How Many Amps to Weld Aluminum? Understanding Amps and Welding Techniques
Published on: April 29, 2025 | Last modified: March 4, 2025
By: Joe Carter
Amps, short for amperes, measure the flow of electricity. Think of it as how much electric current is available to weld.
Many people have asked me about how many amps to weld aluminum. It’s super important to get this right. From my experience, using the right amps means stronger, cleaner welds. Too low, and the weld may not hold; too high, and you risk burning through the metal.
In this guide, I’ll cover several key points, including types of amps for welding aluminum, steps to determine amps needed, factors that can influence your amp settings, and address frequently asked questions like how to set amps for tig welding and how many amps to tig weld 1/4 aluminum.
Contents
How Many Amps to Weld Aluminum?
Amps measure electric current. So, how many amps to weld aluminum? Typically, you need 1 amp per 0.001 inches (0.025 Mm) of thickness. It can be tricky, depending on the material and method used, especially in automotive or aerospace applications.
What Are Amps?
Amps, or amperes, measure electrical current. It’s a fundamental unit in the International System of Units (SI). One amp represents one coulomb of charge passing through a conductor each second. Amps indicate how much electricity flows, making them crucial for welding settings.
When considering how many amps to weld aluminum, you’ll need to match the current to the material’s thickness. Typically, I adjust around 130 to 150 amps for 1/8 inch (3.2 Mm) aluminum. Each welding application varies—sometimes you need more, sometimes less. But that’s a solid starting point!
I found it useful for work, especially when tackling 1/4 inch (6.35 Mm) aluminum. Knowing how many amps to TIG weld 1/4 inch aluminum made a huge difference. It helped me dial in my settings, ensuring I got that perfect bead without burning through the metal. I’ve seen others struggle, but having a reliable amperage setting simplifies the process and leads to better results!
Types Of Amps for Welding Aluminum
What types of amps do you use for aluminum welding?
-
Direct Current Welding Amps
Direct current (DC) welding amps provide a steady flow of electricity. You’ll need around 150-180 amps for aluminum welding with DC. Set your machine to the appropriate amperage level and use a suitable tungsten electrode, like 2% thoriated, with a diameter of 1/16 inch (1.6 Mm).
-
Alternating Current Welding Amps
Alternating current (AC) welding amps switch the direction of current, which is crucial for aluminum. Use about 200-250 amps for aluminum welding with AC. Adjust your welder settings and choose a larger cup size, like #7 or #8, for tungsten shielding. When it comes to protective gear, exploring options such as whether you can view an eclipse through a welding mask can enhance your understanding of welding safety equipment.
-
Pulsed Welding Amps
Pulsed welding amps allow for precise control while welding. This method usually requires 90-150 amps for aluminum. Activate the pulse settings on your welder and set a low background current to maintain heat during welding. When working on vehicles, it is crucial to know what to disconnect when welding to ensure safety and prevent damage.
-
AC/DC Welding Amps
AC/DC welding amps combine both currents for versatility. You’ll want around 130-160 amps for aluminum with this option. Toggle your machine to AC/DC mode and adjust the settings for the thickness of aluminum you’re working with.
-
Root Pass Welding Amps
Root pass welding amps are used for the initial welding layer. You’ll usually need about 120-180 amps for this. Choose a consistent wire feed and adjust your amperage based on the joint configuration and aluminum thickness.
So far we covered various welding amp types for aluminum. Next, let’s look at how to determine the appropriate amperage for welding aluminum.
Steps to Determine Amps for Welding Aluminum
Here are the steps to find the right amps for aluminum welding.
-
Identify Material Thickness
Start by measuring the thickness of the aluminum piece you’re welding. For aluminum, you’ll typically use a metric thickness gauge. As a rule of thumb, you’ll need about 1 amp per 0.001 inches (0.025 Mm). So, for a 1/4 inch (6.35 Mm) thick piece, aim for approximately 250 amps.
If you’re welding thinner materials, like 1/8 inch (3.2 Mm), you might only need around 120 amps. Remember: thicker pieces require higher amps while thinner ones need less. Find that sweet spot for optimal weld penetration.
-
Choose Your Welding Process
What welding method are you using? For TIG (Tungsten Inert Gas) welding, the typical settings differ from MIG (Metal Inert Gas). For instance, if you’re using TIG for 1/4 inch (6.35 Mm) aluminum, set your machine to 250-300 amps. This ensures efficient melting and bonding of the metal.
When MIG welding, you might adjust down to around 200-250 amps depending on your gun size. Adjusting your settings gives better control over weld quality. Don’t hesitate to tweak them based on the process!
-
Set Your Electrode Size
Select the right electrode size for your job. For aluminum, you’ll often use a 2% cerium tungsten electrode for TIG. The diameter of the electrode impacts the amps to use. Generally, each 1/16 inch (1.6 Mm) of electrode diameter allows about 20 amps. So, for a 1/8 inch (3.2 Mm) electrode, prepare for around 80 amps.
Using the wrong size can lead to poor arc stability. Each size affects your machine settings, so consider this when dialing in your amps. The correct electrode minimizes spatter and enhances the weld’s appearance.
-
Adjust for AC or DC Current
Determine the current type that fits your needs. For thin aluminum, alternating current (AC) is usually better. If you’re using AC, you’ll typically need higher amps to maintain an effective arc, often around 140 amps for 1/8 inch (3.2 Mm).
With direct current (DC), set amps slightly lower to achieve the same weld quality with fewer amps. Remember your machine’s capability will dictate the optimal settings, so check your specs before proceeding.
-
Account for Travel Speed
Your travel speed affects your amp settings. If you move quickly, you may need more amps for good fusion, potentially reaching up to 300 amps for thicker aluminum sections. Slower speeds allow less heat buildup, making lower amps sufficient.
The slower you go, the more you can dial back on amps. Adjust your feed rate carefully to avoid overheating the weld. Balancing speed with your amp settings creates a stronger joint!
You should now have a good understanding of how to calculate amperage for welding aluminum. In the next part, we’ll discuss the factors affecting amperage.
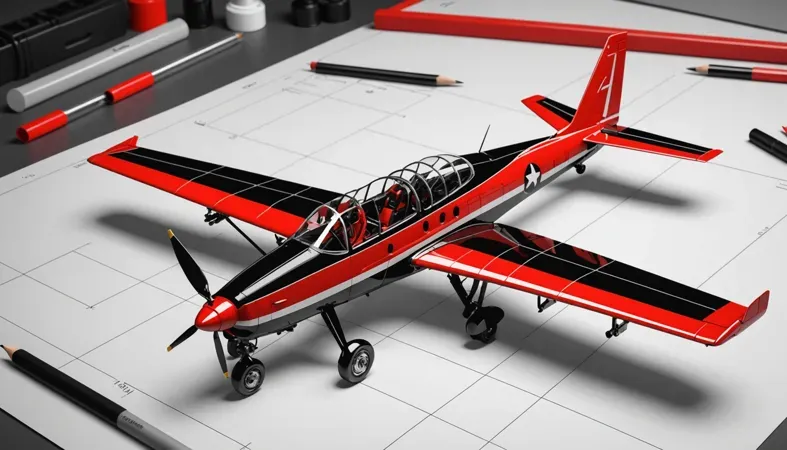
Factors Influencing Amps for Welding Aluminum
What factors impact the amps needed for aluminum welding?
-
Material Thickness
Thicker aluminum requires more heat. For example, 1/8-inch (3 Mm) aluminum needs about 90 to 165 amps for TIG welding.
-
Welding Process
The welding method, such as TIG or MIG, affects the required amps. TIG welding typically requires higher amps than MIG for similar tasks.
-
Type Of Aluminum Alloy
Different aluminum alloys respond differently to heat. For 6061 alloy, you may need 100 to 180 amps, while 5052 works well at 80 to 160 amps.
-
Weld Joint Design
The design affects heat distribution and amp requirements. Flare grooves or T-joints may need different settings compared to butt welds.
-
Heat Input Considerations
Control heat input to prevent warping or burn-through. Reduce amps by about 10% for faster travel speeds to maintain heat balance.
You should now have a good understanding of factors affecting welding amps for aluminum. In the next part, we’ll discuss the recommended amperage table.
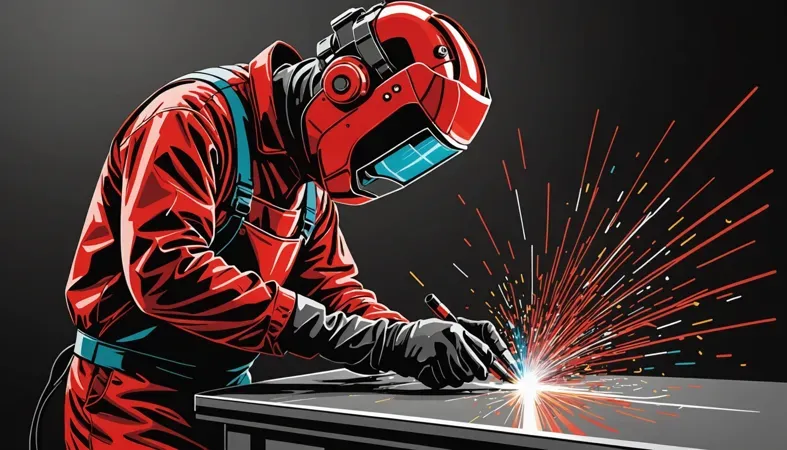
Recommended Amperage Table for Aluminum Welding
Here’s a quick reference table to help you choose the right amps based on aluminum thickness. This can really streamline your decision-making when setting up.
Aluminum Thickness (inches) (mm) | Recommended Amps (A) | Welding Method |
---|---|---|
1/16 inch (1.6 mm) | 80-100 | TIG/MIG |
1/8 inch (3.2 mm) | 130-150 | TIG |
3/16 inch (4.8 mm) | 160-200 | MIG |
1/4 inch (6.4 mm) | 200-250 | TIG/MIG |
3/8 inch (9.5 mm) | 250-300 | MIG |
This table provides a good starting point. Keep in mind that material conditions and joint designs can affect your actual amperage settings. Feel free to adjust as needed!
So far we covered the recommended amperage for aluminum welding. Next, let’s look at common questions and answers.
Frequently Asked Questions (FAQs)
Now let us look at some of the common questions I typically get asked about welding aluminum.
How Much Power Does It Take to Weld Aluminum?
It takes a significant amount of power to weld aluminum, often requiring about 200 to 300 amps (A) for thicker materials. This higher power ensures proper penetration and fusion. For example, 1/4 inch (6 Mm) aluminum might need up to 300 A to properly weld. When discussing welding practices, it’s crucial to be aware of the toxic substances released during these processes.
How Many Amps Does It Take to Stick Weld Aluminum?
To stick weld aluminum, you’ll typically need between 100 to 150 amps (A). This depends on the thickness of the aluminum. Insufficient amps could lead to weak bonds and cracks in the weld.
What Current Do You Need to Weld Aluminium?
You usually need a current of between 140 to 250 amps (A) to effectively weld aluminum. The specific amperage varies with material thickness and welding process. For instance, 1/8 inch (3 mm) aluminum requires about 140 A for a good weld. Understanding the intricacies of aluminum welding can help optimize your welding results.
Choosing the right fire extinguisher is crucial for welding safety, especially when working with flammable materials. To ensure safety during welding activities, it’s important to know which class fire extinguisher is appropriate.
How Many Amps Do You Need to MIG Weld Aluminum?
For MIG welding aluminum, the amperage typically ranges from 100 to 200 amps (A). This range suits materials from 1/8 inch to 1/4 inch thick. More amps yield better penetration and strength in the weld.
What Size Cup for Tig Welding Aluminum?
A size 8 or 10 cup for TIG welding aluminum is often adequate. A larger cup helps provide better gas coverage and reduces contamination during the welding process. Knowing your project specifics can help determine the best size.
Conclusion
That brings us to the end of our discussion. We covered what amps are, types of amps for welding aluminum, steps to determine the right amps, and factors influencing your settings. We also tackled some frequently asked questions to clear up any doubts you might have had.
Hopefully, I was able to impart some of my experience. To sum it up, when figuring out how many amps to weld aluminum, consider thickness. For instance, you’ll need around 130-150 amps for 1/8 inch (3.2 Mm) and about 170-190 amps for 1/4 inch (6.4 Mm). Remember, it’s important to adjust your settings based on these details to get the best results.
If you’re eager to enhance your knowledge further, feel free to return to What is Welding for more insights.
Additional Reading
- ISO. (2017). ISO 3834: Quality Requirements for Fusion Welding of Metallic Materials. Geneva, Switzerland: ISO.
- American Welding Society. (2015). AWS D1.1/D1.1M: Structural Welding Code – Steel. Miami, FL: AWS.
- Miller Electric. (2021). Welding Safety: A Complete Guide. Appleton, WI: Miller Electric Manufacturing Company.
Joe Carter is a retired welding professional with over 40 years of hands-on experience in the industry, spanning ship repair, structural welding, and even underwater projects. Joe is a master of MIG, TIG, and Stick welding. Passionate about mentoring the next generation of welders, Joe now shares his decades of expertise and practical insights to help others build rewarding careers in welding.
Aluminum Alloys, American Welding Society, Amperage Settings, MIG Welding, TIG Welding, Welding, Welding Aluminum, Welding Safety, Welding Techniques