Can You Weld a Cracked Engine Block? Exploring Welding Options and Repair Techniques
Published on: May 16, 2025 | Last modified: March 4, 2025
By: Tyler James
In this guide, we’ll cover whether a cracked engine block can be welded, different types of engine blocks and their weldability, key prerequisites before starting, steps for welding, precautions to take, various welding types, factors affecting successful welding, typical problems you might face, and aftercare. Plus, we’ll look at alternatives for repairing a cracked engine block and answer common FAQs to help you out.
Contents
- Can You Weld a Cracked Engine Block?
- What is an Engine Block?
- Types Of Engine Blocks and Their Weldability
- Prerequisites to Keep in Mind
- Steps for Welding a Cracked Engine Block
- Precautions
- Types Of Welding for Cracked Engine Blocks
- Factors Affecting Engine Block Welding
- Typical Problems to Be Aware Of
- Aftercare, Inspection, and Advanced Tips for Welding a Cracked Engine Block
- Benefits Of Welding a Cracked Engine Block
- Applications You Should Know About
- Alternatives for Repairing a Cracked Engine Block
- Frequently Asked Questions (FAQs)
- Conclusion
- References
Can You Weld a Cracked Engine Block?
Yes, you can weld a cracked engine block, but it’s tough. It’s tricky because of the block’s material and the risk of warping. Using a TIG welder on clean aluminum or cast iron is the best route.
What is an Engine Block?
An engine block is the core component of an internal combustion engine. It houses the cylinders, pistons, and crankshaft, forming the structure that supports the engine. Typically made of iron or aluminum, engine blocks weigh between 120 kg (265 Lbs) and 230 kg (507 Lbs). Their design is crucial for engine function, with tolerances measured in microns to ensure high performance.
Now, let’s address our main concern: can you weld a cracked engine block? I’ve seen many people puzzled by this. Sometimes, I’ve had to guide friends through their options when they found themselves facing a cracked engine block.
I once relied on my uncle’s expertise when my car’s engine block cracked unexpectedly. It was a tense moment as we debated methods like JB Weld. I learned how to handle these tough situations. Understanding if you can use JB Weld on a cracked engine block opened doors for quick fixes, which can save time and money when you’re on a budget.
Types Of Engine Blocks and Their Weldability
What types of engine blocks might you encounter?
-
Cast Iron Engine Blocks
Cast iron is common in engine blocks due to its durability. You can weld cracks in a cast iron block using the right technique. Preheat the area, use a nickel-based welding rod, and cool it slowly to avoid cracking.
-
Aluminum Engine Blocks
Aluminum engine blocks are lightweight and provide good heat dissipation. You can weld a cracked aluminum block. Clean the cracked area thoroughly, preheat to about 300°F (149°C), and use a TIG welder (Tungsten Inert Gas Welder) suitable for aluminum.
-
Steel Engine Blocks
Steel blocks are strong and wear-resistant. You can weld a steel engine block. Grind the crack to a V-shape, use a MIG welder, and apply multiple passes for a solid repair.
-
Composite Engine Blocks
Composite blocks combine materials for lightweight performance. Welding a cracked composite block is tricky and often not recommended. Use epoxy or similar adhesives instead of traditional welding to maintain structural integrity.
-
Flat Engine Blocks
Flat engine blocks are used in specialized applications. You can weld a cracked flat block if made of steel or aluminum. Assess the material and follow the appropriate welding steps based on whether it’s cast, aluminum, or composite.
So far we covered the different types of engine blocks and their weldability. Next, let’s look at essential prerequisites to consider.
Prerequisites to Keep in Mind
What do you need to start?
- Welding Torch: You’ll need a MIG welding torch, like the Lincoln Electric SP-140T. It ensures stable and precise welding on the engine block.
- Welding Rods: You’ll need TIG rod materials, such as ER70S-6, especially for cast iron repairs. These rods provide strong joint integrity, essential for the engine’s heat resistance.
- Engine Block Heater: An engine block heater, like the Endurance 1000W, is vital. It helps minimize thermal stress and prevents cracking during welding.
- Heat Treatment Equipment: You’ll need a heat treatment tool, such as a propane torch, for pre- and post-welding. This controls warping and significantly enhances weld strength.
- Cooling System Sealer: Use a sealer, like Bar’s Leaks Rear Main Seal, to prevent fluid leaks post-repair. It supports the block’s long-term durability and functionality.
We have now covered important prerequisites to consider. Next, we will examine the steps for welding a cracked engine block.
Steps for Welding a Cracked Engine Block
Here are the steps to effectively weld a cracked engine block.
-
Clean the Cracked Area
First, grind or sand down the cracked area on the engine block. Ensure a clean surface for a strong weld. Remove dirt, grease, or old paint using a wire brush or grinder to expose bare metal. Achieve a clean area at least 25.4 mm (1 Inch) wider than the crack.
Next, check the depth of the crack. If it’s severe, you may need to cut deeper into the block. A clean surface helps the weld pool penetrate better, significantly increasing joint strength.
-
Preheat the Engine Block
The next step is preheating the engine block for better welding results. Aim for a temperature between 350°F to 500°F (About 175°C to 260°C). This reduces the risk of cracking while you weld. Use a propane torch or heat lamp, ensuring even heat distribution across all surfaces. Allow the block to cool slowly after preheating. Rapid cooling can create cracks where none existed before. Preheating the area around the crack promotes a stable weld pool and minimizes tension during welding. Ensuring proper techniques when welding pipes is equally important, especially if using electrodes like 6010 for pipe welding.
-
Weld the Crack
Now it’s time to weld. Use a MIG or TIG welder, keeping the amperage around 130-160 A for proper penetration. If you’re welding a cast iron block, consider using nickel-based electrodes. For best results, make multiple passes to gradually build up material and ensure strong adhesion.
Allow the weld to penetrate deeply into the cavity. When I welded my first block, I realized that overlapping too much can introduce weaknesses. Focus on making shorter, controlled passes to achieve a solid joint.
-
Post-weld Treatment
After welding, post-weld treatment is crucial. Allow the weld to cool naturally; don’t quench it with water. This manages stress caused during welding and reduces the risk of cracking. If needed, clean and grind the surface flush to match the block’s profile.
Finally, check for gaps or weaknesses after the surface cools. A pressure test can help verify the integrity of your weld. I’ve successfully used a simple air test to ensure the block holds pressure without leaks.
That covers the steps to weld a cracked engine block. Let’s now take a look at the necessary precautions.
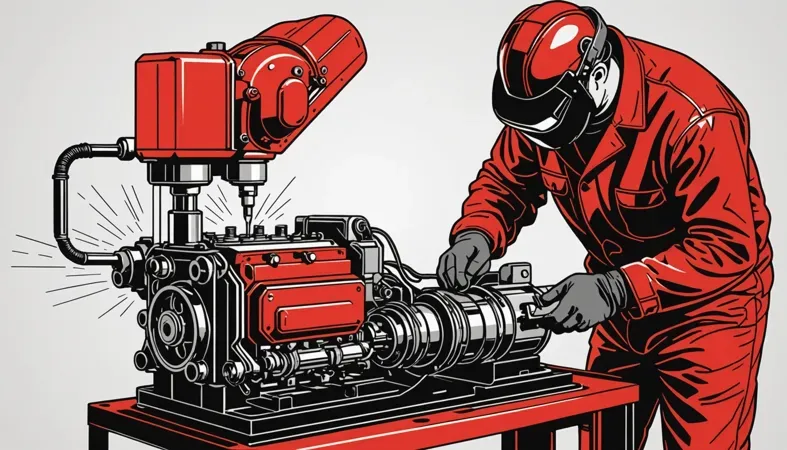
Precautions
Let’s quickly cover vital safety measures for welding engine blocks.
- Wear Protective Gear: Always use gloves, goggles, and flame-resistant clothing. Products like 3M impact-resistant glasses provide crucial eye safety during welding.
- Ensure Adequate Ventilation: Work in well-ventilated areas to avoid harmful fumes. Use an extraction fan, such as a BRF Air Filtration System, to improve air quality.
- Check for Flammable Materials: Remove nearby flammable items to reduce fire hazards. Even a few sparks can ignite flammable liquids like oil.
- Stable Setup: Secure the engine block tightly before welding. A sturdy C-clamp can prevent accidents during the process.
Don’t underestimate safety—it’s crucial for your well-being while welding!
Types Of Welding for Cracked Engine Blocks
Let’s explore different types of welding for cracked engine blocks. We’ll cover MIG, TIG, Stick, Flux-Cored, and Oxy-Acetylene welding.
-
MIG Welding
MIG welding (Metal Inert Gas) uses a continuous wire feed and gas shield, making it ideal for thin metals. It’s relatively easy for beginners. Can you really weld a cracked engine block with this technique? It can work if the crack isn’t too severe, but be cautious of high heat that can distort the block.
-
TIG Welding
TIG welding (Tungsten Inert Gas) uses a non-consumable tungsten electrode and offers high-quality welds. Personally, it’s my go-to for engine block repairs. You get better control, especially with thin materials, and that precision is crucial.
-
Stick Welding
Stick welding (Shielded Metal Arc Welding) involves a consumable electrode. This method is sturdy and works well in difficult positions. Can a cracked engine block be welded using this? Yes, it’s reliable and often used for thicker sections, but it may not provide the neatest finish.
-
Flux-cored Arc Welding
Flux-Cored Arc Welding (FCAW) is similar to MIG but uses a tubular wire filled with flux. It self-generates a gas shield, making it suitable for outdoor work. If you’re facing a tough crack in your engine block, this might be a good option.
Welding in unconventional positions poses unique challenges, especially for overhead applications where mastering welding upside down becomes essential for achieving strong and reliable joints.
-
Oxy-acetylene Welding
This method combines oxygen and acetylene gas to produce a high-temperature flame. It’s versatile and great for heating parts, but might not be suitable for everyone. Can you use JB Weld on an engine block? If welding isn’t an option, that’s a potential solution for smaller cracks outside of precise weld repairs. For those needing to reverse welds, knowing how to remove welds can be crucial.
So far we covered the different types of welding suitable for cracked engine blocks. Next, let’s look at the factors that influence engine block welding.
Factors Affecting Engine Block Welding
What factors impact the decision to repair a cracked engine block by welding?
-
Material Type
Engine blocks can be cast iron or aluminum. Cast iron welds better due to its properties, while aluminum requires specific techniques. Using the correct filler material, like ER4047 for aluminum, is crucial for strength and durability.
-
Crack Size and Location
Small, isolated cracks are easier to weld than large, complex ones. Long cracks near stress points may lead to failure post-welding and often require additional procedures, like pre-heating, to avoid warping.
-
Available Welding Equipment
The type of welding matters. I recommend MIG and TIG for aluminum blocks, while stick welding works better for cast iron. A dedicated MIG welder for aluminum improves precision, resulting in stronger joints.
-
Welding Technique
Each technique has its strengths. For example, TIG welding provides control for thin materials, but it’s slower. MIG offers speed, which is crucial for repairing larger engine blocks. The right technique can determine the repair’s success and longevity.
-
Cooling Rate Post-welding
Cooling the welded area too quickly can cause cracks due to thermal stress. Controlled cooling methods help maintain integrity. A slow, gradual cooling process, such as wrapping in heat blankets, can prevent new cracks from forming after welding.
So far in this section we covered the factors that impact engine block welding. In the next section we will talk about common issues to consider.
Typical Problems to Be Aware Of
Let’s look at issues unique to the engine block that can arise when welding.
-
Porosity in Welds
The engine block can suffer porosity, which appears as small holes in the welds. To spot this, examine the weld for bubbles or a mottled surface. Clean the area and ensure proper gas shielding to fix it.
-
Distortion Of Engine Block
The engine block can distort due to uneven heating. Control heat with a stitch welding technique, and check dimensions after welding. Wrap the block in insulating blankets to limit heat effects.
-
Inadequate Weld Penetration
If the engine block shows insufficient weld penetration, you’ll see “hat” shapes on the joint sides. Increase amperage and preheat the area to fix this, ensuring a solid bond.
-
Cracking Post-welding
The engine block can crack after welding due to thermal shock. Check for fissures using dye penetrant testing, and alleviate stresses by cooling the weld slowly to prevent future cracks.
-
Incompatibility Of Materials
Using different materials on an engine block can lead to issues like premature failure. Conduct a material analysis before welding, and choose compatible filler materials to ensure longevity.
Aftercare, Inspection, and Advanced Tips for Welding a Cracked Engine Block
Here’s essential guidance for maintaining and examining your engine block after welding.
Aftercare Tips
After welding, wait 24 hours before refilling coolant to allow the weld to cure. Monitor temperatures closely—ideally, keep them below 80°C (176°F) during the first drive. Apply anti-corrosion spray to the welded area within one week to prevent rust. It is essential to select the appropriate fire extinguisher to ensure safety while welding, especially when it minimizes the risk of fire hazards, which can be further explored in the right class for welding.
Inspection
Start inspection by checking the weld bead for visual cracks under bright light. Use a digital micrometer (Caliper) to measure micro changes in the block’s thickness—aim for no more than a 0.2 mm deviation. I recommend using a product like Permatex for rib tightening around the weld for added support.
Expert Tips
For experienced welders, use direct current (DC) welding at around 150 amps, depending on the metal type. Preheat to 200°C (392°F) to reduce thermal shock—don’t ignore this step. Experiment with filler rods that match the engine’s aluminum alloy; I’ve had the best results with 4047 (If Applicable).
Fillers and Their Importance
When welding a cracked engine block, the filler material plays a critical role in ensuring a strong bond. Use high-temperature fillers designed specifically for your engine block material. This ensures durability under extreme conditions. To maintain safety and health standards in welding, it is important to be aware of techniques to prevent cancer from welding.
Benefits Of Welding a Cracked Engine Block
The main advantage of welding a cracked engine block is cost savings. When my old car broke down, I used this method and saved hundreds compared to a complete replacement!This repair restores the block’s structural integrity, ensuring reliable engine performance. Welding also extends the engine block’s lifespan, creates a strong bond, and prevents further damage.
Applications You Should Know About
People often use welding on cracked engine blocks for emergency repairs. It has many applications, including:
- Street Racing Repairs: Welded engine blocks help racers quickly fix overheating issues. It’s popular because every second counts on the track.
- Heavy Equipment Maintenance: Repairing cracked blocks on machinery saves money and extends the life of expensive equipment like excavators.
- Marine Applications: Welding cracked engine blocks on boats is common, keeping vessels operational. Fishermen often choose this to avoid costly replacements.
- Restoration Projects: Classic car enthusiasts weld engine blocks to restore vintage vehicles. This method preserves historical rides in pristine condition without losing authenticity.
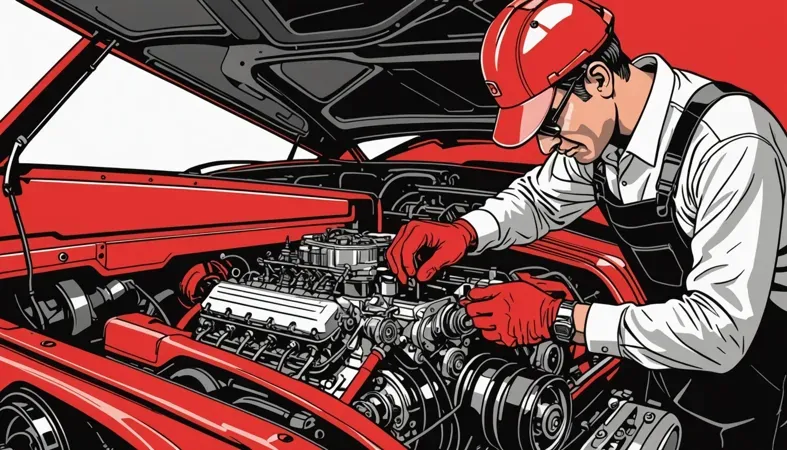
Alternatives for Repairing a Cracked Engine Block
When you’re faced with a damaged engine block, several alternatives exist to achieve effective repairs without welding. You might consider using epoxy-based solutions like JB Weld, known for its strong bonding properties. This option works well for minor cracks, especially when welding isn’t feasible due to access issues.
Another alternative is to use specialized engine block repair kits, such as those from ATP or Permatex. These kits often include sealants and compounds designed to fill and seal cracks. From what I’ve encountered personally, they can offer a quick fix and save time, especially if you’re looking to get back on the road fast.
Frequently Asked Questions (FAQs)
Now let us look at some common questions I typically get asked.
Will JB Weld Fix a Cracked Engine Block?
Yes, JB Weld can fix a cracked engine block. This epoxy is made to withstand temperatures up to 1200°F (649°C) and offers excellent bonding strength. However, it’s best for small cracks; larger issues require professional welding.
Is It Worth Fixing a Cracked Engine Block?
Yes, it’s worth fixing a cracked engine block if the repair cost is lower than a replacement engine. A typical repair costs around $500 to $1,500 depending on severity. If the engine has low mileage and is in good condition, a repair makes sense.
Can You Sleeve a Cracked Engine Block?
Yes, you can sleeve a cracked engine block. Sleeving involves installing a metal sleeve in the cylinder to fix issues. It’s a great option when there’s extensive damage, as it restores the cylinder’s integrity while keeping costs down compared to a full engine replacement.
What is the Best Epoxy for Engine Block Repair?
The best epoxy for engine block repair is high-temperature epoxy like JB Weld High-Temperature. It can handle harsh conditions and bond well to metal surfaces. Research shows it can withstand up to 500°F (260°C), making it ideal for engine repairs.
Can a Cracked Engine Block Be Welded?
Yes, a cracked engine block can be welded. Professional welders use methods like tig welding to repair cracks. Proper preheating and filler material selection are essential to avoid further damage, as misaligned blocks can lead to issues later on.
Conclusion
I’m glad we could cover this together. We discussed what an engine block is, types of engine blocks and their weldability, prerequisites for welding, the steps to weld a cracked engine block, precautions, types of welding that apply, factors that affect weldability, common problems, and aftercare tips along with benefits and alternatives for repair. Each section provided insights to help with the question: can you weld a cracked engine block?
So, can you weld a cracked engine block? Yes, but it depends on the type of block and its condition. Remember many factors, like the material and size, play a role. If you have further questions or need personalized advice on your engine block repairs, feel free to reach out.
For a deeper understanding of welding techniques and resources, be sure to visit What is Welding for more in-depth welding guides and tutorials.
References
- ISO. (2017). ISO 3834: Quality Requirements for Fusion Welding of Metallic Materials. Geneva, Switzerland: ISO.
- Kou, S. (2003). Welding Metallurgy (2nd ed.). Hoboken, NJ: Wiley.
- Schweitzer, P. A. (2007). Metallic Materials: Physical, Mechanical, and Corrosion Properties. New York, NY: CRC Press.
Tyler is a passionate DIY welder and self-taught metal artist with years of hands-on experience transforming raw materials into functional and artistic creations. Specializing in MIG welding, Tyler crafts everything from custom furniture to outdoor sculptures, blending creativity with technical skill. Committed to making welding accessible, Tyler shares practical insights and project inspiration to help beginners and hobbyists confidently explore the world of metalworking.
Aluminum Welding, Automotive Maintenance, Cast Iron, Engine Block Repair, TIG Welding, Welding