How to Weld Fence Panels? A Step-by-Step Guide, Safety Tips, and Common Problems
Published on: January 14, 2025 | Last modified: March 4, 2025
By: Tyler James
One thing that’s regularly asked of me is how to weld fence panels. It’s crucial to know the right techniques to ensure durability and strength in your welds. I’ve seen many projects fall apart due to lack of proper welding, so let’s dive into the details.
In this guide, I’ll cover various essentials, including types of fence panels, prerequisites before you start, step-by-step welding instructions, safety tips, and different welding methods. You’ll also learn about factors affecting your welding, common problems to watch out for, and the benefits you can expect from welded fence panels. Plus, I’ll touch on aftercare and alternatives for welding a metal fence.
Contents
- How to Weld Fence Panels?
- What Are Fence Panels?
- Types Of Fence Panels
- Before You Start (Prerequisites)
- Steps to Weld Fence Panels
- Safety Tips
- Types Of Welding for Fence Panels
- Factors Affecting How to Weld Fence Panels
- Typical Problems to Be Aware Of
- Aftercare, Inspection, and Advanced Tips for Welding Fence Panels
- Advanced Techniques for Welding Fence Panels
- Mathematical Considerations in Welding Fit-Up
- Top Benefits You’ll Expect
- Use Cases Of Welded Fence Panels
- Alternatives for Welding Fence Panels
- Frequently Asked Questions (FAQs)
- Conclusion
- References
How to Weld Fence Panels?
Fence panels are the sections that create your fencing. To weld fence panels, you’ll use a MIG welder, typically at 18-20 volts. Expect mild difficulty; common uses include garden fences and property boundaries.
What Are Fence Panels?
Fence panels are pre-assembled sections of fencing used to create barriers. They typically measure 1.8 meters (6 Feet) high by 2.4 meters (8 Feet) wide. These panels come in various materials, including wood, vinyl, and metal, with metal being the most durable. Research shows that metal fence panels can last over 50 years with proper maintenance, outperforming wood and vinyl options. Now, let’s discuss how to weld fence panels. Using a MIG welder makes the process easier and faster. I remember when I first replaced a rusty metal panel—after learning the right techniques, the finish was surprisingly strong! You might be surprised, but I actually used it for a DIY project in my backyard. I welded a decorative wrought iron fence, and it turned out great! If you’re wondering how to weld a wrought iron fence, it’s all about good preparation and practice, ensuring those joints are solid and secure.
Types Of Fence Panels
-
Wooden Fence Panels
Wooden fence panels are classic choices for residential fencing. To join wooden panels, use metal brackets and screws instead of welding, as wood can’t be welded like metal. First, cut the wood to size, drill holes for brackets, and fasten them securely with screws or bolts.
-
Metal Fence Panels
Metal fence panels offer durability and security. You can weld (Attach With Heat) these panels using a MIG welder at the joints. Align the panels, spot weld them at intervals for stability, then finish welding along the seams for a solid hold. For those working with thinner materials, learning the correct techniques is crucial for achieving strong and clean welds on 16 gauge sheet metal.
-
PVC Fence Panels
PVC panels are lightweight and low-maintenance. Since you can’t weld these, use special PVC glue or brackets to strengthen the connection. To install, securely connect the posts, then seal the panels to the posts using adhesive for a sturdy assembly.
-
Chain Link Fence Panels
Chain link panels provide a cost-effective security solution. Instead of welding, use tension bands to attach them to the posts. Stretch the chain link fabric tightly between the posts, securing it with tension wire at the top and bottom for added stability.
-
Composite Fence Panels
Composite panels combine wood and plastic for durability. These can’t be welded, but they can be drilled and screwed together. Use composite screws to fasten the panels to posts, ensuring each connection is tight for longevity.
So far we covered different kinds of fence panels. Next, let’s look at the necessary preparations before starting.
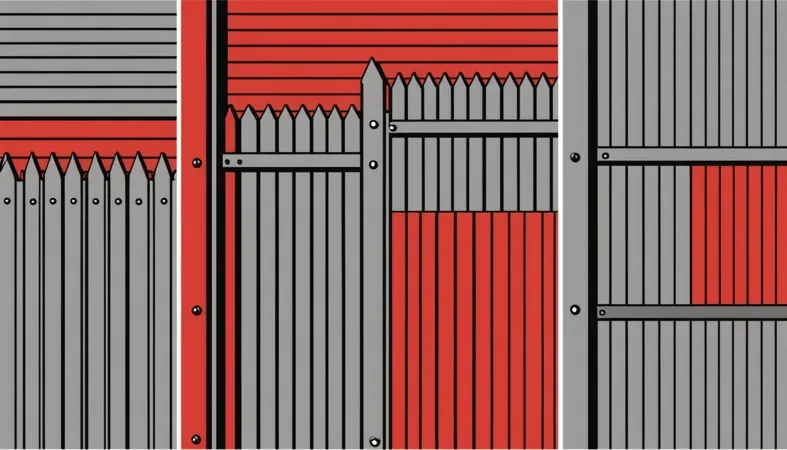
Before You Start (Prerequisites)
What do you need to start welding fence panels?
- MIG Welder: You’ll need a MIG welder, like the Hobart Handler 140. It’s essential for making strong, clean welds on metal fence panels.
- Welding Wire: Get .030-inch (0.76 Mm) ER70S-6 welding wire, such as Lincoln Electric. This wire ensures proper fusion (Joining) in your welds.
- Shielding Gas: Use a mix of 75% Argon and 25% CO2 with a flow rate of 15-20 CFH (Cubic Feet Per Hour). It protects your weld from contamination.
- Clamp or Tacks: A C-clamp, like the Bessey BPC-H34, is vital to hold the fence panels securely in place during welding.
We covered prerequisites for welding fence panels. Next, we will cover the steps to weld fence panels.
Steps to Weld Fence Panels
Let’s cover the steps for successfully welding fence panels. Just follow these instructions, and you’ll get it done right!
-
Prepare the Fence Panels
Start by cleaning the areas where you’ll weld. Use a wire brush or grinder to remove rust, paint, and debris. Aim for a bright metallic surface to ensure a strong weld. Check for any warping in the panels that might affect the weld.
If necessary, cut the panels using a metal cutting saw and wear your protective gear. Accurate measurements are crucial; make cuts at exact angles to fit. If you have multiple panels, consider using a jig for uniformity.
-
Align the Panels
Position your fence panels according to your fencing plan. Use clamps to hold the panels in place; stable alignment is essential! Ensure each panel is level and straight. A carpenter’s level helps maintain perfect alignment along linear runs.
Double-check your spacing. Typical spacing between panels is about 5 to 10 cm (2 to 4 Inches), but this can vary based on design. Precise alignment now makes a big difference in the final look of your fence.
-
Set Up Your Workspace
Create a clean and safe welding area. Find a flat, stable surface like a workbench to support your panels securely. Ensure proper ventilation and remove any flammable materials nearby. Lay down drop cloths to protect surfaces from sparks.
Set up your equipment. A MIG welder works well for most fence panels, especially if they’re steel or alloy. Adjust the settings; typically, a wire feed speed between 200 and 300 inches per minute (IPM) is effective. Have all your safety gear ready, including gloves, a helmet, and protective clothing.
-
Perform the Weld
Start by tacking the corners where the panels meet; this holds them in place while you complete the weld. Use short bursts of weld to minimize heat buildup; about 1 to 3 seconds per tack usually works well. Ensure consistent bead sizes by observing your speed as you move the nozzle. After tacking, you can run longer welds between the tacks for added strength.
Maintain a consistent angle of about 10 to 15 degrees for proper penetration. Move in a straight line for uniformity. If you’re new to welding panels, practice on scrap pieces first to understand how the metal reacts. Good welds should resemble small stacked dimes.
-
Finish Welding
Once your main welds are complete, fill any gaps or uneven areas by going over your welds with additional passes. Aim for a smooth, even surface to enhance both durability and aesthetics. If you need to switch welding machines, adjust the settings as processes can vary.
After completing the welds, visually inspect each one. Ensure there are no large gaps or slag that could weaken the fence. A nice finish can make a big difference, so consider grinding down any rough edges for a polished look.
You should now have a good understanding of welding fence panels. In the next part, we’ll discuss safety precautions.
Safety Tips
Let’s cover vital precautions for welding fence panels.
- Wear Protective Gear: Always use gloves, masks, and goggles, like Lincoln Electric welding gloves. They reduce burns and eye injuries.
- Proper Ventilation: Ensure good airflow. This prevents harmful smoke inhalation. Use fans if needed.
- Check Equipment: Inspect your welder to avoid malfunctions. I recommend the Hobart Handler 140 for reliability and performance.
- Fire Safety: Keep a fire extinguisher nearby. Sparks can ignite flammable materials, so keep your workspace clear.
Remember, prioritizing safety keeps you protected and focused on your work!So far we covered essential safety guidelines. Next, let’s look at different welding methods suitable for fence panels.
Types Of Welding for Fence Panels
Let’s explore the different welding types best suited for fence panels: MIG, TIG, Stick, Flux-Cored Arc, and Plasma Arc.
-
MIG Welding
MIG (Metal Inert Gas) welding uses a wire feed system. It’s effective for thin materials like fence panels and can weld at speeds up to 300 inches per minute (7.6 M/min), making it efficient and smooth.
-
TIG Welding
TIG (Tungsten Inert Gas) welding is great for precise joinery. It offers ultimate control, ideal for intricate designs in wrought iron fences. Though slower, it produces a clean, strong weld.
-
Stick Welding
Stick welding is versatile. It works outdoors and on rusty or dirty metals. You may need to adjust the amperage between 70-160 A based on panel thickness.
-
Flux-cored Arc Welding
This method uses a tubular wire filled with flux, making it perfect for outdoor projects and windy conditions. The heat can range from 200 to 300 A, allowing for deep penetration, essential for durable fence structures.
-
Plasma Arc Welding
Plasma arc welding provides high precision, ideal for thin materials. While commonly used in industrial settings, it can also be used for fence panels when additional detail is required. The temperature can reach up to 30,000°F (16,600°C) for powerful, clean cuts.
Factors Affecting How to Weld Fence Panels
What factors influence the process of welding fence panels? Let’s dive in!
-
Material Thickness
Material thickness directly impacts heat input and welding technique. For instance, 0.25 in (6.35 Mm) thick steel requires different settings than 0.50 in (12.7 Mm). A thicker panel absorbs more heat, so you’ll need to adjust your welder to ensure proper fusion.
-
Welding Method
Common methods include MIG, TIG, and stick welding. Each offers unique benefits; for example, MIG is faster but requires shielding gas, while stick welding is more versatile outdoors. For those looking to start hands-on initiatives, understanding DIY welding projects will help you choose based on your project needs and skills.
-
Welder Skill Level
Your experience level influences weld quality. Novices may need more practice to create clean beads. As you improve, mastering techniques like controlling travel speed and maintaining a steady hand will enhance your results. Understanding various welding positions can further elevate your skills, and knowing the differences among 1F 2F 3F 4F welding positions is essential for achieving optimal welds.
-
Ambient Temperature
Temperature affects metal behavior; warmer conditions can improve weld quality. Welding in temperatures below 50°F (10°C) can cause brittleness in the welds. Aim to maintain a stable environment when working on your panels.
-
Type Of Electrode Used
The choice of electrode affects penetration and bead shape. For example, a 7018 electrode offers better strength for thick metals, while a 6011 is suitable for rusty surfaces. Match the electrode to your materials for optimal results.
Typical Problems to Be Aware Of
Let’s look at various issues unique to fence panels.
-
Weld Cracking
Weld cracking in fence panels usually occurs due to rapid cooling. Look for gaps or lines on the weld’s surface. Resolve this by preheating the metal and welding at a steady pace.
-
Poor Penetration
Poor penetration is common in thin fence panels, leading to weak joints. Check weld consistency and increase amperage or travel speed for better results.
-
Inconsistent Weld Beads
Inconsistent weld beads may appear if the welder’s speed varies. Inspect for irregular bead height. Fix this by stabilizing your hand and maintaining a steady pace.
-
Warping Of Panels
Warping can occur in larger fence panels, often due to excessive heat. If you see buckling, pre-cool the metal before welding and use tacks to anchor it.
-
Overheating
Overheating in fence panels can cause deformation. Look for burnt areas or excessive discoloration. Repair this with proper welding techniques, like managing heat input.
Aftercare, Inspection, and Advanced Tips for Welding Fence Panels
Here’s critical advice on caring for your fence panels after welding, inspecting, and advancing your skills.
Aftercare Tips
After welding your fence panels, allow them to cool completely. This protects the metal from warping. Use a water-soluble rust inhibitor, like WD-40 (200 Ml), to treat exposed areas, extending your fence’s life by at least five years.
Inspection
Inspect the welds for penetration depth. A proper weld should penetrate at least 1.58 mm (1/16 Inch) into the base metal. Look for signs of cracking or bubbling—catching these issues early helps prevent failures. I trust using Miller’s Multimatic 220 welder during inspection checks.
Expert Tips
From one expert to another, always keep your electrode angle at 15-20 degrees for optimal penetration. Adjust your feed speed to 152 mm (6 Inches) per minute for seamless welds without burn-through. Consider using a backing bar for support; it minimizes distortion on intricate designs, promoting precision in your fence panel builds.
Advanced Techniques for Welding Fence Panels
Want to take your fence panel welding skills to the next level? Here are some advanced techniques and considerations to enhance your results.
-
Reinforcement Techniques
Consider using reinforcements for strength. Add gussets or corner braces at joints to distribute stress evenly across the panel. This simple addition can boost your fence’s durability significantly.
-
Adjustable Fixtures
Using adjustable fixtures can help maintain precise alignment while welding. These tools are handy for keeping panels level and may only cost you about $50. They save time and improve the quality of your welds.
-
Cold Welding
Cold welding involves applying pressure without heat. It’s effective for metals like aluminum in areas where you don’t want heat distortion. This method can join materials that are too thin for traditional welding.
Mathematical Considerations in Welding Fit-Up
Understanding geometry helps create a perfect fit for your panels, leading to stronger joints. Let’s break it down.
Panel Type | Angle Adjustment | Weld Size | Material Thickness |
---|---|---|---|
Square Tubing | 45° | 1/4 in (6.35 mm) | 16 GA (<0.06 in or 1.59 mm) |
Round Tubing | 90° | 3/16 in (4.76 mm) | 14 GA (<0.08 in or 2.03 mm) |
Flat Bar | 0° | 1/8 in (3.18 mm) | 3/16 in (4.76 mm) |
This table shows you how to adjust angles and sizes per your materials. Tight fittings can eliminate gaps, resulting in better weld penetration and overall strength.
Top Benefits You’ll Expect
The main advantage of learning to weld fence panels is the durability you gain. I actually used it to create a solid barrier that withstands harsh weather and wear.
Welding also offers versatility, letting you customize designs, achieve a perfect fit, and use various materials like wrought iron or pipe. Plus, it saves you money in the long run since you won’t need to buy pre-made fences or replace damaged panels often.
Use Cases Of Welded Fence Panels
I’ve known people who use welded fence panels for secure boundaries. However, they have many applications, such as:
- Commercial Security Fencing: Welded panels offer strength and durability, making them ideal for protecting warehouses and retail stores. They’re a top choice for businesses wanting to deter intruders.
- Livestock Enclosures: Farmers use welded panels to create durable animal pens. Their robust structure prevents escapes, which is crucial for livestock safety and security.
- Sports Facility Fencing: Welded panels are popular at sports complexes, providing clear boundaries for fields or courts and standing up to wear and tear from active use.
- Temporary Construction Barriers: Welded fence panels are often lightweight and movable, serving as effective safety barriers on construction sites, keeping unauthorized individuals out.
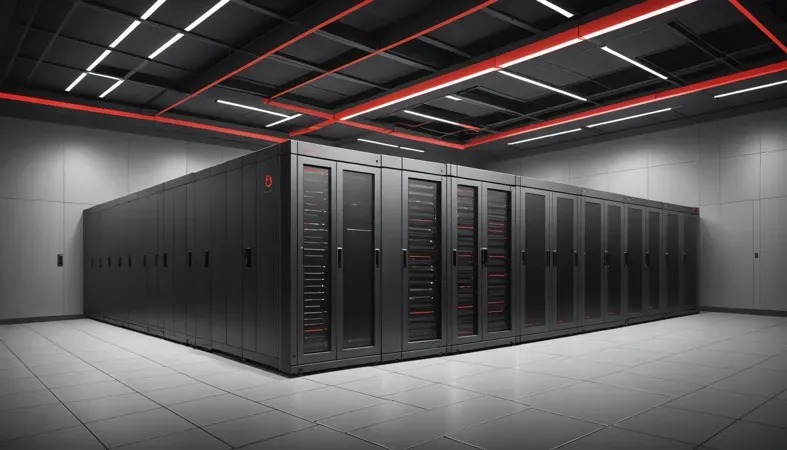
Alternatives for Welding Fence Panels
There are several methods to achieve sturdy fence panels without using conventional welding. One popular option is using a MIG welder, like the Hobart Handler 140, which provides a clean and strong finish. If you prefer something less permanent or easier to work with, consider using metal brackets and bolts, such as Simpson Strong-Tie connectors, which offer robust support.
From what I’ve encountered personally, many folks opt for epoxy or adhesive solutions, like J-B Weld, for a quick fix. These alternatives are often less labor-intensive and can save you time. They’re especially useful for repairs, giving you flexibility in how to secure your fence panels.
Frequently Asked Questions (FAQs)
Now let us look at some common questions I typically get asked.
Can You Weld a Fence Post?
Yes, you can weld a fence post. Welding provides a strong bond that helps secure the post firmly in place. Stronger joints can bear 70% more load than standard ones, ensuring your fence remains stable under varying weather conditions.
How Do You Attach Panels to a Fence?
To attach panels to a fence, you can use either welding or brackets. Welding creates a seamless join, providing durability; brackets allow for easier adjustments. Each option has its perks, but welded joins minimize movement, which can lead to damage over time.
How Far Apart Should Fence Posts Be for Welded Wire Fence?
Fence posts for a welded wire fence should be spaced approximately 6 to 8 feet (1.8 To 2.5 Meters) apart. This spacing ensures that the panels remain taut, minimizing sagging and providing solid structural integrity for the entire fence line.
Can Galvanized Fence Be Welded?
Yes, galvanized fence can be welded, but it requires removal of the zinc coating at the joint, as it can release harmful fumes. Use a grinder before welding. Proper preparation allows a strong bond, ensuring a reliable and durable fence structure.
How to Weld a Pipe Fence?
To weld a pipe fence, first, ensure proper fitting of the pipes. Use a MIG welder set at 240 amps for 3/16 inch (4.76 Mm) wall thickness. This setup ensures strong welds that enhance the fence’s overall strength and longevity.
Conclusion
We’ve made it to the end, and I hope it was helpful. We covered what fence panels are, the types of fence panels, the necessary prerequisites, the steps to weld fence panels, safety tips, and the different types of welding. We also touched on factors affecting how to weld fence panels, typical problems, aftercare, advanced tips, the benefits of welded fence panels, use cases, and alternatives for welding.
So, how to weld fence panels? It’s about understanding your materials, choosing the right type of weld, and following our step-by-step guide. If you need additional advice, I’m here to help with anything from troubleshooting issues to perfecting your welding technique.
For a deeper dive into various welding techniques and their applications, feel free to explore What is Welding.
References
- ISO. (2017). ISO 3834: Quality Requirements for Fusion Welding of Metallic Materials. Geneva, Switzerland: ISO.
- American Welding Society. (2021). AWS B2.1: Standard for Welding Procedure and Performance Qualification. Miami, FL: AWS.
Tyler is a passionate DIY welder and self-taught metal artist with years of hands-on experience transforming raw materials into functional and artistic creations. Specializing in MIG welding, Tyler crafts everything from custom furniture to outdoor sculptures, blending creativity with technical skill. Committed to making welding accessible, Tyler shares practical insights and project inspiration to help beginners and hobbyists confidently explore the world of metalworking.
DIY Projects, Fence Panels, Metalworking, MIG Welder, Safety Tips, Welding, Welding Gloves, Welding Techniques, Welding Wire