What is Tack Welding? Tack Welds, Process, Importance
Published on: January 5, 2025 | Last modified: March 4, 2025
By: Joe Carter
Tack welding is a quick method used to hold materials together before the final weld. It helps set the position and stability of the pieces.
What is tack welding? It’s important because it ensures your workpiece remains aligned during welding. In my experience, using tack welds saved me countless hours on projects, preventing materials from shifting and ruining my hard work.
In this guide, I’ll cover how tack welding works, its types, steps to perform it, factors that affect it, common issues, inspection aftercare, typical uses, and other options you can consider. You’ll also find answers to frequently asked questions about what is a tack welder and what is the importance of tack welding.
Contents
- What is Tack Welding?
- How Does Tack Welding Work?
- Types Of Tack Welding
- Steps to Perform Tack Welding
- Factors Affecting Tack Welding
- Common Issues and Troubleshooting
- Aftercare, Inspection, and Advanced Tips for Tack Welding
- Typical Uses Of Tack Welding
- Other Options You Can Consider
- Related Techniques to Tack Welding
- Frequently Asked Questions (FAQs)
- Conclusion
- References
What is Tack Welding?
Tack welding is a temporary weld that holds parts in place. It’s crucial during assembly, allowing for precise alignment and fit. Typical applications include fabricating structures, like frames or installations, where positioning needs accuracy. Arc control is essential for enhancing weld quality and stability, which you can explore further in the context of arc control on a MIG welder.
How Does Tack Welding Work?
Tack welding is a technique that temporarily joins metal parts. It creates small, quick welds to hold components together before final welding. Typically, tack welds are about 2 to 5 mm (0.08 To 0.20 Inches) in diameter. They provide a strong bond but usually withstand only 60 to 70% of the strength of the final weld.
This process typically involves a tack welder, which can be an arc (Electric) or MIG (Metal Inert Gas) welder. Welders often use these machines to make quick, precise spots. Tack welding isn’t just about holding parts together; it aids alignment and reduces distortion while completing the final weld.
I’ve tackled plenty of projects using tack welding. It’s an essential step in welding, keeping everything aligned while working on larger structures. Tack welding helps maintain the integrity of the final weld, especially when joining different materials.
Types Of Tack Welding
-
Spot Tack Welding
Spot tack welding joins two metal pieces at specific points. This technique is crucial for holding components in place before final welding. Use a spot welder to apply heat at precise spots, creating strong bonds that prepare the workpieces for full welds.
-
Continuous Tack Welding
Continuous tack welding creates a uniform, stable connection along the entire joint. It’s useful when assembling components that need full-length support. Move the welding torch or electrode steadily along the joint to form consistent tack welds for a solid structure.
-
Automated Tack Welding
Automated tack welding uses machines to perform welds consistently and quickly, enhancing productivity in large-scale projects. Set up machinery like robotic arms equipped with precise welding tools to create uniform tacks across many workpieces.
-
Manual Tack Welding
Manual tack welding relies on the welder’s skills to join metal pieces. It’s often used in custom welding jobs where precision is essential. Use a handheld welding tool to carefully apply heat at the joint, creating small welds to hold the pieces until final welding.
-
Resistance Tack Welding
Resistance tack welding uses heat generated from electrical resistance to join metals. It’s widely used in the automotive and appliance industries. Place the electrodes in contact with the materials and pass current through, resulting in quick fusion at the contact points. A crucial aspect of weld quality is managing the welding sequence which includes executing an effective hot pass technique.
We covered the various types of tack welding here. Next, we will cover the steps to perform tack welding.
Steps to Perform Tack Welding
Now, we’ll cover the steps to effectively tackle tack welding.
-
Prepare Materials
Review the workpieces. Ensure they’re clean and free of contaminants like oil or rust. If they’re dirty, clean them with a degreaser or grinder. Clean surfaces improve weld quality.
Consider the types of materials as well. Steel, aluminum, and stainless steel have unique properties. For example, mild steel can be welded at higher speeds than aluminum, which requires slower feed rates.
-
Select Equipment
Choose the right welder for tack welding. A MIG welder is commonly used for its effectiveness on thin sheets. You can also use a TIG welder for aluminum or stainless steel. Ensure you’ve got the right wire, usually 0.030 to 0.035 inches (0.76 To 0.89 Mm) for MIG. Mastering techniques specific to thin materials is crucial, and you can discover practical tips on how to weld 16 gauge sheet metal in this resource for welding 16 gauge sheet metal.
Test your equipment before starting. If you adjust the voltage, aim for around 18-23 volts for mild steel, depending on the thickness. Adjust your wire feed speed accordingly—about 200-300 inches per minute (5-7.6 M/min) is a good rule of thumb.
-
Position Workpieces
Align the parts correctly, ensuring they fit snugly. Poor alignment can weaken joints, so take your time. If you’re tacking multiple pieces, use clamps to hold everything in place before welding.
Trust me: I once skipped clamping and regretted it. The pieces shifted, misaligning my tack welds and wasting time. A good fit prevents this and maintains quality.
-
Adjust Settings
Set your welder based on the materials’ thickness for optimal performance. For 0.020-inch (0.51 Mm) metal, start with a lower voltage and proceed cautiously. For thicker materials, increase the voltage accordingly. It’s important to keep your torch angle at 15-20 degrees for best results, as this technique can enhance your overall welding guidance.
You can also gain insights into specific welding terminology, such as what DCEP means in more complex welding contexts.
Select the right gas mixture for your application. For most mild steel, a mix of 75% Argon and 25% CO2 works well, providing good penetration and a smooth arc.
-
Apply Tack Welds
Now that everything’s set, begin applying your tack welds. For a proper tack, melt both materials at the junction and let them cool quickly. Tacks should be about 1 to 2 inches (25 Mm to 50 Mm) apart for proper heat distribution and to minimize warpage.
Remember, too much heat can burn through your material! Apply the tack for just a second or two. Monitor the metal’s response, adjusting your technique as necessary to maintain quality.
We’ve wrapped up the steps for performing tack welding here. Next up, we’ll look at the factors influencing tack welding.
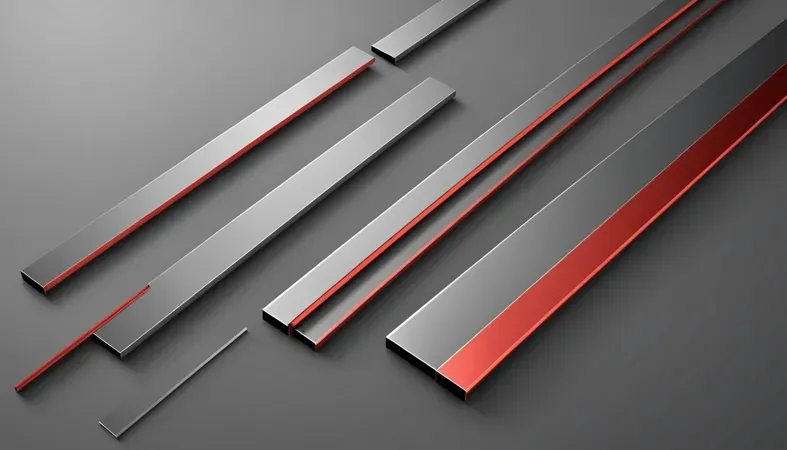
Factors Affecting Tack Welding
What factors influence the tack welding process?
-
Material Thickness
Thicker materials require higher heat input for a solid tack weld. For instance, 10-gauge steel (3.4 Mm) requires a different approach than 16-gauge (1.6 Mm).
-
Welding Speed
Faster welding speeds can lead to inadequate penetration. A welding speed of 2 inches per minute (50 Mm/min) gives better results for most materials.
-
Electrode Type
The right electrode makes a significant difference. For example, E7018 electrodes provide better toughness and strength than E6013 in specific applications.
-
Heat Input
Heat input affects weld properties. Lower input may not melt the base material enough, leading to weak bonds. Aim for 1.5 to 2.5 kilowatts (Kw) for optimal results.
-
Joint Design
Joint design influences heat distribution. A V-joint improves penetration compared to a flat joint, resulting in stronger tack welds.
We covered factors influencing tack welding here. Next, we will cover common problems and how to troubleshoot them.
Common Issues and Troubleshooting
Here are some common problems you might encounter with tack welding.
-
Poor Fusion
Tack welding can suffer from poor fusion if you don’t apply enough heat. Look for undercutting or gaps. To troubleshoot, adjust your welder to increase the amperage. A good rule of thumb is to aim for at least 15% higher settings for tack welds. Mastering different welding positions is crucial for improving your technique, and one might explore more about 3G welding basics.
-
Electrode Wear
Tack welding can overheat the electrode. Check for rounded tips, as this may indicate excessive wear. To fix this, replace the electrode regularly or use lower amperage during tacking.
-
Inconsistent Welds
If your tack welding shows inconsistent weld sizes, check your technique. It’s crucial to maintain the same angles and travel speed. Practice makes perfect!
-
Excessive Spatter
Tack welding can create spatter if the settings are off. Look for small drops around the weld. To correct this, lower the wire feed speed or clean the surfaces before welding.
-
Warpage Of Materials
Warpage is common if you heat too much during tack welding. Check for distortion after welding. To resolve this, clamp your materials or use a stitch method to minimize heat.
We covered common issues and troubleshooting techniques here. Next, we will cover aftercare, inspection, and advanced tips for tack welding.
Aftercare, Inspection, and Advanced Tips for Tack Welding
Here’s essential advice on aftercare, inspection, and advanced strategies for tack welding.
Aftercare Suggestions
After tack welding, wait at least 20 minutes before cooling the weld beads in water to avoid rapid shrinkage (12°C to 28°F Increase). Clean the weld area to prevent contamination. Use a wire brush with a diameter of 0.2 mm to remove slag and spatter for optimal adhesion during the next welding stages. Understanding the various methods involved can enhance your welding techniques, and you can discover the different types of welding.
Inspection Tips
Start inspection by checking for proper tack sizes, ideally 6–10 mm (0.24–0.39 In) in diameter. Ensure the gap between joined parts is consistent (Not More Than 1 Mm or 0.04 In). I use Insta-Check™ gauge tools for quick alignment verification.
Expert Tactics
If you’re experienced, always plan your bolster angles at 45 degrees for a clear pull in dual-direction welding. Limit tack welds to 3–4 per joint using a current of about 300 A for thicker materials (5–10 Mm or 0.2–0.4 In). Use backing bars for consistent heat distribution at joints to prevent warping. Mastery of welding a precise 45-degree angle in such scenarios is essential for achieving optimal weld integrity, and you can explore techniques for welding 45-degree angles effectively.
.
Typical Uses Of Tack Welding
I’ve used tack welding to guide larger welds, but it has many applications, such as:
- Automotive Manufacturing: Tack welding aligns sheet metal parts in car bodies. It ensures everything fits before the final weld, making it popular in auto factories.
- Construction of Pressure Vessels: Tack welding temporarily holds pieces together for large-scale assembly. It’s vital for safety and durability in high-pressure situations.
- Shipbuilding: Tack welding stabilizes various sections of large ships before final welding. This method streamlines production and maintains structural integrity.
- Pipe Spooling: Tack welding joins sections of pipes before the final weld. It saves time and ensures accuracy in thick-walled piping systems.
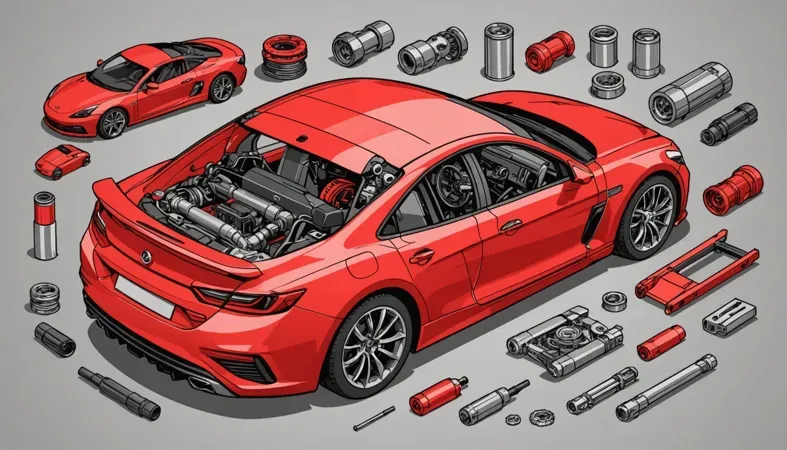
Other Options You Can Consider
When you’re looking to achieve results similar to tack welding, consider alternatives like MIG (Metal Inert Gas) welding or using clamps. MIG welding, such as the Millermatic 211, offers speed and versatility, while clamps can secure pieces accurately during the final weld. You might prefer these methods in tight spaces or when working on delicate materials.
Another option is the use of spot welding, especially with units like the Weldpro 200. Spot welding allows quick joins with minimal heat, perfect for thin sheets. Each method has its pros, so choose based on your project needs and materials!
Related Techniques to Tack Welding
Understanding related welding techniques can enhance your tack welding skills. Here’s a breakdown of a few methods that complement tack welding:
Technique | Overview | Best Applications | Key Benefits |
---|---|---|---|
Butt Welding | Joins two pieces of material end to end by applying heat along their edges. | Used in pipeline construction and sheet metal work. | Great for strong, flush connections. |
Fillet Welding | Forms a right-angle joint between two materials, creating a triangular cross-section. | Ideal for corner connections in structural applications. | Easy to apply; provides good strength. |
Stacked Welding | Involves overlapping multiple weld beads to build up material in thick joints. | Useful in thick metal fabrication where penetration is critical. | Promotes robust joints with significant strength. |
Brazing | Joins metals using a filler material that melts above 450°C (842°F) but below the melting point of the base metals. | Perfect for dissimilar metals and precise components. | Offers great ductility and corrosion resistance. |
Frequently Asked Questions (FAQs)
We have covered some questions you might have about tack welding.
What is the Purpose Of a Tack Weld?
The purpose of a tack weld is to hold parts together temporarily during the welding process. Tack welds provide stability, helping to maintain alignment, ensuring accuracy hence preventing distortion during final welding. Understanding the technology behind welding machines is crucial, and exploring the benefits of a DC inverter welding machine can greatly enhance your projects.
What is the Difference Between a Welder and a Tack Welder?
The main difference between a welder and a tack welder is the scope of their work. Welders perform complete welds, while tack welders make short, specific welds to hold pieces in place before final welding, proving speed and accuracy in setups.
What is the Purpose Of Tacking?
The purpose of tacking is to secure metal components temporarily for alignment. Tacking ensures that everything fits correctly before the final welding occurs, allowing for adjustments and minimizing costly mistakes in assembly.
How Does Tack Welding Work?
Tack welding works by using an electric arc or other heat sources to create small welds. This process melts the edges of the materials, forming a small join, which holds parts together securely until full welds are placed by a welder.
How to Qualify for a Tack Welder?
To qualify as a tack welder, you typically need training in basic welding techniques and safety procedures. Practical experience under supervision often helps, and obtaining certifications from recognized institutions can bolster your qualifications in this field.
Conclusion
Phew, we covered a lot about tack welding. We touched on the definition, the various types, the steps for performing it, and factors affecting it. We also explored common issues, troubleshooting tips, aftercare, inspection, and typical uses. For a deeper understanding of these concepts, you might consider the broader implications of welding fundamentals in different contexts.
Hopefully, I was able to impart some of my experience about what tack welding is. Simply put, tack welding is a quick way to hold pieces together temporarily by applying localized heat. It involves the use of specific techniques, like those we discussed—steps, types, and even aftercare—to ensure your project stays on track.
To further enhance your knowledge and skills, feel free to visit What is Welding for comprehensive resources on all aspects of welding.
References
- American Welding Society. (2020). AWS C5.6: Recommended Practices for Gas Metal Arc Welding. Miami, FL: AWS.
Joe Carter is a retired welding professional with over 40 years of hands-on experience in the industry, spanning ship repair, structural welding, and even underwater projects. Joe is a master of MIG, TIG, and Stick welding. Passionate about mentoring the next generation of welders, Joe now shares his decades of expertise and practical insights to help others build rewarding careers in welding.
American Welding Society, Metal Fabrication, MIG Welding, Structural Integrity, Tack Welding, Temporary Welds, Welding, Welding Equipment, Welding Process, Welding Techniques