How to MIG Weld With Flux Core Wire? Techniques, Steps, Safety
Published on: January 18, 2025 | Last modified: March 4, 2025
By: Tyler James
So, how to mig weld with flux core wire? Following the right steps matters because it affects the quality of your weld. From personal experience, I can tell you that skipping any part of the process can lead to weak joints or a sloppy finish.
In this guide, I’ll cover what’s MIG welding, different techniques, necessary prerequisites, the steps to weld effectively with flux core wire, safety precautions, various processes, factors that impact your welding, troubleshooting common problems, aftercare tips, benefits of this method, industry applications, possible alternatives, and even some frequently asked questions. You’ll learn everything you need, including how to mig weld flux core for beginners.
Contents
- How to Mig Weld With Flux Core Wire?
- What is MIG (Metal Inert Gas Welding)?
- Prerequisites to Keep in Mind
- Precautions
- Steps to MIG Weld With Flux Core Wire
- Types Of Flux Core MIG Welding Processes
- Factors Affecting MIG Welding With Flux-cored Wire
- Common Issues and Troubleshooting
- Aftercare, Inspection, and Advanced Tips for MIG Welding With Flux Core Wire
- Essential Flux Core Wire Maintenance and Care
- Top Benefits You Can Expect
- Industry Uses
- Alternatives That Might Work Better
- Frequently Asked Questions (FAQs)
- Additional Reading
How to Mig Weld With Flux Core Wire?
MIG, or Metal Inert Gas, is a welding technique using a continuous wire feed. To MIG weld with flux core wire, set your welder to 0.8-1.2 mm wire, adjust voltage to 18-23 V, and practice. It’s easier than you think, great for outdoor projects!
What is MIG (Metal Inert Gas Welding)?
MIG, or Metal Inert Gas welding, is a process that uses a continuous solid wire electrode to join materials. The wire feeds through a MIG gun, shielding the weld pool with an inert gas, typically argon or helium. This method allows for high welding speeds and minimal spatter, making it popular in the automotive and manufacturing industries. Statistics show that MIG welding accounts for about 60% of all welding processes in the U.
S., highlighting its widespread use.
When it comes to MIG welding with flux-cored wire, there’s a slight twist. Unlike traditional MIG, flux-cored welding uses a hollow wire filled with flux. This creates a shielding gas during the process, making it suitable for outdoor use. I’ve used this technique for projects in windy conditions where regular gas shielding wouldn’t suffice.
In my work, I’ve used it to weld fences and outdoor structures. Knowing how to MIG weld flux-cored is vital for beginners, especially when facing tough environmental challenges. Setting up requires understanding your machine settings, like wire speed and voltage, to ensure a smooth weld every time. Trust me, experiencing those first successful welds feels incredibly satisfying!Next, we will examine essential prerequisites to keep in mind.
Prerequisites to Keep in Mind
What do you need to start?
- MIG Welder: You need a reliable model like the Hobart Handler 140. It’s crucial for using flux core wire effectively.
- Flux Core Wire: Get the .030 inch (0.8 Mm) Lincoln Electric NR-211-MP. You need high-quality wire for strong, clean welds.
- Drive Rollers: Use a compatible size, like .030 inch (0.8 Mm), from your welder’s manufacturer. This ensures smooth wire feeding.
- Welding Gun: A suitable gun, like the Miller 150, is essential for controlling the weld pool and achieving penetration.
- Adapter Plug: Depending on your welder, an adapter like the Lincoln Electric MIG Adapter Plug may be necessary for a proper electrical connection.
That covers the key prerequisites to consider. Let’s now take a look at the necessary precautions to follow.
Precautions
Let’s cover essential safety measures for flux core MIG welding.
- Wear Protective Gear: Always use well-fitted gloves, helmets, and jackets to protect against heat and sparks. Look for 14 oz (396 G) gloves.
- Ventilation Matters: Ensure proper airflow to avoid smoke inhalation. I recommend the VIVOSUN 6-Inch Air Exhaust Fan.
- Maintain a Clean Workspace: Keep combustible materials clear within 35 feet (10.7 M). Flammable items can ignite easily.
- Check Your Equipment: Ensure your welder and cables are in good condition. Inspect for wear and tear monthly.
Remember, prioritizing safety isn’t just smart—it can save lives, so always stay prepared!That covers important precautions for MIG welding. Let’s now take a look at the steps to MIG weld with flux core wire.
Steps to MIG Weld With Flux Core Wire
Here are the steps for MIG welding using flux core wire. Follow these to achieve the best results.
-
Set Your Welder Settings
Start by adjusting your welder settings for flux core wire. The voltage should typically be between 18-22 volts and the wire feed speed about 220-300 inches per minute (IPM). It’s crucial to get these settings right. Every welding scenario is different, so be ready to tweak them based on material thickness.
If you’re welding thin metal, use lower settings. For thicker materials, increase the voltage and speed. Test welds on scrap material before starting the real work.
-
Choose the Right Wire Type
Select the appropriate flux core wire for optimal performance. Use E71T-GS for general-purpose welding; it’s ideal for outdoor tasks since it’s gasless. For thicker sections, a self-shielding wire like E71T-1 works well and often produces less spatter.
Choose wire with a diameter of .030 inches (0.76 Mm) for most jobs. For slightly heavier metals, .035 inches (0.89 Mm) is a better option. The right wire affects penetration and bead shape significantly.
-
Maintain Proper Stick Out
Hold the electrode with the proper stick-out; about ½ to ¾ inch (1.27 To 1.90 Cm) is ideal. This distance ensures better arc stability and overall control. This is vital for consistent welds—too short risks damaging the nozzle, while too long may cause voltage inconsistencies.
Keep the tip of your wire free of any build-up or contaminants. Adjust the stick-out regularly as you progress along your weld to maintain it.
-
Control the Travel Speed
Pace yourself while welding! Moving too fast leads to poor penetration, while going too slow creates excess heat that can warp your material. Aim for a steady speed of about 4-6 inches per minute (10-15 Cm/min) for most applications. Practice makes perfect—start slow, then gradually increase your speed.
Use a uniform motion; focus on making steady passes rather than starting and stopping randomly. This technique promotes a more even bead and reduces defects.
-
Watch for Proper Arc Length
Maintain a clear and consistent arc length; ideally, it should match the stick-out of your wire. An inconsistent arc length leads to bonding problems and poor welds. Control your distance and monitor your progress to keep the bead smooth and uniform.
If your arc length is too long, you’ll face excess spatter. If it’s too short, you might experience burn-through. Practice on scrap material to find your ideal length before starting your project.
So far we covered the process of MIG welding using flux core wire. Next, let’s look at different flux core MIG welding methods.
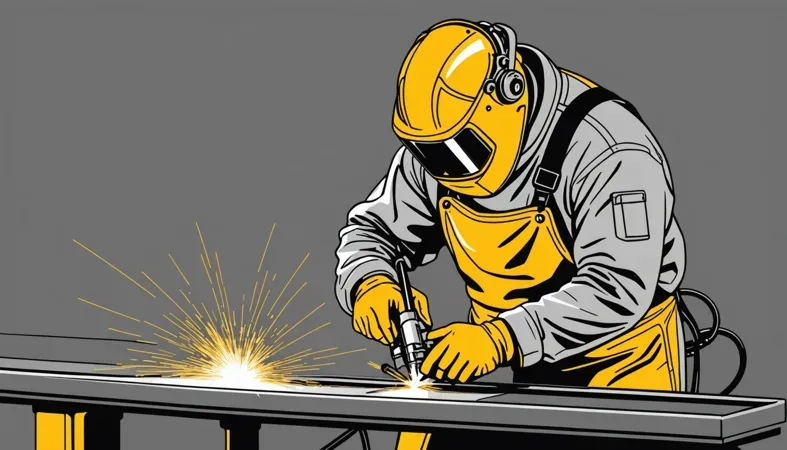
Types Of Flux Core MIG Welding Processes
Let’s explore the different types: Self-Shielded, Gas-Shielded, Dual-Shield, Metal Core, and Electrode Positive Flux Core Welding.
-
Self-shielded Flux Core Welding
This type doesn’t require an external gas supply. It uses a tubular wire filled with flux, making it ideal for outdoor use as it withstands winds up to 20 mph (32 Kph). It’s suitable for materials that are at least 1/8 in (3.2 Mm) thick.
-
Gas-shielded Flux Core Welding
This method adds shielding gas alongside the flux, improving weld quality. You’ll typically work with mild steel or stainless steel, resulting in a cleaner finish compared to self-shielded welding. Understanding the various welding processes can further enhance your skills and ensure better outcomes in your projects.
It’s essential to know the proper care for welding burns to ensure personal safety during any welding process.
-
Dual-shield Flux Core Welding
This technique combines the advantages of gas-shielded and self-shielded welding. An external gas supply and flux-filled wire provide the best of both methods. It’s commonly used in structural applications exposed to harsh conditions.
-
Metal Core Flux-cored Welding
Metal core wires contain metal powder that increases the deposition rate. They produce less smoke, allowing for better visibility of the weld pool. This method can deliver rates up to 30% more than conventional solid wire for thick welds. For optimal shielding in this process, exploring 75/25 welding gas options is beneficial.
-
Electrode Positive Flux Core Welding
This technique connects the electrode to the positive terminal, promoting deeper penetration as more heat generates at the arc. It’s ideal for thicker materials, offering up to 7,000 amps at maximum draw.
Factors Affecting MIG Welding With Flux-cored Wire
What factors influence the quality of flux-cored MIG welding?
-
Welding Voltage
Voltage affects arc stability. A typical setting for flux-cored welding is between 18 and 24 volts. If it’s too high, welds can become overly wide and shallow.
-
Travel Speed
Moving too fast can lead to weak welds, while moving too slowly can cause burn-through. Aim for a speed of about 5 to 12 inches per minute (12.7 To 30.5 Cm/min).
-
Welding Wire Diameter
Wire diameter is critical! Common diameters are 0.030 inches (0.76 Mm) and 0.035 inches (0.89 Mm). Thicker materials require a larger diameter.
-
Base Material Thickness
Material thickness directly impacts your settings. For example, welding sheets over 1/4 inch (6.35 Mm) requires different settings than thinner materials.
-
Environmental Conditions
Welding outdoors can create wind issues that disrupt the arc. Keep conditions calm and dry for the best results.
Common Issues and Troubleshooting
Here are some common problems you may encounter with MIG welding.
-
Inadequate Penetration
MIG welding can suffer from inadequate penetration when the voltage or wire speed is too low. Check settings; aim for 18-24 V for steel. Adjust if there’s excessive splash.
-
Excessive Spatter
MIG may produce excessive spatter if the wire feed rate is too high. It’s essential to adjust that feed rate. Lower it to achieve a clean puddle!
-
Weld Cracking
Weld cracking can occur if the material isn’t prepared well. Remove rust or paint; clean metal ensures a strong bond.
-
Electrode Contamination
Dust or oil on the wire can lead to contamination in MIG welding. Keep your workspace clean, and ensure your hands are grease-free!
-
Wire Feeding Problems
Wire feeding jams can cause MIG welding issues. Regularly check for kinks in the wire and maintain a smooth feeding path. Ensure a steady flow!
Aftercare, Inspection, and Advanced Tips for MIG Welding With Flux Core Wire
Here’s focused advice on keeping your welds strong and your equipment in peak condition.
Aftercare Strategies
After welds cool, clean the area with a wire brush or grinder to remove slag and contaminants. Maintain equipment by lubricating the liner weekly to prevent wear—this ensures a smooth wire feed at pressures of 100 PSIg (689 Kpa). Check for consistent shielding gas flow, aiming for 15-20 CFH (Cubic Feet Per Hour) to enhance weld quality.
Inspection Techniques
Inspect welds visually for cracks or porosity. If issues arise, adjust the wire feed speed to 3-6 inches (76-152 Mm) per minute. Use calipers to ensure bead width is around 5/16 inches (8 Mm) for structural integrity. I’ve used the Lincoln Electric Handheld Spot Inspector for precision checks on welds.
Expert Techniques
If you’re experienced, like me, fine-tune your settings based on material thickness. Use a travel speed of 6-12 inches (150-305 Mm) per minute to optimize penetration. Experiment with multi-pass techniques, applying up to three sequential passes on thicker metals, allowing for a cooldown of at least 10 minutes each time.
Essential Flux Core Wire Maintenance and Care
Caring for your flux core wire setup is key to quality welding.
Daily Maintenance Tips
- Clean the Welder: Wipe down the flux core welder to remove dust and debris. Ensure the nozzle is free from burnt wire and slag.
- Check Wire Feed Tension: Keep the tension consistent. Too tight may cause jams; too loose may result in erratic feeding.
- Inspect Connections: Look at electrical connections regularly. Tighten any loose components to maintain good contact.
Storage Recommendations
- Store Wire Properly: Keep flux core wire in a dry environment. Moisture can cause the wire to rust or weaken.
- Maintain a Controlled Temperature: Avoid extreme temperatures. Ideal storage is between 50°F (10°C) and 80°F (27°C).
Performance Troubleshooting
Issue | Possible Cause | Solution |
---|---|---|
Erratic Arc | Wire feed speed too low | Increase the feed rate to 200-300 IPM (5.08-7.62 M/min). |
Poor Penetration | Voltage setting too low | Adjust voltage to 18-24 V; try test welds on scrap. |
Excessive Spatter | High wire speed | Lower the wire speed; ensure a steady hand. |
Weld Overheating | Too slow travel speed | Increase speed to 4-6 inches per minute (10.16-15.24 Cm/min). |
Top Benefits You Can Expect
The main benefit of learning to MIG weld with flux-cored wire is its versatility. I’ve used it for outdoor welding, even in windy or less-than-perfect conditions.
This process offers quicker welds, less prep time, and stronger joints. Plus, you can often weld thicker materials without needing multiple passes. It’s as user-friendly as it gets, which is great for beginners!
Industry Uses
I’ve used MIG welding with flux-cored wire for various projects. It has many specific applications, such as:
- Automotive Repair: Flux-cored wire is ideal for body repairs and framework. It’s popular because it withstands outdoor conditions and provides strong welds.
- Metal Fabrication: Flux-cored welding is favored for making custom metal products and structures due to its speed and ability to weld thicker metals without pre-cleaning.
- Shipbuilding: In maritime applications, flux-cored wire’s performance in windy conditions makes it a go-to for hull fabrication and repairs.
- Construction Industry: It’s often used for welding structural steel because of its high deposition rate. Contractors prefer it for large projects, as it saves time and costs.
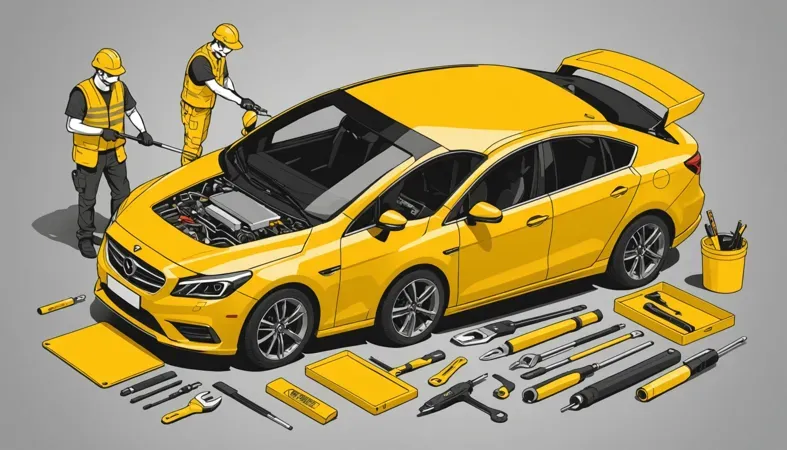
Alternatives That Might Work Better
Looking for other options? You might consider using solid wire with shielding gas, such as ER70S-6. It’s great for clean, solid welds and controls spatter better. Reflecting on my past experiences, switching to a gas setup helped improve penetration in thicker materials.
Another option is to try a multi-purpose flux core wire, like Lincoln NR-211, especially if you’re a beginner. It offers flexibility for various positions and thicknesses. You can tackle different projects without constantly changing your setup. Isn’t that a plus?
Frequently Asked Questions (FAQs)
Now let us look at some of the questions I typically get asked.
Can You Use a MIG Welder With Flux Core Wire?
Yes, you can use a MIG welder with flux core wire. Flux core wire is designed for MIG welders, providing shielding gas through the core of the wire. This method works well for outdoor use or on dirty surfaces, making it versatile for many projects. Setting up a welder correctly ensures optimal performance and safety, especially when working with different types of wires and techniques, which you can explore in more depth by learning how to set up a Lincoln Electric welder.
How to Get Good Welds With Flux Core?
To get good welds with flux core, ensure you choose the right wire and set your voltage and feed speed correctly. Proper settings lead to smoother beads and less spatter, increasing efficiency and quality on welds by up to 50% compared to improper settings.
Building a welding machine involves understanding the fundamental components such as selecting the correct transformer, which is crucial for optimal performance and safety. If you are interested in this key aspect, explore how to make welding machine transformer to gain deeper insights.
Do You Push or Pull When Flux Core Welding?
You pull when flux core welding. Pulling helps create a cleaner weld bead by allowing the molten metal to flow smoothly. This technique minimizes spatter and improves penetration, resulting in stronger joints ideal for structural projects.
Why Are My Flux Core Welds So Bad?
Your flux core welds might be bad due to improper settings, feed speed, or technique. For instance, using too high a voltage can create excessive spatter. Checking your machine’s manual and adjusting settings can help improve your results significantly.
What is MIG Flux Core Welding?
MIG flux core welding is a process that combines MIG welding with a special type of welding wire containing flux. This flux creates its own shielding gas when it melts, eliminating the need for an external gas supply. This makes it great for outdoor and windy conditions.
We are almost done. We covered the essentials of MIG welding with flux core wire, including the definitions, techniques, necessary prerequisites, and detailed steps. We also discussed precautions, common issues, troubleshooting tips, aftercare, and the industries where this method shines.
To sum it up, learning how to MIG weld with flux core wire means you need to remember the basics: set up your MIG welder correctly, understand the types of processes, and practice safe welding. It’s practical knowledge that can save you time and increase efficiency. If you need more guidance, don’t hesitate to get in touch for further assistance.
For additional insight into the world of welding, feel free to explore our homepage: What is Welding.
Additional Reading
- American Society of Mechanical Engineers. (2019). ASME Section IX: Welding and Brazing Qualifications. New York, NY: ASME.
- O’Brien, R. L. (1991). Welding Handbook: Welding Processes, Part 1. Miami, FL: AWS.
Tyler is a passionate DIY welder and self-taught metal artist with years of hands-on experience transforming raw materials into functional and artistic creations. Specializing in MIG welding, Tyler crafts everything from custom furniture to outdoor sculptures, blending creativity with technical skill. Committed to making welding accessible, Tyler shares practical insights and project inspiration to help beginners and hobbyists confidently explore the world of metalworking.
Beginner Welding, Flux Core Wire, MIG Welding, Safety Precautions, Structural Integrity, Welding, Welding Process, Welding Techniques, Welding Wire, Wire Diameter