What is Underwater Welding? Discover Techniques, Applications, and More!
Published on: December 6, 2024 | Last modified: March 4, 2025
By: Tyler James
Underwater welding involves joining metal parts beneath the water’s surface. It’s a specialized skill that merges welding techniques with diving.
It’s a question I’m often asked: what is underwater welding? This skill helps repair ships, pipelines, and structures, making it crucial in marine environments. I’ve seen firsthand how important it is during projects where timely repairs save money and enhance safety.
In this guide, you’ll learn how underwater welding works, explore different welding types, follow the steps involved, and identify factors that affect it. We’ll also discuss common problems and their solutions, plus inspection tips and how this work applies across various fields, like construction and oil rigs. If you’ve ever wondered what does an underwater welder do, you’re in the right place!
Contents
- What is Underwater Welding?
- How Does Underwater Welding Work?
- Types Of Underwater Welding
- Steps for Underwater Welding
- How to Address Common Problems
- Factors Affecting Underwater Welding
- Applications Across Different Fields
- Benefits of Underwater Welding
- Alternatives for Underwater Welding
- Frequently Asked Questions (FAQs)
- Conclusion
- Additional Reading
What is Underwater Welding?
Underwater welding involves joining metal parts while submerged. It’s used in construction, repairs, and salvage work, especially for pipelines and ship hulls. This method’s durability and efficiency make it invaluable in aquatic environments.
How Does Underwater Welding Work?
Underwater welding is a specialized technique where welders join metal structures beneath the water’s surface. It uses either wet or dry welding methods. In wet welding, welders apply electricity in water, using a flux-coated electrode to create an arc. This process generates temperatures around 4,000°C (7,232°F), melting the metal and forming strong bonds. Underwater welding effectively repairs pipelines and ship hulls.
Underwater welding requires extensive training and experience. Welders must understand marine conditions and dive safety. They typically work at depths up to 300 meters (1,000 Feet), where pressure can exceed 30 times atmospheric levels. This expertise is crucial for ensuring both success and safety while working underwater.
I once tried underwater welding during a training exercise. I remember the thrill of diving 15 meters (49 Feet) deep and feeling the coolness of the water while I worked. It taught me that you can weld underwater, but you must be careful and well-prepared for the challenges involved.
Types Of Underwater Welding
What are the types of underwater welding?
-
Wet Welding
Wet welding involves welding directly in water. The welder uses specialized equipment to melt and fuse metals underwater. During wet welding, you must monitor hydrogen production and control your arc to ensure safety. Understanding the different welding by industry can help you select the right technique for your project.
To ensure you have the right materials for underwater projects, it is crucial to know where to buy metal for welding.
-
Dry Welding
Dry welding occurs within a sealed environment. This technique requires building a chamber around the worksite to keep water out. To achieve dry welding, you must create a watertight barrier while completing the welding process. When diving deeper into welding methods, it’s essential to understand the different welding positions that enhance precision and technique.
-
Hyperbaric Welding
Hyperbaric welding takes place under high pressure, making it ideal for deep-sea projects. To execute hyperbaric welding, you’ll need to pressurize the environment, use special equipment, and monitor gas levels carefully to avoid complications.
-
Remotely Operated Vehicle (ROV) Welding
ROV welding uses unmanned remote vehicles to weld in hard-to-reach areas underwater. This is essential for maintenance and repairs. To conduct ROV welding, you’ll command the robotic vehicle to perform precise tasks in challenging conditions.
-
Specialized Underwater Electric Arc Welding
This technique employs electric arcs to weld in water, ensuring a reliable connection despite the tough environment. To carry out specialized underwater electric arc welding, you’ll need a specific electricity supply setup and protective gear to shield against hazards.
So far we covered the various methods of underwater welding. Next, let’s look at the process involved in underwater welding.
Steps for Underwater Welding
Here are the essential steps for underwater welding.
-
Prepare the Site
Assess the underwater site for factors like current and temperature. Water depth affects visibility and the tools you’ll need—common depths are 10-30 m (33-98 Ft). For deeper sites, consider using ROVs (Remotely Operated Vehicles) for better control. I typically check water conditions with specialized sensors.
Document site conditions before starting work. If there’s a strong current, use anchors for stability. Understanding your environment helps tailor your approach and ensures successful welding.
-
Select the Right Welding Method
Choose between SMAW (Shielded Metal Arc Welding) and TIG (Tungsten Inert Gas) based on job specifics. SMAW handles thicker materials well, while TIG provides cleaner welds on thinner sections. Since water absorbs heat quickly, use lower amperage and short arc length for better efficiency. I once struggled with overheating while welding thick metal, so adjusting these factors helped.
Consider the material you’re welding—often austenitic stainless steel is used in underwater settings. Weigh the advantages of each method based on your job requirements.
-
Start Welding
Begin welding with a steady hand and controlled arc. Clean the surface first, as rust and debris can weaken joints—this is especially important underwater. Focus on creating strong, even beads for structural integrity. I’ve found that a consistent travel speed ensures uniform welds.
Monitor your work closely; visibility may be limited underwater. A helmet with a built-in light can help eliminate blind spots. Adapt your technique; adjusting the angle of your torch may improve performance in varying water currents.
-
Cooling and Finishing
After welding, allow adequate cooling time. Water cools the weld quickly, but even slight temperature variations can stress the metal. Inspect weld joints for cracks or inconsistencies—this step is vital. I recommend waiting at least 30 minutes before any additional treatments. After cooling, conduct a visual check for defects. You may also want to perform ultrasonic testing to ensure safety and quality, especially on critical welds. This could prevent significant issues down the line! Using the correct type of fire extinguisher is crucial for welding safety and understanding what class fire extinguisher to use can prevent accidents.
We covered the steps for underwater welding here. Next, we will discuss how to tackle common issues encountered.
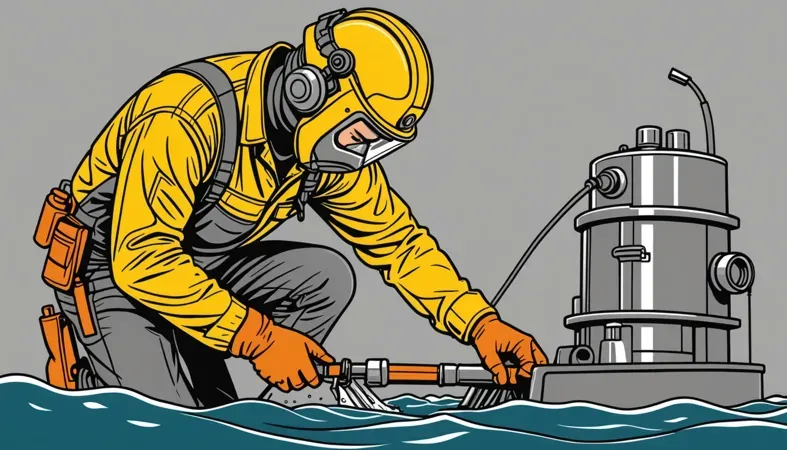
How to Address Common Problems
Let’s look at specific issues in underwater welding.
-
Resolving Arc Disruptions
Underwater welding often faces arc disruptions from water currents. Look for irregular weld beads to identify the issue. To fix it, adjust your position and swimming angle to reduce water flow interference.
-
Managing Equipment Malfunctions
Underwater welding gear can malfunction due to pressure and moisture. I once dealt with a stuck nozzle. Inspect your gear before each dive and keep backup equipment ready to ensure continuity.
-
Dealing With Poor Visibility
Welding in murky waters can hinder visibility. Wear bright wetsuits or welding helmets with built-in lights. Position underwater torches correctly to minimize distortion.
-
Addressing Safety Risks
Underwater welding presents various hazards, such as electric shock and underwater explosions. Regularly assess your surroundings and use proper grounding and safety gear to reduce risks.
-
Mending Incomplete Welds
Underwater welding may leave areas with poor fusion. Use a gauge tool to detect this issue. To fix it, re-weld any incomplete sections, ensuring optimal fusion temperature.
We covered common problems in underwater welding here. Next, we will cover the factors influencing underwater welding processes.
Factors Affecting Underwater Welding
What factors influence the effectiveness and safety of underwater welding?
-
Water Temperature
Water temperature affects welding speed and quality. Cold water below 10°C (50°F) slows reaction rates and decreases weld penetration.
-
Water Salinity
Higher salinity increases conductivity and affects arc stability. Seawater with 3.5% salinity creates more corrosion, making welds less durable.
-
Depth Of Operation
Pressure increases with depth, affecting gas bubbles in the weld. At depths over 30 meters (100 Feet), complexities arise in maintaining consistent arcs due to higher hydrostatic pressure.
-
Environmental Conditions
Current, visibility, and weather can drastically affect underwater welding. Strong currents can push you off course, increasing risks during welding.
-
Type Of Material Being Welded
Materials like steel and aluminum require different techniques. Aluminum’s higher thermal conductivity affects how heat is applied during welding.
Applications Across Different Fields
I’ve known people to use underwater welding for repairs in tough environments. However, it has many unique applications, such as:
- Offshore Oil Platforms: Underwater welding is essential for repairing and maintaining pipelines. It keeps oil flowing and ensures efficient production in harsh sea conditions.
- Bridge and Pier Construction: Welders use this technique to repair structural elements underwater. It strengthens integrity and extends the lifespan of key transport links.
- Shipwreck Salvage: Underwater welding aids in recovering valuable ship materials. It’s popular for treasure hunting and archaeological research.
- Nuclear Facility Maintenance: This welding ensures safe operations by repairing reactor cooling systems. It’s vital for environmental safety and the longevity of reactors.
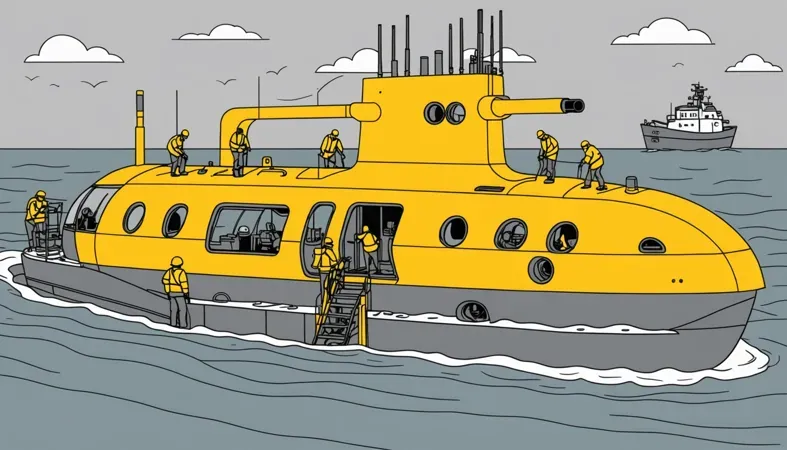
Benefits of Underwater Welding
Underwater welding offers several unique advantages that set it apart from traditional welding methods.
Cost Efficiency
Underwater welding saves time and reduces costs. It eliminates the need for extensive dry-docking or constructing temporary structures. For instance, projects underwater can be completed 20-30% faster than above water, saving thousands in downtime.
Durability of Welds
Welds made underwater are often highly durable due to the cooling properties of water, which prevents overheating. For example, underwater welds can maintain up to 80% of their strength even after exposure to high pressures.
Versatility
This technique can be applied to various materials, from steel to aluminum. It’s adaptable, making it suitable for multiple projects, whether fixing pipelines or constructing bridges.
Access to Remote Locations
Underwater welding allows access to areas that are otherwise difficult to reach. For example, damaged underwater facilities or pipelines in deep water can still be repaired thanks to divers’ skills. While this type of welding is incredibly useful, it’s important to be aware of the potential dangers of welding.
Environmental Protection
By repairing submerged installations, underwater welding helps prevent leaks and environmental damage. This ensures that ecosystems remain protected while vital infrastructure is maintained.
Benefit | Details | Impact on Projects |
---|---|---|
Cost Efficiency | 20-30% faster project completion | Saves thousands in downtime |
Durability of Welds | Maintains 80% strength after high pressure | Reduces need for frequent repairs |
Versatility | Applicable to various materials | Broadens project scope |
Access to Remote Locations | Reaches difficult underwater areas | Enables repairs in isolated setups |
Environmental Protection | Prevents leaks and damage | Sustains ecosystems during repairs |
Alternatives for Underwater Welding
There are alternatives to achieve results similar to underwater welding. For instance, remote-operated vehicles (Rovs) can perform repairs using tools like hydraulic manipulators. In certain cases, products such as the Hyperbaric Welding System are preferred when traditional methods aren’t safe or practical.
From my unique perspective, I’ve noticed that divers often use a method called dry welding, where a chamber maintains air pressure and keeps water out. This allows for a safer welding environment, making it an excellent choice for more delicate tasks. These alternatives can help reduce the risks commonly associated with underwater operations.
Frequently Asked Questions (FAQs)
Now let us look at some common questions I typically get asked regarding underwater welding.
What’s the Point Of Underwater Welding?
Underwater welding is crucial for repairing and constructing structures like pipelines and oil rigs. It helps maintain the integrity of submerged installations, which can prevent leaks and environmental hazards. Seamlessly connecting different metals often requires precise methods, and understanding how to weld thermocouple wire is invaluable for enhancing the reliability of underwater infrastructure.
How Much Do Underwater Welders Actually Make?
Underwater welders typically earn between $60,000 and $120,000 per year, depending on experience and location. High-demand areas, like offshore oil fields, can offer even higher pay due to the rigorous conditions and technical skills required.
Why Are Underwater Welders’ Life Expectancy Low?
Underwater welders face numerous hazards, which can impact life expectancy. The job includes risks like decompression sickness and exposure to hazardous materials, leading to a challenging work environment. Statistics show a decrease in average life expectancy due to these occupational risks.
What Are the Two Types Of Underwater Welding?
There are two types of underwater welding: wet welding and dry welding. Wet welding is done directly in the water and uses a special electrode, while dry welding occurs in a habitat or chamber, allowing for a safer and more controlled environment.
How Does Underwater Welding Work?
Underwater welding works by utilizing specialized equipment to fuse metal pieces while submerged. It involves electric arcs, similar to traditional welding, but adapted for aquatic conditions, ensuring that welds are strong and durable.
What Does an Underwater Welder Do?
An underwater welder repairs and constructs underwater structures, maintaining vital infrastructures. They often deal with a variety of metals, fixing anything from ship hulls to offshore drilling rigs, ensuring safety and durability.
Conclusion
I’m glad we could cover this together. We discussed what underwater welding is, how it works, its various types, steps involved, factors affecting it, common problems, aftercare, inspection, and even some applications across different fields. We also touched on alternatives to underwater welding.
Happy to wrap it up by saying that underwater welding involves fusing metal underwater, typically for repair or construction. We learned that a diver might use special equipment and face challenges like water pressure and visibility. It’s a crucial skill in maritime projects that can happen at varying depths, ranging from just a few feet (1 Meter) to hundreds (Over 300 Feet or 90 Meters).
For those looking to delve deeper into the world of welding, I encourage you to visit What is Welding for more insights.
Additional Reading
- American Society of Mechanical Engineers. (2019). ASME Section IX: Welding and Brazing Qualifications. New York, NY: ASME.
- Canadian Welding Bureau. (2019). CSA W59: Welded Steel Construction. Ontario, Canada: CWB.
Tyler is a passionate DIY welder and self-taught metal artist with years of hands-on experience transforming raw materials into functional and artistic creations. Specializing in MIG welding, Tyler crafts everything from custom furniture to outdoor sculptures, blending creativity with technical skill. Committed to making welding accessible, Tyler shares practical insights and project inspiration to help beginners and hobbyists confidently explore the world of metalworking.
Construction Repair, Diving Safety, Industrial Applications, Marine Engineering, Structural Integrity, Underwater Welding, Welding, Welding Gear, Welding Safety, Welding Techniques