How to Plastic Weld a Bumper? Essential Steps, Types, and FAQs
Published on: February 4, 2025 | Last modified: March 4, 2025
By: Joe Carter
Plastic welding a bumper is a process to repair plastic car bumpers. It joins broken plastic pieces using heat to restore their strength.
One question I was asked a lot is how to plastic weld a bumper. It’s crucial to know the steps, as doing it wrong can lead to a weak repair. In my experience, taking the time to learn the right method really pays off in the long run.
In this guide, we’ll cover how to weld a plastic bumper, types of plastic bumpers, steps for welding, factors affecting plastic welding, and frequently asked questions. If you’re eager to learn these details about how to plastic weld a bumper with a soldering iron, stick around. You’ll gain the knowledge you need to tackle this repair confidently.
Contents
How to Plastic Weld a Bumper?
To plastic weld a bumper means to join plastic parts using heat. To do this, heat the area to 260°C (500°F), apply a filler rod, and let it cool. It’s moderately easy and often used in automotive repairs.
What is Plastic Welding a Bumper?
Plastic welding a bumper involves using heat and a filler material to bond plastic parts, specifically car bumpers. Bumpers, typically made from thermoplastic materials like polypropylene, require precise temperatures—around 210°C (410°F). This process enables effective repairs and creates strong joints that restore functionality. The tensile strength of a well-welded bumper can reach 30 MPa (4350 Psi), providing durability comparable to new parts.
Plastic welding a bumper is straightforward but detailed. The key is to use the right heating equipment and filler, which can vary based on the bumper type. In my experience, taking time to prepare the surfaces really improves the strength of the weld.
When I worked on my friend’s cracked bumper, it was helpful for fixing his sports car’s aesthetics and functionality. Using a plastic bumper welding kit, I followed the technique for welding a plastic bumper, which saved us time and money. Seeing the joint hold up during stress tests after the repair was incredibly satisfying—showing just how effective proper plastic welding can be.
Types Of Plastic Weld Bumpers
Thermoplastic Bumpers
-
Thermoplastic bumpers are made from materials that can be re-melted. Use a plastic welding rod to join them. Heat both the rod and the bumper surface until they’re molten, then press them together.
-
Polyurethane Bumpers
Polyurethane bumpers are flexible. Use a specialized polyurethane welding kit for connections. Clean the surfaces, apply the welding adhesive, and use a heat source to fuse the components step by step.
-
Polypropylene Bumpers
Polypropylene is tough and requires a specific welding method. Use a soldering iron and a polypropylene welding rod. Melt the rod onto both surfaces and merge them once they’re heated.
-
Acrylic Bumpers
Acrylic bumpers provide a clear finish. Use a solvent-based adhesive for bonding. Apply the adhesive to the edges, press them together, and allow it to cure for a stronger hold.
What types of bumpers can you work with?
We have now covered the various types of plastic weld bumpers. Next, we’ll discuss common plastic welding techniques for bumpers.
Common Plastic Welding Techniques for Bumpers
Understanding different welding techniques can enhance your repair skills. Here are some common methods used for plastic welding bumpers.
Technique | Description | Best For | Temperature Range |
---|---|---|---|
Hot Air Welding | Involves using a hot air gun to melt both the plastic and a filler rod. | Thicker materials and larger repairs. | 350°F to 500°F (177°C to 260°C) |
Plastic Rod Welding | Uses a heated rod to melt the edges of the base plastic, fusing them together. | Small cracks or breaks. | 350°F to 420°F (177°C to 216°C) |
Ultrasonic Welding | Employs high-frequency vibrations to melt plastic without additional heat. | Intricate parts or plastics that are difficult to weld. | N/A (no direct heating) |
Laser Welding | Uses laser energy to melt the plastic directly, creating precise and strong joints. | Highly specialized applications. | Varies by material type. |
The right technique can make a big difference. Each method has its advantages, depending on what you need. Have you tried any of these methods before?
We covered various plastic welding techniques for bumpers. We will now cover the steps for welding a bumper.
Steps for Plastic Welding a Bumper
Now, we’ll cover the steps for properly plastic welding a bumper. Follow these closely for the best results.
-
Clean the Bumper Surface
Start by thoroughly cleaning the damaged area of the bumper. Use isopropyl alcohol (70% or Higher) to remove dirt and grease. A clean surface is crucial for a strong weld. Skipping this step can weaken the bond over time.
I once worked on a bumper without cleaning it first. The weld failed just a few weeks later! So trust me—don’t cut corners here.
-
Heat the Weld Area
Use a plastic welding gun set to about 450°F (232°C). This temperature allows for proper melting of the plastic. Move the heat source evenly across the area to avoid scorching. Keep it consistent for a strong joint. Eye safety is crucial in welding due to potential hazards, and you might find it helpful to explore welding’s effect on eyes.
If you’re using a soldering iron, use it only on the thin edges. Overheating might burn through, and then you’re really in trouble!
-
Prepare the Plastic Filler Rod
Select a plastic filler rod that matches your bumper material; polypropylene is common. Heat the rod slightly in the melted area until it softens. Insert the filler into the melted zone while keeping a steady hand to ensure it fuses with the existing plastic.
I made the mistake of using the wrong rod type once. The weld didn’t hold, and I had to redo everything. Always verify compatibility!
-
Apply the Weld
Apply the welding rod while simultaneously pushing it into the damaged area. This creates a strong fusion with the original material. Work steadily—don’t rush; take about 2 to 5 minutes depending on the repair size. Ensuring your workstation is properly set up can greatly improve the welding process, and it is important to know how high a welding table should be.
Maintain firm pressure to ensure the rod connects well with the bumper. If it gets too hot, let it cool a bit before adjusting. You’ll want even seams all around.
-
Cool and Trim the Welded Area
After completing the weld, let the area cool naturally for at least 10 minutes. Don’t rush or use water to cool it; this can lead to cracking. After cooling, check for excess filler and carefully trim to the original line with a utility knife. Different welding positions used in the process can significantly affect the outcome and quality of the weld. For an in-depth understanding of these positions and their implications, explore the various welding positions.
For a clean finish, sand down any rough edges. It’ll make your repair nearly invisible! Plus, you’re less likely to snag anything on your new weld.
We’ve wrapped up the steps for plastic welding a bumper here. Let us turn our attention to factors influencing the process.

Factors Affecting Plastic Welding a Bumper
What factors impact your ability to weld a plastic bumper effectively?
-
Material Compatibility
Different plastics require specific welding rods or techniques. For example, polypropylene (PP) and ABS mixed in bumpers need compatible fillers like PP or ABS rods for effective bonding.
-
Welding Temperature
Welding temperatures range from 350°F to 500°F (177°C to 260°C). Too hot can burn the plastic, while too cold leads to poor adhesion.
-
Technique Used
I once made a mistake by welding at the wrong angle. The technique is crucial—proper gun angle and speed can reduce warping, while the wrong method can create weak spots, especially with more delicate plastics like TPO.
-
Environmental Conditions
Humidity and temperature can affect your weld’s effectiveness. Optimal conditions are temperatures between 60°F and 80°F (15°C and 27°C) with low humidity for the best results.
-
Thickness Of Material
Thicker materials require higher temperatures and longer weld times, often needing more powerful equipment. A bumper’s thickness can vary from 1/8 inch (3.2 Mm) to 1/4 inch (6.4 Mm), impacting your choice of welding technique.
We covered the factors that influence plastic welding a bumper. We will now cover frequently asked questions.
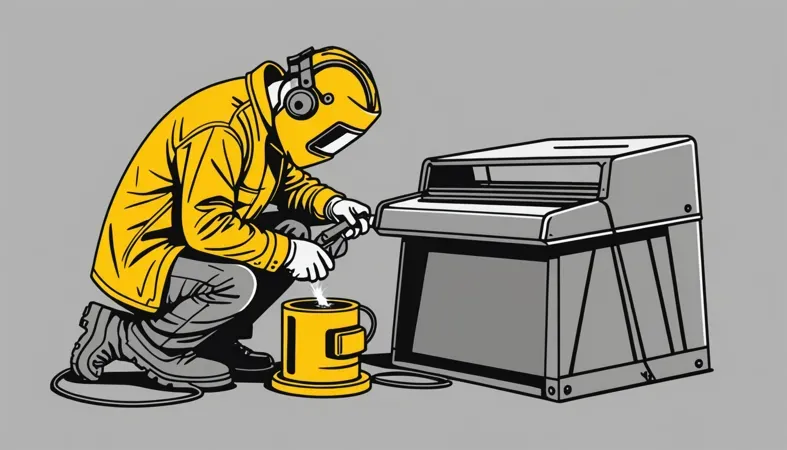
Frequently Asked Questions (FAQs)
Now let us look at some common questions I typically get asked.
Can a Plastic Bumper Be Welded?
Yes, a plastic bumper can be welded. Many modern bumpers are made from thermoplastic materials like polypropylene or ABS, which can be successfully joined using techniques like plastic welding. This method offers a strong bond and can restore your bumper’s original integrity.
How to Fix a Broken Plastic Bumper?
To fix a broken plastic bumper, you’ll want to use plastic welding techniques. This approach allows for a clean repair by melting the edges and fusing them together, thus providing a durable solution. Proper preparation and suitable materials can lead to a seamless finish.
How to Plastic Weld a Bumper Crack?
To plastic weld a bumper crack, start by cleaning the area. Then use a soldering iron or plastic welding tool to melt the crack edges together. This method minimizes visible lines and restores strength, often outperforming traditional adhesives.
How Much Does Plastic Bumper Welding Cost?
The cost of plastic bumper welding usually ranges from $100 to $300. Prices can depend on the damage extent and the technician’s expertise. Investing in a professional repair often pays off in the long run through added durability.
What Type Of Plastic is a Car Bumper Made Of?
A car bumper is mainly made of polypropylene (PP) or acrylonitrile butadiene styrene (ABS). These plastics are favored for their durability, lightweight nature, and ability to withstand impacts. Understanding this helps ensure you use the right welding technique.
Can You Weld Plastic With a Soldering Iron?
Yes, you can weld plastic with a soldering iron. This method involves using a hot tip to melt the edges of the plastic together. Though effective for minor repairs, applying proper technique is crucial for achieving a durable joint.
When discussing safety in welding practices, it’s essential to know that welding masks can also serve unique purposes. For instance, if you’ve ever wondered about safely viewing solar events, you might be interested in knowing more about using a welding mask to view an eclipse.
What’s the Best Method for Plastic Welding?
The best method for plastic welding depends on the type of plastic. Techniques include hot air welding, plastic rod welding, and ultrasonic welding. Evaluating your specific situation helps ensure a tailor-made approach for reliable plastic welding repair.
Conclusion
We covered how to plastic weld a bumper by discussing what plastic welding is, the different types of plastic bumpers, the steps for welding, and the factors that affect the process. We also tackled some frequently asked questions. By understanding these points—like choosing the right tools and methods—you’re better prepared.
In closing, learning how to plastic weld a bumper boils down to using the right equipment, like a soldering iron, and following the steps we covered. First, you clean and prepare the area, then heat and fuse the plastic properly. Feel free to reach out if you have further questions about how to plastic weld a bumper, as I’m here to help you get it right.
For additional insights and guidance on welding techniques, visit What is Welding.
References
- American Society of Mechanical Engineers. (2019). ASME Section IX: Welding and Brazing Qualifications. New York, NY: ASME.
- Kou, S. (2003). Welding Metallurgy (2nd ed.). Hoboken, NJ: Wiley.
Joe Carter is a retired welding professional with over 40 years of hands-on experience in the industry, spanning ship repair, structural welding, and even underwater projects. Joe is a master of MIG, TIG, and Stick welding. Passionate about mentoring the next generation of welders, Joe now shares his decades of expertise and practical insights to help others build rewarding careers in welding.
Art, Automotive Repair, Bumper Repair, Plastic Welding, Polypropylene, Protective Gear, Thermoplastic, Welding, Welding Table, Welding Techniques