Can You Tig Weld With 75/25? Exploring Uses, Techniques, and Benefits
Published on: April 3, 2025 | Last modified: March 4, 2025
By: Joe Carter
75/25 is a gas mixture with 75% argon and 25% CO2. It’s commonly used for various types of welding, making it versatile and effective.
I often hear people ask, can you tig weld with 75/25? It’s crucial to follow the right guidelines for the best results. In my experience, using this mix can affect the weld quality, penetration, and even the overall appearance of the finished product.
In this guide, we’ll explore if you can use 75/25 for TIG welding, types of 75/25 and their weldability, steps to TIG weld with 75/25, factors affecting TIG welding with this gas, and answer frequently asked questions. Understanding these points will help enhance your skills and decision-making in welding projects.
Contents
Can You Tig Weld With 75/25?
Yes, you can tig weld with 75/25. It’s a bit tricky because 75% argon and 25% CO2 is not ideal for TIG. Use pure argon for better control and clean welds. If you use 75/25, expect more spatter.
What is 75/25?
75/25 refers to a gas mixture of 75% argon and 25% carbon dioxide (CO₂). This blend is primarily used for MIG welding and occasionally for TIG welding. Argon provides better arc stability and a smoother finish, while CO₂ enhances penetration, making it ideal for thicker materials—perfect for welding steel.
Can you TIG weld with 75/25? That’s a great question. In my experience, 75/25 works well but can be tricky. The mixed gas may cause more spatter than pure argon. I’ve tried it, and with some fine-tuning, the results were decent.
I found 75/25 useful for work, especially when tackling thicker steel sections. I recall a project where switching to this mix boosted my productivity. However, if you’re considering using 75/25 for welding aluminum, you should explore alternatives like 100% argon for cleaner outcomes.
Types Of 75/25 and Their Weldability
-
75/25 Argon/co2 Gas Mixtures
75/25 Argon/CO2 is commonly used for MIG welding and creates a stable arc. You can weld with this mix using TIG, but set your welder for straight Argon. CO2 can negatively affect weld quality in TIG welding.
Choosing the right welding equipment is crucial, especially for those new to the field, as it determines the ease of learning and project success. If you’re just starting out, it’s worth exploring a good welder for a beginner.
-
75/25 Argon/oxygen Gas Mixtures
This mixture enhances arc stability and provides good penetration. You can also use it in TIG processes. To minimize oxidation, use this mixture sparingly and only when it improves weld efficiency.
-
75/25 Argon/helium Gas Mixtures
This blend increases arc heat and is effective for thicker materials. It’s excellent for TIG welding! Adjust the gas flow and welder settings to maintain control and achieve clean, precise welds.
-
75/25 Argon/other Gases
These mixtures, like Argon/Nitrogen, meet specific welding needs. You can occasionally use them in TIG welding. To ensure optimal performance, identify the gas type and adjust your equipment accordingly. For those interested in expanding their skills, learning how to weld in the overhead position can be beneficial.
We have now covered the types of 75/25 and their weldability. Next, we will examine the steps to TIG weld with 75/25.
Steps to TIG Weld With 75/25
Now, we’ll cover the steps for using a 75/25 gas mix in TIG welding. Follow these steps closely for a successful welding experience.
-
Gather Necessary Equipment
Before you start, ensure your machine is set for a 75/25 gas mix of argon and CO2. This provides unique arc stability, ideal for a clean weld. Use a tungsten electrode with a diameter between 2.4 mm (0.094 In) and 3.2 mm (0.125 In), especially for aluminum. Always check your filler rod’s compatibility with the base material.
Each type of material may require specific settings. For instance, welding stainless steel might need different filler material. Don’t compromise on quality, or you risk weak welds!
-
Prepare the Work Area
Clear any clutter and ensure the area is ventilated. A clean surface improves arc stability and reduces contamination risks. Position the pieces to be welded within reach—good posture helps prevent fatigue. Understanding different welding processes can also aid in selecting the right techniques. If possible, use a welding table for a level surface.
Pay attention to your workpieces’ orientation. A flat setup often yields better results, especially with lighter materials like aluminum. Use clamps to secure everything in place; it’s worth the effort!
-
Set Up the TIG Welder
Connect your TIG torch and ensure all equipment functions correctly. Set your current output based on the material; typically, 100 to 200 amps works for most aluminum jobs. Start at 150 amps and adjust as needed. Keep an eye on pedal responsiveness!
When connecting your gas line, ensure it’s secure. A leaky gas line can lead to contamination, causing poor welds. Trust me; discovering this mid-job is frustrating!
-
Adjust Gas Flow Settings
Set your gas flow rate between 10 to 20 liters per minute (L/min), or 24 to 47 cubic feet per hour (CFH), depending on the application. A slightly higher flow rate often works well for aluminum because the gas shields the weld puddle effectively. Adjust based on environmental factors like wind—excessive wind can create issues.
Consider your torch size. A #7 or #8 series torch is standard for 75/25; you don’t want to compromise gas coverage. Experiment with test beads to find the right settings.
-
Perform Test Welds
Before starting your final work, do a couple of test beads on scrap material. This helps you fine-tune your settings and build confidence. Aim for a steady travel speed—too fast can lead to undercutting, while too slow may cause excessive heat and warpage. A travel speed of around 150 to 200 mm/min (5.9 To 7.9 In/min) is recommended for aluminum testing.
Monitor the arc length, keeping it about 1.5 times the electrode’s diameter—maintain it tight, but not so close that you melt the tungsten. Once you’re satisfied with the test beads, you’re ready to start the project!
We’ve wrapped up the procedures for TIG welding with 75/25 here. Next up, we’ll look at the factors influencing TIG welding.
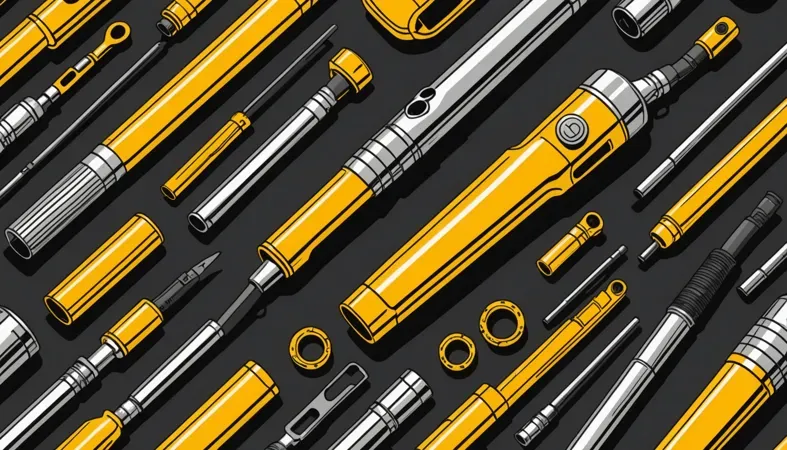
Factors Affecting TIG Welding With 75/25
What factors influence your ability to weld with this gas mix?
-
Gas Composition Quality
The quality of your 75/25 gas mix (75% Argon, 25% CO2) can greatly affect the weld. Impurities can cause defects like porosity, reducing joint strength.
-
Material Thickness Variations
Thicker materials need more heat. A 75/25 mix works best for thinner materials, typically under 5 mm (0.2 Inches).
-
Welding Technique Proficiency
Practice your technique. Accurate arc control is crucial for using 75/25 effectively.
-
Environmental Conditions
Windy or drafty conditions can disperse the gas shield, leading to poor weld quality. Maintain a controlled atmosphere while welding.
-
Electrode Configuration
Ensure your electrode is properly configured. An improper setup can reduce arc stability, impacting the weld with 75/25.
So far we covered the elements influencing TIG welding with 75/25. Next, let’s look at its advantages and disadvantages.
TIG Welding with 75/25: Pros and Cons
Let’s break down the advantages and disadvantages of using 75/25 in TIG welding.
Pros | Cons |
---|---|
Better Penetration | Increased Spatter |
Cost-effective for MIG welds | Less control compared to pure argon |
Works on thicker materials | Not suitable for aluminum |
Common in automotive applications | Poor corrosion resistance on stainless steel |
Using 75/25 can boost penetration when welding thicker materials, making it efficient for certain jobs. But, be aware that it leads to more spatter and less clean results. If you’re working mostly with steel, this mix might still suit you—just remember to use pure argon for aluminum to get the best outcomes.
We have now covered the advantages and disadvantages of TIG welding with a 75/25 gas mixture. Next, we will address common questions.
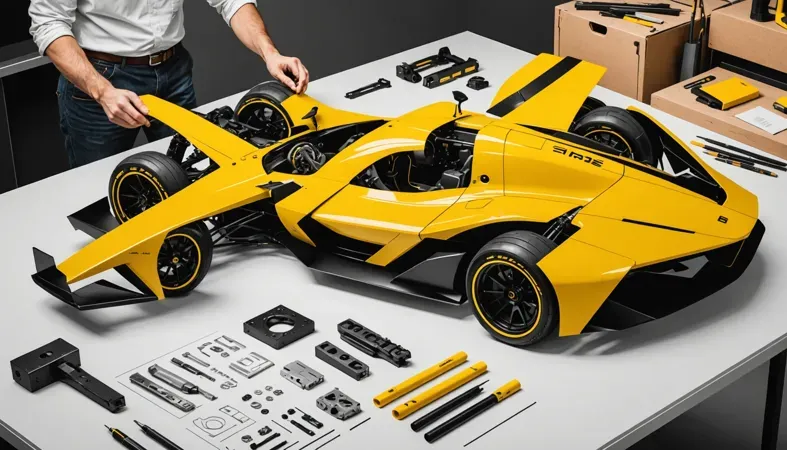
Frequently Asked Questions (FAQs)
Now let us look at some common questions I typically get asked.
What is 75% Argon and 25% CO2 Used for?
75% argon and 25% CO2 is often used for MIG welding. This gas mix provides better arc stability and penetration for steel welding. It also helps reduce spatter, making it easier to manage the weld. You’ll find this mix popular in various industries due to its efficiency.
Can You Weld Aluminum With 75% Argon and 25% CO2?
No, you can’t weld aluminum with 75% argon and 25% CO2. Argon is the preferred gas for aluminum welding because it offers a cleaner weld. Using CO2 can lead to oxidation and poor weld quality for aluminum materials.
Can You Use Argon CO2 Mix for TIG Welding?
No, it’s not ideal to use an argon-CO2 mix for TIG welding. TIG welding generally requires pure argon to achieve the right arc behavior and heat control. Using a mix can result in a less stable arc and inconsistent welds, which are crucial for high-quality results.
What Happens if You Weld Stainless With 75/25 Gas?
If you weld stainless steel with 75/25 gas, it may lead to poor weld quality. The CO2 can affect corrosion resistance and cause discoloration in stainless steel. This gas mix isn’t typically recommended for stainless applications; pure argon is better.
Can You MIG Weld Aluminum With 75/25?
You shouldn’t MIG weld aluminum with 75/25 gas. This mix can create insufficient heat and burn-through in aluminum. For aluminum welding, using 100% argon is essential as it ensures the heat input is adequate and the weld strength is optimal. To achieve seamless operation, it is important to understand hooking up a Miller suitcase welder.
What Applications is 75/25 Gas Suitable for?
75/25 gas is suitable for welding mild steels. It’s popular in fabrication shops and automotive repairs where strong joints are essential. Many welders prefer this mix for its efficiency in creating consistent and durable welds.
Wrapping Up
We covered a lot today. We discussed what 75/25 gas is, its types and weldability, steps to TIG weld with it, factors affecting this process, and answered frequently asked questions. Each item plays a part in understanding the question, “can you tig weld with 75/25?”
In short, yes, you can tig weld with 75/25. That’s 75% argon and 25% CO2, which typically works well for mild steel and stainless steel, but isn’t ideal for aluminum. So, while you can use this mix, aim to stick with pure argon for aluminum welding to get optimal results. Happy welding!
For a deeper dive into the world of welding, be sure to visit What is Welding, where you’ll find a wealth of welding guides and tutorials to enhance your skills.
References
- American Society of Mechanical Engineers. (2019). ASME Section IX: Welding and Brazing Qualifications. New York, NY: ASME.
- Kou, S. (2003). Welding Metallurgy (2nd ed.). Hoboken, NJ: Wiley.
Joe Carter is a retired welding professional with over 40 years of hands-on experience in the industry, spanning ship repair, structural welding, and even underwater projects. Joe is a master of MIG, TIG, and Stick welding. Passionate about mentoring the next generation of welders, Joe now shares his decades of expertise and practical insights to help others build rewarding careers in welding.
75/25 Gas Mixture, Argon CO2 Mix, MIG Welding, TIG Welding, Weld Quality, Welding, Welding Equipment, Welding Table, Welding Techniques