What is Voltage in Welding? Understanding Settings, Types, and Importance
Published on: May 26, 2025 | Last modified: March 4, 2025
By: Joe Carter
Voltage is the electrical force that drives the current through a circuit. Think of it as the pressure that pushes electrons, helping them move along a wire.
A question that keeps coming up is, what is voltage in welding? Understanding voltage in welding is crucial for a stable arc and quality welds. From my experience, sticking to the right settings can save you time and material—no one wants to redo a job because the voltage wasn’t right!
In this guide, we’ll explore what voltage is in welding, how it works, types of welding voltage, steps for setting it, factors that affect it, common issues, aftercare, advanced tips, typical uses, and some alternatives. You’ll also learn how to check voltage on a welding machine and how much voltage is needed for best results.
Contents
- What is Voltage in Welding?
- How Does Voltage in Welding Work?
- Types Of Voltage in Welding
- Steps for Setting Voltage in Welding
- Relation Between Voltage and Amperage in Welding
- Factors That Affect Voltage in Welding
- Typical Problems to Be Aware Of
- Aftercare, Inspection, and Advanced Tips for Voltage in Welding
- Typical Uses Of Voltage in Welding
- Frequently Asked Questions (FAQs)
- Conclusion
- References
What is Voltage in Welding?
Voltage in welding measures the electric potential that drives the welding arc. It’s crucial for controlling arc length and weld penetration. Typically, 20-30 volts is used for arc welding to ensure strong joints.
How Does Voltage in Welding Work?
Voltage in welding is the electrical force that pushes electrons through the welding circuit. It’s measured in volts (V), indicating the potential difference between two points. The open circuit voltage (OCV) typically ranges from 20 to 100 volts (V), depending on the process. Higher voltage can create a stronger arc, but it’s crucial to balance voltage and amperage for optimal results.
Understanding how voltage interacts with current is essential. Different welding techniques require specific voltages. For instance, arc welding often needs 20 to 40 volts (V) for a stable arc, while MIG welding requires around 24 to 30 volts (V) for consistency.
To measure voltage correctly on your welding machine, use a multimeter. Check how many volts your machine generates before starting a project. It’s vital to use the right voltage to avoid issues like arc instability or burn-through.
Types Of Voltage in Welding
What are the different types of voltage?
-
Low Voltage
Low voltage ranges from 10V to 30V (Volts). It helps initiate and stabilize the arc. Set your welder for lower energy input to control heat and prevent burn-through on thin materials.
-
Medium Voltage
Medium voltage falls between 30V and 80V. This range balances performance for various projects. Set your welder to about 50V for effective results on tape or rods, minimizing splatter and improving puddle control. Understanding this adjustment is crucial for achieving quality results and knowing what constitutes a weld enhances your overall welding technique.
-
High Voltage
High voltage ranges from 80V to over 200V. It’s necessary for processes like TIG or MIG welding. Adjust your welder’s output based on material thickness for deeper penetration and stronger joints.
-
Direct Current Voltage
Direct current (DC) voltage provides a steady flow for welding, allowing more control and better penetration. Select the DC option on your welder for improved arc stability and cleaner welds on steel or stainless steel. For a deeper understanding of welding techniques, explore what does a good weld look like in detail.
-
Alternating Current Voltage
Alternating current (AC) voltage cycles current flow multiple times per second, making it ideal for aluminum welding. Ensure your welder has the correct settings to effectively break up oxides on aluminum for cleaner welds and increased efficiency.
We’ve wrapped up the various Types of Voltage in Welding here. Next up, we’ll look at the Steps for Setting Voltage in Welding.
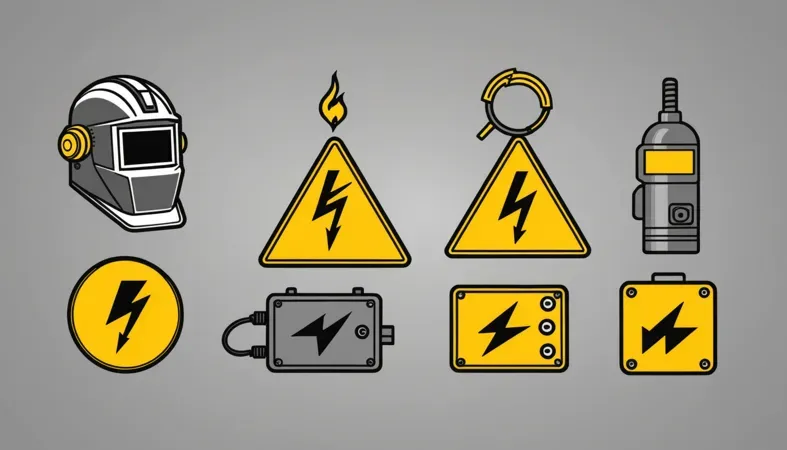
Steps for Setting Voltage in Welding
Now, we’ll cover the essential steps to set voltage in welding effectively.
-
Determine Material Type
Identify the material you’re working with. For example, mild steel needs about 20–25 volts (V) to weld, while aluminum requires 15–20 V. Material thickness matters too; thicker materials usually need more voltage. Adjust your settings based on material and thickness. Additionally, knowing the quantity and type of welding rods required can greatly impact your project’s success. Understand more about 1/8 7018 welding rods per pound.
Keep in mind that different metals have different melting points. Knowing this ensures a stable arc and helps prevent burn-through. If you’re welding stainless steel, aim for about 25 V, while brass may only need around 15 V. Understanding your material is critical to achieving a clean weld.
-
Select Welding Process
Choose your welding process—MIG, TIG, or Stick. Each process has a preferred voltage range. For instance, a MIG welder typically runs on 18–30 V, whereas TIG often operates between 10–20 V. Your selection affects your voltage settings. Choose a process based on your project and expertise.
Factors like joint configuration and desired penetration depth also influence your voltage setting. Using the wrong voltage can lead to problems like excessive spatter or weak welds. Familiarize yourself with each welding process to better understand its voltage requirements. A crucial aspect of welding involves mastering various techniques, such as 3G welding positions.
-
Adjust Voltage Settings
Set the machine’s voltage according to your chosen welding process and material type. For MIG, if you’re welding thin steel (About 3 Mm or 1/8 Inch), aim for around 20 V. For thicker material (6 Mm or 1/4 Inch), you might need 25 V or more.
Your machine’s user manual is essential here. Use it to double-check voltage vs. material thickness recommendations. I once set the voltage too low on thicker steel, which resulted in poor arc stability—don’t make my mistake!
-
Test the Weld
Run a test weld after adjusting the voltage. Observe the arc characteristics: a steady blue arc usually indicates correct voltage. If you see spatter or hear hissing sounds, your voltage might be too high or too low. Check your weld bead; ideally, it should look uniform and smooth.
If the arc is unstable, readjust the voltage. Repeat the test until you achieve a consistent weld. This step is crucial—improper voltage can undermine your entire project. You’ll gain confidence with practice! Understanding how intensely the welding arc shines can also help in making precise adjustments.
-
Fine-tune As Necessary
After testing, fine-tune your voltage settings as needed. You might need slight adjustments for the best results at different angles or positions. For example, vertical welding might require higher voltage than flat welding, as outlined in our comprehensive welding guidance resources.
A crucial aspect is also ensuring optimal visibility under varying conditions, which can be learned through seeing better when welding.
Note how the weld changes with each adjustment. Keeping a log can help you develop a feel for your specific materials and processes. Over time, you’ll find a comfortable range for voltage settings that works across different materials.
We covered the steps for setting voltage in welding. Next, we will discuss the relationship between voltage and amperage in welding.
Relation Between Voltage and Amperage in Welding
Understanding how voltage and amperage work together is critical for effective welding.
Welding Process | Typical Voltage (V) | Typical Amperage (A) | Voltage to Amperage Ratio |
---|---|---|---|
Stick Welding | 20 – 30 | 60 – 120 | 1V : 2A |
MIG Welding | 18 – 30 | 50 – 300 | 1V : 2A |
TIG Welding | 10 – 20 | 20 – 250 | 1V : 1A |
Flux-Cored Arc Welding | 20 – 28 | 40 – 200 | 1V : 2A |
The relationship between voltage and amperage affects your welding results significantly. A higher voltage generally allows for deeper penetration but requires a balance with amperage for stability. Lower voltages may lead to less heat and potential weaknesses in the joint. Adjust both settings based on your material’s needs for optimal results.
When working with coated or treated metals, a specific consideration is the choice of primers that facilitate easier welding. This includes the use of weld-through primer applications which can improve weld quality by reducing contaminants.
So far we covered the connection between voltage and amperage in welding. Next, let’s look at the variables that impact voltage.
Factors That Affect Voltage in Welding
What factors influence the voltage you’ll use when welding?
-
Welding Material Properties
The type of metal significantly affects voltage requirements. Softer metals like aluminum often need about 24 to 26 volts (V) for optimal weld quality, while harder metals like stainless steel might require 20 to 23 V. The inherent conductivity determines how much voltage is necessary to maintain a stable arc.
-
Electrode Type and Size
Your choice of electrode impacts voltage performance. For instance, a 0.035-inch (0.89 Mm) MIG wire typically operates at about 24-30 V, while a larger diameter, like 0.045-inch (1.14 Mm), may need a boost to around 27-35 V. This variance is crucial for achieving the desired penetration and bead shape.
-
Welding Position
Adjust your voltage based on the welding position. Flat welding may need lower voltage, often around 20-24 V. However, vertical welding may require an increase to around 25-30 V to counteract gravity and ensure a strong weld.
-
Arc Length
The distance between your electrode and the workpiece, or arc length, is crucial. Shorter arcs generally require less voltage, often around 20 V, while longer arcs (Over 1/8 Inch or 3 Mm) may need higher voltage levels, up to 30 V, to maintain stability and prevent spatter.
-
Travel Speed
Your travel speed affects voltage in the weld. Faster travel speeds may require higher voltage, around 28-31 V, to sustain the arc, while slower speeds may reduce the voltage requirement to about 22-26 V, affecting the bead’s penetration and width. Proper storage of electrodes is vital to maintain their effectiveness, ensuring they deliver consistent results in varying welding conditions. Explore optimal ways to store welding rods.
We have now covered the factors influencing voltage in welding. Next, we will examine common issues to watch for.
Typical Problems to Be Aware Of
Let’s look at specific issues related to voltage in welding.
-
Overheating Of the Weld
High voltage can cause overheating. It leads to melting and discoloration or bubbles. To fix this, reduce the voltage to match the material, usually around 18-25 volts (V).
-
Inconsistent Arc Stability
Voltage affects arc stability. Fluctuating voltage causes erratic welding. Stabilize your power source and set the voltage within the recommended range.
-
Burn Through on Thin Materials
Excessive voltage can cause burn-through. Holes are a clear sign. To resolve this, lower the voltage to around 14-18V for thin metal.
-
Poor Penetration
Low voltage leads to poor penetration, resulting in shallow welds. Increase the voltage, usually around 22-30V, to improve results.
-
Excessive Spatter
High voltage may cause excessive spatter. If you see many sparks, the voltage might be too high. Lower the voltage to optimal settings, typically between 18-25V.
Aftercare, Inspection, and Advanced Tips for Voltage in Welding
Here are some valuable insights on aftercare, inspection, and expert tips regarding voltage in welding.
Aftercare Tips
After adjusting your voltage settings, check the leads and connections. Maintain a tight grip; a loose electrode can misread voltage. Aim for a maximum open-circuit voltage of 80V (80 Volts) to prevent electrical hazards during cooling.
Inspection Techniques
Inspect your welding machine’s output voltage with a multimeter—it should read between 18V and 25V (18 to 25 Volts) during operation. I use the Klein Tools MM400 for precise measurement. Ensure all connectors are clean to avoid inaccurate readings.
Expert Tips
Tune your arc length while maintaining a voltage of around 22V (22 Volts) for stability. Use pulse welding to prevent distortion, especially with thinner metals under 5 mm (0.2 Inches) at low voltages. Finally, consider installing a higher-rated transformer if your work often demands higher amperage settings.
Typical Uses Of Voltage in Welding
People often use voltage settings for welding precision. However, there are many applications, such as:
- Pipe Welding: High voltage setups deliver deep penetration in thick pipes, ensuring a strong weld joint. This method is popular in the oil and gas industry.
- Metal Fabrication: Controlled voltage produces cleaner, consistent welds on sheet metals, often found in automotive manufacturing.
- TIG Welding: In TIG (Tungsten Inert Gas) processes, voltage adjustments maintain arc stability. This technique is commonly used in aerospace applications where quality is crucial.
- MIG Welding: The voltage setting influences wire feed speed and penetration. It’s widely used in construction for its speed and efficiency.
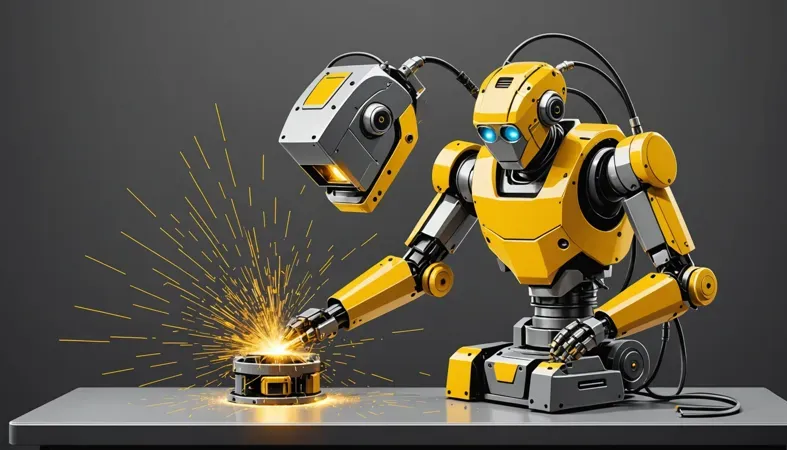
Frequently Asked Questions (FAQs)
Now let us look at some common questions I typically get asked about voltage in welding.
How to Check Volts and Amps on a Welding Machine?
You can check volts and amps on a welding machine using a multimeter. First, set the multimeter to the correct settings for voltage and current, then connect the probes to the welding machine’s output. This helps you monitor your settings, ensuring you run optimal parameters for various welding tasks.
How Much Voltage is Required for Arc Welding?
The voltage required for arc welding typically ranges from 20 to 40 volts. Most electrodes operate best at this voltage range, as it helps create a stable arc, improving your weld quality. Exceeding this range may lead to excessive spatter and increased heat, damaging your components.
What is Open-circuit Voltage in Welding?
Open-circuit voltage (OCV) in welding is the voltage present when the welder is not welding. This value usually falls between 50 and 80 volts for most welding machines. Knowing OCV helps ensure safety and prevents accidental electric shocks before you start welding.
What is Welder Amps and Voltage?
Welder amps refer to the current used in welding, while voltage refers to the electric potential. Typically, currents range from 40 to 300 amps for most welders. Correctly setting these metrics is essential as they directly impact weld penetration, bead profile, and overall strength.
What is the Voltage for MIG Welding?
The voltage for MIG welding usually ranges from 18 to 30 volts. This range ensures a smooth and controlled wire feed, helping you achieve a clean weld. Adjusting voltage within this range based on material thickness is crucial for optimal welding results.
Conclusion
We covered various aspects of voltage in welding including how it works, types of voltage, steps for setting it up, factors that affect it, and typical uses. We also touched on common problems to watch out for, aftercare tips, and some alternatives that might work better. Finally, we answered some frequently asked questions to give you a well-rounded understanding.
In simple terms, voltage in welding is the electrical force that drives electric current through the circuit. We discussed how the required voltage can vary depending on the type of welding—like arc welding, which typically uses around 20-40 volts (V). Happy welding means understanding that correct voltage is key for achieving a strong weld, ensuring safety, and optimizing the performance of your welding machine.
For more comprehensive insights and resources on welding, be sure to explore our homepage: What is Welding.
References
- American Welding Society. (2020). AWS Welding Handbook: Welding Science and Technology (Vol. 1). Miami, FL: AWS.
- Blodgett, O. W. (1996). Design of Welded Structures. Cleveland, OH: James F. Lincoln Arc Welding Foundation.
Joe Carter is a retired welding professional with over 40 years of hands-on experience in the industry, spanning ship repair, structural welding, and even underwater projects. Joe is a master of MIG, TIG, and Stick welding. Passionate about mentoring the next generation of welders, Joe now shares his decades of expertise and practical insights to help others build rewarding careers in welding.
American Welding Society, MIG Welding, Pipe Welding, TIG Welding, Voltage Settings, Welding, Welding Safety, Welding Techniques