Can You Weld A36 to A500? Understanding Techniques and Precautions
Published on: May 8, 2025 | Last modified: March 4, 2025
By: Joe Carter
A36 is a common structural steel grade used in various applications. It’s known for its ability to withstand stress and is often used in construction and manufacturing.
So, if you are wondering can you weld a36 to a500, it’s crucial to understand why proper techniques matter. I’ve seen firsthand how improper welding can lead to structural failures, risking safety and costs. Following the right methods ensures strong, reliable joints.
In this article, we’re diving into the details on can you weld a36 to a500. We’ll discuss the types of A36, their weldability, necessary prerequisites, welding steps, precautions, techniques, and factors affecting weldability. Also, we’ll cover common troubleshooting issues, aftercare, and why this knowledge is beneficial in industry applications. Plus, can carbon steel be welded? Let’s find out!
Contents
- Can You Weld A36 to A500?
- What is A36?
- Types Of A36 and Their Weldability
- Material Compatibility: A36 & A500
- Prerequisites
- Steps for Welding A36 to A500
- Precautions
- Types Of Welding Techniques for A36 to A500
- Factors Affecting Weldability Of A36 to A500
- Common Issues and Troubleshooting
- Aftercare, Inspection, and Advanced Tips for A36 to A500
- Why This is Worth It: Advantages
- Industry Applications for A36 to A500 Welding
- Are There Any Alternatives to Welding A36 to A500?
- Frequently Asked Questions (FAQs)
- Conclusion
- References
Can You Weld A36 to A500?
Yes, you can weld A36 to A500. It’s fairly easy due to both being low-carbon steel. Use E7018 electrode for a strong joint. Ensure proper fit-up and clean the surfaces for best results.
What is A36?
A36 is a carbon structural steel grade commonly used in construction and manufacturing. It conforms to ASTM A36/A36M standards and has a minimum yield strength of 36,000 psi (248.2 Mpa). This grade is known for its excellent weldability and machinability. It mainly consists of iron, with a carbon content up to 0.26 percent, ensuring easy fabrication.
Can you weld A36 to A500? This question often arises in my projects. In my experience, A36, used in structural applications, interacts well with A500, but you need to consider the specifics of the materials involved.
I once used A36 to build a frame for a storage unit. Its properties made the welding process smoother since A36 shares traits with specialized carbon steels like A500. General welding techniques apply here and can also be used with other carbon steels. Ensure compatibility when asking, “Can A36 be welded to high-tensile steel?” Understanding the properties of both materials is crucial for a strong weld!
Types Of A36 and Their Weldability
What types of A36 can you use in welding projects?
-
Hot Rolled A36 Steel Plates
Hot rolled A36 plates are thick, reliable sheets used in construction. You can easily weld these plates to A500 steel. For a strong weld, use E7018 or E6013 electrodes and preheat the plates to about 60°C (140°F). B-pressure welding techniques ensure welds meet critical strength requirements, especially in high-pressure environments, highlighting what is B-pressure welding.
-
Cold Rolled A36 Steel Sheets
Cold rolled A36 sheets are thinner with a smooth finish. You can also weld these sheets to A500 steel. Clean the edges, use a MIG welder with solid wire, and maintain a travel speed to prevent warping.
-
A36 Steel Angles
A36 angles have an L-shape, enhancing structural support. You can stick weld A36 angles to A500 steel. Prepare the joint, use an E6011 or E6013 rod, and maintain good arc control during welding. To achieve precise connections in your projects, understanding how to weld 45-degree angles can be crucial.
-
A36 Steel Channels
A36 channels are shaped like a ‘C’ and provide strength in various applications. You can weld A36 channels to A500 steel, provided you preheat them slightly. Use E7018 electrodes and allow time for cooling to improve the weld.
-
A36 Steel Beams
A36 beams are I-shaped and excellent for heavy loads. Achieve a solid weld between A36 beams and A500 steel by ensuring the ends are clean and beveled, and using a backing bar to maintain penetration and strength.
We have now covered the types of A36 and their weldability. Next, we will examine material compatibility between A36 and A500.
Material Compatibility: A36 & A500
Understanding the compatibility of A36 and A500 can enhance your welding results. Here’s a detailed comparison that can guide your choices.
Property | A36 | A500 |
---|---|---|
Yield Strength | 250 MPa (36 Ksi) | Varies by grade; from 220 MPa (32 Ksi) to 500 MPa (72.5 Ksi) |
Average Carbon Content | 0.25% max | 0.26% to 0.30% |
Applications | Construction, manufacturing | Structural tubing, frames |
Weldability | Excellent | Good |
Fatigue Resistance | Moderate | Higher due to design |
Understanding these properties helps you decide the right welding process. For instance, A500’s yield strength can accommodate significant loads, making joints between these grades reliable in various structures. The right filler material and technique will ensure strong welds.
We’ve wrapped up material compatibility between A36 and A500 here. Next up, we’ll look at prerequisites.
Prerequisites
What do you need to start welding A36 to A500?
- MIG Welder: You’ll need a MIG welder, like the Lincoln Electric POWER MIG 210 MP. It’s essential for consistent heat and penetration when welding these steel types.
- Welding Wire: Use ER70S-6 welding wire, specifically 0.030 in (0.8 Mm) in diameter. It’s ideal for A36 and A500 due to its excellent arc stability and low spatter.
- Welding Gas: An argon-CO2 mix (75-25) is required. This blend prevents oxidation and ensures a cleaner weld on carbon steels.
- Welding Rod: If you’re using stick welding, choose E7018 rods, specifically 3/32 in (2.4 Mm). They provide a strong weld bead, crucial for structural integrity.
- Rectangle Steel Blocks: Use at least 2 in x 4 in x 1/4 in (51 Mm X 102 Mm X 6 Mm) steel blocks to secure your workpiece and maintain alignment.
You should now have a good understanding of the necessary prerequisites for welding. In the next part, we’ll discuss the steps for welding A36 to A500.
Steps for Welding A36 to A500
Here are the steps for successfully welding A36 steel to A500 steel.
-
Clean the Base Metals
Start by cleaning both A36 and A500 steel surfaces. Remove rust, oil, and dirt using solvents or a wire brush. A clean surface prevents contamination during welding, which is crucial for the integrity of the joint. Even small particles can lead to weak welds, emphasizing the importance of proper steel welding.
When welding on a vehicle, it is essential to disconnect specific components to protect the vehicle’s electronics. To understand which systems need to be temporarily disconnected, consult the guidelines on what to disconnect when welding.
I recommend using a grinder for a quicker and more effective finish. Wipe down with a clean, dry cloth to avoid moisture. This step is crucial for strong weld integrity.
-
Preheat the Metals
Next, preheat both metals to a temperature between 150°C and 200°C (300°F to 400°F). Preheating reduces the risk of cracking from thermal shock. Consistent heat across the weld area ensures better fusion, especially with A500, which may have higher carbon content. Awareness of potential hazards like eye discomfort from intense ultraviolet light is essential, especially in welding environments where radiated light exposure is high, as welding can hurt your eyes.
Use a temperature gun for accuracy. Not preheating or failing to reach the right temperature can lead to issues. Keep an eye on that heat—your weld will thank you!
-
Choose the Right Filler Metal
Select a filler metal compatible with both materials. ER70S-6 is a good choice as it works well with A36 and A500. Look for a wire diameter of 0.8 mm (0.030 Inches) for MIG welding or 2.4 mm (3/32 Inches) for TIG welding. The right filler makes a significant difference in weld efficiency.
Matching filler material helps prevent dilution issues. Using the wrong filler can lead to porosity and ruin your welds. Knowledge of your materials is key!
-
Establish Welding Parameters
Set your welding machine to the correct amperage. A good range for MIG is around 200 to 220 A, while for TIG, it’s between 100 to 150 A, depending on thickness. Adjust voltage and wire feed speed accordingly. Testing on scrap metal helps fine-tune settings.
Pay attention to travel speed; usually around 300 mm/min (12 In/min) works well. If you travel too fast, you’ll get incomplete fusion. Tweaking these parameters has made my welding much smoother.
-
Welding Technique
Use the stringer bead technique for better penetration. Maintain a steady travel angle of around 10 to 15 degrees for solid results. Move smoothly to avoid inconsistencies in the bead. Going too slowly can lead to excessive heat input, which is a recipe for disaster.
Consistent technique is important while welding. I tend to pull the weld rather than push for better control. Mastering this step can turn a mediocre joint into a perfect one!
That covers the steps for welding A36 to A500. Let’s now take a look at safety measures and warnings.
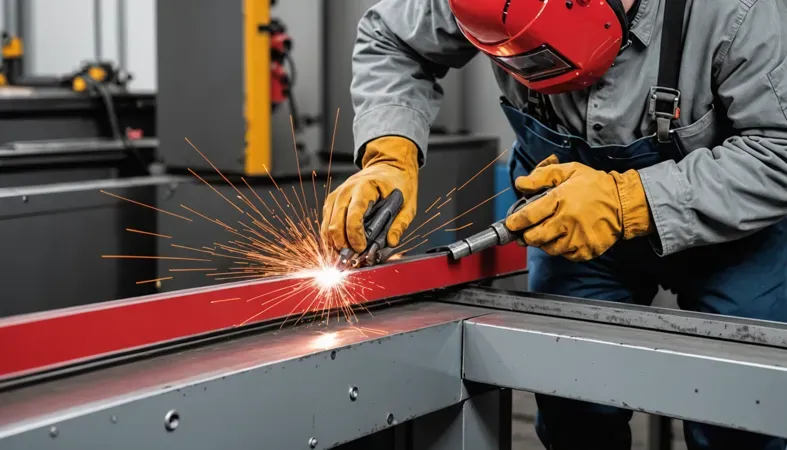
Precautions
Let’s quickly cover the essential safety measures for welding A36 to A500.
- Wear Protective Gear: Use a quality welding helmet, like the Lincoln Viking 3350, to protect your face and eyes. Proper gear prevents burns and injuries.
- Ventilate the Area: Ensure good airflow when welding to keep harmful fumes away. Use fans or welding hoods to enhance ventilation by up to 90%.
- Check for Flammable Materials: Keep flammable materials at least 35 feet (10.67 Meters) from your work area to avoid fire hazards. This is crucial for fire safety.
- Inspect Equipment: Always check cables and machines before use. Look for wear on cables that could cause electric shocks or short circuits.
Always prioritize safety when welding—it just makes sense!
Types Of Welding Techniques for A36 to A500
Let’s explore various welding techniques: MIG, TIG, Stick, Flux-Cored Arc, and Submerged Arc Welding.
-
MIG Welding
MIG (Metal Inert Gas) welding is a fast method using a continuous wire feed. It’s ideal for welding thin to medium sections of A36 and A500 steel, which are commonly used metals in various industries. With a voltage range of 16 to 30 volts, MIG offers excellent penetration and speed, making it a popular choice for those who need a reliable welding technique. For more insights on different types, understanding welding by metals can be quite helpful.
-
TIG Welding
TIG (Tungsten Inert Gas) welding uses a non-consumable tungsten electrode. It provides precise control, making it perfect for various steels, including A36 and A500. You can achieve welds up to 1/4 inch (6 Mm) thick.
-
Stick Welding
Stick welding, or SMAW (Shielded Metal Arc Welding), uses a consumable electrode. It’s versatile for thick sections of A36 and is effective outdoors. Currents range from 40 to 300 amps, making it ideal for strong welds. Proper equipment setup ensures safety and effectiveness in welding, especially when learning how to adjust welding helmet.
-
Flux-cored Arc Welding
Flux-Cored Arc Welding (FCAW) is suitable for thicker A36 and A500 sections. It resembles MIG but uses a hollow wire filled with flux. It can handle welds up to 1 inch (25 Mm) thick, making it robust for heavy tasks. When working with delicate components such as gas tanks, it is crucial to apply proper welding techniques to ensure safety and integrity. Learn how to effectively weld a gas tank.
-
Submerged Arc Welding
Submerged Arc Welding (SAW) is perfect for heavy steel items like A500. This process is highly efficient, with welding speeds over 1 inch (25 Mm) per minute. It produces high-quality welds, excellent for thick materials.
Factors Affecting Weldability Of A36 to A500
What factors influence your ability to join A36 and A500 materials effectively?
-
Material Thickness
Thickness significantly affects weldability. A36 ranges from 1/8” to 8” (3.175 Mm to 203.2 Mm). As thickness increases, you’ll need to adjust your welding approach.
-
Welding Procedures
The method you choose matters. Processes like MIG (Metal Inert Gas) or TIG (Tungsten Inert Gas) affect how you control heat and filler materials.
-
Heat Input
Excessive heat can warp materials, while insufficient heat may create weak joints. I recommend keeping heat input below 1.1 kJ/mm (27.5 Kj/in) for optimal results.
-
Welding Position
Welding position influences weld pool behavior. Whether you’re welding flat or vertical, adapt your technique for a clean weld.
-
Electrical Parameters
Set voltage and amperage accurately. Typically, a voltage of 24-26 volts and an amperage of about 140-180 amps work well for A36.
Common Issues and Troubleshooting
Let’s look at specific issues you might face with A36 steel.
-
Inconsistent Weld Quality
A36 can show inconsistent weld quality due to improper heat settings. Check your welder; it should be set to 170-190 A for SMAW. Adjust the travel speed for better consistency.
-
Warping or Distortion
A36 can warp if you apply too much heat. To reduce distortion, use tacks before full welding. Also, work on a flat surface.
-
Poor Penetration
A36 may have poor penetration if you work too fast or use the wrong electrode. Use a 7018 rod for better penetration at a speed of 10-12 inches (25-30 Cm) per minute.
-
Cracking After Welding
A36 can crack due to fast cooling or residual stresses. Prevent this by preheating to about 150°F (65°C) and maintaining a controlled cooling rate.
-
Porosity in Welds
A36 welding may cause porosity from contaminants. Keep your joint clean—free from rust and oil. Use a wire brush and inspect in good light.
Aftercare, Inspection, and Advanced Tips for A36 to A500
Here’s some insight on post-weld care, quality checks, and advice for welding A36 to A500.
Aftercare Tips
After you combine A36 and A500, control the cooling rate. Avoid rapid temperature changes; keep it above ambient for at least 2 hours post-weld. Passive cooling (Natural Cooling) ensures integrity remains solid; that’s essential!
Inspection
Inspection starts by checking the fusion zone. Look for voids or undercuts—measure gaps less than 1 mm. Use a profile gauge or a simple caliper like the Mitutoyo for precise readings. In my experience, this method reduces rework.
Expert Tips
For experts, consider adjusting preheat temperatures; applying 150°C (302°F) on the A36 side can enhance strength. Pay attention to interpass temperatures—keep them between 60-150°C (140-302°F) to avoid cooling cracks. For filler materials, use E7018 electrodes for strong fusion in challenging conditions!
Why This is Worth It: Advantages
The main benefit of welding A36 to A500 is strength. I once used it for a structural project, and the results were fantastic.
You also gain advantages like easy availability, strong weld integrity, cost-effectiveness, and versatility. These factors make this combination a top choice for many welding applications!
Industry Applications for A36 to A500 Welding
I’ve seen A36 to A500 welding used in critical structures. However, it has many applications, such as:
- Structural Frames: Ideal for commercial buildings, factories, and bridges. It’s popular for its strength and durability.
- Prefabricated Parts: Used in pre-engineered buildings. It’s essential for fast assembly and structural integrity.
- Heavy Equipment Manufacturing: Utilized in creating machinery and frames. Its toughness makes it a favorite for high-stress applications.
- Pipeline Construction: Welded for safe material transfer. It’s chosen for its reliability and ability to withstand pressure.
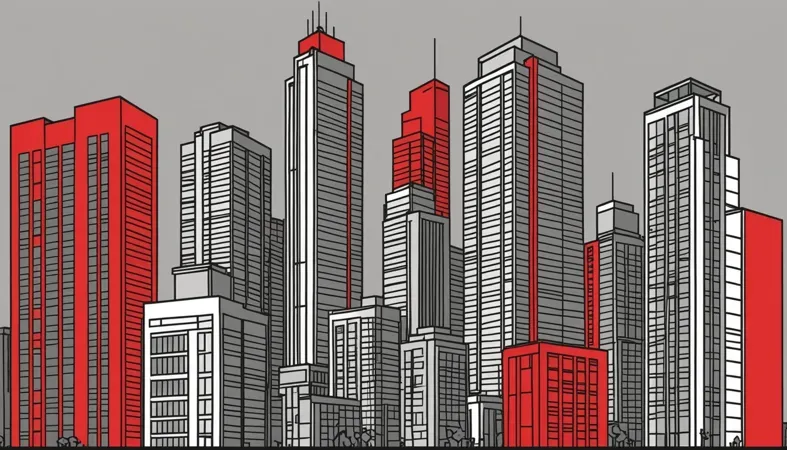
Are There Any Alternatives to Welding A36 to A500?
One alternative is mechanical fastening, like using bolts or rivets. This method provides strong joints without the heat! Products like Grade 8 bolts are perfect for this and prevent any welding distress in the metals.
Another option is adhesive bonding. It’s especially useful when dealing with sensitive materials. Reflecting on my past experiences, it’s clear that industrial-strength adhesives, such as epoxy, bond dissimilar metals remarkably well and offer excellent durability.
Frequently Asked Questions (FAQs)
Now let us look at the questions I typically get asked.
Are A36 and A500 the Same?
No, A36 and A500 are not the same. A36 is a structural steel, while A500 is a tubing specification for cold-formed steel. A36 has a yield strength of 250 MPa (36 Ksi) and A500 varies based on grade, ranging from 220 MPa (32 Ksi) upwards. Understanding this helps in choosing the right material for your projects.
Can You Weld Two Different Grades Of Steel Together?
Yes, you can weld two different grades of steel together. However, it’s vital to ensure compatibility of the base materials to avoid issues during or after the welding process. Different grades may also require adjustments in welding techniques to maintain strength in the weld joint.
Is ASTM A36 Weldable?
Yes, ASTM A36 is a weldable material. It allows for various welding methods, like MIG and TIG, with minimal preheat or post-weld treatment required. A36’s properties help prevent cracking, making it excellent for welded structures.
Can You Weld A36 to 304 Stainless Steel?
Yes, you can weld A36 to 304 stainless steel. You must use the appropriate filler material to accommodate differences in thermal expansion and composition. This ensures a strong joint, though be mindful of potential corrosion issues over time.
Throughout the welding process, issues such as porosity can arise if proper techniques aren’t followed. For a better understanding of what causes porosity in welding, it’s important to consider factors like contamination and gas entrapment.
Can You Weld Carbon Steel?
Yes, you can weld carbon steel. It’s versatile and works well with various welding techniques like stick and MIG welding. Proper preparation and technique are key factors for achieving strong welded joints when working with carbon steels.
Can High Tensile Steel Be Welded?
Yes, high tensile steel can be welded, but it poses challenges. You may need to preheat this steel to prevent cracking, especially when thickness exceeds 12 mm (0.5 In). Following specific welding procedures is crucial to maintaining strength in the final product.
Conclusion
We covered various topics on welding A36 to A500, including definitions, types of A36 and their weldability, prerequisites, and the steps you should take. We also discussed precautions, welding techniques, and factors that influence weldability. Additionally, we touched on common issues, troubleshooting, aftercare, industry applications, and possible alternatives.
In simple terms, yes, you can weld A36 to A500. The key is understanding the proper techniques, like using the right filler material, and ensuring preheating when needed. With A36’s yield strength at about 250 MPa (36,000 Psi) and A500 ranging from 280-500 MPa (40,000-72,500 Psi), it’s important to follow the right steps to avoid issues down the line.
For further insights and resources on welding practices, feel free to return to our homepage at What is Welding.
References
- ISO. (2017). ISO 3834: Quality Requirements for Fusion Welding of Metallic Materials. Geneva, Switzerland: ISO.
- Appleton, W. (2020). Welding and Cutting: A Practical Handbook. Hauppauge, NY: Nova Science Publishers.
- Smith, D. L. (2010). Welding: A Journey to Explore Its History. Dubuque, IA: Kendall Hunt Publishing Company.
Joe Carter is a retired welding professional with over 40 years of hands-on experience in the industry, spanning ship repair, structural welding, and even underwater projects. Joe is a master of MIG, TIG, and Stick welding. Passionate about mentoring the next generation of welders, Joe now shares his decades of expertise and practical insights to help others build rewarding careers in welding.
A36 Steel, A500 Steel, Carbon Steel Welding, MIG Welding, Structural Steel, Weldability Factors, Welding, Welding Techniques, Welding Wire, Wire Diameter