How Much to Weld Exhaust Pipe? Costs, Steps, and Solutions
Published on: May 11, 2025 | Last modified: March 4, 2025
By: Joe Carter
An exhaust pipe is a vital part of your vehicle’s exhaust system. It directs harmful gases away from the engine and out the back of the car.
I’ve been asked many times about how much to weld exhaust pipe. It’s crucial to know because proper welding keeps your vehicle safe and running efficiently. From my experience, good welds can save you from future costly repairs and problems.
In this article, we’ll cover how to weld an exhaust pipe, types of exhaust pipes, important prerequisites, step-by-step welding procedures, safety precautions, different welding methods, factors affecting welding costs, common issues, and maintenance tips. You’ll also learn about the benefits of welding, various applications, and alternatives to welding an exhaust pipe.
Contents
- How Much to Weld Exhaust Pipe?
- What Are Exhaust Pipes?
- Types Of Exhaust Pipes
- Prerequisites
- Steps to Weld Exhaust Pipe
- Precautions
- Types Of Welding for Exhaust Pipes
- Factors Influencing Exhaust Pipe Welding Costs
- Tips for Cost-Effective Exhaust Pipe Welding
- Cost Breakdown for Different Exhaust Pipe Materials
- Common Issues and Troubleshooting
- Benefits Of Welding Exhaust Pipes
- Applications You Should Know About
- What Are the Alternatives to Welding Exhaust Pipe?
- Frequently Asked Questions (FAQs)
- Conclusion
- References
How Much to Weld Exhaust Pipe?
An exhaust pipe directs harmful gases away from your engine. To weld an exhaust pipe, expect costs between $50 to $200, depending on length and complexity. Difficult tasks typically arise in tight spaces or damaged pipes. Commonly welded in automotive repairs!
What Are Exhaust Pipes?
An exhaust pipe is a crucial part of a vehicle’s exhaust system. It channels exhaust gases away from the engine and out of the vehicle, preventing harmful emissions from entering the cabin. Typically made of stainless steel or mild steel, exhaust pipes can withstand high temperatures, often exceeding 260°C (500°F). They usually have a diameter of about 50 to 76 mm (2 to 3 Inches), with variations based on vehicle specifications.
When considering the cost to weld an exhaust pipe, it depends on factors like location and job complexity. In my experience, prices typically range from $50 to $150 for a simple exhaust pipe weld. Keep in mind that if the job requires extra parts or modifications, costs can increase quickly.
I used exhaust welding frequently in my job, especially to fix a friend’s older car. He had a leaking exhaust pipe that needed some TLC. I often wonder, how long will a welded exhaust last? From what I’ve seen, a good weld can secure the pipe for years, sometimes lasting until you’re ready for a new car! Investing in exhaust welding is smart for extending vehicle life.
Types Of Exhaust Pipes
So, what types of exhaust pipes will you deal with when considering welding costs? Here’s a quick rundown:
-
Stainless Steel Exhaust Pipes
Stainless steel pipes are durable and resist corrosion. Welding these pipes costs around $100 to $300, depending on length and location. Clean the area, use a TIG welder with a 316L filler rod, and make multiple passes for strength. Ensuring the proper height when setting up your workstation can enhance precision and comfort, and you might find it useful to know how high should a welding table be.
-
Aluminized Steel Exhaust Pipes
These pipes are coated with aluminum for better protection. Welding typically costs between $75 and $200. To weld aluminized steel, saw the pipe to size, remove the coating where you’ll weld, and use MIG welding to join the edges.
-
Carbon Steel Exhaust Pipes
Carbon steel is strong and cost-effective. Welding can set you back around $60 to $150. Grind the edges to remove rust, preheat the pipe if it’s thick, and use a stick welder with E6013 electrodes. Mastering skills is essential when tackling challenging positions, and you can gain insights on how to weld upside down.
-
Polymeric Exhaust Pipes
These lightweight pipes are gaining popularity in some applications. Welding costs range from $50 to $120. Use a plastic welding tool, heat the plastic edges, and carefully fuse them for a solid joint.
-
Diameter-optimized Exhaust Pipes
These pipes are designed for specific engine sizes, enhancing performance. Welding costs can be around $80 to $250. Measure the diameter, cut the pipe precisely, and consult a professional familiar with various welding techniques for proper attachment. If you’re interested in solar phenomena and how welding gear can provide protection, explore if it’s safe to view an eclipse with a welding mask.
We’ve wrapped up the different types of exhaust pipes here. Next up, we’ll look at the necessary prerequisites.
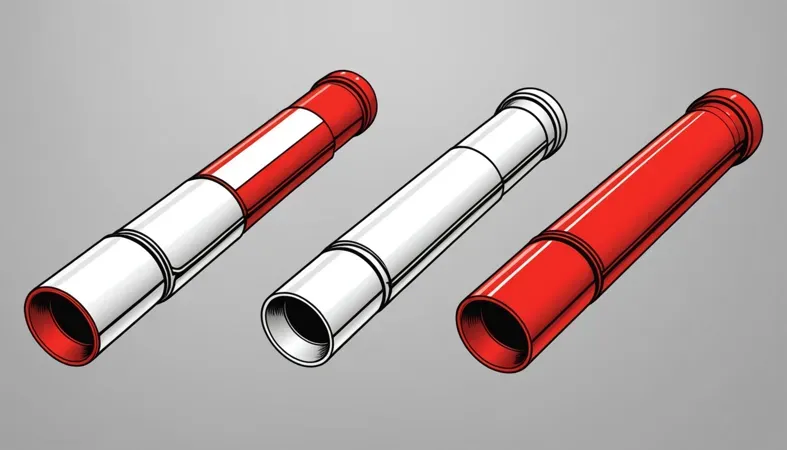
Prerequisites
What do you need before starting the welding process for an exhaust pipe?
- MIG Welder: You need a quality MIG welder, like the Lincoln Electric Power MIG 210 MP. It’s crucial for clean, strong welds on exhaust materials.
- Exhaust Pipe Material: You’ll need the specific pipe, such as a 2.5-inch (63.5 Mm) aluminized steel pipe. Proper materials ensure durability and fit.
- Welding Wire: Use ER70S-6 MIG welding wire, 0.030 inches (0.8 Mm). This wire is ideal for exhaust pipe metals, providing optimal bonding.
- Welding Gas: Get a bottle of a 75% Argon / 25% CO2 mix. This gas blend offers excellent shielding to prevent weld contamination.
We’ve wrapped up the necessary prerequisites here. Next up, we’ll look at the process for welding an exhaust pipe.
Steps to Weld Exhaust Pipe
Here are the steps to effectively weld exhaust pipes along with cost factors.
-
Prepare the Exhaust Pipe
Start by cleaning the area where you’ll weld. Use a wire brush or grinder to remove rust, dirt, and debris. This step ensures solid contact. A clean surface leads to a stronger weld, saving you money on future repairs. Mastering the technique of welding pipe with a 6010 electrode is crucial for achieving reliable results, and you can explore more about how to weld pipe with 6010.
Measure the cut areas accurately. You’ll want 1-2 inches (2.54-5.08 Cm) of clean surface to connect your pipes. I once overlooked this, which led to a weak joint and extra rework costs!
-
Set Up the Welding Machine
Choose the right welding process for exhaust pipes—MIG is popular. Set your machine to a voltage between 16-22 volts (V) and an appropriate wire feed speed, typically 150-250 inches (381-635 Cm) per minute. Proper settings greatly affect weld quality.
Use .030 inches (0.76 Mm) diameter wire for mild steel. This wire size ensures better penetration for thinner exhaust materials. Adjust flow rates: 10-20 cubic feet per hour (CFH) of shielding gas is ideal.
-
Execute the Welding Process
Begin welding at the junction with a steady hand. Maintain a distance of about 1/8 inch (0.32 Cm) from the surface. Move evenly along the seam. Aim for a consistent pace to create smooth, even beads. Understanding the differences between various welding positions such as 1F, 2F, 3F, and 4F can greatly enhance your welding skills. For more information, explore the types of welding positions.
I once made the mistake of speeding up too much, causing undercuts. A good rule of thumb is to let the welder guide you. Don’t rush; quality work saves costs in the long run.
-
Perform Quality Checks
After welding, visually inspect the bead. Look for any gaps or undercuts. Ensure the weld is flush and consistent. You’re looking for good penetration for strength.
Run a pressure test if possible. Use air or a soapy water solution to check for leaks. Sealing leaks early can prevent headaches later and ensure everything functions smoothly.
So far we covered how to weld an exhaust pipe. Next, let’s look at essential safety measures to take.
Precautions
Here are essential precautions for welding your exhaust pipe.
- Proper Ventilation: Always work in a well-ventilated area to avoid harmful fumes. Consider using a vent fan like the iPower 4” fan.
- Appropriate PPE: Wear gloves, goggles, and flame-resistant clothing. Quality options include Lincoln Electric welding gloves. They’ll protect against burns and toxic exposure.
- Check Material Integrity: Inspect the exhaust for oil or rust before welding to ensure a strong joint. Use cleaning solvents to prepare surfaces as needed.
- Secure Workspace: Keep your work area tidy and tools organized to prevent accidents. I recommend the Husky tool organizer for better safety.
Following these precautions ensures your safety while welding. I always prioritize safety for peace of mind.
We covered precautions for welding exhaust pipes. Next, we will cover the various types of welding suitable for this task.
Types Of Welding for Exhaust Pipes
Let’s explore the various welding methods: MIG, TIG, Stick, Flux-Cored, and Gas welding.
-
MIG Welding
MIG (Metal Inert Gas) welding is quick and user-friendly. It uses a continuous wire feed to melt and join metal parts. For exhaust pipes, expect to pay around $50 to $150 for welding services, typically for materials with a thickness of 1/16 inch (1.59 Mm) to 1/4 inch (6.35 Mm). Many automotive professionals rely on this technique extensively, showcasing its importance in automotive welding.
Ensuring a proper setup, such as learning how to ground a welder, is crucial for safe and effective welding operations.
-
TIG Welding
TIG (Tungsten Inert Gas) welding is precise and produces high-quality welds, making it ideal for thinner materials like exhaust pipes. Costs range from $80 to $200, depending on the job’s complexity, typically for pipes of 1/8 inch (3.18 Mm) thickness or less.
-
Stick Welding
Stick welding, or Shielded Metal Arc Welding (SMAW), is versatile and effective, suitable for outdoor conditions and rusty surfaces. You might pay about $40 to $100 for stick welding an exhaust pipe, often joining materials around 1/8 inch to 1/2 inch (12.7 Mm) thick.
-
Flux-cored Welding
Flux-Cored Arc Welding (FCAW) is similar to MIG but uses a tubular wire filled with flux. This method provides strong welds in various positions. Expect costs of $50 to $120, typically for thicker exhaust materials, usually 1/8 inch (3.18 Mm) and above.
-
Gas Welding
Gas welding uses a flame fueled by acetylene and oxygen. While it’s not the most common method for exhaust pipes, it’s still useful for repairs. If you’re considering gas welding, you might pay about $60 to $150, depending on pipe thickness and length.
Factors Influencing Exhaust Pipe Welding Costs
What factors determine your expenses for welding an exhaust pipe?
-
Material Type
Different materials require unique welding processes. Stainless steel (SS304) costs about $0.50 per inch, while mild steel is around $0.20 per inch. Choose wisely!
-
Labor Costs
Skilled labor significantly affects your total expenses. Rates range from $50 to $150 per hour, depending on your location and the technician’s experience.
-
Welding Method
I once mistakenly chose MIG welding for a stainless exhaust. Different methods impact strength and cost. TIG welding, for instance, is cleaner but pricier, averaging $100 per job.
-
Pipe Complexity
Simple bends cost less than intricate designs. For example, a straightforward weld may take 30 minutes, while complex shapes could require 2 hours, doubling costs!
-
Location
The location of the work affects prices too. Urban areas generally have higher rates; expect to pay $20 to $50 more than in rural areas.
Tips for Cost-Effective Exhaust Pipe Welding
Want to save some cash while getting your exhaust pipe welded? Here are some expert tips to keep costs down.
-
DIY Welding
If you have the skills, welding your exhaust pipe yourself can save you a bundle. You could cut costs from $50 upwards, depending on whether you already have equipment.
-
Shop Around
Rates can vary significantly. Get quotes from different welders. You might find prices range from $50 to $200, so looking around could save you $40 or more.
-
Material Choices
Consider using mild steel instead of more expensive materials, like stainless steel. For example, mild steel costs about $0.20 per inch, while stainless can be $0.50 per inch. It’s a smart move if you’re on a budget.
-
Combine Jobs
If your vehicle needs multiple repairs, combine welding jobs. You might save on labor costs this way—get several pipes done together, reducing downtime and expenses!
-
Choose Off-Peak Hours
Some shops offer discounts for work done during less busy hours. Booking on a weekday morning rather than a weekend could save you 10-20% off your total.
Cost Breakdown for Different Exhaust Pipe Materials
Material Type | Cost per Inch (USD) | Typical Pipe Thickness (Inches) | Estimated Total Cost (for 5 feet) |
---|---|---|---|
Mild Steel | $0.20 | 0.035 – 0.062 | $120 |
Stainless Steel | $0.50 | 0.030 – 0.065 | $300 |
Aluminized Steel | $0.30 | 0.030 – 0.100 | $180 |
Polymeric | $0.40 | 0.100 – 0.125 | $240 |
Common Issues and Troubleshooting
Let’s look at specific technical problems with the exhaust pipe.
-
Leaks in Weld Joints
Leaks in the exhaust pipe’s weld joints can release harmful gases. To identify them, listen for hissing sounds or use a soap solution to find bubbles. Fix leaks by re-welding with adequate heat (Around 400°F or 204°C) or applying a suitable sealant.
-
Inconsistent Weld Beads
Inconsistent weld beads on the exhaust pipe can add stress. I’ve made this mistake before; always maintain a steady travel speed of 4-10 inches per minute for even beads. Check for width and uniformity. If necessary, grind and re-weld damaged areas.
-
Rust Formation
Rust on the exhaust pipe indicates exposure to moisture and air. Look for flaky surface corrosion. Sand down rust and apply high-temperature paint to protect joints. A typical exhaust lasts about 5 years with proper maintenance.
-
Heat-affected Zone Problems
The heat-affected zone (HAZ) on the exhaust pipe can weaken its structure. Watch for discoloration or deformation at joint edges. Reducing heat input during welding (Less Than 300°F or 149°C) can help maintain strength. Monitor this area closely.
-
Poor Fit-up Of Exhaust Components
Poorly fitting exhaust pipe components lead to misalignment, causing noise and vibration. Ensure components fit snugly; gaps over 1/16 inch (1.6 Mm) can cause issues. Make adjustments or use a pipe expander for a precise fit.
Benefits Of Welding Exhaust Pipes
The main advantage of welding exhaust pipes is the strength it provides. I used it frequently for my job, especially to ensure joints stay tight and minimize leaks.
Welding also offers durability, enhanced performance, and reliability. It creates a seamless connection, reduces the risk of rust, and effectively handles high temperatures.
Applications You Should Know About
I’ve seen people use welding techniques for exhaust pipes in various projects. It has many applications, such as:
- Custom Exhaust Systems: Builders often fabricate custom exhausts for performance cars, enhancing airflow and sound. This is popular among car enthusiasts.
- Repair Work: Many weld exhaust pipes in older vehicles to fix rust or holes. This saves money compared to replacing the entire system and is commonly done in garages.
- Heavy Machinery Exhausts: Industries weld high-temperature exhaust pipes on construction equipment, ensuring durability and safety, which is critical for machine longevity.
- Marine Applications: Boaters occasionally weld exhaust systems on ships. These pipes must withstand corrosion, making skilled welding essential.
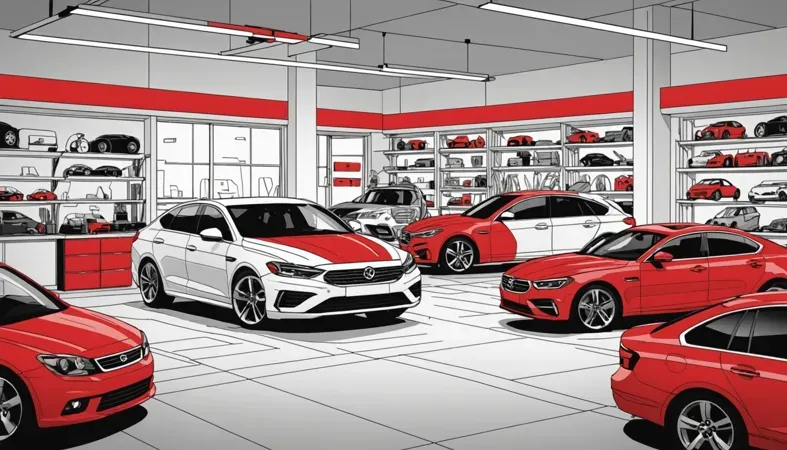
What Are the Alternatives to Welding Exhaust Pipe?
When welding isn’t an option, you’ve got a few alternatives. You could use stainless steel MIG clamps, such as those from Spectre Performance, which offer a solid seal without the heat. Another choice is exhaust adhesive, like Permatex Ultra Copper, which can hold up under high temperatures, making it ideal for quick fixes.
If there’s one thing I’ve gained from my journey, it’s that sometimes sticking and sealing can be just as effective. These methods are often quicker and less messy than welding, especially if you need an urgent repair. Knowing these options can save you time and keep your exhaust secure.
Frequently Asked Questions (FAQs)
Now let us look at some common questions I typically get asked about welding exhaust pipes.
Can a Broken Exhaust Pipe Be Welded?
Yes, a broken exhaust pipe can be welded. Welding creates a strong bond that can restore structural integrity and function to the pipe. Depending on the type of exhaust material and condition, this repair can last several years and costs around $50 to $150.
How Much Does It Cost to Have a Muffler Welded in?
The cost to have a muffler welded in typically ranges from $80 to $200. This cost includes labor and materials. The price may vary based on the make and model of your vehicle and your location.
How Long Does It Take to Weld an Exhaust?
Welding an exhaust usually takes around 1 to 2 hours. The duration depends on the extent of the damage and the complexity of the job. A quick fix might take just 30 minutes, while more extensive repairs could take longer.
How Much to Weld a Hole in Exhaust?
The cost to weld a hole in an exhaust usually falls between $50 and $100. This price reflects the materials and labor involved. Timely repairs can help prevent bigger exhaust system issues and keep your car running efficiently.
How Much Does It Cost to Weld a Pipe Together?
The cost to weld a pipe together generally ranges from $70 to $150, depending on the size and type of the pipe. Factors such as labor costs and accessibility may also affect the overall price.
Conclusion
We are almost done. We covered exhaust pipes, their types, necessary prerequisites, and steps to weld them. We also discussed precautions, types of welding, factors influencing costs, common issues, and benefits of welding.
So, how much to weld exhaust pipe? You can expect to spend anywhere from $50 to $150 based on labor and materials involved. If you consider factors like the type of weld, length of the pipe, and the service location, those details can help you gauge your costs more accurately.
For further insights and invaluable knowledge on welding techniques, tips, and best practices, visit What is Welding.
References
- American Society of Mechanical Engineers. (2019). ASME Section IX: Welding and Brazing Qualifications. New York, NY: ASME.
- American Society of Mechanical Engineers. (2019). ASME Section IX: Welding and Brazing Qualifications. New York, NY: ASME.
Joe Carter is a retired welding professional with over 40 years of hands-on experience in the industry, spanning ship repair, structural welding, and even underwater projects. Joe is a master of MIG, TIG, and Stick welding. Passionate about mentoring the next generation of welders, Joe now shares his decades of expertise and practical insights to help others build rewarding careers in welding.
6010 Electrode, Automotive Welding, Exhaust Pipe Repair, Exhaust System Maintenance, Vehicle Safety, Welding, Welding Costs, Welding Table, Welding Techniques, Welding Wire