Can You JB Weld Aluminum? Exploring Types, Steps, and Precautions
Published on: January 15, 2025 | Last modified: March 4, 2025
By: Joe Carter
JB Weld is a strong adhesive that can bond metal, ceramic, wood, and more. It works like super glue but is much tougher, making it great for repairs.
People often ask us, can you jb weld aluminum? It’s essential to know this because aluminum has unique properties, and using the wrong method could lead to failure. From my own experience, I’ve seen projects turn from unrecoverable messes into durable fixes with the right JB Weld, saving time and money.
In this article, we’re diving into the specifics about JB Weld for aluminum. We’ll explore topics like types of JB Weld available, steps to successfully JB Weld aluminum, precautions to take, factors influencing bond strength, potential issues you might face, and aftercare tips. You’ll also learn why it’s worth your time and what alternatives exist for JB Welding aluminum.
Contents
- Can You JB Weld Aluminum?
- What is JB Weld?
- Types Of JB Weld
- Prerequisites
- Steps to JB Weld Aluminum
- Precautions
- Types Of JB Weld for Aluminum
- Factors Influencing JB Weld Aluminum
- What Could Go Wrong: Common Issues
- Aftercare, Inspection, and Advanced Tips for JB Weld Aluminum
- Why This is Worth It: Advantages
- Benefits of Using JB Weld on Aluminum
- Industry Uses
- What Are the Alternatives to JB Welding Aluminum?
- Frequently Asked Questions (FAQs)
- Conclusion
- Additional Reading
Can You JB Weld Aluminum?
Yes, you can JB Weld aluminum. It’s pretty straightforward but requires surface prep for a solid bond. Clean, sand, and use the right JB product, like JB Weld Steel Reinforced Epoxy, for the best results. Follow the instructions, and you’ll have a strong repair!
What is JB Weld?
JB Weld is a two-part epoxy adhesive known for its strength and versatility. It’s made of a resin and a hardener that, when mixed, create a durable bond once cured. This product can withstand temperatures up to 550°F (288°C) and has a tensile strength of around 3960 psi (Pounds Per Square Inch). JB Weld sets within 4-6 hours, achieving full cure in 15-24 hours under proper conditions.
Now, can you use JB Weld on aluminum? This topic reminds me of times I’ve faced challenges with metal repairs. I’ve worked on many projects, including one where I needed to know: can I use JB Weld on aluminum? I wondered about its effectiveness on aluminum surfaces.
Once, I used it to fix a cracked aluminum boat. I sealed a leak after a careless bump left a gash in the hull. After applying JB Weld, I saw great results; it’s incredibly strong on aluminum when applied correctly. For those asking, “Which JB Weld is best for aluminum?” I recommend using Original JB Weld, as its tensile strength and curing properties are ideal for high-pressure applications—whether you’re patching a boat or fixing aluminum parts.
Types Of JB Weld
What are the different types of JB Weld that work with aluminum?
-
Steel Reinforced Epoxy
This type provides a strong bond and resilience. You can use it for aluminum projects. To apply, clean the aluminum surface, mix equal parts of the epoxy, and spread it evenly on the area needing repair.
-
Clearweld Epoxy
This is a clear, fast-setting adhesive suitable for aluminum surfaces. To use, prepare the surface, mix the resin and hardener, and apply it for a clean finish.
-
Highheat Epoxy
This type withstands high temperatures, making it ideal for heat-prone areas. It’s suitable for aluminum under high heat. To work with it, clean the aluminum, mix the epoxy, and ensure a tight seal on heated parts.
-
Plasticweld Epoxy
This is specifically for bonding plastics, but you can also use it on aluminum. To apply, prepare the aluminum surface, mix the epoxy, and press it firmly onto the surface.
-
Aluminum Weld
This is a specialized formula for bonding aluminum. It’s the best option for aluminum work. To use it, clean the area thoroughly, mix the weld, and apply it to create a strong, lasting bond.
You should now have a good understanding of the different types of JB Weld. In the next part, we’ll discuss prerequisites.
Prerequisites
What do you need to get started with JB Weld on aluminum?
- JB Weld Steel Reinforced Epoxy: You’ll need a product like JB Weld 8265S. It creates a strong bond for aluminum, withstanding temperatures up to 550°F (288°C).
- Surface Cleaner: Use Isopropyl Alcohol (IPA), such as 70% IPA. It’s crucial for cleaning surfaces, ensuring the epoxy adheres properly.
- Mixing Tools: Get a mixing stick, like a standard wooden stirrer. You need this to mix the JB Weld properly for a consistent bond.
- Clamping Device: Use a C-clamp or similar tool. This holds parts together, applying the necessary pressure for a strong bond.
We have now covered the necessary prerequisites for using JB Weld. The next section will discuss the steps to apply it.
Steps to JB Weld Aluminum
We’ll cover steps to effectively use JB Weld on aluminum. Following each step closely ensures a strong bond!
-
Prepare the Surface
Start by cleaning the aluminum parts you’ll bond. Use a wire brush or sandpaper with a grit of 80 to 120 for a rough surface. This helps JB Weld adhere better. Remove any dirt, grease, or oxidation—that’s key for a solid hold.
After cleaning, wipe the area with acetone and let it dry completely. A clean surface makes all the difference, especially for aluminum!
-
Mix the JB Weld Components
Take equal parts of JB Weld resin and hardener. Use a small plastic or metal container for mixing. Stir the mixture using a stick or small tool until it’s uniform, usually about 1 to 2 minutes. Aim for a smooth consistency without clumps.
Keep in mind, JB Weld sets in 4 to 6 hours and reaches full strength in 16 to 24 hours. The correct mix ratio ensures the weld forms properly and achieves maximum strength. Don’t rush this step; it’s crucial!
-
Apply the Mixture
Use a small putty knife or similar tool to apply JB Weld to both surfaces. Spread it evenly across the bonding area to ensure complete coverage. Aim for a layer about 1/8 inch (3 Mm) thick for a strong hold. Consider applying extra in areas that might experience stress.
For those curious about welding techniques, an interesting approach to explore might be understanding seam welding.
Be careful not to over-apply, as excess can create a mess and doesn’t improve the bond. Keep it neat for the best results!
-
Clamp or Secure the Parts
After applying, bring the aluminum parts together and hold them tightly. Use clamps, tape, or weight to apply consistent pressure. This ensures a clean bond and prevents movement during the curing phase. For larger surfaces, a quick-release clamp works wonders!
Ensure the parts remain aligned—precision is important. If you don’t clamp properly, the bond might not hold over time. So, keep it secure and in place.
-
Allow the Mixture to Cure
Finally, let JB Weld cure undisturbed. The initial set time is about 4 to 6 hours, but it’s best to wait 16 to 24 hours for full strength. Keep the piece at room temperature; don’t rush this curing time! Patience here ensures maximum strength.
Once cured, you’ll have a strong bond that can withstand pressure and chemical exposure. I once rushed this step and regretted it—it can backfire!
You should now have a good understanding of applying JB Weld to aluminum. In the next part, we’ll discuss safety measures.
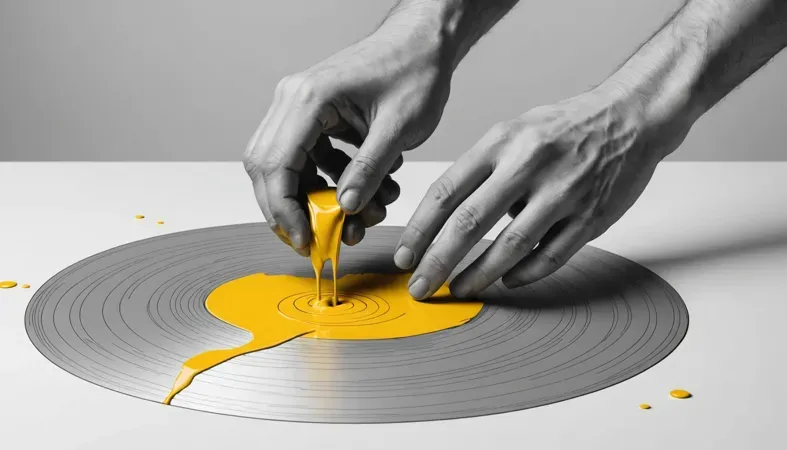
Precautions
Let’s quickly review essential safety measures for JB Weld aluminum.
- Ventilation: Ensure good airflow to avoid toxic fumes. Use exhaust fans or work outside.
- Protective Gear: Wear gloves and safety glasses to prevent skin contact. Consider nitrile gloves like Kimtech.
- Clean Surfaces: Clean joints thoroughly for a stronger bond. Abrasives like 120-grit sandpaper help achieve this.
- Follow Curing Time: Allow full curing for the best results. JB Weld requires 15-24 hours for peak strength.
Your safety’s crucial. I always prioritize precautions when working.
We covered safety measures when using JB Weld. We will now cover the various types of JB Weld for aluminum.
Types Of JB Weld for Aluminum
Let’s discuss the types of JB Weld for aluminum: Standard Aluminum Epoxy, High Temperature Aluminum Epoxy, Quick Setting Aluminum Epoxy, Flexible Aluminum Epoxy, and Structural Aluminum Epoxy.
-
Standard Aluminum Epoxy
This epoxy is ideal for general-purpose bonding on aluminum. It can handle temperatures up to 120°C (248°F) and sets in about 4-6 hours. That’s useful for a quick yet durable fix!
-
High Temperature Aluminum Epoxy
This type is your go-to for heat resistance! Rated up to 150°C (302°F), it’s excellent for engine parts or exhaust repairs. It also sets in about 4-6 hours, just like the standard epoxy.
-
Quick Setting Aluminum Epoxy
This epoxy sets in just 5 minutes, making it perfect for small jobs where you can’t wait. It withstands temperatures up to 120°C (248°F), ensuring it’s tough.
-
Flexible Aluminum Epoxy
This option remains flexible after curing, making it great for repairs on metal that bends or vibrates. It can withstand up to 120°C (248°F).
-
Structural Aluminum Epoxy
If durability is a priority, choose this type. It creates a strong, lasting bond and is excellent for heavy-duty applications. It can handle high stress and performs well up to 120°C (248°F).
I recommend structural aluminum epoxy for its strength in demanding situations. It’s perfect for essential repairs in the item’s structure. Once it sets, you won’t worry about it failing under pressure!
Factors Influencing JB Weld Aluminum
What factors impact your ability to bond aluminum effectively?
-
Metal Cleanliness
If the aluminum surface isn’t clean, you’ll struggle. Dirt or grease can weaken the bond by up to 50%.
-
Temperature Conditions
Apply JB Weld between 10°C and 30°C (50°F and 86°F). Extreme temperatures can hinder curing, so keep it warm.
-
Application Technique
Focus on applying JB Weld evenly. A smooth, thin layer allows for better adhesion. The type of JB Weld, like JB Kwik, also affects application.
-
Cure Time
Wait at least 4-6 hours for a solid bond. Full cure may take up to 15 hours, depending on conditions.
-
Pressure Application
Applying light pressure while curing improves metal-to-metal contact. Excess pressure can cause the bond to fail before it sets.
What Could Go Wrong: Common Issues
Let’s look at some common issues that can arise when using JB Weld.
-
Poor Surface Preparation
JB Weld needs a clean, dry surface. If it isn’t clean, it’ll fail. Check for grease or rust. Clean with alcohol or sand the area before applying.
-
Insufficient Cure Time
JB Weld requires 4-6 hours to set. Wait at least 24 hours for maximum strength. Check adhesion by gently tugging—if it budges, give it more time.
-
Incorrect Mixing Ratio
An incorrect ratio affects JB Weld’s strength. Follow label instructions carefully. A mix that’s too dry won’t bond properly; if it feels crumbly, try again!
-
Exposure to Extreme Temperatures
JB Weld can weaken at extreme temperatures (Over 49°C/120°F). In hot areas, watch for softening. Use it in climates of 15°C-27°C (60°F-80°F) for best results.
-
Overloading Before Cure
Applying stress to JB Weld too soon will cause it to break. Wait the full cure time, then check strength by applying gradual pressure.
Aftercare, Inspection, and Advanced Tips for JB Weld Aluminum
Here’s solid advice on maintaining and ensuring the longevity of your JB Weld projects on aluminum.
Aftercare Insights
After you JB Weld aluminum, let it cure (Harden) for at least 4-6 hours before handling. Avoid water exposure for at least 24 hours; moisture can weaken the bond. For the best results, keep the repaired area in a temperature-controlled environment, ideally between 18°C and 29°C (65°F and 85°F).
Performing a precise welding task involves multiple steps, and each plays a crucial role in achieving a durable joint; understanding what a hot pass in welding helps ensure a strong final weld.
Inspection Checklist
Inspect the bond for any gaps or cracks after curing. Use a magnifying glass if needed to view imperfections. I often use Loctite Instant Mix epoxy for guidance; it helps me spot flaws under 2x magnification effectively before sealing.
Expert Tips for Professionals
If you’ve got years of experience with JB Weld on aluminum, consider pre-treating surfaces with a light scuff using sandpaper (Around 120 Grit). Boost adhesion by slightly heating the metal piece before applying the adhesive for optimal bonding. Finally, remember that mixing ratios matter; stick to a strict 1:1 ratio for the best strength. Feel free to use an ultrasonic cleaner (50-60 Khz) for flawless surface results!
Why This is Worth It: Advantages
The main benefit of using JB Weld on aluminum is its incredible bond strength. I once used it to repair a damaged aluminum frame, and it held up like a champ.
Additionally, JB Weld is resistant to water, chemicals, and temperatures up to 500°F (260°C). You’ll also appreciate its ease of use, quick curing time, and versatility on various surfaces, including aluminum boats and cast aluminum. When tackling a project that involves joining thinner materials, you may need techniques on how to weld 16 gauge sheet metal.
Benefits of Using JB Weld on Aluminum
JB Weld isn’t just for quick fixes; it has impressive benefits for aluminum repairs.
Benefit | Description | Data/Measurement |
---|---|---|
High Bond Strength | Forms a bond often stronger than aluminum itself, ensuring durability. | Tensile strength: ~3960 psi (27.3 MPa) |
Temperature Resistance | Withstands extreme temperatures, making it suitable for various applications. | Up to 550°F (288°C) |
Water and Chemical Resistance | Holds up against moisture and chemicals, perfect for outdoor or marine use. | Resistant to water, oil, and most solvents. |
Quick and Easy Application | Two-part epoxy allows for straightforward mixing and application. | Sets in 4-6 hours; full strength in 15-24 hours. |
Versatile Use | Ideal for indoor and outdoor projects, plus a range of surfaces. | Works on metal, wood, and ceramics, aside from aluminum. |
Industry Uses
I’ve known people to use JB Weld for tough repairs, but it has many applications, such as:
- Automotive Repairs: JB Weld fixes cracked aluminum engine parts. It’s popular among DIY enthusiasts for its strength and durability.
- Marine Applications: Many use JB Weld on aluminum boats. It seals leaks effectively and withstands harsh water conditions.
- HVAC Units: This adhesive’s heat resistance makes it ideal for repairing aluminum ductwork, helping restore efficiency in cooling systems.
- Art Projects: Artists use JB Weld for metal sculptures, bonding aluminum pieces securely. Its versatility and strength keep their creations intact.
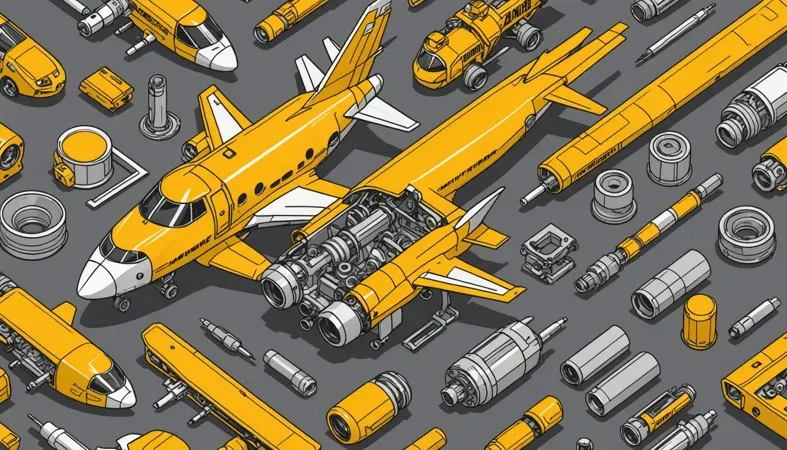
What Are the Alternatives to JB Welding Aluminum?
There are several alternatives to JB Weld for aluminum repairs. You can use aluminum epoxy, such as Loctite Epoxy Metal/Concrete, for strong bonding that withstands high temperatures. For quick fixes, consider using aluminum repair rods, like the famous Alumaloy, which works well when brazing is an option.
Based on my observations, these products often offer better flexibility and ease of use compared to JB Weld. In some cases, especially for boats or high-pressure scenarios, opting for a specific aluminum welding method may yield longer-lasting results. It really comes down to the job at hand and the materials you’re working with when considering welding alternatives.
Frequently Asked Questions (FAQs)
Now let us look at the common queries I typically get asked about JB Weld and aluminum.
Does J-B Weld Hold Aluminum?
Yes, J-B Weld does hold aluminum effectively. This epoxy can withstand temperatures up to 550°F (288°C) and has a tensile strength of about 3960 psi (27.3 Mpa). It’s known for creating a strong bond, making it a popular choice for aluminum repairs.
What is the Strongest Epoxy for Aluminum?
The strongest epoxy for aluminum is usually a two-part epoxy, like J-B Weld. It provides a bond that’s often stronger than the aluminum itself. This results in a durable repair that can last for years under varying conditions.
How Do You Repair Broken Aluminum Without Welding?
You can repair broken aluminum without welding by using a strong epoxy, like J-B Weld. Just clean the surfaces, mix the epoxy, and apply it. This method is useful for items that can’t be welded due to their size or shape.
What is the Best Thing to Weld Aluminum With?
The best things to weld aluminum with are MIG or TIG welding techniques. For MIG, you often use 4043 or 5356 filler wire, while for TIG, pure tungsten electrodes work great. Both methods provide strong, clean welds for aluminum projects.
Can I use JB Weld on aluminum?
Yes, you can use JB Weld on aluminum. It’s designed to create a solid bond on various metals, including aluminum. For best results, roughen the surface and clean it well before application for a stronger adhere.
Conclusion
You made it to the end, and I’m glad you did. We covered key points like what JB Weld is, types of JB Weld, steps to JB weld aluminum, prerequisites, precautions, industry uses, alternatives, and common issues you might face. I hope that gives you a solid foundation on this topic.
So, can you JB weld aluminum? In simple terms, yes, you can. But remember, using the right type of JB Weld for aluminum, following the steps, and making sure to address factors like surface preparation and temperature will give you the strongest bonds possible. Happy repairing!
Conclusion
You made it to the end, and I’m glad you did. We covered key points like what JB Weld is, types of JB Weld, steps to JB weld aluminum, prerequisites, precautions, industry uses, alternatives, and common issues you might face. I hope that gives you a solid foundation on this topic.
So, can you JB weld aluminum? In simple terms, yes, you can. But remember, using the right type of JB Weld for aluminum, following the steps, and making sure to address factors like surface preparation and temperature will give you the strongest bonds possible. Happy repairing!
As you continue your journey into DIY repairs, don’t forget to explore our resources at What is Welding for the latest technical expertise.
Additional Reading
- American Society of Mechanical Engineers. (2019). ASME Section IX: Welding and Brazing Qualifications. New York, NY: ASME.
- Smith, D. L. (2010). Welding: A Journey to Explore Its History. Dubuque, IA: Kendall Hunt Publishing Company.
- American Welding Society. (2021). AWS SENSE: Guidelines for Entry-Level Welders. Miami, FL: AWS.
Joe Carter is a retired welding professional with over 40 years of hands-on experience in the industry, spanning ship repair, structural welding, and even underwater projects. Joe is a master of MIG, TIG, and Stick welding. Passionate about mentoring the next generation of welders, Joe now shares his decades of expertise and practical insights to help others build rewarding careers in welding.
Aluminum Repairs, American Welding Society, Bonding Metals, DIY, DIY Repair, Epoxy Adhesives, Jb Weld, Metalworking Techniques, TIG Welding, Welding, Welding Techniques