How to Weld a Truck Frame? Essential Steps, Safety Tips, and Welding Types
Published on: February 7, 2025 | Last modified: March 4, 2025
By: Tyler James
A truck frame is the backbone of your vehicle. It supports the entire structure and carries the weight of the truck and its loads.
People often ask how to weld a truck frame. Knowing how to weld a truck frame is crucial because it ensures your truck’s integrity and performance. I’ve seen trucks become unsafe due to poor welding, and that’s why I emphasize good welding practices.
In this guide, you’ll learn about truck frames, types and their weldability, what you need to prepare, essential steps to weld, and safety tips. We’ll also discuss which welding methods work best for truck frames, the factors that affect your welding, unique issues you might face, and proper aftercare. Plus, I’ll cover why it’s worth your time and the various applications of welding truck frames.
Contents
- How to Weld A Truck Frame?
- What is a Truck Frame?
- Types Of Truck Frames and Their Weldability
- Prerequisites: Things You Should Prepare in Advance
- Steps to Weld a Truck Frame
- Safety Tips
- Types Of Welding for Truck Frames
- Factors Affecting Truck Frame Welding
- Unique Issues
- Choosing the Right Filler Material for Truck Frames
- Aftercare, Inspection, and Advanced Tips for Truck Frame Welding
- Why This is Worth It: Advantages
- Applications Of Truck Frame Welding
- When to Try a Different Approach
- Frequently Asked Questions (FAQs)
- Additional Reading
How to Weld A Truck Frame?
A truck frame supports the vehicle’s body and parts. To weld a truck frame, clean, fit, and use MIG or TIG welding at 240 amps. This task varies in difficulty, often seen in repairs and modifications.
What is a Truck Frame?
A truck frame, or chassis, is the backbone of a truck. It provides structural support, holding everything together—from the engine to the cargo bed. Generally made of steel, the frame weighs between 400 to 600 lbs (180 to 272 Kg). It’s designed to handle loads up to 3 tons (2,722 Kg) without compromising its integrity.
Now, let’s discuss how to weld a truck frame. When I first tackled this, I learned the importance of proper alignment and strong joints. Trust me, you want a solid connection; it’s critical for safety and durability.
One time, I had to reinforce a truck frame that had seen better days. Knowing how to weld a truck frame is essential when dealing with rusted or cracked surfaces. Choose the welding type, like MIG (Metal Inert Gas) or TIG (Tungsten Inert Gas), based on your material. Repair costs can vary, but typically, you might spend $300 to $800 for frame repairs, and it’s worth it if you want your truck to last.
Types Of Truck Frames and Their Weldability
What types of truck frames will you encounter when welding?
Box Frames
Box frames are sturdy, enclosed structures commonly used in trucks. To weld effectively on a box frame, focus on butt welds (Joining Two Surfaces) or lap welds (Overlapping Two Surfaces). Clean the surfaces thoroughly, use a suitable MIG (Metal Inert Gas) welder, and maintain a steady speed for a consistent bead.
Ladder Frames
Ladder frames resemble a ladder, featuring two longitudinal beams and cross members. Prioritize fillet welds (Triangular-shaped Welds) for strength. Align the beams properly, adjust your welder settings to control heat, and move steadily to avoid warping.
Space Frames
Space frames are lightweight but strong, made from triangulated sections. Use TIG (Tungsten Inert Gas) welding for precise control. Ensure the joints fit perfectly, select the right filler material, and maintain consistent amperage to prevent burn-through.
Modified Frames
Modified frames are custom-altered for specific needs, often found in performance trucks. Welding involves mixing techniques for different sections. Analyze material types, use the appropriate process for each area, and avoid overheating to maintain integrity. It’s essential to understand the brightness levels a welding arc can produce to ensure safety and precision in your work, which is further detailed on how bright a welding arc is.
Monocoque Frames
Monocoque frames integrate the body and frame for weight reduction. Welding these requires high precision. Focus on spot welding techniques, ensure proper fit between parts, and work in small sections to avoid heat distortion.
You should now have a good understanding of truck frame types and their weldability. In the next part, we’ll discuss necessary preparations.
Prerequisites: Things You Should Prepare in Advance
What do you need to get started?
- MIG welder: You need a MIG welder, like the Hobart Handler 140. It’s crucial for welding the truck frame, as it can efficiently handle thick metals up to 0.25 inches (6.35 Mm).
- Welding wire: You should have ER70S-6 wire, such as Lincoln Electric’s .030-inch (0.8 Mm) flux core wire. It ensures strong joints for truck frames.
- Welding cart: A sturdy welding cart, like the Fierce Welding Cart, helps organize your equipment and provides mobility around the truck frame.
- Angle grinder: An angle grinder, such as the Dewalt DWE43114, is essential for prepping the edges of the frame. Clean, smooth edges lead to better weld penetration.
- Steel plates: Obtain 1/4-inch (6.35 Mm) steel plates for necessary reinforcements. They’re critical for patching weak areas in the truck frame.
We’ve wrapped up the essential preparations needed beforehand. Next up, we’ll look at the process of welding a truck frame.
Steps to Weld a Truck Frame
Here are the essential steps to effectively weld a truck frame.
Select Proper Welding Techniques
Choose between MIG welding and Stick welding based on your frame’s condition. For thin materials, I recommend MIG welding. It requires lower heat input and offers better control. Stick welding can penetrate deeper and is useful for thicker sections.
If you’re working with stainless steel or aluminum frames, consider TIG welding. It provides precision and strong, clean welds, which ensures durability. Each type has its advantages, so assess your truck frame’s needs to make the best choice.
Prepare the Surface for Welding
Clean the areas around the welds thoroughly. Remove rust, paint, or grease using a wire brush or grinder. I often use a flap disc with a grinder for efficient cleaning. Aim for a bright, shiny surface—it helps the welds adhere better. Effective welding starts with selecting the right rod and you can master welding pipe techniques using 6010 welding rods.
Next, bevel the edges if they’re thicker than 5 mm (0.2 Inches). Beveling creates a V-groove, increasing weld strength by allowing better penetration. This step significantly affects the outcome!
Proper welding techniques minimize defects such as porosity which can compromise the integrity of the weld. Learn more about what causes porosity in welding to enhance your results.
Secure the Frame Position
Secure your truck frame using clamps or a welding table. You want the frame to be immovable while welding; even slight movements can ruin alignment and strength. Use C-clamps or locking pliers for tighter grips.
Also, consider using filler material to create a gap for the welds, typically around 1.5 to 3 mm (0.06 To 0.12 Inches). This gap provides adequate space to work and improves weld penetration.
Perform the Welding Process
Start the welding process with your chosen technique. For MIG welding, set your machine to 0.8 mm (0.03 Inches) wire and a voltage between 18-20 volts. Ensure your travel speed matches the wire feed; I usually maintain a speed of 2-3 inches per second for a good bead.
If you’re using Stick welding, keep a steady arc length of about 3-5 mm (0.12-0.2 Inches). Moving too fast cools the weld too soon, while moving too slowly can cause burns. Focus on a steady rhythm; it’s critical for even welds.
Monitor the Weld Quality
Observe the strength and consistency of your welds as you go. Look for uniform beads. A good weld should form a slight volcano shape; this indicates solid penetration. Feathering the edges ensures no sharp transitions that could lead to stress points.
Make sure you’re welding in the right position. Flat and horizontal welds are typically easier than vertical or overhead ones. If you switch positions, adjust heat settings and technique accordingly.
That covers the process of welding a truck frame. Let’s now take a look at essential safety tips for welding.
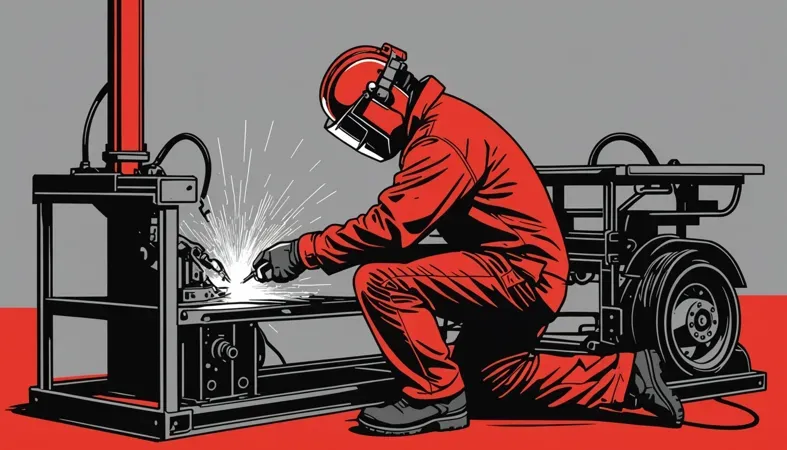
Safety Tips
Let’s quickly discuss essential precautions for welding a truck frame.
- Wear a Welding Helmet – It protects your eyes from harmful rays and sparks. Products like 3M Speedglas helmets provide full protection.
- Ensure Proper Ventilation – Good airflow prevents inhaling toxic fumes, which are harmful in concentrations over 5.0 ppm. A simple fan or a ventilated work area helps.
- Use Fire-Resistant Clothing – Materials can easily catch fire, so wear flame-retardant clothes like a welding jacket. Brands like Lincoln Electric offer excellent options.
- Check Electrical Equipment – Faulty gear can cause electric shock. Routine checks every month ensure your equipment is safe for use.
Taking safety precautions is vital; I can’t stress this enough!
So far we covered essential safety guidelines. Next, let’s look at the different welding methods suitable for truck frames.
Types Of Welding for Truck Frames
Let’s explore the different welding techniques used for truck frames: MIG, TIG, Stick, Flux-Cored, and Submerged Arc welding.
MIG Welding Techniques
MIG welding (Metal Inert Gas Welding) uses a continuous feed of filler wire and a shielding gas, typically argon or CO2. It’s versatile and effective for welding mild steel, making it ideal for many truck frame repairs. Voltage typically ranges from 18-26 volts, with current up to 300 amperes.
TIG Welding Techniques
TIG welding (Tungsten Inert Gas Welding) uses a non-consumable tungsten electrode while manually feeding in filler material. This technique is perfect for precise work on thin materials and provides a clean finish. It generally operates at lower amperage, around 150-200 amps, allowing better control when welding truck frames.
Stick Welding Techniques
Stick welding (Shielded Metal Arc Welding – SMAW) uses a coated electrode to provide both melting and shielding gas. It’s effective for rusty or dirty surfaces, making it handy for rusted truck frames. This method requires a voltage of about 20-30 volts, with amperage between 40 and 300, depending on electrode size.
Flux-cored Welding Techniques
Flux-Cored Arc Welding (FCAW) uses a tubular electrode filled with flux. This technique can be performed with or without shielding gas, making it suitable for outdoor work or windy conditions. Welding voltage ranges from 20-30 volts and current from 130 to 180 amps, effective for heavy-duty truck frames.
Submerged Arc Welding Techniques
Submerged Arc Welding (SAW) covers the weld area with a layer of flux, resulting in a smooth weld with minimal spatter. It’s excellent for thick sections and provides high deposition rates, useful for larger truck frames. Expect voltages around 24-40 volts and currents ranging from 150 to 1000 amps, depending on the application.
Factors Affecting Truck Frame Welding
What factors impact your welding skills on a truck frame?
Material Thickness
Material thickness ranges from 1/8 inch (3.2 Mm) to 1/2 inch (12.7 Mm) on truck frames. Thicker materials require higher amperage settings, typically between 180 to 250 amps, to achieve a solid weld.
Welding Position
You may weld in flat, horizontal, or vertical positions. Each position affects your torch angle and travel speed, influencing bead shape and penetration depth.
Joint Configuration
Joint types, such as butt seams or lap joints, significantly affect the weld. Proper joint preparation, including beveling edges, enhances penetration and strength, especially on thicker frames.
Heat Input Control
Controlling heat input is crucial. Excessive heat can warp the frame, while insufficient heat leads to inadequate penetration and weak joints. Ideal heat settings typically range from 300 to 400 degrees Fahrenheit (149 to 204 Degrees Celsius).
Cooling Rate
The cooling rate affects the weld’s hardness. A slow cooling process reduces stress and brittleness, making it ideal for heavy-duty frames. Consider preheating the area when working with thicker metal.
Unique Issues
Let’s look at issues unique to the truck frame.
Frame Rust and Corrosion
The truck frame often collects road salt and moisture, leading to rust. Check for flaky spots or holes. To fix it, clean the area with a wire brush, apply a rust inhibitor, and consider welding a replacement patch if necessary.
Frame Alignment Challenges
The truck frame can bend after heavy impacts, causing uneven tire wear. Use a frame alignment tool to measure. If it’s misaligned, take it to a professional or use a frame jig for correction.
Weight Distribution Concerns
Proper weight distribution is critical for the truck frame’s longevity. Overloading can cause sagging. Regularly check load distribution and redistribute or trim excess cargo weight to maintain balance.
Compatibility With Existing Structures
When welding modifications to the truck frame, compatibility is key. Verify with the manufacturer’s specifications. If new parts don’t fit, custom fabrication may be necessary.
Load-bearing Requirements
The truck frame must support heavy loads without compromising safety. Consult specifications for maximum load ratings. Weld reinforcements where needed to strengthen weak points.
Choosing the Right Filler Material for Truck Frames
Your choice of filler material is just as important as the welding method. Here’s a breakdown:
Filler Material | Best for | Tensile Strength (psi) | Welding Method |
---|---|---|---|
ER70S-6 | Mild steel frames | 70,000 psi | MIG |
E7018 | High tensile frames | 70,000 psi | Stick |
308L | Stainless steel repairs | 80,000 psi | TIG |
ER120S-X | High-strength applications | 120,000 psi | MIG/TIG |
Selecting the right filler material enhances joint strength, ensuring your weld holds up under pressure. Remember, quality filler can save you from costly repairs down the line!
Aftercare, Inspection, and Advanced Tips for Truck Frame Welding
Here are crucial aftercare steps, inspection points, and expert tips to ensure your welded truck frame is sound.
Aftercare Tips
After finishing your welds, let the truck frame cool naturally—don’t quench it. Cooling with water can cause warping. Wire brush any freshly welded section, then apply at least 2 coats of anti-corrosion spray, like Rust-Oleum, to prevent rust.
Inspection
Inspect your welds visually. Look for signs of undercutting and check for keyhole effects along the bead. Use a calibrated gauge measuring at least 1.5 mm (0.06 In) to ensure weld depth and maintain quality and structural integrity. I trust the Weld Monitor 5000 for precision assessments.
Expert Tips
For seasoned welders, practice the “puddle technique” to maintain balanced heat distribution across thicker metal parts. Use preheating techniques for steel over 13 mm (0.5 In) to ensure proper penetration. Also, adjust your welding arcs to 90 amps for optimal control in critical areas like cross members. Understanding where to source your materials is also crucial for successful projects; discover options for buying metal for welding.
Why This is Worth It: Advantages
The biggest benefit of knowing how to weld a truck frame is durability. A solid, well-welded frame keeps your truck on the road longer and can withstand heavy loads.
Moreover, you’ll save money on repairs and maintenance. Plus, with welding skills, you’ll enjoy greater flexibility in customization, improved overall vehicle safety, and an increased resale value for your truck.
Applications Of Truck Frame Welding
I’ve known folks who use how to weld a truck frame for restoration projects, but it has many uses, such as:
- Loading Dock Repairs: Fixing heavy-duty support beams. Strong welds ensure the structure can bear weight, making it popular in logistics.
- Off-Road Enhancement: Reinforcing frames for off-roading. It’s vital for durability, especially in extreme conditions, and popular among enthusiasts.
- Fleet Maintenance: Businesses weld truck frames for fleet vehicles. Regular maintenance prolongs vehicle life, which is crucial for cost-saving.
- Custom Modifications: Welding custom frames for performance upgrades. Tailoring a frame improves vehicle handling and is common in racing.
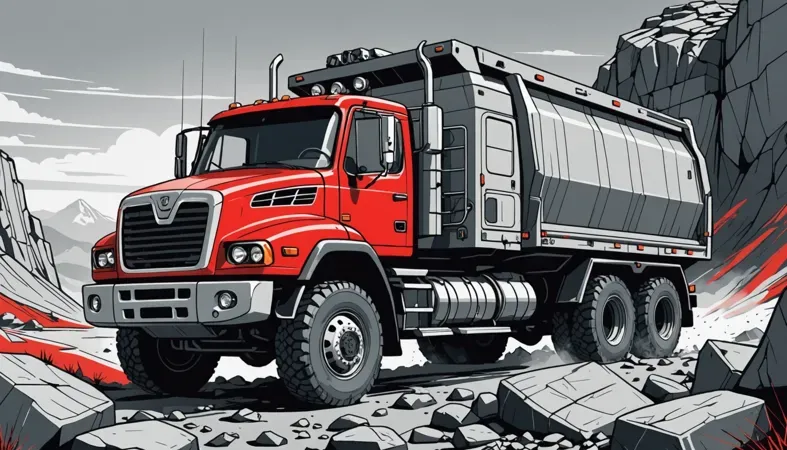
When to Try a Different Approach
Sometimes, you might not need to weld at all. Options like using a truck frame repair kit or bolting reinforcements could do the job just fine. For minor repairs, adhesives like epoxy resin can also work, especially if you want to avoid heat distortion.
As someone who’s been in the field for a while, I know that each method has its perks. For example, with bolted joints, you get easier disassembly down the line. Plus, it’s good to consider the legal weld truck frame rules; sometimes a clean, legal method is your best bet!
Frequently Asked Questions (FAQs)
Now let us look at some common questions I typically get asked.
What Kind Of Welder Do I Need to Weld a Truck Frame?
You need a MIG (Metal Inert Gas) welder to weld a truck frame. MIG welders are ideal for thick materials, like truck frames, because they can deliver high penetration and strong joints. Look for a welder with a power output of at least 180 amps, which gives flexibility for various thicknesses.
Can a Rusted Truck Frame Be Welded?
Yes, a rusted truck frame can be welded. However, you must clean the rust off first; otherwise, the weld won’t bond effectively. Using a wire brush or grinder can remove rust, making up to 80% of the seam stronger if prepared correctly.
Can You Stick Weld a Truck Frame?
Yes, you can stick weld a truck frame. Stick welding is suitable for thick materials and outdoor applications due to its versatility. However, MIG welding is generally preferred for truck frames because it provides cleaner beads and less post-weld cleanup.
What is the Best Welding Rod for a Truck Frame?
The best welding rod for a truck frame is E7018. This rod offers high tensile strength, adequate penetration, and a good finish. Using E7018 rods can result in welds that can withstand loads of at least 70,000 psi (Pounds Per Square Inch), which is essential for the integrity of the frame.
How Much Does It Cost to Weld a Truck Frame?
The cost to weld a truck frame typically ranges from $300 to $1500. The price depends on the extent of damage and local labor rates. For example, minor repairs may cost around $300, but extensive work might push expenses up to $1500 or more.
For more in-depth information and resources about welding techniques and practices, feel free to visit What is Welding.
Additional Reading
- Lincoln Electric. (2020). The Procedure Handbook of Arc Welding (15th ed.). Cleveland, OH: Lincoln Electric Company.
- Cary, H. B., & Helzer, S. C. (2005). Modern Welding Technology (6th ed.). Upper Saddle River, NJ: Pearson.
Tyler is a passionate DIY welder and self-taught metal artist with years of hands-on experience transforming raw materials into functional and artistic creations. Specializing in MIG welding, Tyler crafts everything from custom furniture to outdoor sculptures, blending creativity with technical skill. Committed to making welding accessible, Tyler shares practical insights and project inspiration to help beginners and hobbyists confidently explore the world of metalworking.
MIG Welding, Safety Tips, TIG Welding, Truck Frame, Welding, Welding Table, Welding Techniques, Welding Wire