How to Replace Cab Corners Without Welding? Steps, Materials, and Tips
Published on: May 5, 2025 | Last modified: March 4, 2025
By: Mark Carter
Cab corners are the sections at the bottom rear of a vehicle’s cab. These parts often rust out, particularly in trucks, and need replacing to maintain the vehicle’s integrity.
A question that keeps coming up is how to replace cab corners without welding. It’s crucial to get this right, as poorly done cab corner replacements can lead to leaks and even more rust. I’ve seen friends struggle with this, and it’s no fun when problems arise later.
In this guide, I’ll discuss cab corner basics, types of cab corners, necessary tools, steps to replace them without welding, precautions to take, material options, factors influencing replacements, how to tackle common issues, aftercare tips, advantages of this approach, and some alternatives. You’ll even learn about how to weld a corner joint if you ever decide to go that route.
Contents
- How to Replace Cab Corners Without Welding?
- What Are Cab Corners?
- Types Of Cab Corners
- Prerequisites
- Common Tools for Replacing Cab Corners Without Welding
- Steps for Replacing Cab Corners Without Welding
- Precautions
- Types Of Materials for Replacing Cab Corners
- Factors Influencing Cab Corner Replacement
- How to Address Common Problems
- Advantages Of Replacing Cab Corners Without Welding
- Applications Of Cab Corner Replacement
- Alternatives That Might Work Better
- Frequently Asked Questions (FAQs)
- Conclusion
- References
How to Replace Cab Corners Without Welding?
Cab corners are the rear sections of your vehicle’s cab. To replace cab corners without welding, use adhesive bonding kits. These are strong and typically rated for 3,000 pounds (1,360 Kg) of shear strength, making them suitable for most applications. In welding, various issues can arise, such as crater cracks, which occur at the end of a weld and need addressing to ensure structural integrity. To explore what leads to these occurrences, you can read more about causes of crater cracks.
What Are Cab Corners?
Cab corners are the rear corners of a vehicle’s cab, where the side meets the back. These areas are usually made from 18-gauge (1.22 Mm) steel. They’re vital for structural integrity. If they rust or get damaged, serious safety issues can arise.
Replacing cab corners without welding is quite popular. You can use adhesive methods and patch panels to save time and reduce costs. I once replaced cab corners on an old truck using non-welding methods, and it made a significant difference.
While working on that truck, I used a 3M adhesive to bond the patch. It held strong and created a clean finish. This experience highlighted the importance of understanding various repair techniques, such as the difference between welding and adhesive methods for cab corners.
Types Of Cab Corners
What are the types of cab corners for replacement without welding?
-
Factory Cab Corners
Factory cab corners are original parts made by the vehicle manufacturer. To replace these without welding, use adhesive bonding. Clean the surface, apply a strong automotive adhesive, and press the new corner into place securely for a lasting hold.
-
Aftermarket Cab Corners
Aftermarket cab corners are produced by third-party companies and fit various models. You can replace aftermarket corners without welding by using self-tapping screws. Start by aligning the corner, drilling pilot holes, and then fasten it securely with screws for a tight hold.
-
Custom Cab Corners
Custom cab corners are tailored for specific vehicle designs. To replace a custom corner without welding, use 3M panel adhesive. First, remove the damaged section, clean the substrate, apply adhesive, and set the custom corner in place for a strong solution.
-
Pre-fabricated Cab Corners
Pre-fabricated cab corners are ready-made parts designed to fit multiple vehicles. Install these without welding by using liquid nails or construction adhesive. Ensure the surface is clean, apply adhesive generously, and carefully position the corner, pressing firmly for a strong bond.
-
Universal Cab Corners
Universal cab corners are generic options that can adapt to many trucks. For this type, use clamping techniques instead of welding. Cut to size, position the corner, and clamp it in place while using a polyurethane adhesive to secure it.
We’ve wrapped up the different Types of Cab Corners here. Next up, we’ll look at necessary Prerequisites.
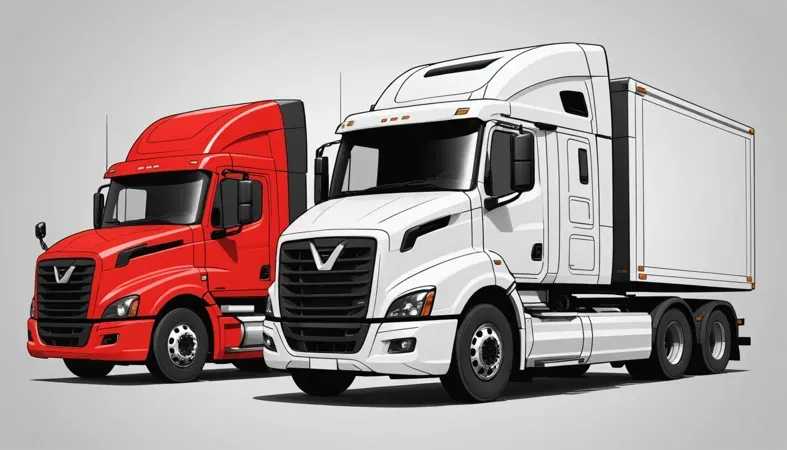
Prerequisites
What do you need to get started?
- Fiberglass Reinforcement Tape: You need a product like 3M 03440. It’s essential for strengthening your cab corners before applying filler.
- Auto Body Filler: A product such as Bondo 907 is crucial for smoothing and finishing those corners after repairs.
- Epoxy Adhesive: Use a product like Eastwood 2-Part Epoxy to securely bond repairs and prevent rust.
- Plastic Covering: Consider a plastic tarp to protect your vehicle’s interior during the repair process.
We’ve wrapped up the prerequisites for the project here. Next up, we’ll look at common tools for replacing cab corners.
Common Tools for Replacing Cab Corners Without Welding
Using the right tools can make the process simpler and more effective. Here’s a list of essential tools that will help you replace cab corners without welding.
Tool | Description | Purpose |
---|---|---|
Angle Grinder | A powerful tool with a rotating disc. | To cut out damaged cab corners and prepare surfaces. |
Rivet Gun | A handheld tool that inserts rivets. | To secure patches if adhesives are not sufficient. |
Utility Knife | A sharp knife for cutting materials. | For trimming patch materials to size. |
Hand Sanding Block | A block used for manual sanding. | To smooth edges and surfaces before adhesive application. |
Caulk Gun | A tool that dispenses adhesive or sealant from a tube. | For applying adhesive evenly for repairs. |
Moisture Meter | A device used to measure moisture content. | To check for remaining moisture before applying adhesives. |
We’ve wrapped up common tools for cab corner replacements without welding. Next up, we’ll look at the steps for replacing them.
Steps for Replacing Cab Corners Without Welding
Here are the steps to install cab corners without welding—be sure to follow them!
-
Prepare the Work Area
Start by clearing your workspace. Ensure you have enough room to move around without bumping into anything. A clean area helps you focus and avoid accidents. You’ll also need proper lighting to see every detail.
I recommend laying down a tarp to catch any debris as you work. This keeps your area clean and helps you see what you’re doing. You don’t want to trip over scrap parts!
-
Remove Old Cab Corners
First, remove the damaged cab corners. Use a grinder or cutting wheel to cut along the edges, going about 1 inch (2.54 Cm) into the solid part of the cab. This removes all rust and corrosion.
Carefully detach the old corner piece with prying tools or a hammer. I once rushed this step and tore the surrounding metal. Take your time and wear protective gear.
-
Fit New Cab Corners
Next, take your new cab corners and place them against the cab to check the fit. Ensure they align well with the existing body lines for a seamless look. If they don’t fit snugly, trim them slightly for a perfect fit.
After confirming everything matches, mark where the new corners will attach. Be precise! Leave about a 1/4 inch (0.635 Cm) overlap on the seams for better adhesion.
-
Secure New Cab Corners
Now, attach your new cab corners. Use automotive adhesive suitable for metal; this provides a strong grip without welding. Apply a generous amount and press the new corner into place firmly.
For added hold, you can use screws alongside the adhesive. Be sure to use stainless steel screws to prevent rust. You want this to last, since replacing cab corners can be costly!
-
Finish and Inspect the Installation
After securing the corners, let the adhesive cure for the recommended time on the product’s instructions, usually 24 hours. During this time, double-check that everything looks good and there are no gaps.
Once cured, sand any rough edges and apply rust-proof paint to further protect your new cab corners. Make your ride look sharp!
We have now covered steps for replacing cab corners without welding. Next, we will examine important precautions to consider.
Precautions
Let’s cover the safety tips for removing cab corners.
- Wear Protective Gear: Always wear gloves and safety goggles to protect against sharp tools and metal debris.
- Verify Tool Condition: Regularly check your tools for damage. A broken tool can cause injury; use brands like DeWalt or Milwaukee.
- Work in a Ventilated Area: Ensure good airflow to avoid inhaling fumes. Choose a location with effective air circulation; around 2-3 fans should suffice.
- Stay Organized: Keep the workspace tidy. Clutter can lead to accidents; use a sturdy toolbox, like a Husky, for storage.
Remember, safety should never take a back seat; let’s keep you safe!
Types Of Materials for Replacing Cab Corners
Let’s discuss the types: Fiberglass Panels, Steel Overlays, Aluminum Sheets, Composite Materials, and Plastic Inserts.
-
Fiberglass Panels
Fiberglass panels are lightweight and rust-resistant. They’re often pre-formed for easier installation. You can find panels that fit your cab corners, generally about 1/8 inch (3.2 Mm) thick.
-
Steel Overlays
Steel overlays provide durability and strength. They can be made from 16- to 18-gauge steel, adding extra protection. These overlays bond directly to existing corners with adhesives, so you won’t need to weld. If welding cannot be avoided, it is important to know how to prevent inhaling welding fumes.
-
Aluminum Sheets
Aluminum sheets are lightweight yet strong. They resist corrosion and come in various thicknesses, typically about 0.040 inches (1 Mm). You can shape them around cab corners with screws, allowing for an adjustable replacement method without welding.
-
Composite Materials
Composite materials combine plastic and fiberglass for a strong solution. Commonly used in marine applications, they resist water damage as well. At about 1/4 inch (6 Mm) thick, they also perform well in tough environments.
-
Plastic Inserts
Plastic inserts are a quick fix for minor damage. They’re flexible, inexpensive, and usually made from durable polyethylene. Simply slide them into place—no welding needed.
Factors Influencing Cab Corner Replacement
What factors influence replacing cab corners without welding?
-
Material Quality
High-quality materials ensure longevity. Steel components should have at least 15-20% tensile strength for durability.
-
Existing Rust Damage
Severe rust can weaken the structure, often requiring replacement of larger sections—up to 30% more than planned.
-
Environmental Conditions
Replacing cab corners during rainy weather can be a mistake. Humidity can hinder adhesive bonding and cause premature failure.
-
Availability Of Tools
Access to specialized tools is crucial. A lack of tools like grinders or adhesives can increase the time needed by 25% or more.
-
Skill Level Of the Installer
An experienced installer will complete the job up to 50% faster than an amateur. Skills directly affect the finish and safety.
How to Address Common Problems
Let’s look at some technical issues related to cab corners.
-
Poor Fit Of New Corners
Cab corners often don’t fit well due to manufacturing tolerances. Measure closely—1/16 inch (1.5 Mm) gaps can lead to cracks. Use body shims for adjustments. Ensure a tight fit before welding.
-
Adhesive Failure
Cab corners can loosen if adhesives fail. I once used a low-grade adhesive by mistake. Look for delamination. Use a stronger epoxy or consider riveting as an alternative method.
-
Remaining Rust Spots
Cab corners may still have rust after replacement. Inspect closely, especially at least 1 inch (2.5 Cm) from the edges. Sandblast or use rust converter before installation.
-
Moisture Trapping
If cab corners lack drainage, moisture can get trapped, leading to decay. Check drainage holes—.187 inch (4.8 Mm) is ideal. Punch holes if missing—it’s a simple fix!
-
Structural Integrity Issues
Cab corners must support weight. Inspect for flex—any bending is a red flag. Reinforce with additional metal supports if needed. Remember, stability is key!
Advantages Of Replacing Cab Corners Without Welding
The primary benefit of replacing cab corners without welding is simplicity. When I worked on a classic truck restoration, I chose this method for its ease of installation and clean finish.
Moreover, this method reduces the need for specialized equipment and skills. You’ll save time, cut costs, avoid warping metal, and gain more flexibility in your repairs.
Applications Of Cab Corner Replacement
I’ve seen people use alternatives to welding for cab corner replacement. This method has various unique applications, including:
- Semi-truck Restoration: It’s commonly used to restore older semi-trucks. Many owners choose this method to save costs and preserve the truck’s original value.
- Custom Hot Rod Builds: Builders often use cab corners for customizations, ensuring a sleek appearance while avoiding the complexity of welding.
- Body Shop Repairs: Some auto body shops prefer this method for quicker repairs, allowing them to turn cars around faster without compromising quality.
- DIY Enthusiasts: Hobbyists appreciate this approach for enhancing their trucks at home, avoiding the need for specialized welding skills or equipment.
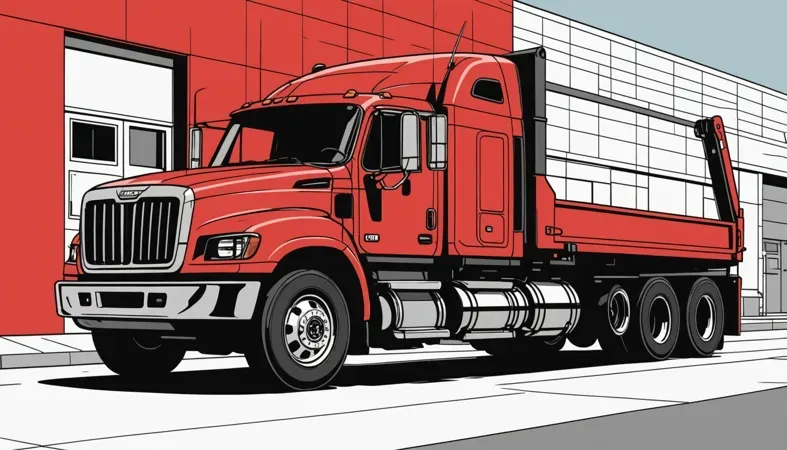
Alternatives That Might Work Better
There are other methods to tackle your cab corner repair. For example, consider using panel bonding adhesives like 3M Panel Bonding Adhesive. This product works great for securing metal and plastic without welding. It’s ideal if you want to avoid heat damage or distortion in the surrounding area.
You can also explore using slip-on cab corners or replacement panels designed for non-welding installation. Companies like LMC Truck offer these parts for popular models. They make installation faster and can deliver solid results, especially if you’re dealing with rust issues. For those tackling projects that require specialized techniques, mastering the art of welding upside down can be invaluable.
Frequently Asked Questions (FAQs)
Now let us look at some common questions. I typically get asked about cab corners and welding techniques.
How Much Does It Cost to Replace Cab Corners?
Replacing cab corners typically costs between $200 and $600 USD. This price includes parts and labor. Additional costs arise if you’re hiring a professional, as labor rates can range from $50 to $150 per hour depending on your location.
Is It Better to Weld or Glue Rocker Panels?
It’s generally better to weld rocker panels than to glue them. Welding provides a more durable and lasting bond, essential for structural integrity. Glue can cost less but might not hold up under stress, which is crucial in auto repairs. When removing previous welds to ensure a clean installation, it’s important to know how to cut welds effectively.
What is the Cheapest Way to Fix Rusted Rocker Panels?
The cheapest way to fix rusted rocker panels is to use rust converter along with some patching techniques. This method can cost as little as $50 USD for materials. However, this solution may not be as long-lasting as replacing the panel completely.
Do You Have to Weld Rocker Panels?
No, you don’t have to weld rocker panels, but welding is highly recommended for a stronger repair. Alternative methods, such as using adhesives, might save money but could lead to weaker joints that may fail over time.
How to Weld a Corner Joint?
Welding a corner joint involves securing the metal pieces at a right angle and then running the weld along the edge. For best results, practice with your welder’s settings to achieve the right penetration, which should be about 1.6 to 3.2 mm (1/16 to 1/8 Inches). A thorough understanding of electrode classification can help ensure proper metal fusion and welding stability; discover what electrode classification E316-16 means for welders by clicking here.
What Does It Mean to Wrap Your Corners in Welding?
Wrapping your corners in welding means completing the weld around all edges of the joint. This technique increases strength and helps prevent weakening caused by fatigue over time. It’s a good practice, especially for structural components. Mastering techniques to enhance visual accuracy can significantly improve your work quality, so it’s worth exploring how to see better when welding.
How to Weld Cab Corners?
Welding cab corners involves cutting out the old sections and fitting new metal in place. Ensure you grind the surrounding area to remove rust and paint for a solid weld. Use proper settings and filler material for effective penetration and a smoother finish.
How to Tig Weld Inside Corners?
TIG welding inside corners requires precise control and technique. Use a small diameter tungsten electrode to access tight spaces and maintain a steady speed to avoid burning through. Keep your filler material in the right position for a strong bond.
Conclusion
Phew, we covered a lot. We discussed cab corners, the types of cab corners, prerequisites for the job, effective steps for replacement without welding, necessary precautions, suitable materials, factors influencing replacement, how to tackle common problems, and aftercare tips. Plus, we explored the advantages and applications of replacing cab corners without welding, along with some alternatives.
I trust these insights have been helpful in answering how to replace cab corners without welding. Use the right materials, follow those detailed steps, and pay attention to precautions to ensure a successful repair. With the right approach, you can tackle cab corners effectively – no welding required.
If you’d like to delve deeper into related topics, What is Welding is an excellent resource to explore further.
References
- ISO. (2017). ISO 3834: Quality Requirements for Fusion Welding of Metallic Materials. Geneva, Switzerland: ISO.
- Cary, H. B., & Helzer, S. C. (2005). Modern Welding Technology (6th ed.). Upper Saddle River, NJ: Pearson.
- Little, R. L. (1999). Welding and Welding Technology. New York, NY: McGraw-Hill Education.
Mark is a skilled welding engineer specializing in advanced metal joining technologies and process design. With a formal education in welding engineering and a background rooted in practical experience, Mark bridges the gap between theory and application. He is passionate about making technical concepts accessible, empowering welders to embrace innovation while mastering essential skills. Mark combines his scientific expertise with a commitment to supporting the welding community alongside his uncle, Joe.
Adhesive Bonding, Auto Repair, Cab Corners, DIY Vehicle Maintenance, Rust Prevention, Safety Tips, Structural Integrity, Welding, Welding Alternatives, Welding Techniques