Can You Weld Cold Rolled Steel to Hot Rolled Steel? Understanding Weldability, Tools, and Techniques
Published on: April 13, 2025 | Last modified: March 4, 2025
By: Joe Carter
Now, can you weld cold rolled steel to hot rolled steel? This is important because understanding the difference between the two can affect your weld’s strength and quality. I’ve seen firsthand how failing to recognize these differences can lead to weak joints, so it’s crucial to grasp this concept well.
In this guide, I’ll cover what cold rolled steel is, types and weldability, essential tools needed before you start, the main steps for welding, important precautions, types of welding techniques, factors affecting weldability, unique issues specific to cold rolled steel, aftercare and inspection tips, advantages, common applications, and alternatives for welding cold rolled steel to hot rolled steel. We’ll also answer some frequently asked questions about when you might want to consider these aspects.
Contents
- Can You Weld Cold Rolled Steel to Hot Rolled Steel?
- What is Cold Rolled Steel?
- Types Of Cold Rolled Steel and Their Weldability
- Essential Tools Before You Start (Prerequisites)
- Steps to Weld Cold Rolled Steel to Hot Rolled Steel
- Essential Precautions
- Types Of Welding for Cold Rolled to Hot Rolled Steel
- Factors Affecting the Weldability Of Cold Rolled Steel
- Issues Unique to Cold Rolled Steel
- Aftercare, Inspection, and Advanced Tips
- Advantages
- Typical Applications
- What Are Alternatives to Welding Cold Rolled Steel to Hot Rolled Steel?
- Frequently Asked Questions (FAQs)
- Conclusion
- References
Can You Weld Cold Rolled Steel to Hot Rolled Steel?
Yes, you can weld cold rolled steel to hot rolled steel. It’s not too tricky, but you need to mind the differences in carbon content. Preheating helps reduce the risk of cracking. Stick with MIG or TIG for best results!
What is Cold Rolled Steel?
Cold rolled steel refers to steel processed by rolling it at room temperature. This method produces a smoother surface and improved dimensional accuracy. It’s typically manufactured to specifications like ASTM A1008/A1008M or equivalent, with a yield strength ranging from 250 MPa (36,000 Psi) to 340 MPa (49,000 Psi) and a tensile strength between 400 MPa (58,000 Psi) and 650 MPa (94,000 Psi). Cold rolling also reduces oxidation and corrosion, making it a reliable choice for various applications.
Now, can you weld cold rolled steel to hot rolled steel? From my experience, you can, but be aware of potential challenges. The differences in properties can cause issues like distortion or heat-affected zones if you’re not careful with your welding technique.
During a project involving both steel types, I aimed for the best weld quality. I explored whether you can weld hot rolled to cold rolled steel. I learned it’s essential to adjust the welding parameters to account for varying thermal conductivity and mechanical properties to ensure a clean and strong joint. It’s not just about skill; it’s crucial to understand the materials you’re working with.
Types Of Cold Rolled Steel and Their Weldability
What are the types of cold rolled steel, and how do they weld?
-
Commercial Steel
Commercial steel is popular for its malleability (Flexibility) and strength. You can weld it to hot rolled steel. Clean both surfaces, preheat if needed, and use a suitable filler metal for a solid bond. Learning the correct techniques is also essential when connecting components like thermocouple wires, which you can better understand through practical guides on how to weld thermocouple wire.
-
High-strength Low-alloy Steel
This type increases strength while staying lightweight. It’s weldable to hot rolled steel. To ensure a proper weld, use the correct welder settings and a compatible filler rod.
-
Cold Rolled Sheet Steel
This steel is often used in automotive and appliance manufacturing. You can effectively weld it to hot rolled steel. Clean both surfaces and use MIG welding for the best results.
-
Carbon Steel
Carbon steel comes in various grades and is known for its durability. You can weld it to hot rolled steel. Ensure proper edge preparation and use a compatible filler to prevent cracking.
-
Electrical Steel
This steel is made for electrical applications and has specific magnetic properties. It’s not ideal for welding to hot rolled steel. Use low heat settings and consider alternative fastening methods to minimize issues.
We have now covered the different types of cold rolled steel and their weldability. Next, we will examine essential tools needed before starting.
Essential Tools Before You Start (Prerequisites)
What do you need to weld cold-rolled steel to hot-rolled steel?
- MIG Welder: You’ll need a MIG welder, like the Lincoln Electric SP135 Plus. It requires a voltage input of 120 V (Volts).
- ER70S-6 Welding Wire: You’ll need ER70S-6 wire, such as Hobart 308517-R41. It’s essential for strong welds between cold and hot-rolled steels.
- Argon-CO2 Mixture Shielding Gas: You’ll need a gas mix, typically 75% argon and 25% CO2 (Also Called C25). It protects your weld from contamination and oxidation.
- Welding Cleaner/Brush: You’ll need a stainless steel wire brush or a cleaning solution, such as 3M Clean-N-Strip. It prepares the metal surfaces for better weld quality.
So far in this section we covered the essential tools needed for welding. In the next section we will talk about the steps to weld cold rolled steel to hot rolled steel.
Steps to Weld Cold Rolled Steel to Hot Rolled Steel
Here are the steps to weld cold rolled steel to hot rolled steel successfully. Follow them closely for the best results.
-
Select the Right Materials
Ensure the cold and hot rolled steel are compatible. Cold rolled steel typically has a higher yield strength, around 200 MPa (29,000 Psi), compared to hot rolled steel at 250 MPa (36,000 Psi). This difference affects the welding process, so you may need additional filler material. A MIG (Metal Inert Gas) setup works best with ER70S-6 or a similar filler wire for stronger bonding.
-
Prepare the Metal Surfaces
Clean both metal surfaces thoroughly. Use a wire brush or grinder to remove rust, dirt, or oil, as these can compromise a weld. Understanding the various welding by metals will further enhance your technique. Smooth edges will help prevent issues during welding. Inadequate cleaning can lead to problems like porosity or weak joints, resulting in failure.
To ensure optimal performance and ergonomic comfort during your welding projects, it is important to understand how high a welding table should be.
-
Set Up Your Welder
For your MIG welder setup, set the voltage between 18 to 24 volts. Adjust the wire feed speed (Usually Between 2.2 To 5.0 Meters Per Minute) for optimal penetration. You may need to tweak settings based on steel thickness—thicker metals require higher settings. Start with the lower voltage and gradually adjust until you achieve the desired bead.
-
Weld the Materials Together
Begin by tacking the pieces in place, using short welds to hold them without warping. Maintain a steady pace and consistent travel speed—around 10 inches (25 Cm) per minute is effective. Avoid weaving motions; use short bursts to keep the bead focused. Ensure a slight overlap into both steel types to improve joint integrity.
We covered the steps to weld cold rolled steel to hot rolled steel. Next, we will cover essential precautions.
Essential Precautions
Let’s look at precautions for welding cold and hot rolled steels.
- Proper PPE: Always wear gloves and a face shield. I recommend durable leather gloves to prevent burns. This minimizes the risk of personal injury when welding.
- Ventilation: Ensure good airflow to avoid fumes. Use a fume extractor with 300-500 cubic feet per minute (CFM). Proper ventilation protects your lungs from toxins.
- Material Cleanliness: Clean surfaces to remove dirt and oil. For cleaner finishes, use a degreaser like acetone. Residue weakens welds and creates defects.
- Gauge Thickness: Match metal thickness for stable welds. Use calipers to measure; ensure even pressure for effective bonding. Improper thickness can lead to weak joints.
Never overlook safety precautions; they’re crucial for a successful project!
Types Of Welding for Cold Rolled to Hot Rolled Steel
Let’s discuss types of welding: MIG, TIG, Stick, Flux-Cored Arc, and Submerged Arc welding.
-
MIG Welding
MIG (Metal Inert Gas) welding uses a continuous wire feed as an electrode. It’s fast and efficient, making it ideal for welding thin sheets of cold rolled steel to thicker hot rolled steel. At a speed of 300 to 600 inches (7.6 To 15.2 Meters) per minute, it’s perfect for projects needing quick results.
-
TIG Welding
TIG (Tungsten Inert Gas) welding offers precision. This method uses a non-consumable tungsten electrode, allowing control over heat and the weld pool, which is ideal for thin materials.
-
Stick Welding
Stick welding, or SMAW (Shielded Metal Arc Welding), uses a consumable electrode. It’s versatile and effective for thick materials, especially on dirty or rusted surfaces when welding cold rolled steel to hot rolled steel.
-
Flux-cored Arc Welding
Flux-Cored Arc Welding (FCAW) combines MIG’s benefits with a tubular wire. It’s preferred for outdoor jobs since the flux protects the weld from contamination. It efficiently welds cold rolled steel to hot rolled steel with a high deposition rate.
-
Submerged Arc Welding
Submerged Arc Welding (SAW) is a high-productivity technique that feeds a bare wire electrode and granular flux. It’s mainly used for heavy steel applications, making it suitable for thicker cold and hot rolled steel connections.
We’ve wrapped up the types of welding for cold rolled to hot rolled steel here. Next up, we’ll look at factors affecting weldability.
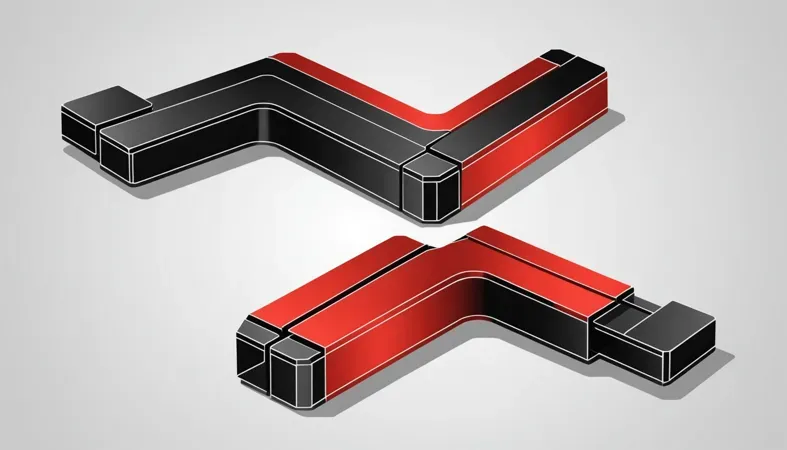
Factors Affecting the Weldability Of Cold Rolled Steel
What factors determine welding compatibility between cold and hot rolled steel?
-
Material Thickness
Thicker materials require more heat to weld. For example, 3 mm (0.12 In) cold rolled steel needs different settings than 1.6 mm (0.063 In) hot rolled steel.
-
Welding Method
MIG and TIG welding are popular for steel. Each method provides different heat levels and control, impacting metal fusion.
-
Heat Affected Zone (HAZ) Considerations
Minimize the HAZ to avoid brittleness. Preheating is necessary if the cold rolled steel is too thin, particularly at around 150°C (302°F).
-
Surface Contamination
Oil, rust, or dirt can compromise weld quality. A clean surface leads to better fusion at the joint, resulting in stronger welds.
-
Electrode Type
Choosing the right electrode is crucial. For example, E7018 rods work well for both steel types, providing stronger joints.
You should now have a good understanding of the factors influencing cold rolled steel’s weldability. In the next part, we’ll discuss issues unique to cold rolled steel.
Issues Unique to Cold Rolled Steel
Let’s examine the unique challenges of welding cold rolled steel.
-
Higher Distortion
Cold rolled steel often warps during welding due to rapid temperature changes. Monitor heat flow closely to manage distortion. Use preheating techniques.
-
Cracking Susceptibility
Cold rolled steel can crack easily at stress points. Ensure proper joint design and use filler material that matches its properties.
-
Increased Surface Hardness
The cold rolling process adds hardness, making machining difficult. Use softer tools or adjust speeds to prevent tool wear.
-
Tension Variation
Cold rolled steel often has inconsistent tension, which may lead to uneven welds. Conduct tension checks and adjust your setup as needed.
So far we covered the specific challenges associated with cold rolled steel. Next, let’s look at maintenance, inspection, and expert advice.
Aftercare, Inspection, and Advanced Tips
Here’s guidance on caring for your welds, what to check, and pro tips for cold rolled steel.
Aftercare Tips
After welding cold rolled steel, cool it slowly. Rapid cooling can cause warping or cracking. Use tools like a heat sink to regulate temperatures; aim for a cooling rate of 10 °C (18 °F) per minute. If you are considering welding different types of steel like zinc-plated steel, it’s important to understand the specific challenges and techniques.
Inspection
Inspect your welds for undercutting, especially in cold rolled steel, using a visual inspection method. Check for displacement exceeding 0.5 mm (0.02 In) along the edge. I used a Magnetic Particle Tester (MT) to identify surface-breaking defects.
Expert Tips
From one expert to another, always preheat cold rolled steel to about 100 °C (212 °F) before welding. Use a filler rod with low hydrogen content to avoid cracking, aiming for less than 5 mL of moisture. When finishing, grind the surface and apply a corrosion-resistant coating within 72 hours.
That covers aftercare, inspection, and advanced tips. Let’s now take a look at the advantages.
Advantages
The main benefit of welding cold-rolled steel to hot-rolled steel is the ability to combine different material properties, enhancing performance. This process creates strong, durable structures that can withstand various stress conditions.
Additionally, you gain several benefits. First, it improves versatility in fabrication, allowing effective use of both steel types. Second, it offers cost savings by utilizing leftover materials without waste. Third, it broadens applications to include automotive, construction, and heavy machinery. Finally, it enhances the final product’s strength without compromising ductility (Flexibility).
Typical Applications
I’ve seen people weld cold rolled steel to hot rolled steel for various tasks. Here are some unique applications:
- Structural Frames: Used in buildings, combining strength and flexibility. Cold rolled offers better finishes, while hot rolled provides weight. It’s popular in the construction industry.
- Automotive Parts: Welded for chassis fabrication. Cold rolled ensures a smooth surface, and hot rolled delivers durability. Common in custom fabrication shops.
- Machinery Components: Joining parts to enhance performance. Cold rolled provides precision, while hot rolled ensures toughness. Essential in manufacturing sectors.
- Artistic Fabrications: Used for sculptural works. Cold rolled allows intricate designs, while hot rolled offers a strong base. Gaining popularity in the art world.
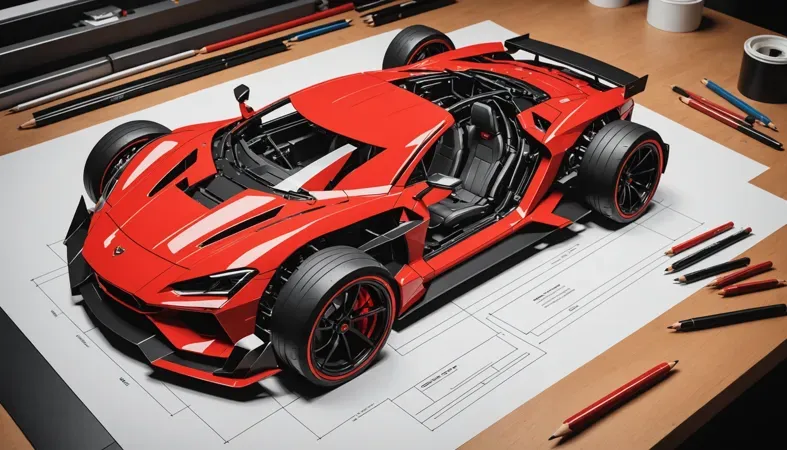
What Are Alternatives to Welding Cold Rolled Steel to Hot Rolled Steel?
If you’re looking for alternatives, consider using mechanical fastening methods like bolts or rivets. These can provide similar strength and are often easier to work with than traditional welding. You might also explore adhesive bonding, using products such as epoxy or polyurethane, which can achieve impressive results without introducing heat, thus reducing distortion.
In some cases, you can also use methods like brazing or soldering. These techniques involve melting a filler material, creating strong joints while minimizing heat effects on the base metals. These options can be a smarter choice when working with cold rolled materials due to their sensitivity to heat and potential for defects like porosity.
Frequently Asked Questions (FAQs)
Here are some questions I typically get asked about welding cold rolled steel.
Which Steel is Stronger, Hot Rolled or Cold Rolled?
Hot rolled steel isn’t as strong as cold rolled steel. Cold rolled steel has a tensile strength of about 550 MPa (80,000 Psi) compared to hot rolled steel’s 410 MPa (60,000 Psi). The difference in strength is due to how each type is processed—cold rolling strengthens it through strain hardening.
Can You Weld Cold-formed Steel?
Yes, you can weld cold-formed steel. It’s important to consider the steel’s thickness and ensure proper welding techniques are used. Cold-formed steel is typically thinner, which means you may need to adjust your settings to avoid warping or burning through. When dealing with thinner materials such as 16 gauge sheet metal, it is crucial to understand how to weld 16 gauge sheet metal effectively.
Can Cold Rolled Steel Be Hardened?
Yes, cold rolled steel can be hardened. This process often involves heat treatment to increase its hardness and strength. Methods like quenching and tempering can raise hardness levels to over 600 HV (Hardness Value Units), making it suitable for various applications.
How to Prep Hot Rolled Steel for Welding?
Preparing hot rolled steel for welding is crucial. Clean the surface to remove any scale, rust, or oil. A cleaner surface ensures better weld penetration and a stronger bond. Also, bevel edges if necessary, especially for thicker steel, to allow better weld access.
Can You Weld Hot Rolled Steel?
Yes, you can weld hot rolled steel. It’s easier to work with due to its malleability. However, make sure to account for scale formation that can arise after processing, as it may affect the weld quality. Proper cleaning and preparation are key.
Conclusion
We covered a lot in this article. We discussed cold rolled steel, its types, their weldability, and the essential tools you need before starting. We also touched on the steps for welding, essential precautions, types of welding methods, and factors that affect weldability, along with common issues and aftercare tips.
So, can you weld cold rolled steel to hot rolled steel? Yes, you can. Consider the grades you’re working with, such as S235 (Hot Rolled) and CS1018 (Cold Rolled), and remember that heat affects both materials differently. As you weld, watch for warping or joint integrity, especially since the different cooling rates can lead to cracking.
If you want to delve deeper into welding techniques and best practices, you can visit What is Welding for a comprehensive overview of the subject.
References
- American Welding Society. (2015). AWS D1.1/D1.1M: Structural Welding Code – Steel. Miami, FL: AWS.
- American Welding Society. (2020). AWS Welding Handbook: Welding Science and Technology (Vol. 1). Miami, FL: American Welding Society.
- Blodgett, O. W. (1995). Design of Weldments. Cleveland, OH: James F. Lincoln Arc Welding Foundation.
Joe Carter is a retired welding professional with over 40 years of hands-on experience in the industry, spanning ship repair, structural welding, and even underwater projects. Joe is a master of MIG, TIG, and Stick welding. Passionate about mentoring the next generation of welders, Joe now shares his decades of expertise and practical insights to help others build rewarding careers in welding.
American Welding Society, Cold Rolled Steel, Hot Rolled Steel, Metal Fabrication, Weldability, Welding, Welding Table, Welding Techniques, Welding Wire