
The type of electrode significantly affects the outcome. For instance, 4047 is excellent for MIG welding, while 5356 works well for both MIG and TIG, offering better strength and corrosion resistance.
-
Argon Purity
Using high-purity argon (At Least 99.99%) is essential to prevent contamination. Impurities lead to porosity, weakening your welds and making them less visually appealing, which is crucial for aesthetic projects.
Welding Aluminum Alloys: Detailed Techniques
Let’s dive into the specific welding techniques for various aluminum alloys. Each alloy behaves uniquely during welding, and knowing how to adjust your approach can enhance your results significantly.
Aluminum Alloy | Recommended Welding Technique | Filler Material | Optimal Amperage Range (A) |
---|---|---|---|
2024 | TIG | 4047 | 80-130 |
6061 | MIG or TIG | 5356 | 130-200 |
7075 | TIG | 4047 | 100-200 |
5086 | MIG | 5356 | 150-250 |
4047 | TIG or MIG | 4047 | 100-200 |
In the table above, notice how different alloys require specific techniques and filler materials. For example, 6061 aluminum, one of the most popular alloys, can be welded using both MIG and TIG methods, with 5356 filler often providing excellent results.
Did you know? Using the right filler is key! For aluminum alloys like 2024 and 7075, you might see improved performance with 4047 because of its lower melting point, which helps prevent distortion. Isn’t that fascinating?
Typical Issues in Aluminum Welding
Here are specific problems that can arise with aluminum welding.
-
Porosity in Welds
Aluminum can trap gas during welding, creating tiny holes. Look for a sponge-like texture in the weld to identify this issue. Use proper shielding gases and clean the surface thoroughly.
-
Cracking in Welded Joints
Aluminum may develop cracks, especially when cooling. I’ve encountered this with 6061-T6 alloy. Check for intergranular or hot cracks. Preheating and using the right filler material can help.
-
Inadequate Penetration
Welds in aluminum often experience low penetration. If you notice a lack of fusion, increase the voltage and slow down the travel speed to enhance penetration.
-
Weld Pool Contamination
Contamination from oil or oxide layers can affect aluminum. Identify this issue by a dull appearance in the weld bead. Cleaning the surface and using a dedicated aluminum filler can resolve it. For optimal results, it’s important to select the right welding rod.
-
Heat Affected Zone Softening
Heating aluminum alters its properties in the heat-affected zone (HAZ). Look for distortion or weakening. Use smaller heat inputs and slower travel speeds to manage heat and reduce softening.
Aftercare, Inspection, and Advanced Tips for Welding Aluminum
Here’s essential guidance on caring for your welds, inspecting them closely, and leveling up your skills.
Aftercare Tips
After completing your work, cool the weld gently to prevent cracking. Keep the temperature below 120°C (248°F). Rinse the joint with warm, soapy water to remove flux residues, then rinse with distilled water to avoid contaminants.
Inspection
Inspect the aluminum weld for a penetration depth of at least 1.5 mm (0.06 In). Use an ultrasonic thickness gauge, like the GE PRO, to detect hidden faults. Check the surface for signs of porosity or undercut to ensure integrity—common issues with aluminum.
Expert Tips
If this isn’t your first time, increase your pulsed MIG settings for aluminum. Aim for a duty cycle of around 60% at 150 A to reduce heat input. Use a braided liner for improved wire feeding and minimize adjustments to your Argon gas—a mixture ratio of 75% Argon to 25% Helium increases arc stability.
Why This is Worth It: Advantages
The main benefit of learning to weld aluminum is its lightweight strength. Aluminum has an excellent strength-to-weight ratio, making it ideal for various applications, from automotive to aerospace.
This skill offers several perks. First, you get better corrosion resistance, leading to longer-lasting results. Enhanced electrical conductivity is a plus, especially for certain projects. It’s cost-effective too; welding aluminum can save you time and money on repairs. Finally, the ability to combine aluminum with different metals opens up even more opportunities!
Typical Applications
I’ve seen people use aluminum welding to build lightweight structures. However, it has many applications, such as:
- Aerospace Components: Used for aircraft frames and parts due to their low weight and high strength. It’s popular in the aviation industry for improved fuel efficiency.
- Automotive Manufacturing: Used in car chassis and bodywork. It’s favored for reducing overall vehicle weight without compromising safety.
- Marine Fabrication: Essential for constructing boats and yachts. Aluminum resists corrosion, making it ideal for watercraft.
- Food Packaging: Important for making aluminum cans and containers. It keeps food fresh, and its lightweight reduces shipping costs.
Exploring Alternatives to Welding Aluminium
Looking for alternatives to welding aluminum? You can consider options like adhesive bonding using products such as 3M Scotch-Weld, or riveting with solid aluminum rivets. These methods may be preferred in situations where heat distortion is a concern or when working with thinner materials.
Metal lath and flux can offer great results too! If you’re looking for a simple and effective way to join aluminum, sometimes methods like aluminum brazing with a torch come in handy. As someone who’s been in the field for a while, I’ve seen these alternatives work wonders depending on your project needs.
Frequently Asked Questions (FAQs)
Now let us look at the questions I typically get asked about aluminum welding.
What Kind Of Welding is Used for Aluminum?
For aluminum, the most common welding methods are MIG and TIG welding. MIG welding is fast and efficient, making it ideal for mass production, while TIG welding offers excellent control and is better for intricate work. Each method is suited for different project needs.
What is the Easiest Way to Weld Aluminum?
The easiest way to weld aluminum is using MIG welding with a spool gun. A spool gun helps manage aluminum’s softness and reduces feeding issues. With the right setup, you can achieve strong welds without a lot of experience.
Can a Beginner Weld Aluminum?
Yes, a beginner can weld aluminum, especially with MIG welding. With appropriate equipment and practice, it becomes manageable. Keep in mind that learning the specifics of aluminum characteristics makes a big difference in your results.
Can You MIG Weld Aluminum?
Yes, you can MIG weld aluminum. It requires a spool gun or push-pull setup, which helps feed the aluminum wire correctly. Using an inert gas like argon is essential to prevent contamination during the process.
What Do You Need to Weld Aluminum?
To weld aluminum, you need a quality welding machine, aluminum filler rod, and appropriate shielding gas, usually argon. Also, you’ll need protective gear to ensure safety while welding. Having the right tools makes a huge difference in the outcome.
What Should I Consider When Welding Aluminum?
When welding aluminum, consider its cleanliness and preparation. Aluminum oxide forms quickly, so clean the surface with a wire brush or chemical cleaner. Also, preheat thicker sections to avoid cracking, especially if they’re above 6.35 mm (1/4 Inch).
Conclusion
We have covered a lot in this article on how to weld aluminum. We discussed what aluminum is, types of aluminum and their weldability, and prerequisites for welding. We also looked at the steps to weld aluminum, precautions, different welding types, factors affecting welding, common issues, and aftercare tips.
So, how to weld aluminum? It’s about knowing your materials, using the right techniques like MIG or TIG welding, and following safety practices. If you need proper equipment, temperatures, and processes, you’re set. Contact me if you’d like more guidance on this worthwhile venture, like what equipment and practices you’ll need at home.
For additional insights and resources, you can visit What is Welding to deepen your understanding of all aspects of welding.
References
- Lincoln Electric. (2020). The Procedure Handbook of Arc Welding (15th ed.). Cleveland, OH: Lincoln Electric Company.
- Smith, D. L. (2010). Welding: A Journey to Explore Its History. Dubuque, IA: Kendall Hunt Publishing Company.
Joe Carter is a retired welding professional with over 40 years of hands-on experience in the industry, spanning ship repair, structural welding, and even underwater projects. Joe is a master of MIG, TIG, and Stick welding. Passionate about mentoring the next generation of welders, Joe now shares his decades of expertise and practical insights to help others build rewarding careers in welding.
Adhesive Bonding, Aluminum Alloys, MIG Welding, Safety Precautions, TIG Welding, Welding, Welding Aluminum, Welding Techniques, Wire Feed Speed