Can You Weld Stainless Steel? Overview, Methods, Techniques
Published on: May 23, 2025 | Last modified: March 4, 2025
By: Joe Carter
If you are curious about can you weld stainless steel, you’re not alone. Knowing how to properly weld stainless steel is crucial for achieving strong, long-lasting joints. In my experience, following best practices during welding really makes a difference in quality and prevents issues down the line.
In this guide, I’ll cover what stainless steel is, types of stainless steel and their weldability, essential prerequisites, steps for welding, safety tips, types of welding for stainless steel, factors affecting welding, typical issues you might face, as well as aftercare, inspection, and advanced tips. I’ll also touch on the benefits of welding stainless steel, applications you should know about, and some alternatives to welding stainless steel.
Contents
- Can You Weld Stainless Steel?
- What is Stainless Steel?
- Types Of Stainless Steel and Their Weldability
- Essential Prerequisites to Get Started
- Safety Tips
- Steps for Welding Stainless Steel
- Types Of Welding for Stainless Steel
- Factors Affecting Welding Stainless Steel
- Typical Issues With Welding Stainless Steel
- Welding Stainless Steel: Best Practices for Success
- Benefits Of Welding Stainless Steel
- Applications You Should Know About
- Are There Any Alternatives to Welding Stainless Steel?
- Frequently Asked Questions (FAQs)
- Conclusion
- References
Can You Weld Stainless Steel?
Yes, you can weld stainless steel. It’s a bit tricky due to its high heat conductivity, but using TIG or MIG welding works best. Always keep the workspace clean to avoid contamination.
What is Stainless Steel?
Stainless steel is an alloy made primarily of iron, with at least 10.5% chromium by weight. This chromium content forms a passive layer of chromium oxide on the surface, giving it corrosion resistance. Stainless steel can also contain nickel, molybdenum, and other elements to enhance its properties. Generally, it has a tensile strength of about 520 MPa (75,000 Psi) and a melting point ranging from 1400°C to 1450°C (2550°F to 2640°F), depending on its composition.
So, can you weld stainless steel? I’ve done it many times in my career. The process can be tricky if you’re not familiar with the material’s properties. You must carefully prepare the weld joint to ensure a solid, durable connection.
It was very helpful in a recent project that required joining stainless steel to carbon steel. I learned that you can weld stainless to carbon steel, but it requires special kits and precautions. This knowledge helped me avoid costly mistakes and ensure a clean joint, which is crucial for maintaining structural integrity and corrosion resistance.
Types Of Stainless Steel and Their Weldability
What are the types of stainless steel, and how do they handle welding?
-
Austenitic Stainless Steels
Austenitic stainless steels have high corrosion resistance and excellent weldability. You can join these types easily. To weld them effectively, you might want to consider various techniques outlined in the stainless steel welding resources. For this process, use a MIG (Metal Inert Gas) welder with a filler wire like ER308L, and set the argon gas at 15-20 cubic feet per hour (Cfh) for better shielding.
-
Ferritic Stainless Steels
Ferritic stainless steels contain less nickel and offer good resistance to stress corrosion. You can weld these, but do so with caution. Utilize the SMAW (Shielded Metal Arc Welding) process with an E309L electrode, and preheat workpieces thicker than 3 mm (0.12 Inches).
-
Martensitic Stainless Steels
These steels are strong and wear-resistant, but less resistant to corrosion. You can definitely weld them. Preheat using a torch and use an E7018 electrode for stick welding, maintaining a 4°C (40°F) heat for best results. For those looking to perfect their technique, exploring heliarc welding methods can be particularly beneficial.
-
Duplex Stainless Steels
Duplex stainless steels combine austenitic and ferritic properties for added strength. Yes, these can be welded. For welding, an E2209 filler is recommended; keep travel speeds slow to avoid overheating.
It’s critical to consider safety when welding materials like galvanized steel due to potential health risks from fume exposure. Learn more about welding galvanized steel dangers.
-
Precipitation-hardening Stainless Steels
These heat-treatable steels gain strength through aging. You can weld them, but you need to be cautious. Use a TIG (Tungsten Inert Gas) welder with a filler rod like 660, and preheat to prevent cracking. Understanding the best welding by metals can significantly improve your results.
For those working with specific materials like thermocouples, it’s essential to understand the proper techniques for welding thermocouple wire.
You should now have a good understanding of stainless steel types and their weldability. In the next part, we’ll discuss essential prerequisites to get started.
Essential Prerequisites to Get Started
What do you need to weld stainless steel?
- MIG Welder: You need a machine like the Hobart Handler 190. It’s essential for delivering the precise heat required for stainless steel.
- Argon Gas: You need a mix of 75% Argon and 25% CO2, often sold as C25. This gas protects your weld from contamination.
- Stainless Steel Filler Rod: A rod such as ER308L is necessary for a strong bond. It matches the composition of the stainless steel you’re welding.
- Welding Brush: Get a stainless steel brush, like one from Lincoln Electric. It’s crucial for cleaning the surface before welding to ensure a good fit.
You should now have a good understanding of the essential prerequisites needed to begin. In the next part, we’ll discuss safety tips.
Safety Tips
Let’s cover essential precautions when welding stainless steel.
- Personal Protective Equipment (PPE): Always wear protective gear like gloves and goggles. I recommend the 3M 9010 respirator for safety.
- Ventilation: Keep the work area well-ventilated to avoid harmful fumes. Aim for at least 500 cubic feet per minute (Cfm) of airflow.
- Inspect Equipment: Regularly check your welding machine and cables. It’s a good practice to check for wear every month.
- Stable Workspace: Ensure your work surface is firm and clean. Ideally, worktable height should be waist high for comfort.
Remember, prioritizing these safety tips is crucial for your well-being.
We covered essential safety tips here. Next, we will cover steps for welding stainless steel.
Steps for Welding Stainless Steel
Here are the steps for welding stainless steel effectively. Follow these steps for solid welds.
-
Clean the Surface
Start by thoroughly cleaning the stainless steel. Dirt, oils, and contaminants can affect your weld. Use a stainless steel brush or grinder to clean the weld area, ensuring it’s free from grime. A clean surface reduces the risk of weld defects and improves adhesion.
Note that different stainless steels, like AISI 304 and 316, may require specific preparation methods. For example, 316 contains molybdenum, which can create nodules if not cleaned properly. Take your time here; it pays off later.
-
Choose Your Welding Method
Select a welding process suitable for stainless steel. You can use MIG, TIG, or stick welding, depending on your skill level and equipment. MIG welding is often easier for beginners, while TIG offers precision. Each method has different settings; for MIG, a voltage of 23-25 volts is standard.
If you choose stick welding, use a 308L stainless steel electrode, designed for stainless with a good balance of strength and corrosion resistance. Consider the material’s thickness as well.
-
Adjust Your Settings
Your welder’s settings must match the stainless steel type and thickness. For example, weld 3 mm (1/8 Inch) thick stainless at around 120 amps. Adjust your wire feed speed accordingly; about 350 inches per minute is standard.
Improper settings can lead to undercutting or burn-through. I once used a wire feed that was too high with 316 and burned the edge badly. Remember, practice makes perfect; test settings on scrap material first.
-
Weld With Consistency
When you’re ready to weld, ensure a consistent travel speed. Move at a steady pace; a speed of about 6-8 inches per minute often works well for thin stainless. Don’t linger too long in one spot to avoid overheating the steel.
Maintain a travel angle of about 15 degrees toward the direction of the weld. Staying consistent with your angle helps achieve a smoother bead. Pay attention to the puddle; it provides valuable feedback on the weld’s progress!
-
Test Your Welds
Once you finish welding, inspect your work. Look for a uniform appearance and any signs of defects like cracks or lack of fusion. A good weld should be smooth and shiny.
If you notice any issues, address them right away. Don’t skip this step! I regretted ignoring bad spots once, and it caused problems later during testing. Fix it now, and you’ll save headaches later.
That covers the steps for welding stainless steel. Let’s now take a look at the various types of welding for stainless steel.

Types Of Welding for Stainless Steel
Let’s explore the main types of welding for stainless steel: TIG, MIG, Stick, Laser, and Plasma Arc welding.
-
TIG Welding
TIG (Tungsten Inert Gas) welding uses a non-consumable tungsten electrode to produce the weld. You can precisely control the heat, making it excellent for thin materials. This method creates high-quality, clean welds on stainless steel.
-
MIG Welding
MIG (Metal Inert Gas) welding employs a continuously fed wire electrode. It’s fast and versatile, suitable for thicker stainless steel sections, and allows you to adjust the wire diameter for various thicknesses.
-
Stick Welding
Stick welding, or SMAW (Shielded Metal Arc Welding), uses a consumable electrode coated in flux. It’s simple and requires minimal equipment. Yes, you can stick weld stainless steel, especially outdoors or in windy conditions. However, it’s crucial to recognize the dangers of welding without proper protective gear. Understanding what happens if you weld without a mask highlights the importance of safety equipment.
-
Laser Welding
Laser welding uses a focused beam of light to melt stainless steel. This process allows deep penetration and incredible precision. It’s often used in high-speed applications but requires specialized equipment and skills.
-
Plasma Arc Welding
Plasma Arc Welding (PAW) is similar to TIG but uses a plasma torch, offering better control and higher temperatures. It produces tighter welds and a more focused arc, making it ideal for thick stainless steel sections. Though it’s less common in home shops, it’s powerful in industry.
Choosing the right welding technique is key. Here’s a quick breakdown:
Welding Method | Best For | Pros | Cons |
---|---|---|---|
TIG Welding | Thin Sheets | High-quality, minimal spatter | Slower, requires skill |
MIG Welding | Thicker Metals | Speed, ease of use | More cleanup needed |
Stick Welding | Outdoor Conditions | Portable and simple | Dirty appearance |
Laser Welding | Precision Work | Deep penetration, fast | Expensive equipment |
Factors Affecting Welding Stainless Steel
What factors determine if you can join stainless steel successfully?
-
Material Thickness
Thicker stainless steel needs more heat to melt properly. Generally, materials over 3 mm (1/8 Inch) may require special techniques like TIG (Tungsten Inert Gas) welding.
-
Welding Speed
Welding too fast can result in weak joints, while too slow may cause burn-through. Aim for a steady pace—about 5 to 10 inches per minute (12.7 To 25.4 Cm) is ideal.
-
Heat Input
The right heat input is crucial. Excessive heat can warp the stainless steel’s composition, affecting corrosion resistance. Use about 1.5 to 2.5 kJ/cm for optimal results.
-
Pre-welding Treatment
Cleaning surfaces before welding is essential. Removing contaminants like oil and grease increases the chances of a strong bond, especially for metal joints.
-
Filler Material Compatibility
The choice of filler material is key. Using the wrong filler can create weak points—use compatible alloys like ER308 for austenitic stainless steel.
Typical Issues With Welding Stainless Steel
Here are some common problems encountered when welding stainless steel.
-
Corrosion Resistance Loss
Welding stainless steel can result in loss of corrosion resistance due to heat and contamination. Check for rust spots to identify this issue. To resolve it, use anti-corrosive fillers and ensure the base metal is clean.
-
Inconsistent Heat Distribution
Welding stainless steel often suffers from inconsistent heat distribution, which can create weak joints. Spot this issue through visual inspection. Adjust your welding parameters to ensure even heat flow.
-
Weld Cracking
Weld cracking in stainless steel occurs due to rapid cooling. Inspect weld areas for fractures to identify it. Preheat the steel before welding and use low-hydrogen rods to remedy this.
-
Discoloration After Welding
Welding stainless steel may cause discoloration, such as rainbow hues, due to chromium carbide precipitation. Inspect the joint for color changes. Clean with pickling paste to restore appearance.
-
Difficulty With Post-weld Cleaning
Post-weld cleaning of stainless steel can be challenging. Residues may be tough to remove. Check for visible residue to identify this issue. Use specialized cleaners and abrasives for effective cleaning.
Welding Stainless Steel: Best Practices for Success
Let’s dive into advanced techniques and best practices for welding stainless steel effectively.
Key Considerations for Perfect Welds
Here are essential factors to remember while welding:
- Heat Management: Maintain proper heat levels. Too much can warp stainless steel, while too little can lead to weak welds. Aim for 1.5-2.5 kJ/cm.
- Travel Speed: Keep a steady pace of about 5-10 inches per minute (12.7 to 25.4 cm). Consistency is crucial for a good bond.
- Purging Techniques: For thicker materials, use argon back purging to protect the underside of the weld from oxidation.
Post-Weld Maintenance
After welding, proper care ensures longevity:
- Cleaning: Use vinegar and water immediately to remove contamination.
- Inspection: Check for cracks and corrosion. A good weld should appear smooth and shiny.
- Corrosion Prevention: Apply inhibitors like WELEDA for Metal to shield against rust.
Expert Tips
Here’s a pro tip: adjust your heat settings to between 135°C (275°F) and 426°C (800°F) to avoid redox issues. Implement a back purging technique when welding metals thicker than 5mm to keep the weld pool balanced. Using an argon flow of 15 Cubic Feet per Minute (CFM) improves gas coverage during critical joint areas.
Benefits Of Welding Stainless Steel
The biggest benefit of welding stainless steel is its durability. I found it very helpful for a project requiring corrosion resistance in a humid environment.
You also gain enhanced strength, rust resistance, and aesthetic appeal. It maintains its integrity at high temperatures, and it’s easy to clean and maintain.
Applications You Should Know About
People use stainless steel in various industries. Its applications include:
- Aerospace Components: Used in aircraft frames and engines. Its corrosion resistance is crucial for safety at high altitudes and is popular in aviation.
- Food Processing Equipment: Essential for mixers and tanks, it prevents contamination and maintains hygiene. Common in restaurants and food factories.
- Marine Structures: Used in boats and docks, stainless steel withstands saltwater corrosion, which is vital for longevity. Common in coastal areas.
- Automotive Exhaust Systems: Found in exhaust pipes and manifolds for its heat and rust resistance. Popular in high-performance cars.
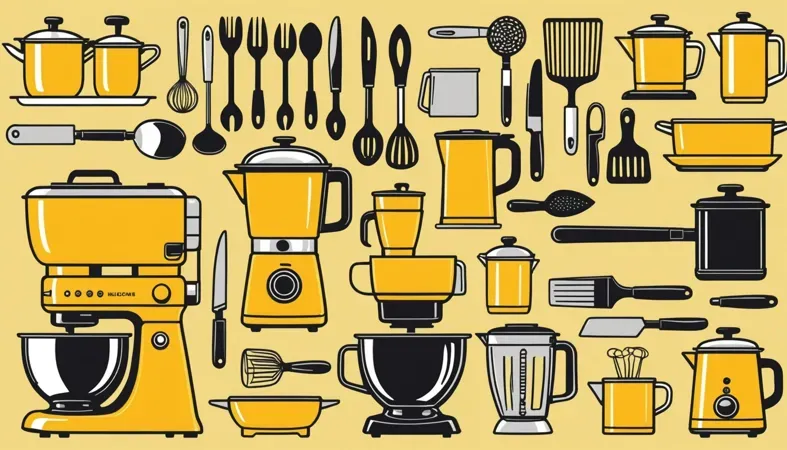
Are There Any Alternatives to Welding Stainless Steel?
Some alternatives to welding include using adhesives, brazing, and mechanical fastening. Adhesives like Loctite or epoxy can bond stainless steel effectively, especially in low-stress applications. This method may be preferred when heat from welding might warp the metal or cause discoloration.
Brazing involves a filler material with a melting point above 450 °C (840 °F), such as silver or copper alloys, creating a strong joint. You might choose this method when joining stainless steel to dissimilar metals, like aluminum, since it’s less invasive. For certain projects, mechanical fasteners like bolts and screws provide a reliable and easy-to-implement solution.
Frequently Asked Questions (FAQs)
Now let us look at some questions I typically get asked.
Is It Difficult to Weld Stainless Steel?
Yes, it is difficult to weld stainless steel. Stainless steel requires precise technique and settings due to its low thermal conductivity, which affects heat distribution. If not done right, you might face issues like warping or cracking during the process. For those interested in exploring the safe observation of solar eclipses, there are options to view an eclipse safely with a welding mask.
What Kind Of Weld Do You Use on Stainless Steel?
You typically use TIG (Tungsten Inert Gas) or MIG (Metal Inert Gas) welding for stainless steel. TIG gives you better control over the weld and is great for thin materials, while MIG offers speed and is effective for thicker sections.
Can You Weld Stainless With Regular MIG Wire?
No, you can’t weld stainless with regular MIG wire. Standard wire is not optimized for the unique properties of stainless steel, which could lead to poor bonding and rust issues. Use specific stainless steel wire for best results.
Can You Weld Stainless Steel to Carbon Steel?
Yes, you can weld stainless steel to carbon steel, but special considerations are needed. Using the right filler material is crucial to avoid potential corrosion problems that can arise from different base metals.
When working with thinner materials, it’s essential to know how to weld 16 gauge sheet metal effectively using appropriate techniques and equipment.
Can You Stick Weld Stainless Steel?
Yes, you can stick weld stainless steel. Stick welding (SMAW) is practical for various stainless steel thicknesses. It’s a portable option, but it does require skill to manage changes in properties of the two metals during the process.
Can You Weld Stainless Steel to Regular Steel?
Yes, you can weld stainless steel to regular steel by using proper techniques and filler materials. It’s essential to manage heat input and use compatible weld rods to prevent issues like brittleness and corrosion.
Conclusion
I’m glad we could cover this together. We discussed the various types of stainless steel and their weldability, essential prerequisites to get started, steps for welding, and safety tips. Additionally, we touched on the types of welding suitable for stainless steel, factors affecting welding, typical issues you might face, aftercare, as well as benefits and applications of welding stainless steel.
So, can you weld stainless steel? Yes, you definitely can. It’s crucial to choose the right type of stainless steel, like austenitic, preferred for its good weldability, and understand techniques like TIG or MIG welding. If you need additional advice, I’m here to help with questions about welding stainless to steel, carbon steel, or anything else you might want to know.
For further insights and information, feel free to check out What is Welding, your comprehensive resource on all things related to welding.
References
- Schweitzer, P. A. (2007). Metallic Materials: Physical, Mechanical, and Corrosion Properties. New York, NY: CRC Press.
- American Welding Society. (2020). AWS A3.0: Standard Welding Terms and Definitions. Miami, FL: AWS.
Joe Carter is a retired welding professional with over 40 years of hands-on experience in the industry, spanning ship repair, structural welding, and even underwater projects. Joe is a master of MIG, TIG, and Stick welding. Passionate about mentoring the next generation of welders, Joe now shares his decades of expertise and practical insights to help others build rewarding careers in welding.
American Welding Society, Metalworking, MIG Welding, Safety Tips, Stainless Steel, TIG Welding, Welding, Welding Techniques, Wire Diameter